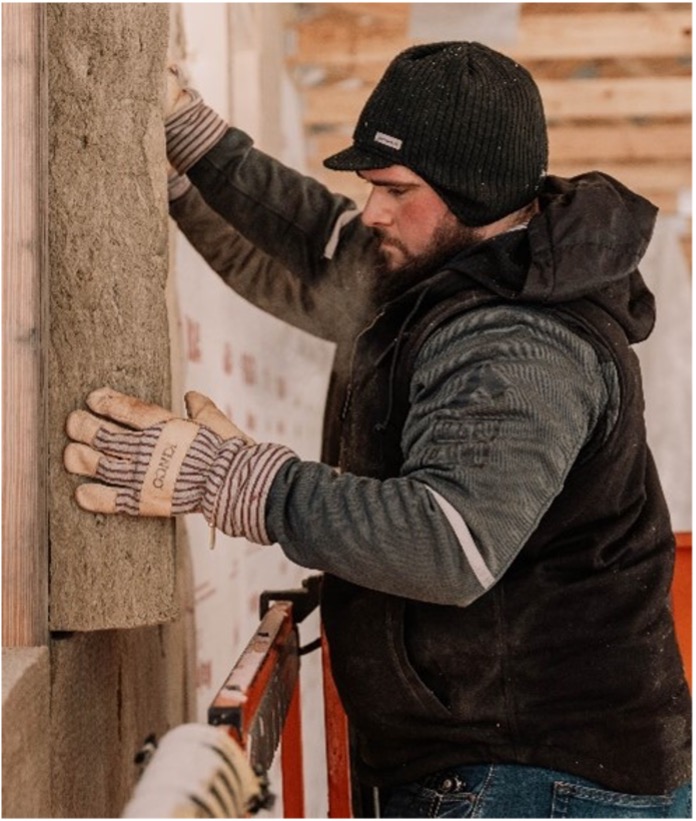
I recently wrote a two-part article covering the pros/cons and code requirements for continuous insulation. In the first article, I referenced table R402.1.3, which is found in Chapter 11, Energy Efficiency, of the 2021 International Residential Code (IRC). The table shows the R-value and U-factor requirements for several building components and assemblies. The data I referenced was taken from the first edition of the 2021 IRC. In the article, I stated, “Climate Zones 1, 2, and 3 are unique in that they have the option of cavity-only insulation. Climate zones 4 through 8 are required to have some amount of continuous insulation.”
GBA reader “jimmybpsu” pointed out in the comments section of the article that he had a different version of table R402.1.3, which allows for cavity-only insulation in Climate Zones 4 through 8. As it turns out, he is right.
Why does my hard-copy code book show one option while the reader’s edition says something else? It’s the difference between print- and web-sourced information. The digital version of 2021 IRC’s chapter on Energy Efficiency allows you to toggle between two editions of the same code. The first version includes table R402.1.3 and is the same as my print edition; the second version shows an updated table allowing for cavity-only insulation.
Why are there two versions of the code?
This begs the question: Why was there an update in code between normal code cycles? I reached out to Glen Mathewson, who writes a regular column, Know the Code, in Fine Homebuilding magazine. He responded:
“The short answer is errata. The staff at the International Code Council (ICC) has one heck of a tough job combining all the approved proposals, including changes made to the proposals during the hearing process. Many proposals overlap the same code sections. So human error always happens. The first printing of a code is always the worst one. If you can wait to purchase, wait until the second printing where mistakes are fixed. ICC provides all errata for all editions from 2000 here. More importantly, you can submit errata when you find it. I submit all the time. At least once a month I find something.”
I’m glad jimmybpsu brought this to my attention. Now I know that the different versions of the table were not a code change between code cycles but rather the result of correcting human error.
How is R-30 achieved with cavity-only insulation?
So long as we are on the topic, let’s discuss the R-30 cavity-only option. Here’s the updated R402.1.3 table:
With 2×6 framing, the only way to get R-30 using common insulation strategies is with closed-cell spray foam. Moving to a 2×8 wall allows for high-density batt options like Rockwool’s ComfortBatt, which achieves R-30 in a 7-1/4-in. batt.
Several manufacturers of high-density fiberglass batts can also fit in the 7-1/4-in. cavity. Standard-density mineral wool products and fiberglass have lower R-values per inch; using these products requires a 2×10 wall. Dense-packed cellulose has R-values ranging from 3.6 to 3.8. A 2×10 wall cavity will be required when using dense-packed cellulose as well. How about open-cell spray foam? With R-values ranging from 3.7 to 4, this will require a 2×10 wall too.
Technically, to meet the R-30 cavity-only option in climate zones 4 through 8, the insulation material will need to have an R-value of 4.14 per inch to be used in a 2×8 wall cavity. Otherwise, either a 2×10 wall will be needed or a combination of closed-cell spray foam and fibrous insulation, aka the flash and batt method.
In my opinion, the industry would have been better served by lowering the cavity-only option slightly to allow common, less dense insulation options to satisfy the code requirement. Then again, maybe the overall goal is to encourage the use of continuous insulation, in which case the R-30 decision is brilliant.
____________________________________________________________________
Randy Williams is a builder and energy rater based in Grand Rapids, Minnesota. Images courtesy of the author.
Weekly Newsletter
Get building science and energy efficiency advice, plus special offers, in your inbox.
21 Comments
I haven't read the entire series of articles so please excuse me if this is covered elsewhere. I just wanted to point out that the draft 2024 IRC is out and about and it seems to be stepping wall and roof insulation requirements back from the 2021 figures to the 2018 figures.
It turns out my continuous exterior is not as continuous is I thought.
The framers decided for me that they should remove the foam where the deck attaches to the house. The insulation contractor wanted to stuff the band boards with fiberglass. I knew it was not the best idea but being zone 4 with continuous exterior insulation decided not to fight that battel and the band board is fine where there is exterior insulation. I happened to remove some of the fiberglass behind the deck and find mold.
Just make sure your insulation is continuous.
Walta
Walta, deck codes don't allow you to attach a ledger through foam, so you have to either use stand-offs or make the deck freestanding. I seem to run into this issue on every project I do with exterior insulation and it's always a bit of a challenge.
Free-standing is the way, In my opinion!
Walta,
A house designed with continuous exterior insulation needs a detail for the attachment and waterproofing of the deck ledger called out, or the framers have no choice but to omit the insulation there.
Walt, can you add more detail on exactly where the mold was found?
The mold was on the band board in between each joist where the deck abuts the house.
Walt
I my major city, Rock Wool doesn't exist as a buying option.
Spray foam is questionably installed when installed thick.
A lot of people seems to think rigid iso/EPS is found equally easily with foil or foil-less configurations--they aren't.
Cathedral "C" fluffy insulation doesn't exist in my major city.
Maybe the question should by, if code is hoping for energy improvement why not make code start in the correct order first--make walls required 2x8 or greater first. Once standardizing on a wall cavity material because less driven to a product that, honest guys, isn't half as available as some on here believe.
A double stud wall is another way to achieve higher R value walls without continuous exterior insulation. Two 2x4 walls with a 1.5” gap between them would work if filled with cellulose at 3.7 R/inch. The insulation in the gap is actually continuous insulation, but it’s located between the 2 walls instead of on the exterior. I like the main photo of Colter; you can see his breath!
The use of OSB sheathing necessitates the use of a continuous exterior insulation to create a thermal break to minimize mold issues. Additional low density insulation in the wall, creating a higher R-value, will not reduce potential mold issues, rather, it can increase the potential by lowering the exterior sheathing temperature, while doing little to lessen the diffusion of moisture. In forty years of building, I used open cell insulation in only two homes.
super1,
While I'm not a fan, I'm not sure I'd go as far as saying OSB necessitates the use of exterior insulation. Providing good drying ability to the outside by adding a rain-screen cavity can also reduce the risk, and houses here built with OSB sheathing before rain-screens became common, that had a good interior air/vapour barrier, only seem to see problems due to bulk water intrusion from the outside.
I'm a NJ (climate 5 & 4) Builder and Lic'ed Architect. I can say that both of these industries are up in arms over the state's implementation of an R60 roof and new wall requirements. They speak of these new requirements as impossible or too much work to meet. Some are paying the $500 fee to BS artists (BS: not 'building science) to get the rescheck to justify lower insulation values (imagine that: paying more money to build worse!). I could not be happier w/ the new requirements and find them very easy to meet. Americans need to start building within their means (of square footage) so that they can afford to build correctly. It's a sad state of affairs the quality (or lack thereof) that the most powerful country in the world is building to when compared to other civilized countries.
Yes,
We have made no progress or very little in the 40 years I have been promoting high performance residential building. Why no progress? Follow the money, building better takes skill and commitment, both lacking these days. Canada is adopting a Step Code that will require quite a high level of building efficiency by 2030 or something like that. In reading some wording on the new code I was struck by the provision for a continuous air barrier. It seemed word for word what the state of Minnesota said in the mid 1990's in their effort to update the state energy code. For those of us who have followed the movement a little creativity would be appreciated.
Doug
I politely beg to differ. Consider 2 new houses that are built identically but one has R60 in the roof and the other R49. How much additional energy savings comes with that additional R11 and at what cost? Could that money be put into other more effective measures?
Unless perhaps you are in zones 7 or 8, I think a code minimum of R60 is overkill. Incidentally, others may think the same because the draft IRC 2024 is reverting to the 2018 insulation levels.
While I have been designing R-60 roofs (or higher) using cellulose for over ten years without what I would consider excessive complications, it does seem that for most architects and builders, it automatically means spray foam as a solution, which is expensive and a terrible choice for the environment. I'm excited about the 2024 IRC shift back down to R-49 if it means less "need" for spray foam.
There are many ways to skin this cat. As a general contractor, this is why my company, Bloedel Builders, frames exclusively with ThermalStud's Tstud products. By using a 5.5" Tstud, 3" of closed-cell PUR, and R-11 batt fiberglass (could use alternatives here), our walls are rated R32. No exterior insulation material or complications. Address the sheathing condensation concerns and air sealing simply with the PUR foam (CZ6). Tstud's are also available in 2x8, 2x6 R19, and 2x6 WarmStud configurations, with more iterations in development. This is also why we soon be producing a unique hybrid sip panel (first in the world with this specific configuration) produced with the Tstud and PUR for pure BS (the good kind) wall, floor, and roof panels. The website http://www.centuryhomekits.com has more information, we are updating model configurations and pricing, and will also be offering the panels for custom configurations. Please reach out for more information.
100% with @Michael Maines on the attic R-60 vs. R-49. This is a simple execution when planned right and we find in our planning and numbers that R-60 of blown in cellulose is more cost effective than even R-49 in a closed/open cell combination. Sadly in high performance building, cost often wins.
In the case of R-60/R-49 attic insulation, I think it's clear that blown in cellulose can help both the builder's budget and also the environment.
I believe I skimmed the whole series but have not read all earlier comments. I apologize if I repeat something already addressed.
Wood Wall Calculator
The Applied Building Technologies Group LLC has a Wood Wall Calculator which I found to be quite detailed, enlightening and interesting to use.
It helps one to comprehend the impact of exterior to interior insulation ratio on the moisture performance of the wall.
For a given annual HDD, the threshold ratios for Class 1 2 3 and no VR are generated and compared to the proposed assembly.
Paint as VR
I had heard various stories about interior paint permeability. Is it 14.3 p or 1.4 p or 0.14 p? How does one evaluate multiple layers? I have heard that you do not simply take the inverse of the sum of the resistivities as one does for materials with more substantial thicknesses.
From a design or modeling perspective one should evaluate the more problematic end of the scale.
Exterior Insulation type and performance
The rated R value label for thermal insulation is Required to be at an average temperature of 75F (50 on one side and 100 on the other) .
Exterior CI with cavity insulation does its work at a higher average temperature or lower average temperature. For Mold Growth Potential this gets pretty important if the insulating capacity goes down with decreasing temperature. That is the case with polyisocyanurate which uses pentane for the insulating gas.
You can count on R5 per in. if it’s the only insulation (inside temp 70, outside 20, avg 45 )
But if you have R10 for stud void and R20 for exterior ci, the sheathing is at 58, the avg temp is 39F. That lowers the the exterior P-iso R value and further lowers the sheathing temp and average temp. Empirically, 1 iteration is enough, 2 is justified only if it’s fun.
The story I tell myself is that 1/2” P-iso under new siding serves little thermal purpose in the heating season.
Windows
I thought installing windows in the middle to reduce microclimates made them “ ‘tweenies”.
I thought that was the “right “ thing to do.
It is comfortable, but visually the window becomes porthole- like . I’ve flared the interior and exterior returns where feasible. (Interior flares are less of an issue visually, but compelling with in-swing tilt/turn windows.
It’s easier if your replacement window is narrower than the original.
I have always been skeptical of the vapor barrier paint as part of a robust wall assembly. Often this includes drying to the warm side against the flow of heat. Does this type wall assembly require disclosure to the owners as to what has been done and what will be expected in the future for building longevity? No Mango Mud !!
Doug
If you have a very deep window jamb; consider doing a mirrored jamb wrap like I did for this basement window. It may not work aesthetically for every room's style but for some rooms like this home gym it worked out well.
Hi Randy W,
Appreciate your in depth follow-up on this code 'version' issue we discovered back in your original article. Frankly I wish your version of the code is what would have been what came out (no version for cavity-only insulation in my Climate Zone (CZ5)) ... so I will just have to continue to advocate for continuous insulation here until the code catches up.
Thanks again,
James Bischoff
Log in or create an account to post a comment.
Sign up Log in