1929 Brick Building in Zone 5A needs insulation— Half of the low-slope roof is very tight and not accessible

We have a 1929 Brick building in Zone 5A with an 8,000 square foot low slope EPDM Roof. It has old single pane windows with cheap metal storm windows attached. The exterior walls are 13″ thick, with 9″ of hollow bigger bricks, and 4″ of regular nice looking bricks).
The first floor has been renovated already, and now we would like to add apartments to the top floor. Before we do this we would like to make some energy efficiency upgrades. Can you recommend what would be best for insulating the attic and or walls?
North half of attic has room to move around in
Currently we are thinking to add blown in cellulose to the North Half since it is easy to access and move around in. I have heard EPDM roofs act as a moisture barrier, will this work in this case or should I be adding something else?
Construction from the roof deck down is:
- 43″ air gap
- HVAC return vents
- 4-6″ of cellulose
- Lathe & plaster in bad condition – missing plaster, broken through etc.
- HVAC ducts
- Suspended Ceiling 12″ below lathe & plaster
South half of attic has higher ceilings and is not easily accessible
There is already some cellulose in the attic, but multiple insulation contractors have said they would not be able to add more cellulose or spray foam without gutting the ceiling because there is not enough room to get around in the attic. We would like to avoid a costly tear out of the ceiling, so we were thinking of applying rigid foam to the existing ceiling and then drywall over that.
Side note: There is about 1500 square feet of unheated hallway and storage space on the South Half of the building. We would like to leave this as is, but will not insulating above this nullify insulating the heated spaces?
Construction from the roof deck down is:
- 30″ – 19″ air gap – tapers to the south
- HVAC ducts
- 4-6″ of cellulose
- Lathe & plaster in bad condition – missing plaster, broken through etc.
- 1×3″ furring strips
- 12×12″ fiberboard ceiling tiles – Would like to replace with drywall
Exterior Walls
The exterior walls have been furred out with 2×4’s and drywall, and insulated with fiberglass batts. I have read about not insulating your walls too much because it causes the bricks to stay cold and wet. The brick looks like it is in very good condition, however it could use some repointing in some areas. Should I be concerned with the existing fiberglass insulation, or does it not sound like an issue in this climate and I should be adding more cellulose or R-foam to the walls?
GBA Detail Library
A collection of one thousand construction details organized by climate and house part
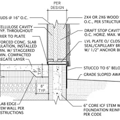
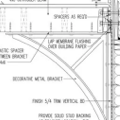
Replies
Aaron,
Since you have ducts in the attic, the best approach is to install insulation (rigid foam) above the roof sheathing. Of course, this approach would require the installation of new roofing. If you take this approach, don't forget to insulate the attic walls.
For more information on insulating the walls of an older brick building, see Insulating Old Brick Buildings.
If you have 2' roof overhangs you probably don't need to worry too much about the interior side studwall, but if those bricks get much rain-wetting the studs and the cavity-side face of the gypsum are going to run pretty damp, with high mold/rot potential. The "right" way do it would be to install the studs with the edges 1-1.5" (or more) off the brick, and apply an inch or so of closed cell polyurethane foam on the brick so that there is foam between the studs and brick, sealing the stud-bays from each other, then filling the cavity with blown cellulose (or 1.8lbs density blown fiberglass.) That would meet code-min, have sufficient R at the foam/fiber interface to avoid accumulating winter moisture in the fiber, and sufficient vapor retardency between the fiber and brick that moisture from the brick can't affect the stud cavity moisture much (and conversely.)
The hollow cores of the 9" blocks will give you some moisture drive relief- maybe even enough. You may want to inspect or monitor a few cavites of the already built-out part on the most rain-exposed side.
If you put at least R20 as rigid foam between the roof deck and the membrane roof you can then put up to ~R40 or so in cellulose below without risk of accumulating wintertime moisture in the roof deck with an unvented approach. That means you could dense pack the thin edge of the wedge with cellulose to where the height is 10-12", which means the rest could be done as open-cell foam (which may be easier/cheaper than fiber in netting- certainly quicker. But without the R20+ above the roof deck you need to vent the roof deck. R20 roofing iso is 3.5" thick, and runs about $60-65/sheet new f.o.b. the distributor's yard, but in some places you can get reclaimed roofing iso at 1/4-1/3 the price of virgin stock. (In Massachusetts there are several vendors of reclaimed goods.) More is always better- a double-layer of 2" with seams staggered between layers performs better than a single layer of 4" since you won't have un-blocked gaps opening/closing with seasonal dimension changes.
If the existing single-pane windows are in good shape, scrapping the crummy storms and installing some Harvey Tru Channel storms with the low-E glazing option, or the silver/gold Larson low-E storms would bring the performance to about code-min at a much lower cost than a code-min replacement window. (Harvey has the tightest in the biz, the Bronze Larsons are pretty leaky and have lousier hardware- it's worth the up-charge for the silver or gold versions.)
DO insulate the unheated space- walls included. By air sealing and insulating that space you will reduce the mold hazard, and reduce the energy use of the adjacent fully-conditioned spaces. Putting thermal partitions between heated/unheated spaces inside the pressure envelope of the building is just begging for a mold problem. The the right place for the insulation is the exterior surfaces (walls/ceiling or roof/floor).
Walls
We do not have any overhangs, but we do have tall parapet walls on the roof.
You pointed out that the ideal way to insulate the walls would be to tear off the drywall, remove the fiberglass batts and use spray foam against the brick, followed by cellulose. This sounds ideal, but is too expensive for us, so we are considering the following options:
1) Dense pack cellulose - I have not found a contractor yet who thinks he can do this behind fiberglass batts.
2) Use Applegate R-foam - I have read about shaving cream like foam products being used behind fiberglass batts but it sounds like they all suffer from shrinkage around the edges, any thoughts on this type of system?
Which one would you suggest and would either of these methods present a problem with moisture and freeze thaw in the brick walls?
Attic: North Half
Dana said: "If you put at least R20 as rigid foam between the roof deck and the membrane roof you can then put up to ~R40 or so in cellulose below without risk of accumulating wintertime moisture in the roof deck with an unvented approach. "
We do have a vented roof, the North Half of the attic has 4 side wall vents, and 1 Large barn vent, 1 regular sized barn vent.
You mention the ideal method would be to add R20 Iso board to the roof deck. We may end up doing this, but we will have to wait until we re-roof which may be 5 years from now.
Which of these seems to be our best current option?
1) Spray foam the underside of the roof deck - Expensive, but will act as a moisture barrier. Will also need to insulate attic walls.
3) Blow in R60 of Loose Cellulose and cover existing return duct work - Most economical but does this provide a vapor barrier? Will this create moisture problems in our vented attic if we do not have Iso board on the roof deck?
Attic: South Half
There are no side wall vents, and 2 regular sized barn vents in the roof.
Which of these seems to be our best current option?
1) Dense pack the attic cavity - It is 19" at the smallest point, so that would be a lot of insulation to dense pack.
2) Blow in more cellulose - This would require holes all over the ceiling to be able to reach each rafter bay.
3) Install R-10 XPS rigid board to ceiling - This would create an air barrier, and would not require demolition of the ceiling. I think we are leaning towards this.
Response to Dana
Thanks for the tip on insulting the unheated spaces; we will definitely treat the entire building envelope the same regardless of heated vs unheated space.
I have started looking into re-claimed Iso board, and I will try to get some for when we re-do our roof.
Response to Martin
Thank you for writing such detailed and brilliant articles! I thought it might be helpful for others to see what articles have been most helpful for my situation so far:
Insulating Old Brick Buildings
https://www.greenbuildingadvisor.com/blogs/dept/musings/insulating-old-brick-buildings
Insulating low slope residential roofs
https://www.greenbuildingadvisor.com/blogs/dept/musings/insulating-low-slope-residential-roofs
How to install rigid foam sheathing
https://www.greenbuildingadvisor.com/blogs/dept/musings/how-install-rigid-foam-sheathing
All about attic venting
https://www.greenbuildingadvisor.com/blogs/dept/musings/all-about-attic-venting
Aaron,
You have pointed out that you can't afford to perform the work in ways that are recommended on the GBA site. That's understandable. However, I can't recommend halfway measures.
If you want to insulate the walls of an older brick building, I recommend that you follow the guidelines in my article. The best approach is to insulate the brick walls on the exterior. If you want to install interior wall insulation, and if a survey indicates that the building has bricks that will not be harmed by interior insulation, then the only approach I would advise is the use of closed-cell spray polyurethane foam.
Similarly, my attic advice remains unchanged. If you have attic ducts, the insulation should be installed above the roof sheathing, and you should install new roofing. This approach would require you to insulate the attic walls.
If you choose a different approach, your building could easily have a variety of moisture or performance problems.
On a plank sheathed roof deck closing off the venting and spraying 6-12" of half-pound foam (open cell) onto the underside of the roof deck will usually be fine- won't be the mold/rot nightmare that you would get were it OSB, especially if you can then spray-paint the foam on the underside with "vapor barrier" latex. The folks at Building Science Corp say that the v.b. latex won't perform to the ~0.5 perm spec if applied directly on open cell foam, but you'll get about 5 perms, which is enough to control the moisture reasonably in plank sheathing, if marginal for OSB. When it's time to re-roof, you can then add the exterior R20, which will lower the wintertime moisture build up even further. R20 over the roof deck with 6" of open cell under the roof deck meets IRC 2009 code-min for zone 5A but you'd need to bump the open cell to at least 9" to hit the IRC 2012 code min. From an installation point of view it's easier & better to stop at 6", otherwise it has to be applied in multiple lifts. (If in the mean-time you can find a source of reclaimed roofing foam and put up R30 instead of R20 over the roof deck you'd be at IRC2012 levels for less money than the extra lift of spray foam too.) At 6" with open cell foam you're looking at about $2 per square foot, installed price. With reclaimed roofing foam R20 (3.5" polyiso or a layer of 1.5" and layer of 2", seams staggered) is about 60-75 cents/square foot, R30 would be about a buck a foot (a layer of 2-inch plus a layer of 3", seams staggered), plus installation labor & scrap rates.
If taking the rigid foam on the ceiling approach, rather than 2" XPS on the ceilings, go for 2.5-4" of EPS in two layers. XPS uses high global warming potential blowing agents and is a bit on the vapor-tight side if you decided to go unvented on the roof later. The blowing agents for EPS and iso are much more benighn, and EPS is at least semi-permeable even at 4", which provides a drying path toward the interior.
With no overhangs on the roof insulating the walls from the inside is risky, since the brick is guaranteed to be rain-wetted regularly. The non-expanding injection foams have outgassing issues (they are a reformulation of the urea formaldehyde foams of class-action lawsuit infamy of the 1970s), and they are highly vapor permeable, providing none of the moisture protection you get with closed cell polyurethane or expanded polystyrene. I'm with Martin on this one: A 1-2" shot of closed cell on the exterior becomes it's own weather resistant barrier (needs to be under siding to protect it from UV degradation thouugh), and is sufficient exterior R to allow you to fatten out the R on the interior with an insulated studwall approach. Code-min would be met with 1" of exterior polyurethane foam, and a fiber-insulated 2x4 interior stud wall, but a 2x6 stud wall would work too.
Deal with the roof first- if it fails, it damages the rest. From the staining/mold it looks as if there has been chronic air leakage &/or roof leaks in parts of the attic space.
It seems like the recommendation for closing off the vents and installing the Polyiso rigid foam on the roof side of the deck, and spray foam on the bottom of the deck, is so that the condensation of moisture in the air from the living spaces below, will not condense on the bottom of a cold roof and create mold and rot.
It also seems like this is the recommended way to do things IF the attic contains the HVAC vents.
-But-
What if we move the HVAC vents to the interior side of the ceiling, and re-do the ceiling taking care to correctly air seal it.
Currently we have drop ceilings in the North half which look bad, but they cover up the deteriorating lathe and plaster ceiling. What if we tore out the drop ceiling, and added a new layer of drywall over the lathe and plaster. This would create an air barrier (we will not use can lights), give us more ceiling height, and look much better.
The HVAC for the North 4 units is coming from 1 very old furnace. If we added a new smaller furnace for each unit, we could then remove the junky grey insulated flexible ducts, and replace them with new ducts located below the newly built drywall ceiling.
With a reliable air barrier in place, duct work below the attic, and a vented low-slope roof, the logical way to insulate would be to blow in cellulose over the attic floor creating a total of R-60. Right?
The South side of the building has 3 units and currently 1 furnace. What if we added 3 new furnaces, dropped the duct work down under the ceiling, and added 4" of rigid foam to the ceiling, then covered with new drywall. I think we would want ISO or XPS on the ceiling to help create a moisture barrier if we are keeping the attic vented.
On a side note, we have bathrooms that vent in to the vented attic. Is this OK or should we extend these up through the roof.
Thanks for keeping up with me, I'm trying to understand how you think so I can answer my own questions for future projects.
Aaron,
If you want to try to make your low-slope roof a ventilated roof, make sure that you follow Joe Lstiburek's recommendations for vent openings. You'll need a "doghouse" or vented cupola in the center of the roof (or, in your case, perhaps in the center of each section of roof). These details are explained in my article, Insulating Low-Slope Residential Roofs.
Dana, you mentioned:
I assume you are saying this because you want a drying path to the interior so that if we ever did close off the roof vents, the attic could still dry out.
I found a good source for Recycled ISO board. Would this be acceptable to use on the ceiling above new drywall without creating a moisture problem in the attic.....if we were to ever seal off the vents?
I'm saying that primarily because the pentane used to blow EPS is about 1/200th the global warming potential of the HFC134a used for blowing the XPS. A vented attic doesn't need a vapor retarder, but 4" of type II EPS is by itself a class-II vapor retarder, which is more than enough to not worry about vented/unvented. At 4" XPS is about 0.2-0.3 perms.
With polyiso the vapor permeance is all in the facers. The paper faced and fiberglass faced stuff is usually 0.5-1 perms (usually crudely specified as "less than 1 perm"), but foil-faced goods are in the 0.03 perms range- a true vapor barrier.
The Attic is vented now, so Installing polyiso board with a fiberglass face, (not a vapor retarder) will work.
If the Attic gets rigid foam on top in the future, and we close off attic vents, will it be a problem that the polyiso board is letting vapor through and the roof is not vented? If so I should go for the EPS now or polyiso with a foil face right?
Thanks for the clarification.
Aaron,
Q. "Installing polyiso board with a fiberglass face ... If the attic gets rigid foam on top in the future, and we close off attic vents, will it be a problem that the polyiso board is letting vapor through and the roof is not vented?"
A. First of all, as Dana explained, the fiberglass face is a vapor retarder. It has a vapor permenace of only 0.5 to 1 perm. That is quite low.
Second, the major vapor transport mechanism from the interior of a building to the attic is air leakage, not vapor diffusion. Stop worrying about vapor diffusion. if you want to limit moisture transfer, pay attention to air leakage.
Ok, thanks for clarifying.