Moisture control in unconditioned storage space under detached garage

Hello, we are building an unconditioned detached garage on a sloped lot in MD with a lower level that will be used as an additional garage space as well as storage for tools, power equipment, and even kids’ toys and bikes. We would like to do our best to prevent rust and and mold in that space, but we have struggled with figuring out the best approach. This lower level space will be a 25’x35’x7′ concrete cave with a slab on grade, a structural slab for a ceiling, and concrete walls that are on one end fully below grade, on the other fully above grade.
We will set a drain line for a dehumidifier just in case, but we would prefer to build the structure in a way that does not require running one. If there is such a way.
Question #1: Our thinking is to provide mechanical ventilation and eliminate condensation surfaces. Will that be enough in the mixed, humid MD climate to make this space useful for our intended purpose or there is no other way than to build it as air tight as we can and dehumidify?
Question #2: How to build it? What we have so far:
Floor slab: 4″ clean gravel + 2″ XPS foam board + poly vapor barrier under the 4″ slab to prevent moisture from coming up from ground as well as from condensating on the slab surface in warm months.
Footing: capillary break between the footing and the foundation walls (no gravel or insulation underneath the footing)
Upper level slab: no insulation since the garage above will be unconditioned
Concrete walls: the walls will be unfinished and just have exterior waterproofing. But what about insulation? Would it make any difference to try to keep the walls from becoming condensation surfaces? If so, would it make any sense to insulate just the below-grade part of the walls from the exterior with XPS? (full height exterior insulation is not appealing because it would cause trouble for the stone veneer; while interior insulation isn’t appealing because we assume it would need to get covered with drywall per fire code)
We have been struggling to find information on best practices for building unconditioned spaces, so any help would be greatly appreciated!
GBA Detail Library
A collection of one thousand construction details organized by climate and house part
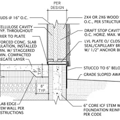
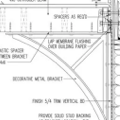
Replies
This is in fact a tricky situation, and one for which finding good guidance is hard.
First the simpler issue: XPS is made with a gas that has a huge global warming impact, more than 1000X worse than CO2. EPS has an impact that is hundreds of times smaller. XPS has a little higher R-value per inch (when it's new), which sometimes is an advantage, but there's no shortage of space under the slab, so you can use 2.5" of EPS and get the same R value as 2" of XPS with the advantages that 1) it's cheaper, 2) it retains its R-value better since it doesn't depend on the special gas, which diffuses out over time, and 3) You avoid the largest climate impact of any building material.
As for humidity control, insulation under the slab isn't as good as putting it on top of the slab, because the slab's thermal mass keep it cool from say a cool night, and then warm humid air coming in during the day combined with the coolth of the slab leads to high humidity. But it's hard to find a garage floor material you can use on top of insulation, so you are pretty much stuck with putting the insulation under the slab.
For the below-grade walls, you could argue that putting the insulation on the interior would make sense for the thermal mass reason, but covering insulation with dirt is cheaper than covering it with drywall.
Then you have the question of whether to insulate the above grade walls. I can see arguments both ways on that. One is that you want the space to be as warm as possible in the summer for lower relative humidity, and that allowing heat through those walls only helps. The other argument is that a big part of the problem for rusting tools, etc. is temperature swings--when you have a load of daytime warm humid air in the space, you'd rather not have it cool off too quickly at night. Overall, I think that insulation would be helpful.
But I also think that sealing the space tightly and running a dehumidifier might not be such a bad idea, energy-wise. If there's no moisture source, the dehumidifier doesn't need to run much.
If you can air seal well (not easy with a typical garage door) and have something to reduce vapor permeability, then running a dehumidifier works very well and doesn't cost much.
When the insulation is preventing the garage from warming up, it has a negative effect on humidity. My guess is no net benefit to humidity.
I'd look for (ie, no idea if it's out there) smart powered ventilation that only runs when dew points indicate it would be advantageous. You really don't want to bring in more warm, humid air when tools and concrete are cold. With this, insulation should be beneficial (heat can be retained longer).
Re: XPS
If below is at all accurate, then where you get the foam from (ie, transport distance) is vastly more important than whether you use XPS or EPS.
http://www.xpsa.com/pdf/CO2%20emissions%20&%20XPS%20insulation4'6'05Final.pdf
XPS might be a reasonable choice for anyone running into thickness limitations (ie, considering less insulation).
Jon,
I think you read the graphs in that report wrong. The "transport" color is about the same as the "cooling" color. Of those two, only "cooling" turns out to be significant. On the scale shown, transport doesn't show up at all.
I've done similar calculations and the transportation wasn't significant. And if it is, EPS has an additional advantage: The final expansion is a relatively low-tech process and there are many more EPS producers spread around the country than XPS producers, so the transport distance is almost surely reduced.
You are right (ie, disregard transport costs) - thanks.
There may rarely be a good reason to use XPS, but on the other hand, there are many ways to make up for the relatively small global warming impact.
You could build a small sunspace with ventilation fans with exhaust and intake. Small hot water panel, or conventional heater attached to a piece of baseboard heat or radiant loop.