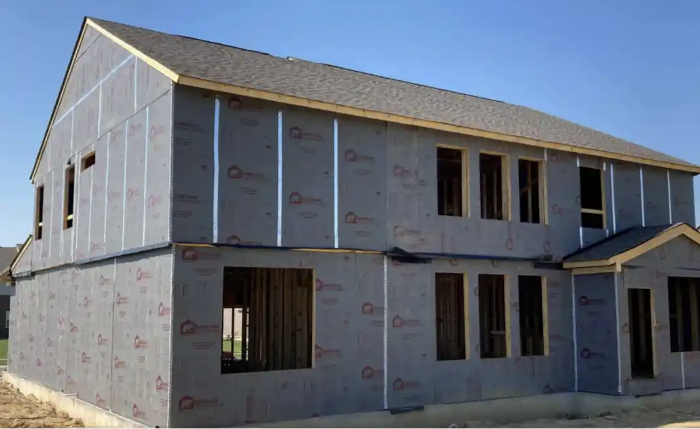
Huber’s Zip System wall sheathing has become a popular alternative to conventional wood sheathing because the system incorporates an air and water-resistive barrier, which negates the need for papering with house wrap (no more sheets torn and flapping in the winter winds). Since Huber obtained its patent in 2005, the innovative panels have become synonymous with high-performance building envelopes. Integrating resin-saturated paper over Structural 1 Oriented Strand Board (OSB) provided a bulk water–resistant coating that remains permeable to water vapor. Air-sealing is achieved with pressure-sensitive tape applied over adjoining panel seams and building corners.
Zip System panels are installed with conventional nails or wide-crown staples, as you would install wood sheathing. Some building experts have expressed concern that nail-head punctures in the water-resistive layer may compromise the system’s integrity. Builders sometimes coat nail heads with liquid flashing or tape over any nails that appear to have damaged the coating layer. However, the ZIP System warranty does not require covering nail heads unless they are driven more than halfway through the panel.
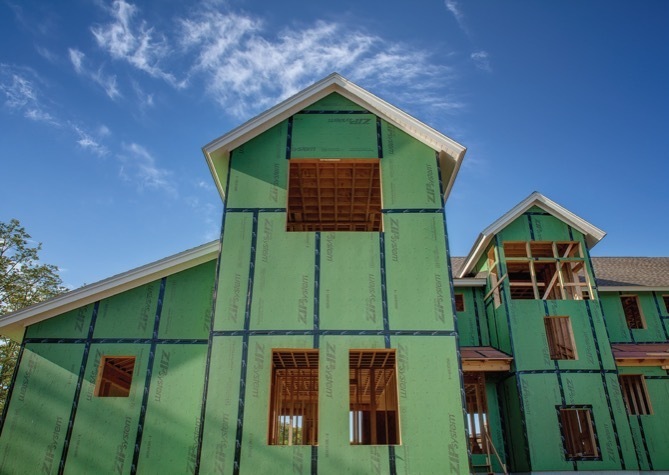
Because OSB is the structural element in the Zip System, when OSB prices climbed, builders began looking for alternatives at a lower cost. Wood panel prices have come down significantly, although not to pre-pandemic levels. Today, a 4×8 sheet of 7/16 Zip panel costs about $27.20 at Home Depot.
Other integrated sheathing panels
Several manufacturers offer alternative brace-wall sheathing that incorporates air and water barriers. This article focuses on those options and newer offerings that also incorporate continuous exterior insulation into a single-application panel.
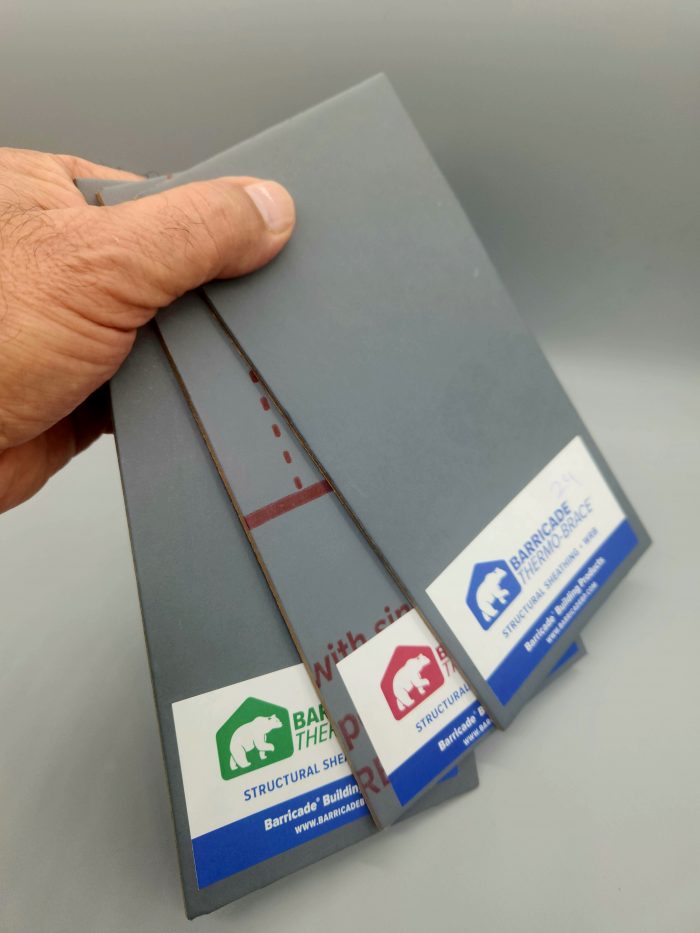
At $18.51…
Weekly Newsletter
Get building science and energy efficiency advice, plus special offers, in your inbox.
This article is only available to GBA Prime Members
Sign up for a free trial and get instant access to this article as well as GBA’s complete library of premium articles and construction details.
Start Free TrialAlready a member? Log in
20 Comments
Thanks. This was informative.
When doing comparisons like this it would be good to incorporate some way to compare products with regard to environmental issues as well, sustainability of material sources, toxicity, embodied carbon, etc. I'm sure this is a concern of many, if not all, of the people who enjoy the GBA website.
Perhaps this is sheathing snobbery - but should we entertain thin-fiberboard sheathing at all?
"The International Residential Code recognizes Thermo-Brace to have a higher shear value level than OSB testing standards."
0. What does that sentence even mean?
1. The IRC doesn't recognize products.
2. There's a caveat in the footnotes of the green/red/blue docs "Minimum ½" gypsum wallboard must be installed as part of the wall assembly" Otherwise the braced wall length is multiplied by two.
3. Comparing themselves to any 7/16" structural panel is a bit disingenuous.
They claim 245 plf at a 3" OC fastening schedule @ 16" OC using 16 gauge crown staples. Zip's 7/16" shear is rated at 240 lbf, at 6" OC perimeter nailing using 8d fasteners. (without the drywall contribution on the other side"). Tighten that down to 3" and it is increased to 450/500 plf, depending on the structure/1 version. Not to mention the out of plane / transverse loading, and puncture resistance, and construction durability.
The price / capability / durability just isn't there, even when compared to commodity OSB, trading at $10 right now.
"It makes sense to explore alternatives to integrated OSB-based materials like Zip System even while prices for wood sheathing remain low. This way, builders can immediately turn to a vetted alternative when a hurricane hits and wood sheathing prices spike." Sometimes OSB makes sense. Other times it does not. I usually install drywall on the interior side of my exterior walls, so this does not seem like a significant penalty. I don't advocate against OSB, only for alternatives when they exist. I have used Thermobrace insulated panels and like them because the insulated OSB is unwieldy. If you build in California or along the hurricane coasts, use OSB or better plywood. By saying the IRC recognizes, they mean ICC-ES reports. The IRC is a model code, but the ICC does provide compliance reports--although Barricade employs a different lab for the brace wall testing. You can find the details here: https://www.drjcertification.org/system/files/DrJ/TER/node/495/ter_1004-02.pdf
Anyone have GP Forcefield experience to share? I really haven't noticed anyone in my local area using it at all, but Zip usage is somewhat rare here too.
I got a sheet to cut up and test, starting with the 3M 8067 and Zip tapes for some baseline (my local Home Depot carries the ForceField sheet but not the FF tapes).
I tried to remove/reposition the Zip tape before rolling it, and the tape peeled the silver WRB facing right off the OSB substrate, starting from the edge. Definitely a completely different WRB material and lamination process than ZIP, almost a post-adhered sheet instead of an integral part of the lamination process.
I'm wondering if that's why the GP tapes are thinner and with a different adhesive system....? It is a very smooth WRB facing though, so a less aggressive tape is likely fine without needed to fill a rougher Zip-type surface profile.
I think it was only $1/sheet more than commodity OSB at the time, so wanted to check it out. Otherwise seems like a very cheap alternative to Zip, if incidental WRB damage can be monitored before cladding.
Wondering the same. Great question.
I'm finishing up a spec house that I framed with Forcefield. I chose it because it was slightly cheaper than Zip and I was REALLY concerned about the budget as it's the first house I've ever built. The fact that Corbett Lundsford used it on his house gave me the confidence to try it because he seems to do everything to 11.
That being said I probably wouldn't use it again. As you say when you try to reposition the tape it usually peels the facer off the board. From what I understand Zip's facer is applied when the OSB is pressed and it seems to me like Forcefield's facer must be applied separately as it comes off so easily.
When I first picked up the Forcefield the facer had wrinkles on it where it wasn't adhered to the OSB. I called GP and the guy told me he didn't know what I was talking about but if the facer is intact, it's fine.
Additionally the grey seam tape (packing tape like) they sell would tear when getting it off the roll if you even looked at it wrong. Perhaps I got an old batch. When I ran out of the grey I used their yellow seam tape plus (more like Zip tape) which worked really well.
I would need to double check this but I think the facer's dots for nailing assumed a vertical installation even though the panels say they can be installed vertically or horizontally which was annoying.
I'm interested in using Zip in the future.
A few comments. First, full disclosure--BSC has had paid jobs with Huber Engineered Woods (manufacturers of ZIP), so you can take our potential bias as you will.
Re GP ForceField: I have only encountered it 'in the wild' once back in 2018. But in the example that I saw, the water/air control surface was a very thin plastic/paper layer that was easily damaged--much less robust than ZIP sheathing surfaces (pictures below). I don't know if that has been changed since then.
Also, the system tape in 2018 was a "packing tape" (OPP) type product--not very robust for watertight sheathing joints. But looking at the current website, it appears that they offer a tape very similar to ZIP tape (FORCEFIELD® SEAM TAPE PLUS, https://buildgp.com/product/forcefield-seam-tape-plus/). I suspect they might be buying their tape from the same source as Huber, given the settled lawsuit for patent infringement between Huber and GP (Huber Settles Patent Lawsuit with GP, https://www.sbcmag.info/news/2017/mar/huber-settles-patent-lawsuit-gp).
"The settlement includes a license under HEW's patents to GP to cover sales of GP's ForceField products with a payment of an undisclosed upfront amount and ongoing royalties."
Lastly, re "thin profile" sheathings. I have used them on projects in the past, but have always felt a bit wary about their strength and durability compared to traditional panel sheathing (OSB/plywood). Then I saw this JLC article on wind storm failures in Texas (A Texas Tornado: Lessons Learned, https://www.jlconline.com/how-to/framing/a-texas-tornado-lessons-learned_o). If you look closely, many of those failures appear to be a similar thin profile sheathing product. I cannot speak to whether this is unfortunate small sample statistics--i.e., the storm track happened to hit a development built with this sheathing. But it did not improve my gut feel confidence in the product.
That looks like the same laminate layer that peeled off during my tape tests, so seems like it is still same product (I did my informal testing this past Fall). That layer was starting to fray and peel at the edges from normal handling, which didn't instill confidence either. It's really a shame, because it's less than half the sheet price of Zip.
Our 1989 house is sheathed with some flavor of ThermoPly, and sounds like the walls move around a bit when it's very windy. I've never heard a modern-ish house make so much framing noise. We're due for a siding and window replacement (both are original), so may consider sheathing options at that point. I can't imagine what it's like to remove Thermoply though, with that very tight nail/staple spacing. Maybe you take it off with a roofing spade......
I have a Master's Degree in structural engineering (not licensed as a PE or SE though). I wouldn't touch thin sheathing like that. I always specify plywood fully sheathed exterior walls. If contractors want to use OSB I insist the price difference is credited to the client.
Also full head common nails only for exterior sheathing. No box nails, no clipped nail heads. Structural failures in shear panels usually happen because of the nail pulling through the panel. Thin panels are far more prone to this.
What do you recommend for a WRB when using plywood? I'm building a small house and wonder if old school tar paper is adequate.
tim_william,
Building paper works fine once it is up and covered. The problem is that it is very vulnerable to damage and wrinkling when left exposed for more than short while.
Joyy, if you're a structural engineer, you also know that most failures in earthquakes and hurricanes are not due to shear walls but to roof-to-wall-to foundation connections. You can achieve this with sheathing, but mostly with the proper hardware. I go on post-disaster inspection trips with FEMA and others, and we generally discover that the failures are attributable to installation errors and not to the use of approved materials. All the "I would never do it this way" or that way obey personal opinion. I would defer to testing lab results. We saw many plywood-clad buildings fail after Northridge, and few had anything to do with the shear walls. Mostly roofs coming off the house, and houses coming off the foundations. I hurricanes, this applies double. I am not knocking plywood or OSB, saying alternatives exist.
I try to be careful and precise in what I say.
"Structural failures in shear panels usually happen because of the nail pulling through the panel."
That is why it would take me boatloads of test results before I'd consider thin panels.
That is ALL I was talking about.
You are absolutely correct that there are seismic structural failures for many other reasons and they are more frequent, soft stories (the subject of my master's thesis at UC Berkeley), foundation bolt issues, unreinforced cripple walls, etc. That wasn't what I was talking about. I was talking specifically, ONLY, about failures within shear wall panels.
If you want to have an argument with someone please don't make up stuff, put it in my mouth, and then argue with me about it. Find someone else to argue with.
There's a reason why Thermo-Brace panels require using nails with very large heads, at half the spacing. I wouldn't risk it. That's my opinion. You're welcome to your opinion.
jgsg,
"soft stories (the subject of my master's thesis at UC Berkeley)"
You must have watched the recent quake in Turkey with interest. It looked like the form of their mid-height buildings with soft stories was a large contributing factor.
Yes, Malcolm. It's really a pity. We know what the problems are. But we're faced with 2 obstacles, a large old housing stock that is sub-standard and in the case of Turkey, probably a lot of recent building that was done in an "informal" manner, to put it politely. I worked in the Middle East for 5 years and saw lots of that going on.
Soft stories are a specific issue, and we agree. Not everywhere has seismic risk. My focus is affordable housing, so I always resist the application of the best and highest cost as the first or only option. I have built many homes in a long career, even with blackjack, and all still stand, including in California. Code is generally enough to guarantee performance if you follow the manufacturer's recommendations and code minimum. All the alternatives here have code approval; some are even in California. Of course, this is a personal choice, too.
I’m concerned with the lack of discussion in the article about the permeability of the various panels. ZIP plywood is permeable, as are their insulated panels. But the materials with aluminum facings are not. Most builders are still covering the interior of exterior walls with poly, and the combination of impermeable barriers on both sides is a recipient of disaster, as we learned in the mold crisis of the past.
The manufacturers offer different products under their lines, each with its perm rating. So the options exist. Even the foil face has perforations. Depending on the product you want to consider, look at the website to read about the perms.
"What do you recommend for a WRB when using plywood". I use Henry VP100 Blueskin as a permeable WRB and as a primary exterior air sealing measure. Tough, easy to apply and works very well. Although it's not an effective air seal, tarpaper is an effective WRB.
On recent projects we've designed, we specify Solitex Mento....And we've always used plywood sheathing, both for its structural value and being less subject than OSB to problems due to water penetration (of course, in a perfect world, there wouldn't be any, but who lives in a perfect world).
Log in or become a member to post a comment.
Sign up Log in