Thermal bridging of the sill plate

I’m planning on building a SIP over timber frame home. The 1st attachment is the wall section detail that the frame company sent me to pass on to my drafting person.
Assuming this makes sense the drafter would reference this but do something slightly different than shown because we plan to use ICFs on the foundation wall. Also, because only 2 walls are buried and 2 are ground level “walkout” walls we want to have the outside of the SIP line up with an OSB sheathing placed over the outside of the ICF so that we can seamlessly carry the siding down the sides of the walkout walls to just above ground level.
One other consideration is I need to make sure that timer frame posts, which will stand on the main floor decking and will be blocked underneath in between the joists, are situated such that they have at least 6in of their 8in depth over the top of the foundation wall. After speaking with the ICF guys about this they suggested using a flared ICF at the top which expands the concrete thickness out to 11.5in. This is shown in the 2nd attachment.
The Timer Frame + SIP company’s detail (see 1st attachment) shows they use a shoe plate inside of the SIP and at its bottom. The shoe plate gets attached to the sill plate before the SIP (which has some of its EPS cut out so it fits over the shoe plate) is lowered over the shoe plate and fastened to it. They say they do it this way so that the exterior OSB sits over the sill plate.
The problem I see with this design is that it requires the sill plate to be carried all the way out to where it is in contact with the outside air, or at least the air in the gap where the siding is stood off from the outside of the building. The sill plate has the joist band and outside of the joists sitting on it. Those in turn are underneath the main deck. As a result this seems to me to be creating a direct thermal bridge from the main deck to the outside of about 2in in height going all the way around the outside of the building.
In addition to the above 2in of the shoe plate is in contact with both the inside and outside of the SIP’s OSB sheathing. The SIP’s interior sheathing is in contact with the joist band’s full height, the thickness of the subfloor on the main floor deck, and the interior wall finishing. So it seems there would also be additional thermal bridging going on there too.
My question is am I worrying too much in thinking that this is not the most energy effecient design?
Should I be looking for a different approach for securing the bottom of the SIPs which will reduce or eliminate this kind of thermal bridging?
My thinking is that the answers are no (I’m not worrying too much) and yes (I need a different approach). The 3rd attachment is one approach I thought of. This calls for trimming back both the sill plate and shoe plate so that the appropriately trimmed SIP can sit both on top of the shoe plate while still having 2 inches of EPS outside of both the shoe and sill plates and also allowing the exterior OSB sheathing to be fastened to those two plates by nails or screws which pass through the exterior OSB and EPS then are secured into the shoe and/or sill plates.
My thinking behind my approach (assuming it is structurally sound) is that it interrupts any direct thermal bridging, leaves only 1 gap (between the top of the ICF and bottom of the SIP) that has to be sealed, and also places about 2 inches of EPS (for about R-7) on the outside of any components that are in thermal contact with the interior (such as the sill plate) above and beyond the meager insulation values provided by the R-1 of the wood itself.
Assuming that I’m not worrying too much and should use a different approach from that shown in the Frame/SIP company detail does my approach make sense or is there a better way to do this?
thanks.
GBA Detail Library
A collection of one thousand construction details organized by climate and house part
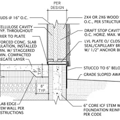
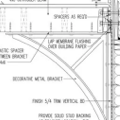
Replies
Hello Jay,
What climate zone are you building in? Unless it's extremely cold there I don't think I'd worry about the thermal bridge at the mud sill. I've used this detail in Wisconsin many, many times in TF/SIP homes I've built. Keep in mind:
• You can (and should) seal the 2X6 plate to the top of the mud sill, and the mud sill to the top of the foundation wall. So if executed well, you should be only dealing with a slightly under-insulated area (I usually figure wood at R1 per inch).
• Your alternate detail would be difficult to execute without compressing the thin band of foam, resulting in an uneven surface. Further, SIPs are typically engineered to bear on both skins, as in the typical framing detail you provided.
• There is a 2X6 buck around each window and door, which technically is less insulated as well. These are inevitable. The thinking is that it's a damnside better than a stick framed wall, with framing taking up 1/3 of the wall area. Again, it's sealed well if executed properly.
As an aside, I prefer running the timber post through the floor system so that it bears on the mud sill. If you do block the post bearing area solid as your detail shows, be sure to orient the blocking with grain running vertically, so that shrinkage doesn't cause the post to "settle'.
Hi Chris,
Thanks for answering.
The site is in Hyde Park, Vermont just north of Stowe. REM/Design thermal modeling calculates maximum heat load for -6F based on Montpelier. My lot got down to -27F during the cold snap a few weeks ago. NOAA degree days for heating are just over 8800
Depending on where you are in Wisconsin my location may not be any worse than this.
I was surprised that the frame design doesn't call for it being brought down through the floor system. I forgot why they said they do it this way. Thanks for the pointer about orienting the wood for the blocking.
I see what you are saying about screwing through the SIP to the sill and/or shoe plates possibly causing compression. If I did go that route then a possible solution to that would be to drill a hole into the 2 inches of EPS left on the SIP inboard of the exterior OSB sheathing and slide a 2in long tubular nylon spacer into it which the fasteners could pass through. That should eliminate the potential for compression.
I think before making any decisions on this I should both talk to the frame guys and go back into REM/Design and see what the thermal modeling I've assumes about how whether or not the sill plate contacts the outside. It might be that the modeling I've done is already accounting for this in the heat loss calculations. If the tool can handle it I can probably model the amount of thermal loss this would cause to better determine whether I need to worry about it.
thanks for the real world feedback.