Dry unfinished basement subflooring: What is best method to avoid moisture problems?

Putting in a workout room. Floor is currently poured concrete and level.
What is the best way to mitigate possible moisture issues in the future? Some say 6mm plastic sheeting then underlayment then the click floating floor. To me this sounds like moisture will be trapped under the plastic and against the concrete into perpetuity. DriCORE has plywood on top of 1/4″ waffled plastic problem w this is the plywood is susceptible to mold and rot.
What is the best approach. Want to use engineered hardwood or bamboo.
Thank you
GBA Detail Library
A collection of one thousand construction details organized by climate and house part
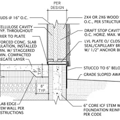
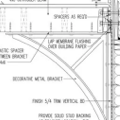
Replies
Go with a floating floor over whatever moisture barrier material the manufacturer recommends, and don't worry about whatever moisture is in the slab. It will stay down there, where it belongs, instead of migrating into your living space. Millions of floors are installed like this, and it works fine.
Pat,
David's advice makes sense. There are different ways to protect yourself from future moisture problems. If you know your basement to be dry, then you are probably willing to accept more risk (and spend less money) than a homeowner with a basement that is occasionally damp.
There are advantages to installing a continuous horizontal layer of rigid foam on top of your basement slab before installing finish flooring, but the foam costs money and affects your ceiling height and the bottom riser on your basement stairs.
In a recent article titled Fixing a Wet Basement, I wrote:
"The usual technique [to insulate an existing basement slab] is to install 1 or 2 inches of XPS or EPS foam insulation on top of the existing concrete, followed by a layer of plywood that is fastened through the foam to the concrete with TapCon fasteners. (If you are still worried that your slab may sometimes be damp, you might want to install a layer of dimple mat under the foam.) When installing this layer of foam, it's important to make the installation as airtight as possible, to make it impossible for any humid interior air to contact the concrete. Seal the edges of each piece of foam insulation with a high-quality European tape, with caulk, or with canned spray foam. If you don’t want to lose the height required for rigid foam, you could try installing a dimpled subfloor product like Delta-FL. (Note that some similar products, notably DRIcore, have mixed reviews from some builders.)"
Thank you.
I will have a dehumidifier maintaining <50% humidity levels. I was looking for a small "just-in-case" solution. Frustrating to me that there is not a product out there that is the silver bullet. I like the idea of DRICore. But it needs to be perfected (top layer - plywood in this case, needs to be impervious to rot and mildew yet non-toxic). Seems like there is an opportunity out there to create such a product.
DriCore or dimple-mats alone isn't sufficient to deal with mold & subfloor rot issues in flooring in every climate. The deep subsoil temperature and average summertime dew point matter:
If the summertime interior air dew point is 60F and the deep subsoil temp is 50F, a rug or cardboard box on the floor has sufficient R-value for that section of subfloor to hit the dew point (even in a 70F basement) and take on water, reaching mold/rot inducing levels. Running a dehumidifier to keep the humidity at 50% RH @ 70F (dew point = ~50F) can keep the subflooring from becoming saturated, but not necessarily below the mold-threshold in every US location, and will suck up 500-1000 kwh/year in power use.
The solution is a modest amount of moisture-tolerant insulation between the subfloor & concrete. An inch of EPS (R4) is good enough for dew point control at the subfloor in the eastern US climate zones up to zone 5A, but more may be necessary in zones 6+ , or if you ever intend to put down things like large 1" foam mats, thick rugs, or a stack boxes. The western -B climate zones are a bit more tolerant due to lower summertime dew points.
http://www.earthrivergeo.com/img/geothermal-article/geothermal-subterrainean-temperature-contour-map.jpg
https://www.greenbuildingadvisor.com/sites/default/files/images/H-T%20Zones%20with%20Cities%20ABC+.jpg
If thickness is an issue you can get by with 3/4" XPS, maybe even half-inch XPS in zones 4 or less (despite a much crummier environmental footprint than EPS), but not polyiso, since polyiso is hygroscopic and can pick up moisture over time.
I love the level of detail/expertise on this forum. In my dealings with GCs in my area, they look at me like I just landed from Space when I ask them questions about what materials they will use and why, are there better products out there, and what their approaches are. I share my research with them and I get some blank looks. Many seem NOT to be experts at all.
To be clear about what I have read so far on here. Layering as follows:
concrete->XPS->6mm plastic sheeting (seams taped)->recommended underlayment->floating floor
is this correct? Thank you all very much
Do you know what's under the slab? Is there insulation already there?
House was built in 1972 is all I know re: the slab
Crushed stone then poured concrete and no insulation on the floor currently (unfinished)
Dana is correctly pointing out that there are two possible issues. One is moisture migrating from below the slab into the room. The other is condensation of interior humidity on the surface of the slab. If the slab currently "sweats" during the summer due to humidity, then that will possibly continue even if you install flooring over a moisture barrier, and moisture might accumulate on top of the moisture barrier, under the flooring where it can do damage.
If you don't have insulation under the slab, adding some on top is good from an energy perspective as well as for condensation control.
What climate zone or zip code are you in?
Bringing up an old floor but wanted to see what folks though about
1" XPS -> SuperSeal Dimple Mat -> carpet.
This would be over my concrete slab in the basement. Under the slab is a plastic poly sheet and gravel.
What about using a radon fan to control the moisture below the slab?
David,
Your proposed floor might work, but might have problems. I'm not sure whether you are thinking for of the dimple mat for moisture control or structural reinforcement. I don't think you need it for moisture control, especially with the poly under the slab, but I don't think it would be a problem for moisture. But structurally it might not be adequate. XPS can be dented by foot traffic. Over time, it can get further and further compressed. Normally a plywood subfloor goes over the foam to spread the load over a wider area, which solves that problem. The dimple mat isn't really rigid enough to do that very much, I don't think. That's my gut feel; if you want to confirm, get a doormat-sized piece of XPS and put dimple mat and a carpet scrap over the top. Put it somwehere you walk regularly and see how it holds up after a month or so of foot traffic. I'm pretty sure you'll see dents in it.
I would also recommend EPS over XPS because EPS is much less environmentally damaging--XPS bubbles are blown with a gas that has 1400X the global warming impact of CO2. Although some EPS is low density and would not hold up as well as standard XPS, there are higher density EPS options going up to as high density as you want.
So my recommendation would be tongue and groove plywood or OSB subfloor over EPS.
Pat Tucci’s Question in Post # 5 remains unanswered. I too would love confirmation on the following assembly:
concrete->
XPS/EPS->
6mm plastic sheeting (seams taped)->
recommended underlayment (my choice is either:
- 2 layers of 1/2” Advantech screwed into each other but floating on rigid foam with 1/4” expansion gap around perimeter OR/
-1 layer 3/4” Advantech if slab reasonably flat & level) ->
floating floor (luxury vinyl planking / tile)
QUESTION 1:
To be clear, is the 6mm plastic layer acceptable to be ABOVE the ridged foam insulation and immediately BELOW the OSB/Ply subfloor layer?
OR....
Must it be in direct contact with the concrete slab?
QUESTION 2:
What negative (if any) would there be making a 6mm poly plastic sheeting sandwich if the basement already has a layer of 6mm poly BELOW the slab and then I put another above? (I will drill an exploratory hole in my 2009 Atlanta built home and expect it already has poly below the slab).
I still welcome an answer as a 6mm poly layer between my smelly EXS rigid foam & subfloor will seal off the styrene off gassing, provide a slip layer between EPS & OSB, and contain any bulk water events above the insulation and slab.