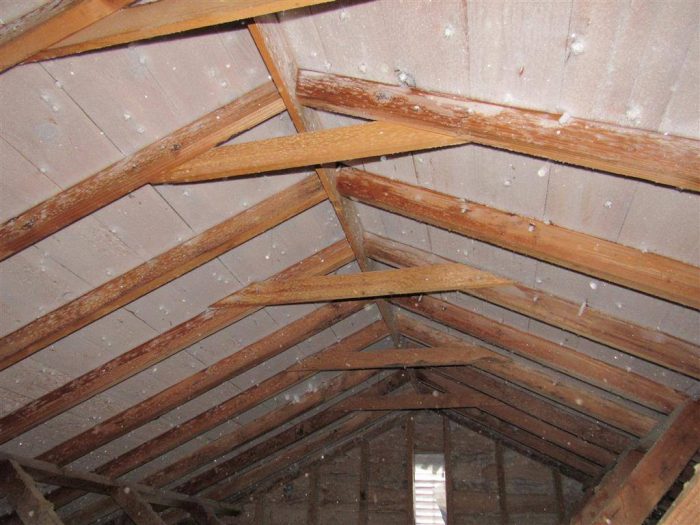
Here are a few recent building code trends:
- Airtightness requirements are becoming more stringent.
- An increasing number of jurisdictions are mandating blower door tests.
- An increasing number of jurisdictions are requiring homes to have ventilation systems.
Among builders, there is some resistance to these trends. During a visit to your local lumberyard, you may hear a builder grumbling: “No one wants to live in a plastic bag. The new airtightness requirements make no sense—these tight buildings are all going to rot. It’s always better to build your walls and ceilings to be a little bit leaky. You need some air movement to keep a wall dry. That’s why walls stayed dry in the old days. Back then, when walls were leaky, we didn’t have as many problems with mold and rot as we do now.”
While these opinions sound like common sense, they are ill-founded. Let’s delve a little deeper into these issues to understand why.
Why, exactly, do you like air leaks?
Builders who argue in favor of leaky walls aren’t always clear about their motivations. To address their concerns, we need to distinguish clearly between two entirely separate issues:
- Issue 1 is a concern about occupant health.
- Issue 2 is a concern about material durability—specifically, a concern about moisture accumulation leading to rot.
Both concerns are legitimate. In this article, I’ll explain why random air leaks aren’t a good way to address either concern.
Ensuring high indoor air quality
We can all agree that “no one wants to live in a plastic bag.” We want our indoor air to be high-quality air.
Most people agree that we don’t want indoor air to be stale or smelly. Others strive to attain a particular technical goal—for example, they may want to keep indoor…
Weekly Newsletter
Get building science and energy efficiency advice, plus special offers, in your inbox.
This article is only available to GBA Prime Members
Sign up for a free trial and get instant access to this article as well as GBA’s complete library of premium articles and construction details.
Start Free TrialAlready a member? Log in
25 Comments
Another great column, Martin! I always look forward to them.
There appears to be a couple of small typos in the fifth paragraph under the subheading "What about rainscreens and vented attics?". The references to "attic insulation" in the PNW and Florida should be "attic ventilation," I believe.
Bryan,
Thanks for your sharp eye! I have corrected the typos. I appreciate your help.
On attic venting. Venting at both the eave and ridge is important as many times the ridge vent will be covered in snow for a portion of the winter. The eave vents do allow for some cross ventilation in this case. Thawing of snow at the ridge vents when all else is cold is a sign of heat loss into the attic.
Doug,
You're right that thawing of snow at a ridge vent is usually a sign that a leaky air barrier and insufficient insulation is creating a warm attic -- flaws that need to be remedied by air-sealing measures and insulation improvements.
You point about the advantages of "cross ventilation" from soffit vent to soffit vent is situational -- such ventilation is beneficial in some, but not all, climates. (The Pacific Northwest and Florida are two examples that I provided of geographical regions where such ventilation can be problematic.)
Yes another good article. These concepts may be obvious for most GBAers, but many still don't think about it this way. And even for those who do understand these things, it can be hard to effectively communicate it with other folks.
I will say that I expect the John Straube quote could cause some raised eyebrows or confusion, since it may 'appear' to contradict prior notions:
“I am with Martin: drilling holes in your sheathing is nutty. It might actually help drying because it will tend to increase air leakage, but that is not a good approach.”
As stated in the article, I think part of the confusion stems from the fact that whether air movement aids in drying or contributes to wetting is complicated and situational. The takeaway is certainly that—on average and with certainty—preventing airflow is safer and more efficient than guessing whether air flow will lead to net wetting or drying.
Despite that being the obvious take-away, I've still often wondered if there is some way to quantify whether air will lead to drying or wetting based on its energy, moisture content, and possibly flow regimes?
I expect that relative humidity of the air is a key component. Very warm air with the same absolute water content as cooler air will have more energy available to promote drying relative to the moisture available for wetting. This seemingly implies that dew-point of the air is less relevant than RH.
Air that comes into contact with an object at or below the dew point of the air will certainly drop some moisture (at the first sign of trouble!) in the form of adsorption/condensation. But if that air stream is persistent and has available energy (which any air that's not saturated will—and the lower the RH, the more available energy) that object could become energized to a temperature above the dew point. So also relevant is how far below dew point the object started.
Perhaps this also suggest that air with a very steady and consistently located stream is more likely to cause drying over time than air that is dispersed into assemblies and cannot concentrate enough energy to raise material dew points?
So the contributing factors I see:
1)RH of the indoor air (if winter) or outdoor air (if summer)
2)Temperature of the susceptible materials in relation to dew-point.
3)Flow regime of the air; steady and predictable paths being less risky than dispersed and intermittent flows (this probably far less so than the first 2).
yeah I suppose we ought to just build tight...
Tyler,
The idea behind the round holes in the sheathing was to allow moisture to escape by diffusion, not air-movement (although we were a bit fuzzy about the distinction) as construction in Canada at the time did emphasize air-sealing through an interior poly air-barrier. The flaw in the idea was of course that vapour diffusion is proportional to the area of each material, so the amount of moisture able to diffuse through the holes covered by only a WRB was inconsequential.
Thanks Malcolm.
Yeah I took a look at that thread and came to that conclusion. Another reason why Straube's quote is a bit confusing in isolation. He did cite air movement, not diffusion, in that quote after all.
Bad assumptions can be made when we view words, even from experts, and don't understand what underlies their words.
I gotta say, fun to read that from 2012!
Tyler,
You're overthinking again! We need to come up with construction details that are robust in a variety of conditions; we don't need to install RH sensors, absolute humidity sensors, temperature sensors, and wind speed sensors that operate mechanical dampers that open and close our soffit vents.
(Of course, I'm not implying that you were proposing such a complicated Rube Goldberg device... just saying that we don't need to perform every possible calculation to build robust buildings.)
Martin,
I just lost a job because I suggested that the client's proposed long 2/12 shed roof wouldn't vent adequately. Builders he spoke to told him I was nutty too.
Malcolm,
Every one of us in the GBA community has been called "nutty" multiple times -- sometimes because we're nutty, and sometimes when we aren't.
Martin,
Guilty as charged. Might be my MO ;)
But to be clear, I expound in this way to better understand underlying principles, not to suggest we need to analyse every little detail for construction purposes. That's why I agree with your main point—build tight and feel confident you're safe. My long post could be viewed as the headache one can avoid by doing so :)
And I understand that there is an element of counter-productivity to making something overly complex. I'm just trying to stock as much ammo as possible here.
In my defense, I do think valuable insight can be gained (if folks are so inclined and interested) from understanding the finer points.
For example:
Armed with the assumptions I've made, one can see that old buildings have at least a few things going for them (I know many already know this):
1) The temperature of the sheathing would be kept higher in a poorly insulated building (closer to, if not above, the dew point of the interior air). And
2) A REALLY leaky building is losing enough air (and moisture with it) that the RH is being kept lower. So there is actually more energy to dry.
In turn, this may help to explain to the old timers why old, super leaky houses were, in fact, drying through air loss, while modern efficient envelopes are quite possibly wetting.
Some might choose to simplify it to something along the lines of: 'an old building is using excess energy to aid in drying.' And perhaps that suffices.
Well, I've got to get back to work filing that patent on the quadra-sensor mechanical soffit damper.
Tyler,
You've made a lot of good points. As you note, old leaky houses had a high rate of air exchange -- so the indoor air during the winter was very, very dry. That means that in the old days, exfiltrating air carried less moisture per unit of volume than exfiltrating air in a more modern (tighter) house.
The internet never forgets. Yep, got called nutty by both Martin and John Straube. On balance it turned out to be a good experience - and of course they were right.
Too Funny! Don't worry Malcolm (not that you are). You've long since redeemed yourself by helping countless people in the GBA community.
Rick,
It was a good reminder to be open to new information, even if it challenges some of the things you consider core knowledge.
Malcolm,
In this article, I never mentioned your name! Thanks for all of your valuable contributions to GBA.
Martin,
Not at all. Much of my life seems to be devoted to increasing the number of self-depreciating stories I have available for use when invited to parties. That was just one of hundreds.
My wife and I are currently (on hold due to COVID19) building a home. Like most people, I started the process totally ignorant of what it takes to build a good home - focusing on ceiling lights and high ceilings, etc.
Almost a year and a half ago,I happened across an interview of Rob Dunn who wrote “Never Home Alone”. This is a nonfiction book about our homes as an ecosystem. So I read the book and there was a discussion on mold and gypsum board. This prompted a simple google search about mold in homes which lead me to a GBA article that started with a picture of a nice piece of bleu cheese!
https://www.greenbuildingadvisor.com/article/common-sense-mold
Since then I paid for a GBA subscription and learned as much as I could to make sure we detail our home following building science principles. I am fortunate to have a GC who is patient with me and interested in making our home’s construction follow these principles. We are making it as tight as possible. It may not be as ‘green’ as it may have been if I lost my total ignorance (of building science) when we were in the design phase, but it’s better than it would have been.
Thanks, Martin, for introducing me to GBA. I hadn’t heard the term ‘building science’ before ‘discovering’ GBA. This latest article approaches the topic nicely contrasting the breathing building mindset with air tight construction. Much appreciated.
Alan
https://www.amazon.com/Never-Home-Alone-Millipedes-Honeybees/dp/1541645766/ref=nodl_
Alan,
I'm glad that you have found articles on GBA to be valuable. Welcome to the GBA community.
By the way, the book you mention (Never Home Alone) was reviewed in 2018 for GBA by Peter Yost. Here is a link to his review.
Is there a tipping point (ACH50 number) where the home is considered 'tight enough' and further efforts to make it tighter have diminishing returns?
Thanks
Alan
First, thanks Martin for this simple explanation that finally crystallized in my mind: "In a leaky house, the air exchange rate will be high in windy weather and very cold weather (because the stack effect, a powerful driver of infiltration and exfiltration, is strongest during cold weather), but the air exchange rate will be low when winds die down or the weather is mild."
Re Tyler Keniston's remarks about sensors and your serious caveats...for new buildings of course I understand that sealing details are better than mechanical remedies. But for a retrofits I have not ruled out a differential-dewpoint controller for a crawlspace in mild but marine climate zone. So far it appears infeasible or unwise to include that crawl in conditioned space.
TK, I think it would be hard to patent bec . they already exist, mainly in SE US and various European locations (commercial anywhere I think can have similar or more complex vent controls). And there is also open source software and hardware. I wonder if this is interesting to DD, or maybe he can rule our the idea based on first principles, again I'm mainly talking retrofits and unconditioned spaces.
David,
The main argument against installing fans wired to a differential-dewpoint controller to provide powered crawlspace ventilation is that complicated systems eventually break -- usually sooner rather than later, especially if the equipment is home-brewed. No one will ever maintain this type of system, or even notice when it stops working. And it won't be cheap.
David, on two project now I have spec'd mechanical crawlspace ventilation for sealed crawlspaces. Both were in Maine, one new and one renovation; we have cold, dry winters but also warm, humid summers and air conditioning is relatively rare. Both included an inline fan and registers to the living space, controlled by a thermostat and a humidistat wired in series. I'll cut to the chase: I would only use such a system if there were no other good options available. They are tricky to get right and too complicated for homeowners to maintain.
To be clear (in case its not), I was never advocating for sensors and solenoids, etc. Though I see nothing wrong with an RH sensor here and there—maybe in the bathroom, in the woodshop...
I was just interested in the science, thinking it might help inform certain decisions. Turns out psychrometry is both fascinating and complicated.
Thanks to all for that. Martin inspired me to look at warranties for differential dewpoint controllers. He's right, they're not great, 2-3 year typical. :<. Maybe 5 years if someone could get the Honeywell to work in a residence, or supplement SmartVent with additional stuff to do balanced instead of negative pressure. Roughly speaking I think a 100 year old house needs a 20 year plan.
Tyler, having sensors around has helped me understand particulate and humidity migrations through leaks. Decoding the charts is not my favorite activity but it seems to me the sensors also confirmed some indoor humidity improvements that came with envelope repairs/remediations. Acurite seems to have the cheapest multi-sensor mesh network, I think you can expect to cover 6 places interior + leave 1 sensor outdoors for under $200. (The software forces you to label them as outdoor sensors if you want dewpoint, but with that workaround you automatically get a time series for dewpoint along with temp and humidity.) The particulate sensor I borrowed for a few weeks, would like one but that's maybe another $200 all-in. I covet the PurpleAir indoor-outdoor bundle.
Log in or become a member to post a comment.
Sign up Log in