Venting and finishing an attic of a timber frame home

I’m hoping some folks wiser than I can chime in with their thoughts on how to properly finish off the attic space of a former New England Barn.
In a nutshell here are the existing conditions:
-A 200+ year old Post and Beam building near the ocean. (good breezes)
-An unaccessible dirt floor crawl space with No vapor barrier
– Wall insulation : 1-2″ Encompassed Balsa wood insulation snaking between offsetting 2×3’s (airflow from the crawl space up thru the walls is good for air circulation and bad for R value.)
-2 finished floors of existing living space
-An unfinished attic space with fiberglass batt insulation covering the 2nd floor ceiling joists
-A new(ish) Architectural asphalt shingled roof
– wide wood planks as roof sheathing
– 4″x4″horizontal perlins spaced roughly 4′ apart vertically
– Ventilation is provided by windows in the attic which are opened in the spring and closed in the late fall.
My goal: To finish off the attic space as cost effectively as possible. My question pertains mainly to the ventilation issue for the roof assembly. I have read and spoke to a few people who say a cold roof system is the way to go. But in my situation the cost of furring and re-roofing a 50×40 roof is not palletable due to sheer cost.
My questions are: Would closed cell foam on the bottom of the roof assembly trap all the moisture coming up from the dirt floor crawlspace/living space? My thought is yes, and the potential stack effect would potentially compound the issue leading to a big risk of mold.
My alternative thoughts and I am hoping someone out there has experience with this:
I fur out the rafters and Insulate the roof deck with Rockwool. To ventilate I’ll cut in soffit vents down the eaves and use air baffles along the roof deck. At the perlins is my obvious problem- so my thought is to make some site built baffles (with some 1″ polyiso ridgid foam) to take the air from the air baffle on either side and tape off the connections with some HVAC tape. (yeah, that sounds crazy to me too!)
To vent to roof I was considering either cutting in a ridge vent about 6″ below the ridge or adding (2) 32″ x 32″ cupolas.
Just typing that makes me think I’ve lost my mind. So if you’re still reading and haven’t fallen off your chair laughing yet- my other thought is to not insulate the roof deck at all since this space is only going to be used in the summer months. I would keep the insulation in the 2nd floor joist bays. And perhaps utilize a whole house fan and a cupola to vent the hot air from the day out the cupola.
Is there a solution out there that I’m totally overlooking? I know I’ve lost my mind, but hopefully there is something that can be done to achieve the goal of creating useable living space for the summer months here in New England.
Thanks all
GBA Detail Library
A collection of one thousand construction details organized by climate and house part
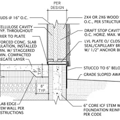
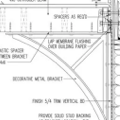
Replies
Tates,
Start by reading this article: How to Build an Insulated Cathedral Ceiling.
Closed-cell spray foam is a vapor barrier, an air barrier, and an effective insulation material. It will not "trap all the moisture coming up from the dirt floor crawlspace/living space," whatever that means.
(You seem to be operating under the false assumption that your ceiling or roof should remove moisture from your house. It shouldn't. If you need to remove moisture from your house, get a ventilation system or a dehumidifier.)
Martin, thank you for your insight. I have read over more of the links on your site regarding the recommendations for flash and batt in the attic over the last couple days. I think I have the right mode of thinking this time, but there was a lot to digest.
If I pointed in the wrong direction now, let me know.
The site conditions are 3" horizontal purlins. The building inspector is making me achieve R49 due to the conversion of unconditioned to conditioned space. So I will need to furr out the purlins and create some cavities for the insulation. Also worth noting, there is newer unfaced and uncompressed R38 rolls covering the attic floor which I was hoping to utilize rather than adding to the dumpster.
My plan is to furr out using 2x8's. My cavity for insulation should be 8 3/4" if all goes to plan.
To get to R49 I am thinking the most economical means is to use:
3" closed cell @ R 6.9= R20.7
9 1/2" of compressed fiberglass batt to fill the remaining 5 3/4" cavity = Reduced Rvalue of R21
1" of XPS panel over the batt = R5
Which only gives me a total R of 46.7ish.
I'm going to ask the Foam installer if they would do 3.5" of closed cell. He seems like he is very willing to do whatever is asked. If he did do 3.5" that would bring me closer to the required R49 (although the 1/2 of compressed fiberglass would need to be deducted. I think I would be close)
I have 6 or 7 skylights which will be installed in the roof. I know they won't help my heat retention for the space but I wanted to mention this in case.
Lastly two of the foam installers recommended an air exchanger be installed to address any moisture concerns coming from the basement crawlspace/living spaces below. Would you concur this would be a wise investment. In the summer, the windows will be open and the winter everything in the attic will be sealed up.
Thanks again for all your valued input. There is a lot to take in for sure!
Matt
Matt,
OK, so you are going with a flash-and-batt approach. That means that you have to follow the R-value ratio rules for combining foam insulation with fluffy insulation. The rules are explained in this article: Combining Exterior Rigid Foam With Fluffy Insulation. (Although the article discusses rigid foam rather than spray foam, the ratios in the article apply in both cases.)
To figure out whether your proposed assembly is safe, we need to know your climate zone or geographical location, which you haven't told us. We just have clues: you are in New England, and near the ocean. That probably means that you are either in Zone 5 or Zone 6.
You propose installing spray foam insulation with an R-value equal to 44% of the R-value of the total assembly. That approach is safe in Zone 5, but inadequate in Zone 6.