Insulation dew points and archaic insulation

I have a couple of questions, both somewhat academic since there may be little to do about them.
I live in a 1938 1.5 story (Cape-style) house in St. Paul, zone 6. About 3 years ago the shoddily-added back porch was falling apart and the roof shingles were shot , so I tackled both in one, replacing the back of the house with a new addition, and re-roofing the entire house using this “cold roof” article in JLC as a model (in short, adds 3″ XPS foam plus 1-1/2″ air gap above the original roof): http://www.jlconline.com/rooftop-accessories/retrofitting-an-insulated-cold-roof.aspx
It’s been very successful qualitatively, with much improved comfort summer and winter. Energy costs seem lower, though comparing year to year can be tricky. As you might expect, ice dams were a constant issue before, and are almost nonexistent now. However this was all done long before following this site, so one thing I wish I’d known back then was dew point calculations.
On the main house, the roof is framed with 2x4s, so we have approx R15 beneath the sheathing, and 3″ XPS foam above for a further R15. Assuming 20F outside/70F inside, the sheathing is at a comfortable 45F. On the addition, though, the roof was framed with 2×10 and filled with fiberglass batts (another thing I might have done differently), so we now have R30 inside and the same R15 outside, giving sheathing temperature of 37F, clearly below the dewpoint.
So now I know enough to figure this out, should I be concerned, and by how much?
Things that might be relevant
1) the ceiling below the addition roof has a vapor barrier poly sheet, albeit with perforations from attaching T+G wood.
2) all sheathing is plywood not OSB
3) the addition is a simple “shed roof” off the main roof, with lower pitch; the transition between them lies in the conditioned attic crawlspace. The joist cavity is not as well sealed in here – sloppy fitment of poly sheeting, which I still intend to correct – but before doing so, might this leakage aid drying or make things worse?
That’s all on that part. I’m sure I left out important details which may hinder input, but I didn’t want this to get too long.
I have a separate photo which is partly amusement value, of the original house wall insulation, “Snell blanket insulation” constructed from newspaper batts. This proudly proclaims itself to be equivalent insulation to “15 inches of plaster”. I’m curious:
1) what chance this has any kind of truthfulness?
2) what kind of R-value might this produce?
Thanks for your thoughts
GBA Detail Library
A collection of one thousand construction details organized by climate and house part
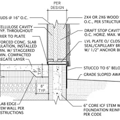
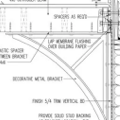
Replies
Easy check, from on top of roof, open up a spot and look. I have Ridgid inspection video cam that could look inside a small hole. I also have moisture meters. Both are inexpensive to buy or rent or buy/rent/return...
Graham,
To answer your last question first: plaster has an R-value of about R-0.3 per inch, so 15 inches of plaster has an R-value of about R-4.5. So, do I think it is possible that Snell Blanket Insulation has an R-value equal to or greater than R-4.5? Sure.
I agree with A.J. that the best way to determine if your roof sheathing is developing problems is to look at it. The roof sheathing near the ridge is likely to be the first to rot.
You made three mistakes, as far as I can determine:
1. You didn't include enough rigid foam on the exterior side of your roof sheathing.
2. You filled your rafter bays with fiberglass batts instead of cellulose.
3. You didn't include a very good air barrier above your tongue-and-groove ceiling.
It's really hard to speculate about whether these problems are serious. The answer depends on (a) your indoor relative humidity during the winter and (b) how much air is leaking through your ceiling into the rafter bays.
Thanks for the tips. Fortunately there has been no sign of egregious moisture accumulation so I'm hopeful I may get away with it, but collecting some data would be good. I expect air leakage into the rafter bays (through finishing nail holes in the poly, which land on the rafters) should be fairly minimal, but of course that's just a guess. Indoor humidity is maintained around 35% during winter.
I think it would be almost impossible to inspect from above, through a metal roof and two layers of sheathing. The top sheathing layer should be immune to problems in this area because of the 1-1/2" air gap beneath it. The bottom layer is what I guess I need to monitor, and I can access the underside through the rafter cavity from the attic.
Oh well, if I waited until I knew enough to get everything right, I'd probably never build anything at all...
Is there a particular time of year to check (like early spring)? I was surprised to see how inexpensive pin-type moisture meters can be ($20-30).
Graham,
Q. "Is there a particular time of year to check (like early spring)?"
A. Yes. You want to check your sheathing in March.