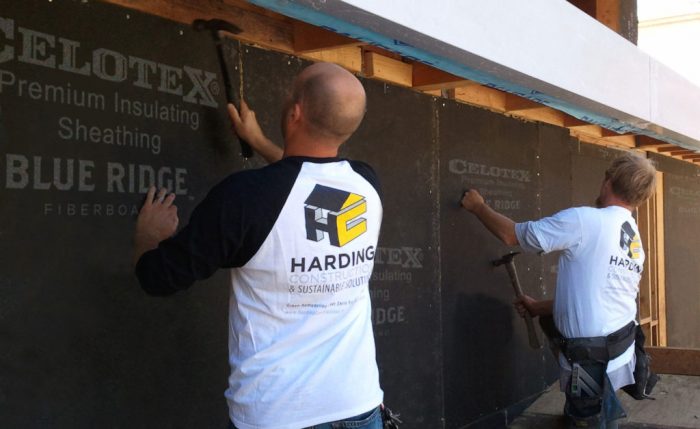
When the price of conventional sheathing shot up to record highs, some builders began using fiberboard as a lower-cost alternative. Meanwhile, manufacturers of fiberboard advertise their products as an alternative to structural bracing. Some products do provide a modicum of shear value (from 170 to 260 plf) when nailed at 2- to 4-in. centers. Fiberboard manufacturers also signal the insulating value of about R-1.3 per 1/2 in. in contrast with OSB at about R-0.62 (Tables of Building Material R-values).
I’m old enough to have installed a lot of fiberboard sheathing. I miss only one aspect of this erstwhile building material, the cost. It’s cheap (about $16 a sheet at Home Depot), and although no longer in widespread use, you can still buy it. But today’s alternative sheathing products, including engineered structural panels, such as Zip Wall Systems, and rigid foams like Halo Exterra, offer benefits that include water-resistance and continuous insulation, which fiberboard does not.
A quick look back
Originally designed as an interior material, fiberboard sheathing breaks down in the sun and rain, curling up and swelling if left exposed too long. The core material, the fiberboard, is not waterproof. To make it moisture-resistant, manufacturers treat the board with a water-resistant surface coating, such as wax or, more typically, asphalt. The problem with swelling and warping comes at untreated edges and cuts. UV rays degrade the surface.
In the past, fiberboard sheathing was called blackjack, gray board, or buffalo board because rather than coated, the material was impregnated with asphalt. It was not the healthiest to cut and handle. The major brands of this material include Celotex Fiberboard, Homasote, and Hardboard Masonite. Although commercial production in the U.S. dates to 1907, the material has existed since 1772, when Henry Clay patented a paper-based fiberboard for interior walls and door panels.
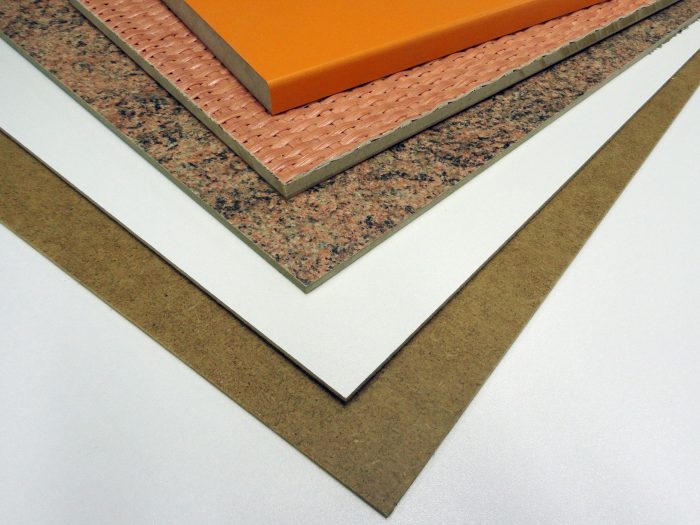
The early fiberboard products were made with fiber materials, including jute, straw, sugar cane stalks, flax, hemp, grass, newspaper, and peanut shells. Nowadays, in North America, these products are manufactured exclusively from wood fiber. Abroad, you can still find the old-fashioned fiberboard in use, made with sugarcane bagasse and urea-formaldehyde. Some imported fiberboard panels may have these ingredients. (For a complete and fascinating history of fiberboard, visit the USDA Science & Technology Program page Early 20th Century Building Materials: Fiberboard.)
Engineering considerations
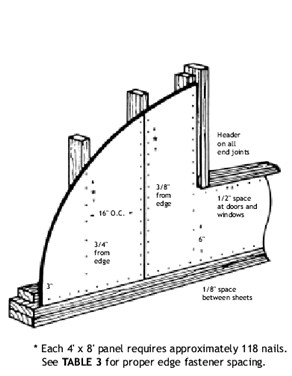
Some structural fiberboard products can replace corner bracing when applied vertically or horizontally to the wall. However, this application does not have i-Code acceptance and will require submitting the manufacturer’s engineering reports. Because the materials are not equivalent to OSB and plywood, this application may not work in high-wind or seismic areas. The North American Fiberboard Association provides a table with nailing requirements for structural applications.
While structural fiberboard sheathing can replace brace-wall sheathing in some applications, a code-compliant wall will generally require let-in diagonal bracing as well. Since the insulation values do not match continuous insulation materials, in many areas, the code may still require a continuous foam over the top to prevent thermal bridging and control vapor permeance through the wall assembly.
What the codes say
The model codes now offer detailed vapor management tables that unfortunately do not reference fiberboard. Generally, the material has an average vapor permeance rating of 5 perms that you must consider when designing a wall assembly.
For the use of non-structural panels with alternate bracing methods, refer to the following: 2015, 2018, 2021 IBC Table 2308.6.3(1) Bracing Methods, 2015, 2018, 2021 IRC Table R602.10.4 Bracing Methods. You will find a bracing methods table here.
Today’s fiberboard products
The Canadian company MSL Fiber makes non-structural fiberboard panels from 100% recycled content that remains 100% recyclable. Their panels contain no formaldehyde or VOCs (volatile organic compounds). And offer a whopping thermal performance of R-3 per in. (rigid foams typically offer R-5 per in.).
Blueridge Fiberboard manufactures a non-structural exterior sheathing panel. It provides R-1.3 per in. and contains recovered and recycled wood fibers. To replace OSB and plywood corner bracing requires let-in-bracing or another bracing method. Cost is $14 per sheet. (This was the one manufacturer who responded to my request for pricing.)
Homasote makes a range of fiberboard products mainly for soundproofing. They do not offer a structural panel but boast that all their materials have a high level of recycled content, up to 98% post-consumer. The company has a table on its website showing the content of each product manufactured.
Feasibility of fiberboard sheathing
Although some builders have re-embraced fiberboard sheathing as a cost-saving measure, I remain skeptical—especially now that the prices for conventional choices including plywood and OSB are falling back to earth. Make no mistake, as an affordable-home builder, I make every attempt to reduce construction costs, but I prefer to use rigid foam sheathing. While foam offers no structural benefit, it adds continuous exterior insulation, from R-5 to R-10. I can use alternative methods to meet the brace-wall requirements, such as shear-nailed 1/2-in. drywall, as they do in Canada and New Zealand, or old-fashioned 1×4 let-in-diagonal bracing. For my dollar, foam surpasses fiberboard sheathing and conventional wood panels.
Many green builders regard foam as a bad environmental performer due to its embodied carbon, whereas fiberboard may contain recycled content. Some of these builders don’t realize OSB has a rather poor environmental profile, too. Without weighing in the insulating energy benefits of foam, plywood and fiberboard represent the greenest choices.
________________________________________________________________________
Fernando Pagés Ruiz is a builder and an ICC-certified residential building inspector active in code development.
Weekly Newsletter
Get building science and energy efficiency advice, plus special offers, in your inbox.
3 Comments
Fernando,
Like you I've used a fair amount of fiber-board but stopped three decades ago - and like you I don't see much point to it now. Apart from shear resistance, sheathing can also disperse vertical loads, act as an attachment point for furring strips, cladding and trim, and offers some resistance to pests entering the walls. Fiber-board does none of these. If for whatever reason the decision is made not to use a structural sheathing, I think it's a better idea to forgo sheathing altogether and just use a robust WRB instead.
The "good old days" of using blackjack. I remember them well. Worse was the asphalt impregnated drywall. I forgot what that was called. Heavy like "well drywall" and yet supposed to be water resistant. Neither of them offered any stability to the wall. Back then everything was 2x4 walls. And braces were 1x4's. Didn't leave much room for insulation. The good kind of insulation from JM with the huge glass splinters in them. And of course what respectable builder used gloves. Yup the "good old days". I don't think I'd ever compromise on using OSB sheathing today. The stability of the wall is far preferable to saving a few bucks.
Thank you for this article! I absolutely agree with your thoughts about OSB. It has a lot of different minuses.
Log in or create an account to post a comment.
Sign up Log in