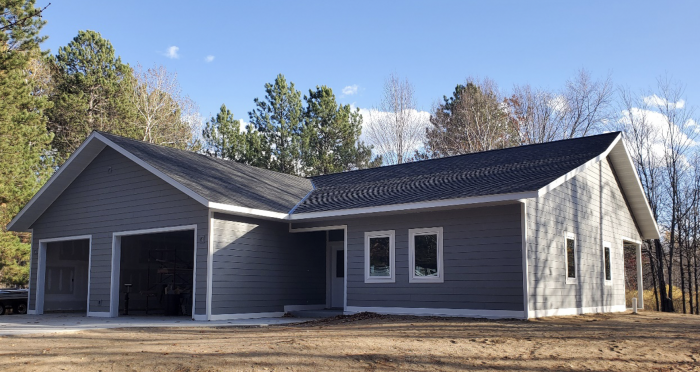
Not every new home built has the budget to be high performance. That doesn’t mean some energy efficiency measures and decisions based on sound building science can’t be added to a design to build a better house.
Recently, I was involved in a project that had a tight budget, but we were able to squeeze an additional 3% in to accommodate a few upgrades that I felt would reduce operating costs, result in more comfortable conditions, and improve the durability of the structure. This build happened during the summer/fall of 2020, right at the time of the lumber price hikes. Luckily, most of the materials had been ordered before the increases.
The home is located in northern Minnesota, climate zone 7. It’s a slab-on-grade, three-bedroom, two-bath, 1550-sq.-ft. ranch-style house. There is an attached, conditioned garage with an additional 720 sq. ft. The main source of heat is in-slab hot water served by a natural gas boiler, which also supplies the domestic hot water. A minisplit air-source heat pump supplies supplemental heating and as well as cooling. There is also a sealed-combustion gas fireplace sized large enough to heat the entire home should the boiler fail. A heat recovery ventilator (HRV) supplies fresh air and is used for spot ventilation—bump switches in the bathrooms increase the HRV’s fan speed when the bathroom is in use.
During the initial planning, I conducted a simple energy model using the Department of Energy’s BEopt 2.8 software. I was looking at two different upgrades. The first targeted energy efficiency; I knew it was possible to improve the airtightness from 3ACH50 to less than 1ACH50. The second was to see how adding exterior insulation—done to eliminate the need for a class I or class II vapor retarder—would affect the performance. Because this home…
Weekly Newsletter
Get building science and energy efficiency advice, plus special offers, in your inbox.
This article is only available to GBA Prime Members
Sign up for a free trial and get instant access to this article as well as GBA’s complete library of premium articles and construction details.
Start Free TrialAlready a member? Log in
22 Comments
A lot of nice air sealing detail. Can you put a rough number on the annual energy saved due to the tested .75 ACH50 vs the code required 3 ACH50. It does not seem like an extraordinary amount of extra time and materials were invested to achieve this savings. The cost of energy is always a factor in ROI calculations and those off the natural gas grid would do well with a building envelope upgrade.
Hi Doug, In this case, the improvement in the air sealing wasn't a large amount of energy savings. The BEOPT program estimated less than $100 per year at today's natural gas prices.
Thanks Randy, great article.
At less than $100/yr energy savings, what is the payback period on the upgrades?
At current energy prices, you're looking at decades. We didn't have a major expense in the air sealing details, the cost for a few rolls of tape and caulks/sealants. The biggest expense was the ceiling strapping detail that keeps all the electrical wires and boxes that would normally be outside the air control layer inside and adds durability to the ceiling air control. That expense would be much more costly today with the price of lumber. We didn't break out the exact costs in the air sealing detail, but I would estimate we ended up around $3-$4000. There are many advantages to air sealing that go beyond energy cost savings, all were taken into account in the decision to spend the time and money on the improvement. Thanks for the question!
Randy,
For educational purposes can you express the Btu savings for this house for .75 ACH50 vs code 3 ACH50. Most all rural MN homes are off the natural gas grid and use propane, heating oil or electricity for heat. I used a volume for this house of 18,160 cubic feet in my calculations including the garage because it is heated. I estimated 9,000 Hdd for zone 7.
The annual savings for .75 ACH50 vs 3 ACH50 are as follows;
$208.72 Propane @ current $1.85 per gallon and 90% appliance efficiency
$235.23 Heating oil @ $3.18 per gallon and 90% appliance efficiency
$273.84 Electricity @ .10 kWh
With the low cost of mortgage money these day,s increasing air tightness especially for homes off the natural gas grid might be the money best spent.
Hey Doug, I think you are close with your estimates with the cost of the air leaks. BEOPT suggested a saving of 2.4 million BTU's per year in reducing the air leakage from 3 ACH50 to 1 ACH50. The blower door number of .75 ACH50 did not include the garage, I would expect the .75 to be a little higher with the garage included. Last I checked, natural gas in the my area is around $1.30/therm and the actual volume used to calculate the ACH was 14,941, without the garage. The efficiency of the boiler that was installed is listed at 95%.
Randy,
My manual calculation using 14,941 cubic feet of volume and 9,000 HDD shows 10,251,284 Btu infiltration heat loss @ 3 ACH50 and 3,417,094 @ 1 ACH50. Either I have forgot the calculation for infiltration heat loss or BEopt is light on the estimated heat loss reduction.
Great article, very cool to see high performance techniques on a "normal" house.
One very specific question - do you drill through the double plate with a masonry bit or wood bit? I did the exact same double plate detail on my garage, down to tacking the first plate in place with tapcons. I marked a spade bit at 2.75" , drilled the plates, leaving a 1/4" of 2x6 to the concrete then followed with the hammer drill. I am wondering if you have a better method.
Hi Tim, we predrilled the holes in the top bottom plate before we stood the walls, then finished drilling with the hammer drill. I have a large spline drive hammer drill that has no problem drilling through the treated bottom plate.
Very informative article. I’m curious about the attached garage. What kind of door was used for car access and were any special insulation or air sealing methods used for it?
Hi Henry, the insulation strategy was the same as the home, R-21 walls which are fiberglass batts, R-60 in the ceiling, blown fiberglass. The air sealing details were also the same with the exception of the inner air control/vapor control. We just used standard 6 mil poly on the exterior walls and lid in the garage area. The common wall between the home and garage is just drywall, no poly on the garage side. The overhead garage doors are 2 inch insulated. Most garage doors are hard to get a good air seal and have much lower R-values than the wall. This door is less than R-10 though I see Clopay has a 2 inch door that is R-18.
A concern I have with attached, heated garages in my climate is how to deal with the increased moisture load from the snow and ice that melts off vehicles during the winter months. We installed a small exhaust only fan that senses both moisture and CO and will automatically turn on if either become elevated.
Thanks Randy. Great idea to use that auto-sensing exhaust fan. I was wondering if there was anything specific that you did (or could do) to improve air sealing at sides, top and floor once the overhead door is in its closed position.
Good question, something I am currently looking for. I have seen where someone installed an inner seal around the garage door, I believe it was the same seal used on the exterior. I have also seen a track system that had "curves" built into the track that forced the door against an outer seal when in the closed position. They are called ThermoTraks, should be able to find them online. I'm currently working on a design for a customer who wants a "high performance" pole structure. Part of the air sealing challenge is with the large overhead doors. Hoping to have a post about those challenges if the build happens.
Can you expound a bit on ventilation. What ERV/HRV does it have, how is it controlled and how often does it run, etc.?
We installed a Broan HRV T90 which can move 35-120 CFM. Minnesota has it's own formula for calculating capacity, this home needed 90CFM intermittent or 45 CFM continuous operation. We chose to set the HRV at a continuous 50 CFM. Instead of using traditional bath fans, we installed exhaust ports for the HRV in each of the bathrooms and added a bump switch to increase the HRV fan speed when needed. I tested each bathroom exhaust ports while in the high setting and found each moving a little over 50 CFM. Not installing the traditional bath fans eliminated a couple holes through the air barrier. The HRV also has a central wall control where changes to how the HRV is controlled can be made. I'm trying to spec better controls for the balanced ventilation systems we install. I've been in many homes where the homeowner needs to make adjustments depending on outdoor temperatures and desired indoor humidity levels. This can be confusing to some, I'm hoping these more advanced controls will make it easier.
IMO that's the way to do ERV/HRV stale air ducting. Is fresh going in to the return duct?
Are you doing any CO2 monitoring? If we'd have done just MN code ventilation we'd frequently have very excessive and unhealthy CO2 levels. Even w/ 2.1x MN code we sometimes exceed healthy levels.
The HVAC control industry is exceptionally antiquated. Our Honeywell zone controller and redlink system are 1990's technology at best. There's a lot of opportunity for improvement in that arena.
The HRV's fresh air has it's own ducting and is dumped in two closets on either end of the building. I was a little worried about the owner having a comfort issue, but he didn't notice the fresh air ducts were even in the closets. We are not doing indoor air quality monitoring yet. This home is only occupied by one person, not too worried about elevated CO2 levels with just the one occupant.
I agree completely on controllers, one of my pet peeves with HVAC in general are controls that are confusing to operate and little or no interface between systems.
Thanks. Interesting idea w/ the closets. Why did you decide to do that?
We decided to place the fresh air dumps in closets to help with comfort. I've talked with a few people that won't run the HRV because of the uncomfortable temps around a supply duct at certain times of the year. It helps if there is a ductwork system to temper the air before it gets to an occupant, this home has no ductwork. Both closets are close to the bedrooms, but not in the bedrooms. First time we did this, seemed to work well.
Nice article and good job on a high quality “regular” house. What is the exhaust only fan you used in the garage?
Thanks, Rick, the garage exhaust fan is made by Humidex, GVS-SD. Home Depot used to carry them, lately I've only been able to find them through WayFair.
Great article BUT thats a poorly overpriced fan. Look intoACinfinity, very sophisticated controller quieter and well built -at Half the price for a 6 inch fan . I https://www.acinfinity.com/hvac-home-ventilation/inline-duct-fan-systems/cloudline-t8-quiet-inline-duct-fan-system-with-temperature-and-humidity-controller-8-inch/?gclid=EAIaIQobChMIjdOb_7Hj8QIVFK_ICh38XgG2EAQYAyABEgLRe_D_BwE
AI-CLT8
CLOUDLINE T8, QUIET INLINE DUCT FAN SYSTEM WITH TEMPERATURE AND HUMIDITY CONTROLLER, 8-INCH
$199.00
4.8 star rating
39 Reviews
would though recommend stepping up to the 8 inch version IF you can easily cut the exhaust hole, esp during new construction. More headroom to exhaust that large space quickly and still only $199. Not many tradesmen carry an 8 inch hole bit though , esp for retrofits; the 6 inch is ok for most people
Log in or become a member to post a comment.
Sign up Log in