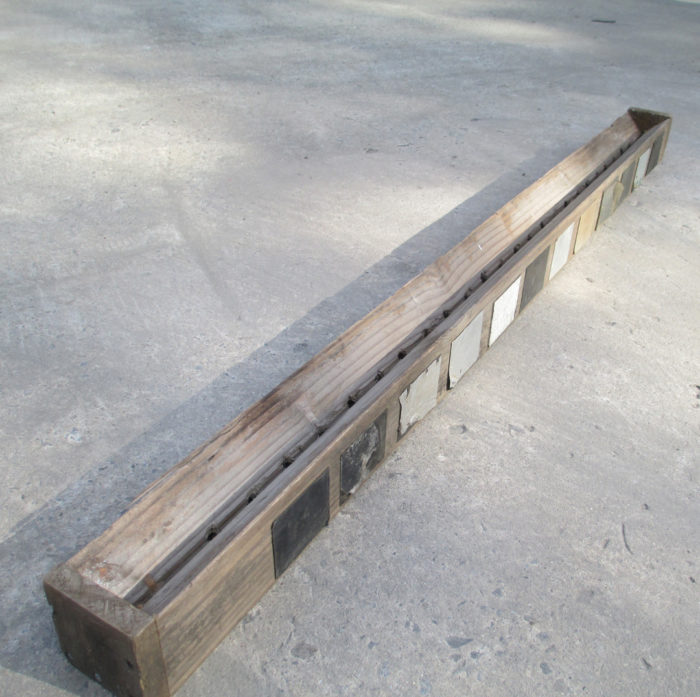
Image Credit: All photos: Martin Holladay
More than 12 years ago, I wrote an article on peel-and-stick window flashing. The article, “Choosing Flexible Flashings,” appeared in the June 2001 issue of The Journal of Light Construction (JLC).
My article surveyed a variety of peel-and-stick products, including products with butyl adhesive as well as products made from rubberized asphalt. As part of my research, I interviewed industry experts to find out more about the strengths and weaknesses of these materials. I also interviewed builders about their job-site experiences with these products.
Back in 2001, I obtained samples of 21 brands of peel-and-stick flashing and performed a backyard test. First, I built a small wooden “bathtub.” Then I drilled a series of 7/16-inch holes in the bathtub and patched each hole with a sample of peel-and-stick. All of the samples were numbered. Fourteen hours later, I filled the bathtub with water.
I hoped that this backyard test would tell me whether peel-and-stick flashing is really waterproof.
So what were the results? One minute into the test, the first of the 21 brands of peel-and-stick showed signs of leakage. Six minutes into the test, four more products began leaking. After 20 minutes, 12 of the 21 tested products were leaking; then the situation stabilized. The 12 leaky products continued to leak, while the remaining nine products appeared to stay watertight. After 45 minutes, I discontinued the test. (For the record, the nine tapes that didn’t leak were Sealtight Air Shield, Dur-O-Wall Polytite PolyBarrier, Vycor Plus Self-Adhered Flashing, NEI AC Homeseal Self-Adhesive Membrane, MFM Building Products Sub Seal 40, Protecto Wrap BT20XL Building Tape, Ridglass Kwikwrap, Sandell Presto-Seal, and International Diamond Systems Tape Flashing.)
I discussed the results of the test with my JLC editor, who decided that the test wasn’t scientific enough to report. In the published article, I alluded to the test without reporting the individual results:…
Weekly Newsletter
Get building science and energy efficiency advice, plus special offers, in your inbox.
This article is only available to GBA Prime Members
Sign up for a free trial and get instant access to this article as well as GBA’s complete library of premium articles and construction details.
Start Free TrialAlready a member? Log in
9 Comments
Heating up the tape helps bonding
If I have a very critical spot where I need the rubberized asphalt tape to stick securely, I've found that heating it to about 120F really increases the tenacity of the bond. So I have a hunch that your test rig saw some bright sunshine and warm temperatures for at least a few days, and the tapes "healed themselves".
In another experience of mine, I had some cold-applied PW BT20XL just peel itself off a vertical wall made of OSB. The temperature during application was around 50F.
A roller should be used to help ensure a good seal on wood.
Nice addition to the tests sifu Martin!
I've worked with a few ( only a very few ) peel stick tapes in the last 6-7 years.
I've had to chance to re-work some of the tapes for various reasons. ( remodeling, completion of old works etc.. )
I can testify that the ones i've used all gain strength with age.
It is nearly impossible to remove asphalt based peel sticks from epdm,tyvek, aluminium and most dry lumbers after only a few years IF 1 condition is met.
HEAT .
All tapes that see sun, facing near south or get their temp elevated by being covered with anything dark colored will almost instantly ( 1 year ) gain this magical stickiness.
So as Kevin pointed out, i now heat ( with electrical heatgun set at low ) and roll ALL of my peel stick tapes. It does work much better with aluminum faced than plastic faced for obvious reasons.
On a side note,
The 2 main tapes i've used are cross-poly faced, and both loose their "face" much too quick to my taste. You can easily "peel" the facing material from most of the 4-5 years old + ( no direct sun exposure ) without too much effort, leaving only an unprotected asphalt layer.
So if you need the tapes to be water tight immediately for some reasons, heat + roll.
If not, roll and let time do its work ( assuming water and dirt is not going to make way before it all sticks up together )
Ah yeah, i would put my money on aluminum faced anytime for longevity vs the cheap plastic facings they all use ( if only i could find some locally :p )
Response to Kevin Dickson and Jin Kazama
Kevin and Jin,
Thanks for your comments. I certainly agree that these products need heat to bond well.
In my original 2001 article, I wrote, "Trying to install a peel-and-stick flashing on a cold wall can be frustrating. Both rubberized asphalt and butyl become less sticky as the temperature drops, and below 40ºF some products just won’t stick. ... The minimum application temperatures provided by flashing manufacturers vary from 10ºF to 50ºF ... These recommendations should be taken as a guide, not a guarantee. An installer can push the minimum application temperature somewhat by storing the flashing in a warm location before use."
It's also a good idea to use a roller. In the 12-year-old article, I wrote, "Many, but not all, manufacturers recommend that their flexible flashing should be installed with a steel or hard-rubber J-roller — the same type of roller used for gluing plastic laminate countertops. Many manufacturers’ reps admit that this recommendation is widely ignored, but doing so carries some risk: When it comes to priming and using a roller, the bottom line is that builders who deviate from a manufacturer’s recommendations can’t expect any support from the manufacturer if something goes wrong."
20 year test and 30 years.
You will keep the "bathtub" and report on the results at 20 years and 30 years right?
Good story and article.
Response to Dennis Heidner
Dennis,
I'll be 76 years old when it's time for the 30-year test. I might just be retired by then. We'll see.
SIGA - Wigluv is a great flashing option
This is a great article, but some of the products on the market are absolutely terrible especially in extreme temperatures. Please add SIGA Wigluv to your study and test at more extreme temps. SIGA's Wigluv product comes as wide as 9" (specifically for flashing) to include 4" and 6" as well.
Response to Todd Collins
Todd,
I have conducted a one-year backyard test of Siga Wigluv, and have written two articles on the results. Here are the links:
Backyard Tape Test
Return to the Backyard Tape Test
For more information on problems with peel-and-stick flashing tapes in very cold temperatures and very warm temperatures, see my article, “Choosing Flexible Flashings.”
Thanks Martin
I saw the backyard tape test articles - thank you and nice work on that. Thanks also for the "flexible flashings" link. Also helpful.
Do you plan any tests for window flashing? I am very interested in learning more about liquid applied and Tape products. When referring to Siga Wigluv, I was referring to flashing windows. However, I believe the black Wigluv can be used for roofs. It is better in UV.
Thanks again, Todd
Response to Todd Collins
Todd,
Q. "Do you plan any tests for window flashing?"
A. Almost all of the products mentioned in this article -- flexible flashing products (peel-and-stick) -- are used as window flashing and are sold by the manufacturers for that purpose.
Log in or become a member to post a comment.
Sign up Log in