Affordable backfill without sacrificing drainage?

My upslope lot results in one wall of the first floor performing as a retaining wall, with retaining walls extending some distance beyond on each side. About a 10% upslope behind the retaining wall as well. I will create a swale some distance above the house to direct most water away, but I still want to build in protection from potentially significant water during heavy rains.
Obviously it would be best to backfill with ¾” rock, so any water could drain freely to the drain tile at the bottom of the wall. However, the volume to fill is from 4′ to 6′ deep by 10′ high for some 70′ length, which—if rock—will cost a small fortune. There is however no shortage of soil.
Is there some method whereby I can fill a 1′ trench with rock and the rest with soil? I was thinking of building the two layers up at the same time with a plywood panel between that would have straps attached so the backhoe could pick it up after filling both sides. Labor for this also seems expensive.
Alternatively, will a drainage mat handle bulk water in fairly large volume if necessary?
Note that the house will have 4′ eaves, and 6″ gutters draining to daylight on the other side of the house; I think I’m talking about redundant measures here.
Thanks very much!
GBA Detail Library
A collection of one thousand construction details organized by climate and house part
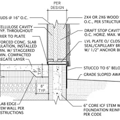
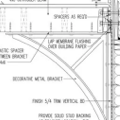
Replies
David,
You are right. There is no benefit to filling that large an area with rock.
The excavators I use routinely backfill full height with a layer of rock against tall walls by simply alternating between buckets of drain rock and pushing soil against the filter fabric separating the two materials. Talk to your contractor and see what they are comfortable doing. Maybe they would prefer to try your panel idea?
Drainage mats may not be able to immediately disperse a very large volume of water, but as long as it isn't allowed it to accumulate against your foundation it doesn't really matter. What makes its way through will be channeled to the perimeter drains without any hydrostatic pressure to force it towards the interior.
Both ways work I've always relied on rock.
How about this: Drainage mat against concrete; drain tile at bottom covered with rock and geotextile fabric; dirt up to about 18" shy of daylight; secondary drain tile covered with rock to daylight at top (rock = 18" by 18" trench)?
Presumably secondary drain tile would handle any bulk water that may get past swale at top of hill (30' away). This would be significantly more efficient for the excavator.
David,
Trench drains work well for surface water. Their weakness is that unlike perimeter (French) drains they are very susceptible to clogging over time as there is nothing to keep the surface debris out of them. For lots that slope down to the house it is a good idea (and here a code requirement) to grade so that the lowest point is several yards from the wall. A trench drain there is a better idea than one right against the foundation.
As an excavating contractor I agree with Malcolm. We alternate filling with dirt and clean stone to cut down on costs. Keep in mind that stone fill exerts less lateral pressure on your walls than most on site fill materials. Have you priced out the stone? It pencils out at about 9 dump truck loads, which cost about $250 per load in my area, and you'd have a few hundred dollars to place the stone. Not that terrible to keep your house dry.
We've had some 20 year storms in our area recently and upward sloping lots can be a real problem. I've seen houses get flooded with mud... Windows blown in, furnaces ruined, etc. Not good. Definitely plan for a redundant system.
Our home is also built into an upsloping hill. It's lovely David, but it came at a price.
We have Form-A-Drain footers, ICF wall, Platon membrane, another drain line, about 3-5' of 2B stone, geotextile fabric, clay rich subsoil backfill, and then dirt. I use the term "dirt" pejoratively, as it's going to be some time before I can work some of this into decent topsoil; it does grow grass though.
I have done a lot of grading to direct water away from the home, and more will happen when we someday build our garage further up the hill.
Our 1st floor trusses are ledger mounted into the ICF and they are turned 90 degrees versus what you might expect for the EW rectangular orientation of our home, so that they "push" against the upside of the hill. This meant additional bearing walls and corresponding footings inside. The structural engineer also added ladder bracing in the truss bays at the NS walls, and we ended up with an informal shear wall in the middle too since we sheathed all four walls of our mechanical room so we could mount equipment, shelves, etc.
I thought we had it all right, but there was one area we might have done differently, and that was the five penetrations for our geo and water wells through that upslope ICF wall. There were sleeves put in the ICF before the pour for these lines, and those penetrations were liberally slathered with sealant once the piping was installed. Guess what, still had water come in after very heavy rains, and darn it isn't there always a cardboard box of something sitting on the floor of a mechanical room.
The good news is that I think I am observing that this leaking around our piping is no longer happening, or at least not as much. I suspect that is because the subsoil and "dirt" is settling into place, and heavy rains do now sheet off around the house as was the original plan. I still don't put boxes on that end of the mechanical room floor though. (And yes it would have been even better if we could have routed those penetrations through a different wall, by making a 90 degree turn in the lines outside.)
I hope you have a stout foundation! Crushed stone with geotextile fabric is wonderful. If you can get "bank run" or "run of the bank" which is a mix of sand and small gravel from river and stream banks, it is great stuff. It is what they use as sub base on highways and roads, too. I made Wunderlich's pit rather profitable on my site. The ROB sand (which is a screened version) is great drainage material too, and is usually at a discount from the material with the random gravel in it. At my business, many years ago I had a similar situation with a very gentle slope but a basement door in that direction facing uphill. At that time in the late nineties when the thunderstorms started getting more severe, I bought about forty tons of #2 stone (not crushed) and filled a dry well and several Swales and covered with geofabric. I pushed the water around the building with a completely hand dug excavation in the native yellow sand. Several hundred wheel barrels later it all came together. To this day it works. However, I think about how when I was in my twenties and early thirties, no amount of hand digging deterred me, unlike nowadays!!!