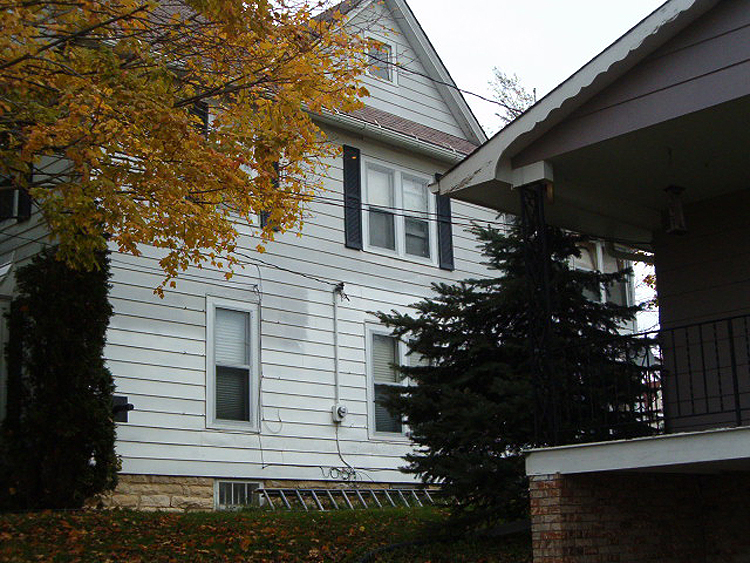
Image Credit: Northeast Iowa Community Action Corporation **Spider webs are diagnostic tools.** Because they need air movement to catch their food, spiders can help you find even the smallest air leaks in your home. The dust collecting in this joist bay is a good telltale sign too. **Keep water out and heat in.** The NEICAC crews have found that putting poly sheeting over dirt floors deals with most of the moisture in a crawlspace that doesn't have noticeable groundwater coming in. In this relatively dry crawlspace they chose to use non-paper-faced fiberglass batts to insulate the walls. In wetter locations they would opt for polystyrene boards sealed in place with spray-foam. **Air seal before you insulate.** Even with good insulation in an attic, air that escapes through recessed lights, unsealed chases, and various other holes can add up to big energy losses. Canned spray foam is an easy solution for filling thin cracks and can even work well for larger gaps. **Dirty insulation means that air and heat are moving.** Air leaking from conditioned space below had blackened the old fiberglass with dirt. After removing this poorly installed insulation and air sealing all penetrations, Jim and his crew topped the attic floor with blown-in cellulose.
Integrated solutions address energy, health, and safety in this state-funded assistance program
Each year, Northeast Iowa Community Action Corporation (NEICAC) uses state funding to weatherize about 100 homes. On this 100-year-old two-story home, and others like it, weatherization crews have performed a variety of diagnostic tests and implemented low-cost, high-return strategies for improving overall energy efficiency — without extensive modifications.
This 2,500-square-foot home is typical for the area but larger than many of the houses in NEICAC’s program. The work done on this house reduced air leakage by almost 50%.
Design approach: integrated solutions
All weatherization projects aim to improve a home’s energy efficiency. The best weatherization programs take a whole-house systems approach, integrating energy efficiency improvements with measures designed to address combustion safety, moisture management, ventilation, and overall building durability. The basic process is tailored to the unique challenges of each house as revealed by diagnostic tests.
Fortunately, this home didn’t have any complex needs, but Jim Perry says that it’s always best to be careful. For example, large atmospherically vented furnaces connected to oversized brick chimneys contribute to high air exchange rates. Although these high infiltration rates exact an energy penalty, they help keep the house dry. “In an old, damp home with an old furnace, if you take that furnace out and put in a high-efficiency condensing furnace, now the furnace is not helping dry the place out,” said Perry. “You have a bigger problem than you had to begin with.”
Evaluate conditions, educate homeowners, and execute a plan
Jim’s weatherization team includes two two-man crews, a coordinator, and an evaluator. First, they evaluate the home. This includes photos, preliminary diagnostic tests, inspecting for moisture and health issues, and checking combustion equipment and appliances for efficiency and carbon monoxide emissions. At this stage, they talk with the homeowner, give them a lead safety booklet, and explain how they approach lead-safe weatherization.
Once the homeowners give permission to make improvements, the crew begins. Most air sealing work is performed in the attic and basement, where it will have the biggest effect. The crew also adds weatherstripping and insulation, and replaces incandescent bulbs with CFLs.
When necessary, they replace energy-wasting refrigerators and freezers. The appliances at this house, however, weren’t bad enough to warrant switching. A weatherization project, including final inspection and testing, can take anywhere from three to six months to complete; this house took four.
How to do a lot with a little
Because state financing is limited, weatherization projects incorporate only the lowest-cost, highest-return measures; despite the wishes of many clients, these measures do not typically include new windows or doors. Ultimately, basic weatherization strategies are able to reduce energy costs and extend fuel assistance dollars for a larger group of people than large-scale energy retrofits might.
Weekly Newsletter
Get building science and energy efficiency advice, plus special offers, in your inbox.
Lessons Learned
Every house has unique challenges
For this home, one of the trickiest spots was an open porch with a roof above it. The wall and floor cavities of the adjacent conditioned spaces of the home have nothing but board sheathing between them and the enclosed porch ceiling. Because the crew realizes that this is a common situation in many homes of this era, these thermal flaws are spotted quickly. The required solution — opening up the porch ceiling so that workers could climb in — was a bit more invasive than most weatherization procedures, but that was the only way to get at these gaps to seal them.
Sometimes weatherization isn't the answer
A successful weatherization project requires a look at the whole house. NEICAC has a set of project guidelines to help crews cover all the bases. For example, if a home's blower-door test shows less than 0.35 air exchange per hour, Jim's crew must install a mechanical ventilation system. This house didn't require one; but if a house does, the team checks for an existing exhaust fan or adds a low-decibel, high-efficiency fan to the bathroom, often with a dehumidistat or a timer programmed to stop after 20 or 30 minutes.
If a home has significant structural, moisture, or mold problems, the team tries to address these first, bringing in additional expertise if necessary. If a problem is extensive, however, simple weatherization may not be the answer. Weatherization contractors must rely on a thorough evaluation and strong intuition when deciding whether it's time to jump in and get to work or to admit that the best solution is outside the scope of their responsibilities.
Further Resources##
The U.S. Department of Energy has a list of state weatherization contacts on its weatherization home page.
General Specs and Team
Location: | West Union, IA |
---|---|
Additional Notes: | **Weatherization contractor:** Jim Perry, Northeast Iowa Community Action Corporation
**Area affected:** 2,500 sq. ft.
##General Principles##
|
0 Comments
Log in or create an account to post a comment.
Sign up Log in