Roxul board used in basement as insulation against concrete wall?

I just watched a mike Holmes episode. He was building out a basement for bar, home theater, gym, etc. against all the walls he used roxul board as an insulation barrier then the walls were framed. I’ve read where Martin Holliday advised against this practice. Who’s right? It makes more sense to use foam or foam board as it won’t hold water. Thanks for any clarification on this topic.
GBA Detail Library
A collection of one thousand construction details organized by climate and house part
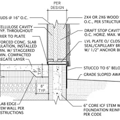
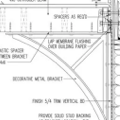
Replies
Without weighting in on the merits of either side, I'd say judging by past experience Martin can sleep easy tonight. Mike Holmes has recommended some spectacularly stupid building techniques.
Hah this is exactly the issue i'm running into. My contractor agrees with the Mike Holmes approach, but the internet and Martin don't agree..I have no idea what to do at this point
I think the normal train of thought is that it is a bad idea to use fibrous insulation (fiberglass, Roxul, cellulose) against basement walls. The insulation will likely make the wall cold, below the dew point, and simultaneously allow air laden with water vapor to penetrate to the wall. The result is sodden insulation and mold. The only way you could make it worse would be to use a plastic vapor barrier on the inside of the wall, guaranteeing trapped moisture. The technical description of this situation escapes me at the moment, but "diaper" is in the title.
IMO, I'd use rigid foam, probably not polyiso (either EPS or used XPS), and make sure the foam can't wick moisture up from the floor.
It's not surprising that most of the people here are fans of Martin's advice ... otherwise we might not be here. So I got curious--is there another discussion group where Mike Holmes fans congregate, and would take the opposite view? So I Googled the keywords, Mike, Holmes, forum. The top three results were "Mike Holmes Built it Wrong," "Mike Holmes is an idiot," and "Mike Holmes Fan Forum Closed." So just on a general credibility score, I think it's pretty clear who is a better bet.
But you can also base it on the engineering principles. If you put mineral wool board there, room air and moisture can permeate through. In some conditions, the dew point of the air can be higher than the temperature of the foundation wall. The result will be condensation on the concrete. It's true that the mineral wool doesn't mind that--it won't rot or support mold growth, and won't absorb much water either. But the water will then run down the wall and puddle at the bottom, unless it's frozen, in which case it won't run down until spring when it thaws. That puddle will get some wood wet and the wood will get moldy. I suppose you could combine the mineral wool with an interior drainage system, but building it without a plan for what happens to that moisture is asking for trouble.
Charlie,
My favourite Mike Holmes moment was watching him checking two kitchen counters by placing a level across them and looking at the bubbles at both ends.
Hey guys, 75% of my basement is going to be finished, for the unfinished space which is my mechanical room and one wall that has my electric panel and main water lines etc, would it be ok to pin roxul directly to the concrete? Or should I not bother insulating the unfinished portion of the basement and just use rigid foam against the concrete walls that are up against the framed drywall and conditioned space? Basically trying to figure out if the whole basement should be rigid foam including the finished and I fished spaces or just where I'm conditioning it, and then what type of material. I'm in. Zone 4-a so I only need r13-15 for my basement walls. Should I drylock everything first? I don't have any water issues, just get moisture down there..Thanks!
Jason R, tell your contractor that you want EPS or a combination of EPS with foil faced Polyiso (being sure that the seam where the foam is exposed is not touching the concrete and I would use a tape to do this) on the inside with the foil facing into the space behind the studs. If he has an issue, then remind him who signs the name on the bottom of the check. With the foil faced polyiso, honestly you may not need a stud wall in front of it if you aren't finishing the basement, but check with you ur local inspector.
Hi Joe,
Thanks, my contractor will do whatever I want, he just won't stand behind something he doesn't recommend. So for the unfinished space I would just pin or fasten the Rigid foam against the concrete and leave as is with the foil side facing in. For the finished section that has exterior walls I would use the rigid foam and then just build a frame in front of it and drywall. The only concern I have with the rigid foam is ensuring its sealed. My ceilings have an existing plaster/concrete lathe that was applied all the way though, so my contractor would have to break through that section in order to spray foam or ceil the section that sits above the basement ceiling and the first floor. He proposed to do blown in cellulose there to fill the cavity, but I'm not sure it's worth doing it. Is it recommended I either do that or have the guy break it open so they can seal on top? I feel like otherwise the foam isn't created a true vapor barrier. Roxul up against the walls in the unfinished unframed space isn't correct/worth doing?
In zone 4 in a basement with no flooding history, go ahead and DryLock everything, then glue a 1"-1.5" of EPS (faced or unfaced) to the wall with blobs of foam-board construction adhesive all the way down to the slab, put an 3.5" wide strip of 1"-1.5" EPS under the bottom plate of a 2x4 studwall, and put unfaced or kraft-faced R13-R15 fiberglass or rock wool batts in the studwall. Tape the seams of the foam with the appropriate tapes, and seal the top & bottom to the concrete with can-foam. Paint the drywall with a latex primer or leave it unpainted.
The EPS forms a capillary & thermal break sufficient to keep ground moisture from wicking through the fiber to the wood, and keeps the wood above the summertime outdoor dew point, and is sufficient dew point control on the above grade section for wintertime interior moisture.
Martin would object that basements can flood (and they can), but fiberglass won't wick moisture upward very far if that happes. You'd still have to demo the wallboard up to about a foot above high-tide and replace the batts from that level down, but it's not an ongoing disaster. If it's walk-out basement it's even less risky, since the tide might not even reach as high as the batts.
Roxul directly against the concrete will wick moisture from the concrete to the wood and drywall. If everything is super-dry in the basement that might be OK, but the top part of the Roxul will retain moisture in winter, and the bottom part will in summer. The risk of mold is higher without the foam from both a dew point and wicking point of view.
The performance of 1" EPS + R15 batt wall will be about the same as a continuous R15.
A 1.5" EPS +R13 wall would do slightly better than a continuous R15- more foam, but cheaper batts.
It's fine to fill the ceiling cavities with cellulose, but only if there's an inch of foam between the cellulose and the concrete. Cut'n'cobbled foam over the top of the foundation sill and covering the band joists (seams sealed with can-foam) is also preferred, but it's better to use unfaced foam there.
I watched a video of the building science guys at the Univ of Minnesota and the gentlemen stated that basement insulation should always be applied to the exterior side of the basement wall. He stated adding foam to the interior side of the wall could allow moisture accumulation and mold growth between the concrete and foam.
Roxul's website states the following setup for basement walls (Concrete, Air/Moisture Barrier, ComfortBoard IS, 2x4 framing filled with ComfortBatt, Vapor barrier (if required), drywall.
I think that idea is that the ComfortBoard IS creates a gap between the framing and the concrete at the top of the wall thereby allowing some drying if moisture gets behind the wall.
http://www.roxul.com/products/residential/technical+documentation
With an air & moisture barrier next to the concrete in the interior it's certainly no better for the moisture content of the wall than a layer of foam, since it doesn't allow the ground moisture an escape path to the interior, so the concrete dries only through the above-grade exterior. As long as there is a capillary break between the concrete and the foundation sill it doesn't matter AT ALL if the concrete has a higher moisture content in a zone 4 climate, but if sufficiently saturated in a zone 6 or 7 climate (like MN) there's a higher (but still bounded) risk of freeze/thaw spalling of the above grade concrete.
If mold can grow between the concrete & foam (but it doesn't if the concrete & foam are clean when installed, since neither is mold-food), it'll also grow between the moisture barrier and concrete.
With the rock wool tight to the moisture barrier on the concrete, the moisture barrier near the bottom of the wall will be colder than the dew point of the summertime ventilation air and will run moist, creating a mold potential. And in the winter the moisture barrier at the above grade section will run colder than the interior air dew point and accumulate moisture. And if you install a vapor barrier on the conditioned space side of the assembly to try to manage this it creates a moisture trap. These problems go away when the layer next to the concrete is air-impermeable foam of sufficient R value for dew point control at the foam/fiber boundary. In zone 4A it only takes about R2.5 for dew point control on the exterior side of R15 on the above grade section, but may take somewhat more for summertime dew point control near the bottom of the wall. An inch+ of EPS is a cheap & effective solution for both seasons, and it gets you to the code-min R15-whole-wall performance. If unfaced, the EPS would offer a reasonable drying path toward the interior, and the moisture content of the concrete near the foundation sill will be lower.
I appreciate all of your answers. For the finished sections of my basement it sounds my approach is going to be drylock the walls, 1.5" EPS against the concrete, frame, fill the frame with either fiberglass or roxul to get to about R15 or so, then drywall. That sounds like my best option. What i'm struggling with is the unfinished section, this area has all of my mechanicals and a bunch of water pipes and electric wires all going to my electrical panel and everything. What type of foam or product would you recommend for that area if I'm not going to frame and use drywall. That's what I thought the roxul would be good for if i'm just leaving it unfinished and unconditioned. For the opposite interior walls that are up against the finished space, am I ok using roxul safe n sound, or should I be using insulation with R Value?
Why are all of the international and local organizations now advising against using XPS and EPS, http://www2.buildinggreen.com/blogs/avoid-polystyrene-insulation ..it looks like EPS is the only one out of the 3 that don't off gas, but now its not advisable to use in most places! I'm not going to frame out the unfinished areas, so no idea what I should do for that area, or if I should even be insulating that in the first place?
Dana, if Polyiso is considered the safer less dangerous version of rigid foam compared to the other two, could I get away with just using a 2" Polyiso R13 panel and forget about using fiberglass or wool? And what about the unfinished space, if I get the foil faced type can I leave that just exposed in a mechincal room
Panel systems?
The standard basement wall insulation advice is rigid foam against the wall (say R15 for most of zones 4-8), followed by a stud wall that may or may not have additional insulation (probably not). Then you have to cover everything for fire protection, typically using drywall. And make sure you put in capillary breaks.
Yes, if you’re not putting in any studs/wiring/drywall in some unfinished area, you could possibly use Thermax.
Seems relatively straightforward (in theory), but kind of a bother, and insulation plus 2x4 studs takes a lot of depth.
Has anyone used a panel approach, using something like [Basement To Beautiful] basement wall panels, or DRIcore SMARTWALL? The Basement To Beautiful panels use graphite-infused foam, 2.5” thick, have integrated but thermally isolated metal strips to screw into, and have molded slots for horizontal and vertical wiring runs. All you’d have to do is screw on drywall.
The 2x8’ DRIcore wall panel has OSB framing with tongue and groove on the face, EPS insulation (3 ¾”), plus pre-primed drywall. It also incorporated wiring channels. No framing required, and no taping micro bevels on the drywall.
It seems like these panelized systems, assuming they use appropriate amounts of rigid foam, would be easier for everyone, but especially DIYs who try to finish the basement later in the life of the building.
Are these just too new for many to have tried, or are the costs a lot higher?
There is an eps that has OSB furring embedded into it as well. I have a sample. You can order any thickness you want, say 3 or 4 inches. It even has wiring chases embedded behind the furring strips. They make these in 4x8 sheets.
For my mechanical room I want to insulate, but there are so many pipes and wires that are practically up against the walls that getting foam behind these sections is impossible, and then on top of that if I want to leave the foam there I need to get specific ones that are allowed to be exposed without drywall. For this area is there any harm in just pinning ROXUL to the walls? I'm not going to have any wood frames or drywall that are near it, and will have my whole basement dehumidifier down there keeping moisture at bay if it needs it, so whats the harm in letting the walls breath but also have some thermal and heat value added. Whats the viewpoint on this?
2 years ago I attached a single layer of ComfortBoard (R6 mineral wool board) to the inside surface of my concrete foundation wall and left it fully exposed. Even at 40% humidity I've had no sign of condensation on the concrete wall nor puddling on the floor. No smell and, when I took off a piece to check this year, no sign of anything growing.
Before insulating it, I sprayed the wall with Concrobium mold control, so perhaps that helped. Also, we have a seasonal low temperature of -5C (24F) here.
I found that my initial choice for fastening the ComfortBoard to the concrete, construction adhesive, was a terrible choice and ended up tearing off the fibre board when bumped.
Orange Great Stuff spray foam has been a terrific adhesive though and is still holding strong.
So, for my climate (4 Marine), it's been a good solution.
Jason- 2" polyiso doesn't get you to code-min R15, but 2.5" does. Going with 2.5" fire-rated Thermax for the unfinished portion of the basement works just fine, as long as the fire rating meets local codes. This blog series is probably worth reading before diving in:
http://blog.energysmiths.com/2011/07/basement-insulation-progress.html
http://blog.energysmiths.com/2011/07/basement-insulation-part-2.html
...and especially...
http://blog.energysmiths.com/2011/08/basement-insulation-part-3.html
For the finished parts of the basement 2.5" of polyiso strapped to the wall with 1x furring through-screwed to the foundation works, and it doesn't have to be Thermax. I used 3" of reclaimed fiberglass faced roofing polyiso in my house, which probably comes in at about R17-R18. (Newer stuff would be R19+.)
Dana, is there a reason why Roxul in the unfinished space doesn't make sense? Any way I look at it I just really don't like the idea of foam. These guys seem to make a non formaldehyde EPS , anyone have any experience with them? http://concreteinsulationsystem.com/
If it's any help on the fastening problem, adhesive *does* work if
you pre-treat the Roxul the right way. I did this on the exterior
of my foundation last year and wrote it up. I wouldn't go whacking
things against it but it's plenty solid, without any additional
external protection. The dirt back against it also helps.
The cinderblock wall is definitely staying warmer inside its fuzzy
blankie in general, but it hasn't really gotten decently cold enough
around here to get the long-view flow measurements I want.
_H*
The rigid foam makes sense to me in the finished area of thee basmenrt where I'm going to frame and drywall and heat. The unfinished area is where I'm trying to figure out why pinning roxul to the concrete and leaving it as is , is wrong. I'm not going to have any wood or drywall near it and it's not going to be heated or cooled, if I want to address some thermal issues there, what's the risk in having just roxul there?
In a zone 4A climate the below grade portion of the foundation will be well below the outdoor air's (and ventilation air) dew point in summer if insulated on the interior. With air permeable insulation that's a mold-risk. You might get away with it in zone 4B or 4C but the risk is much higher in 4A.
I thought roxul itself is mold resistant, what exactly would get moldy? The concrete behind the roxul? all i have in that space is mechanical items and a dehumidifier
I'm not really able to do rigid foam in the unfinished space, i have too many old pipes and wires and objects mounted all over and too close to the walls, and i'm not having them all relocated. It almost sounds like i'm better off leaving the unfinished space as is un-insulated, and just using roxul R15 on the interior walls to insulate the conditioned area. For the finished space that will be up against the exterior walls I'll just use rigid foam, I don't have any existing pipes or wires to be concerned about there. Is that a better solution
Can you do foam on the top portion of the wall in the unfinished space, so you get the above-grade part, that is the coldest in the winter?
Or insulate that portion on the exterior, perhaps digging a foot down below grade.
Jon.
An alternative is close-cell spray foam.
my basement ceiling is covered with a concrete/plaster lathe that sits right below the floor joists. Getting up into that area seems like it would be a big expense and big pain. I'm planning to have my contractor drywall over the plaster lathe, but i had the option of having that cavity dense packed with cellulose, is that not advised either? This is all coming from Dr. Energy
A flash-inch of closed cell polyurethane would be sufficient for dew point control, summer & winter with up to 4" of rigid rock wool on the interior, and it would effectively water-proof the foundation from bulk water intrusion, and would air seal the foundation sill & band joist if you make it a contiuous shot right up to the sub-floor above (recommended.) With 1" ccSPF + 3" of rigid rock wool you'd be at about R16, meeting the R15 code min. Budget about a buck a square foot for the foam.
For best adhesion clean up the foundation first rather than spraying it on a layers of cob web, peeling paint and efflorescence.
All EPS products are "...non formaldehyde...".
Real world foundations and installed fiber insulation are never perfectly clean, and will contain some mold-food. It's common to find mold behind rigid foam insulation applied to concrete or CMU foundations too. But in the case of air-permeable insulation the mold spores have access to the room air, not so with air-impermeable foam. The thermal effectiveness of wet rock wool layers is also compromised, not that it's a large energy use adder in a zone 4A climate.
If you dehumidify the basement to a dew point temperature below the temp of the deep subsoil you won't get get much moisture accumulation from interior moisture drives, but that's another energy cost. If you need to run a dehumidifier in the basement to keep it dry enough it may make sense to install a heat pump water heater to convert that latent heat into hot water inside an insulated tank rather than hot air in a summertime basement.
Hi Dana, I thought in order to create a true vapor barrier I need at least 2" of XPS or EPS directly against the concrete walls? If not and 1" foam and 3" roxul is good, would you do foam, frame, roxul packed in the frame, or foam, roxul, then frame, then drywall? no vapor barrier or poly of course
alright, i'm not going to go with the Thermax sheating for the unfinished space, its not in the budget.
How about this...
I do the Foamular 3" against the exterior walls for the finished basement space which would give me my R15, or the 2" which gives me my R10, and then fill the cavities with fiberglass? OR is that not advised?
Then the 2" foamular (unless I can use 1" ?) for the unfinished space, and put a layer of the roxul wool over that to give it more R value and the fire protection. Does that meet code since Roxul can be left exposed? or does the layer of foam behind it not meet code? Please let me know if this is acceptable for thermal and vapor and all that good stuff. Thanks!
I want something that doesn't use formaldehyde or is greenguard gold certified, thermax is unfortunately neither..anyone know of one that is, and that would work in my example above but also can be left exposed in an unfinished space without framing and drywall?
Jason, I believe I will be going with Owen's Corning Foamular XPS for my basement insulation. I know it isn't the "healthiest" product, but it is greenguard certified. I am not sure if it could be left exposed though.
Jason,
Code interpretations concerning whether or not rigid foam can be left exposed in a basement vary widely. The only person who can provide you the interpretation that matters is your local inspector or building department.