Vapor-permeable barriers and brick walls (MemBrain, Intello+, etc.)

I have a ~100 year old solid brick house in zone 5 – Northern IL ~1/2mi to Lake Michigan. The walls are 2+ courses wide with ~1″ gap between.
We’re slowly rehabbing the house floor by floor. And trying to decide what the best way to deal with air infiltration and vapor permeability. From my reading, it looks like I could put Membrain or Intello+ on the brick directly, then build a (non load bearing) studwall on the inside and insulate that.
Is there a problem with putting a variable perm barrier on a cold surface? .
Any reason to spend the extra on Intello? It seems like the main advantage of Intello is it’s greater strength for installing densepack insulation. We plan on using Roxul for the DIY and so the strength is a moot point.
(Yes, I know I could build air-tight drywall, but for $200 per floor to avoid sealing metal electrical boxes and rigid conduit seems well worth the cost.)
The only wall exposed to rain is the east wall. (north/south are close enough to other houses and gutters, etc that there’s minimal possible rain reaching the brick. The west wall is face brick – glazed and so less moisture loading.
Thanks
James
GBA Detail Library
A collection of one thousand construction details organized by climate and house part
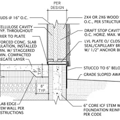
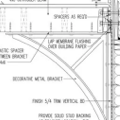
Replies
James,
Insulating an old building with multi-wythe brick walls is tricky, especially in a cold climate. There are many pitfalls.
In general, experts recommend that the safest insulation strategy (assuming that you want to insulate the walls on the interior) is to use closed-cell spray foam, and not much of it -- usually only 2 inches of spray foam. Even that much insulation is sometimes dangerous, and can lead to permanent damage.
For more information, see Insulating Old Brick Buildings.
It's a cavity wall, with a 1" gap between wythes, which means there is no need for the brick to dry toward the interior- both wythes can dry into the cavity, and there's nothing more effective than 1" of air as a capillary break to keep moisture from wicking from the exterior wythe to the interior. The non-structural studwall would be potentially at some risk if butted up against the masonry if the flashing leaks, but using a smart membrane between the studwall & brick would not decrease the hazard to the susceptible structural wood joists, etc.
Putting sufficient R-value as rigid foam or closed cell spray foam for dew-point control for the fiber insulation and skipping the interior vapor retarder entirely is pretty safe. The only hazard areas to pay attention to is where & how joists are being supported by the structural brick. At the support points it's best to use 1-2" of spray foam with no fiber insulation, to keep the joist ends from running too cold (and thus damp.)
Verifying that the cavity is vented both top & bottom is a good idea- weep holes at the bottom and vents at the top can be added if they were not part of the original construction, or were filled in during re-pointing, etc.
Argh. Silly website just ate my longer reply.
Thanks guys for the reply's. I've done a good bit of reading, and a bit more now.
Dana - Would 2 layers of 3/4" EPS (lapped) + 3.5" of roxul be a reasonable setup in your book? I worry a bit about the lower vapor permeability of rigid boards vs membrain/intello. Is that a valid concern?
The brick is pretty sound. There's an old, unused chimney (20+ years) that is in pretty good shape. I had some repointing work done about 2 years ago, and the top ~4' of the chimneys had a thin layer of sand between the bricks, no mortar left and no cap. None had spalled or failed. On the body of the house, the only spalled bricks were where there was standing water from poor grading or long-term failed downspouts.
The mortar is either a very low concrete type O mix, or pure lime.
The walls don't have any (intentional) vents for the middle cavity. The top is mortared over, with a 2x10 on top that the rafters attach to. No weep holes (did they have them for pre-cement heavy mortars?). And brick all the way down - no concrete foundation, though I've not dug all the way down to the footers. Very well draining soil - pure clean sand below ~2', and little/no clay.
The brick doesn't need to dry to the interior, with the possible exception of the areas where the joists are embedded or hung. (The attachment methods matter.). Going with a low-perm foam is just fine elsewhere.
With 1.5" of EPS (R6.3, for Type-II) and 3.5" rock wool R15) you would be right at the minimum ratio required for limiting condensation at the foam/fiber boundary in your climate. The IRC prescriptive for 2x4 construction with wood sheathing in zone 5 is R5 (See: http://publicecodes.cyberregs.com/icod/irc/2012/icod_irc_2012_7_sec002_par025.htm ), so you're probably fine with that stackup, though it's still economic to go higher R than that. Code-minimum is R13+ 5, and with R15+ 6.3 you'd be somewhat ahead of code, there is a long term rationale for more. An R13+ 5 wall has a "whole-wall" R of about R15 after factoring in the thermal bridging (assuming no wood sheathing, and 24" o.c. framing with single headers & plates, since it's not a structural wall). The R15+ 6.3 wall is still less than R19 whole wall- it's worth going a bit higher.
See Table-2 p.10 of this document as a starting point:
http://www.buildingscience.com/documents/bareports/ba-1005-building-america-high-r-value-high-performance-residential-buildings-all-climate-zones
In the zone-5 wall they are suggesting R30, but it would be hard to build that as an interior side retrofit without eating up a lot of space. Going with 2" of EPS next to the brick and 1" of polyiso adds up to about R15, adding a 2x4 wall rock-wool insulated wall inside of that brings it up to about R25 whole-wall at a total depth of 7" between the interior paint and the brick. That's 1.5" deeper than the 1.5" EPS + 2x4 solution, but higher performance. An alternative would be to go with 1" EPS + 1" polyiso, and 3.5" rock wool without thermally bridging studs, hanging the gypsum on 1x furring. That's an R25 wall at 5.75" wall thickness, but could be a bit hard to make a truly flat wall. If you built R15 + 1"iso +1" EPS with the studs thermally bridging the rock wool it comes out at only R20, which isn't terrible, and only a half-inch thicker than your proposed stackup.
Using the same/similar stackup in the basement works too, just put an inch of EPS (and not iso) between the bottom plate and studwall, (and the cut edge of any polyiso) and the slab as a thermal & capillary break. The above-grade portion of an insulated basement wall should be at least R13 + 5 in your climate for dew point control, with no interior vapor retarders other than latex paint on gypsum, so that ground moisture can't load up inside the stud cavity. (An interior poly vapor barrier there would almost certainly be dripping wet inside the wall cavity in summer, even if the basement is pretty dry and well drained.)
It's worth adding exterior venting for the masonry cavity on the exterior side. Depending on how hard the mortar is you may be able to drill ~3/16-1/4" holes into the vertical mortar lines on the top & bottom courses of brick every 3-4 brickso allow convection to take it's course. If the mortar is too hard (probably not if it's a lime mortar) and that approach would compromise the brick, coring 1" holes with a diamond hole saw every 4-5' (both top and bottom), and inserting screened soffit vent plugs (eg: http://www.ventmyhouse.com/categories/Round-Soffit-Vents/ ) in the holes to keep the large insects & small rodents from building condo complexes in there works.
The chimney is probably a real leak point from basement to the attic. Using sheet-metal & duct mastic to build tighter air-barriers where it passes through floors is worth it while you have it open. If you NEVER plan to use it it may be worth taking it out, but if you want to mothball it, capping it with flat terra-cotta tile (and a mortar dome on top of the tile for drainage), bricking up any unused ports into the flue is worth it. An unused chimney still has a stack effect that will depressurize the house anywhere air can pass from conditioned space into the flue, driving air infiltration 24/ 365.
James,
Dana is very smart, and his analysis is well thought-out. But I think that his recommendations concerning insulating your old brick building are overconfident.
There are few building science issues that contain more interlocking puzzle pieces than the challenge of insulating the interior of an older brick building. Factors to consider include the quality of the bricks, which can vary from orientation to orientation; the amount of rainfall that reaches the walls; the quality of the mortar; the minimum winter temperature; the frequency of mid-winter thaws; the number of embedded joists and beams; the possibility of hidden air pathways in the brick wall assembly or between the brick wall and the new insulation; and the interior humidity level in winter.
The best building scientists in the country advise anyone attempting this type of work in a cold climate to stick with closed-cell spray polyurethane foam, and not much of it.
Old brick buildings have been ruined by builders who made the wrong judgment when it comes to interior insulation details. If Dana has the necessary experience to provide the advice he is sharing, hats off to Dana. I don't.
Good luck with your project.