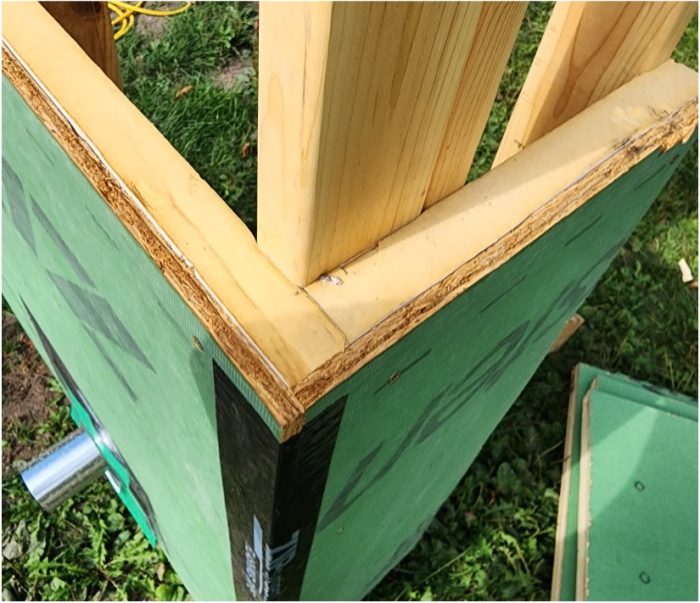
In the first post of my three-part series on continuous insulation (CI), I covered building codes and some basic building science principles and how they relate to CI. This second part will discuss some of the difficulties builders have with getting the details right.
I remember my first time using exterior CI on a new home. I had many questions; where to put the WRB, how to attach the cladding, how to address the windows and doors, and how much insulation to use. That home is over 12 years old without any complaints from the homeowner. Would I change some of the details I implemented on that first project? Absolutely. But the design and execution seem to be performing well.
What I would do today would be based on whether I was dealing with new construction or a renovation. Other factors would be budget, the construction crews’ experience level, and how the homeowner intends to use the building. For example, maybe a family member has a health condition that requires higher than average indoor humidity, or maybe the homeowner is planning on an indoor swimming pool. I would approach those projects differently than I would building to code minimum requirements for CI outlined in Chapter 11 of the IRC.
Common materials used for continuous insulation
There are four main materials used for exterior CI, plus a new one just now coming onto the domestic market. Most installations will include some sort of rigid insulation, but fibrous insulation can be an option with certain designs and assemblies. (I won’t be covering the fibrous options in this post.) In no specific order, the most commonly spec’d materials are extruded polystyrene (XPS), expanded polystyrene (EPS), polyisocyanurate (polyiso), and rigid mineral wool (e.g. Rockwool’s ComfortBoard 80). Another product that has been around for a while in…
Weekly Newsletter
Get building science and energy efficiency advice, plus special offers, in your inbox.
This article is only available to GBA Prime Members
Sign up for a free trial and get instant access to this article as well as GBA’s complete library of premium articles and construction details.
Start Free TrialAlready a member? Log in
7 Comments
A bit of an esoteric concern maybe, but when I design I usually try and stick to 16" or 24" increments when possible. With exterior insulation, I wonder if it makes sense to include the thickness in those considerations - especially if using Zip? I already do that with decks - dimensioning them 2" less that those increments to allow the decking to overhang.
Great series, Randy, thank you; I look fwd. to Part 3. It reinforces what this DIYer building his own house has already learned through painstaking research thx to GBA, the resid. code, Joe Lstiburek, etc. ....plus I'm learning a few new facts here too. Question, though, I don't think you've addressed (maybe you will in Part 3?): so where exactly does the WRB go in the whole wall 'sandwich'? For my North Carolina zone 3 house I plan to do 2x4 @ 16" walls, then 1/2" plywd sheathing (is taping necessary?), then 1-1/2" EPS (= R-5.4) even though no CI is req'd. in my zone (under the 2018 code version I'm permitted under nor even the soon-to-adopt 2021 version), then vert. & horiz. strips of 1 x 1 lath for a rainscreen for my vertical T&G 1x8 wood siding. As far as the WRB (have already bought 475 Supply's Mento 1000), I'm told that goes OVER the foamboard (but of course under the rainscreen lath).....that make sense to you? Related question is: Don't all these fastener penetrations thru to the studs (from whatever: insul'n board / rainscreen / maybe siding itself) compromise integrity of WRB's whole purpose??
Is there any concern for the shrinkage of foam over time and the viability of the brace wall as the sheathing becomes loose from the framing?
I'm assuming you are talking about Zip-R panels. That would be a great question for Huber. Some of the research I've conducted shows shrinkage rates of about 1/4" over 4' of product for polyisocyanurate. Assuming this ratio to also be relevant to shrinkage in thickness, we are talking somewhere between 1/64 and 1/128 of an inch.
Interesting on the polyiso shrinkage, Randy. So, some shrinkage comes with aging of the sheet? We may have to age it like cheese before using. I have used polyisocyanurate quite a number of times and like it as an exterior insulation. An R-21 wall with 1 1/2" polyiso exterior is quite a good wall in southern MN.
Doug
Great series Randy.. many, many THX.
Building our forever home, new construction in climate zone 4Marine (Portland, Oregon) and planning 2x6 structure(R23 BIB fiberglass), ZIP sheathing (air barrier), GPS 1inch (R5) continuous insulation... and then a 1x3 rainsreen and some Hardie lap siding.
So, the ZIP sheathing is warmed by the R5 GPS but you always want some venting incases of low temp condensation. This structure is designed for 30F (ASHREA 99) but we get 20F on occasions. The HALO GPS specification is 1.32 perm allows for drying to the exterior. This particular GPS product skin is perforated and falls into the class 3 vapor barrier category but IMHO it's closer to a class 2 vapor barrier (class 2 to class 3 transitions at 1 perm).
I initially planned a vapor open assembly (1.5" rockwool at R6.3) but rockwool is currently on allocation and not available in Feb 2024. Plus the demand of Rockwool has driven the price point to $1.5 psf and GPS is $0.65 psf in my location. So, this seems like a no-brainer for choosing a GPS solution....
My three hesitations are first; when hanging concrete siding on the 1x3 furring, will the 10psi compressive resistance of GPS be sufficient to prevent racking in some weird way. Second, is the 1.3 perm specification real world accurate. I want outward drying. Third... going to all the trouble to install 1" (R5), should I spend a few more dollars for 1.5" getting R7.5? Rockwool was my perfect solution but I need to be flexible as building is this spring....
I'm a HUGE fan of GBA and appreciate all the insights and comments from GBA experts.
CH, I’m interested in what you ended up doing. I’m also in Portland, OR, new to GBA, and planning upgrades to my existing home. The ability of GPS to dry outward interests me.
Have you looked at ThermalTight? Their specs say it has 3.5 perm. Much better than the Halo at 1.32 perm. The price point is much higher though. I got a quote last year at $1.20 psf for 1”. That does include the WRB built into the foam sheets, but not the needed seam tapes to finish flashing and the air barrier. Considering it removes the need for ZIP it may be cheaper. They didn’t have a northwest supplier when I talked to them last year though, so shipping costs added to the price significantly.
I’m curious where you are getting the Halo? I haven’t shopped around for what is available here yet.
Thanks!
Log in or become a member to post a comment.
Sign up Log in