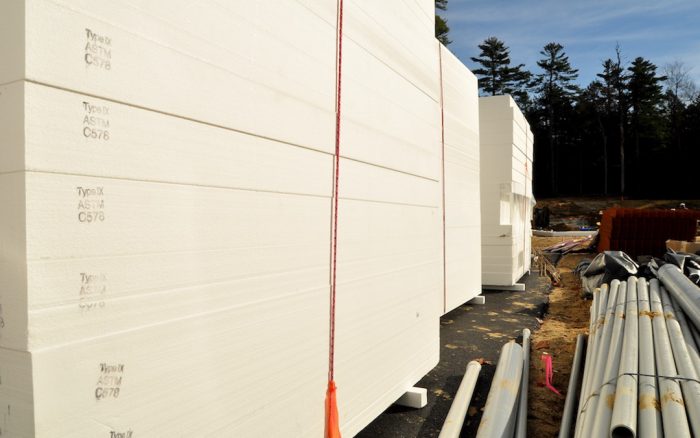
Q: Some builders and designers shun certain types of insulation because of their potential to damage the environment. What are the environmental tradeoffs involved in selecting insulation and why are some builders “foam free” advocates?
A: Life was a lot simpler when we could select insulation solely on the basis of how effectively it stopped the flow of heat. The higher the R-value, the less heat would sneak through a wall or a roof and the more comfortable the occupants would be.
That’s still true. The R-value of any given insulation is an important consideration. Building assemblies with higher R-values require less energy to heat and cool, so some builders and designers lean heavily toward the types of insulation with the highest available R-values. This list includes several varieties of foam available in sheet form—expanded polystyrene (EPS), extruded polystyrene (XPS), and polyisocyanurate. In addition, there are two types of spray polyurethane foam—open- and closed-cell—that are applied as a liquid. They quickly cure into a solid mass and are often used in exterior walls and roofs.
Foam insulation tends to have relatively high R-values when compared to other materials. XPS, for example, has an R-value of 5 per in. when manufactured, and some types of closed-cell spray polyurethane foam have R-values of greater than 7 per in. All of these options look better than some of our old standbys, such as fiberglass batts with an R-value in the neighborhood of 3.5 per in.
Some manufacturers have been careless or misleading with their R-value claims, and there are building scientists who would like to junk the metric altogether. The R-value of polyiso declines in cold temperatures while other types of insulation show one R-value at the time of manufacture and another a few years down the road as the insulating…
Weekly Newsletter
Get building science and energy efficiency advice, plus special offers, in your inbox.
This article is only available to GBA Prime Members
Sign up for a free trial and get instant access to this article as well as GBA’s complete library of premium articles and construction details.
Start Free TrialAlready a member? Log in
44 Comments
The best performing walls are those with insulation outside of the sheathing. My house features double stud walls and I don't lose sleep over it. But I would have preferred 'outsulation' over insulation.
The challenges with natural alternatives to exterior rigid foam are numerous. Currently, wood fiber boards come in odd dimensions, are expensive, and heavy. Also, despite some manufacturer claims that they don't need a WRB over wood fiber boards, I would still be inclined to add a WRB over the wood fiber board. Its hard enough to attach exterior rigid foam already. Adding a WRB under your strapping and over your wood fiber boards seems like a nightmare to me. You don't need a separate WRB for exterior rigid foam. It is generally fine if it is wet. Tape the seams if you must.
Also, some rigid foam, like Polyiso can serve as a vapor retarder for hot summer days. All natural forms of insulation are totally vapor open. I'm not sure I want that all the time.
Other natural outsulation options might include straw bale walls or Larson/Corsen Truss walls filled with cellulose. The Straw Bale wall is my favorite for many reasons but I acknowledge the numerous challenges with building one (keeping it dry, plastering, selling the idea to a client, etc). Larsen/Corsen Truss walls are great for pre-fab but require your insulation contractors to use scaffolding, etc if site-built.
People like Mike Maines and Bruce King have really helped me (and I hope others) understand that not only do builders/designers have an opportunity to make choices that reduce the environmental footprint of their buildings, they also have an opportunity to fight climate change with their buildings by using carbon-storing materials.
Building/designing thick walls/roofs can lead to failure if not done correctly. I think the High-Performance /Building Science community has done a great job of educating people on how to build with physics in mind. This has been quite an evolution. Using carbon storing insulation might be the next frontier. There are challenges to overcome (as I described above) but they are surmountable with the continued sharing of ideas, techniques, product development, and increased awareness. I'm sure GBA will lead the way.
>"Using carbon storing insulation might be the next frontier."
It's the NOW frontier, not the next frontier. Cellulose is cheap and reliable, with a negative carbon footprint (it's sequestered carbon).
Thicker mid density fiberboard sheathing and woodfiber batt insulation still aren't widely available in North America, MSL's SONOclimatECO4 or Go-Logic's pending product lineup notwithstanding:
https://www.mslfibre.com/Produits/Fiche/13/SONOclimatECO4
https://golab.us/products/
But hopefully GoLab's stuff will be available soon. Their goal is/was to have goods available for the 2021 building season, but that goal was pre-pandemic. Hopefully they'll come close to hitting that mark, and they might, given that Maine has so far managed to avoid major COVID outbreaks. If they meet their schedule that makes it the current frontier, not the next frontier. They're even talking about offering up to 10" thick fiberboard(!) which would be north of R30, with a significant amount of thermal mass benefit from the lignin & cellulose content, which offers very favorable thermal diffusivity in high temperature swing environments.
From a carbon footprint point of view, this comparison is on a lbs per cubic foot basis, per R, but it's still pretty telling. Wood fiber insulation is carbon negative at any R:
https://i0.wp.com/golab.us/wp-content/uploads/2020/09/Insulation-Products-LCA.png?resize=1313%2C1536&ssl=1
I am on fence in this analysis. I am trying to avoid the use of closed cell foam in a new design, not due to the carbon sequestration but more to the vapor permeability. In looking at the physics for a retirement home, it boils down to plywood and a R5 material so thing dry out. Then use heat pumps and a good hydronic design, with simple IAQ system you are comfortable. The end goal is that the people in the house are comfortable and healthy.
The additional cost of healthy insulation alternatives is a few percent in a home - not insignificant, but not a deal-breaker either. The global warming argument leaves me cold - not when coal burning continues to zoom in the developing world and increases in CO2 overwhelm whatever cuts the developed world makes.
ah the 'you first' mentality. Getting people places since never. Chicken much? Ends bad if everyone has that attitude.
COULDNT agree more-i am totally down with combating global warming but this amounts to little more than virtue signaling at the level of. A Single residence. Seriously-think about it- better to Use the money you save and donate to a cause or lobbying group that is engaged at attacking global warming a significant level. A very easy one are NGOs that plant trees; especially in the Amazon basin.We are simply not gogin to solve global warming one person a a time
Doug,
Wouldn't your argument apply to nearly everything discussed here at GBA?
Or is your point that GBA should really be PBA (Performance Building Advisor) and any discussion of 'green' is moot by virtue of relative scale?
Yes of course you are absolutely correct-but so am I. .... my point is actually highly germane to those whose interest is primarily being green when they build. If such person is serious (as opposed to virtue signaling) about global warming, well then get serious-take the money you save by using foam and put it to much more effective use to save the planet.
The money you save by using foam? Cellulose is a lot cheaper, per unit volume or per unit R-value. I guess you are talking about things like sub-slab insulation?
Doug,
I don't see it as an issue of who is right or wrong.
I think this sort of point is fine to make, and can be a good point to keep in mind—big picture stuff. Jon R is constantly making points about $ per carbon and it's a good point.
I do think there is a limit to the usefulness of that point. It simply depends on the specifics of how its being made. It can pretty quickly turn from a good point to a trite point if it's being used to justify not paying attention to certain consequences of our actions.
If someone truly wants to run the numbers on how they could personally have the greatest positive environmental impact, I'm all for it. Usually, I don't see that level of analysis though. Additionally, there's lots of ways to 'save money' and spend it elsewhere. How do we determine where to save to spend, and where to spend to save?
Only other point I'll make is that what starts as small decisions can lead to industry wide (or systemic) changes given enough momentum. In other words, if the foam industry got off it's butt and made foam with low GWP the standard instead of the specialty, how much better off would we be? How do we get the industry to do that?
Tyler, there is in fact progress on that front: See this article:
https://www.greenbuildingadvisor.com/article/xps-makers-announce-more-planet-friendly-formulations
And the last comment notes new legislation that will be going to the EPA for rulemaking.
> How do we get the industry to do that?
Charge for the externality (environmental damage), making it financially better for them to change.
Planting trees is also virtue signalling, as it doesn't make much of a dent in the greenhouse gas problem. You need to be planting millions of trees per day, in perpetuity, to offset civilization's greenhouse gas output. You'll run out of land to plant trees in pretty short order, which cements the action as "for show" only. Not only this, but trees can only store carbon, not any of the more serious offenders (e.g. the blowing agents in most foam insulation).
Avoiding putting greenhouse gases in the atmosphere, at any level, is more meaningful than your suggestion of planting trees.
The term "virtue signaling" is designed to allow selfish people to feel justified in not doing the right thing. There is nothing wrong with doing the right thing, even if it has a small impact. By talking about doing the right thing we convince others to do the right thing, and it starts to have an impact. When the message we put out is that our efforts to do good are for show only, we allow polluting behavior to continue.
When you have a choice between two options that are similar in price and performance, but one harms the environment while the other helps the environment, why would you not choose the one that is best for everyone?
A few thoughts:
1. In "Blowing Agents Give Foam Its Lift", 3rd ¶
a. It is my understanding that the EPS blowing agent is air, not pentane. Without any special gas inside the bubbles to induce a diffusion potential, there is no displacement and consequent deterioration with age.
b. It is my understanding that pentane is the typical low GWP blowing agent for polyisocyanurate. Over time, this hydrocarbon is displaced by air leading to thermal drift over time. Science informs me that the boiling point is about 36.1ºC (96.98ºF), and consistent with life's stories, increasing pressure raises the boiling point. If pentane wants to be a liquid at standard conditions, are we surprised that it becomes more of liquid as temperature drops reducing the effective R value? It is my understanding the National Roofing Contractors Assoc. has recommended their members use R5/in. as a reliable value for polyisocyanurate, I presume to avoid condensation litigation down the road. Using polyiso in sufficient thickness allows the outer portion to function at R4, the inner layer at R6 and the in-between layer at R5. This sounds like fun applied calculus.
2. Although HFO as a blowing agent is being used for closed cell polyurethane spray foam, I have yet to see any HFO blown XPS on the market. I have heard a rumor that 2021 holds promise, I assume on account of regulatory deadlines, for whatever that is worth. Owners, specifiers, builders and building supplies vendors can make that happen sooner by specifying, buying and offering low GWP products. If XPS stays on the shelf, the industry will switch.
3. EPS seems to have its place in the building envelope as a lower cost, durable, reclaimable and recyclable material. It seems to have the highest degree of semi permeability (among foams), so if used in sufficient thickness, its drying potential appears to be adequate. I perceive EPS as an affordable c.i. for retrofits and new construction where fire risk is limited, and more a case of personal responsibility than external sources of ignition. (I think immediately of sprawling suburbia and barbies under the eaves.) Mineral wool board and wood fiber board would cost 3 to 4 times as much as an EPS based "outsulation" retrofit. That savings can then be plowed into the heat pump and mechanical ventilation.
4. EPS, like XPS, thermal resistivity increases with decreasing temperatures. When its really cold out, that outside layer is working that much better. Balancing cost, density / compressive strength, thermal resistivity, moisture accumulation, insulation goals and durability at installation leads to an optimum density for each situation.
5. I perceive EPS as a relatively healthy insulation that can get more homes more insulated sooner. Sequestering carbon in our homes buy using carbonaceous fibers in the insulation, favoring wood siding over cement or vinyl, and so forth will get easier as petroleum product and energy costs go up. A GWP tax would also help with that decision process.
Going foam free costs money, so it simply isn't in everyone's housing budget. And in the lower end housing market, the added cost of non-foam solutions may not be as recoverable at re-sale.
That's the story I tell myself, until I am better informed.
Eddy, the styrene beads used in both EPS and XPS are created using a pentane compound. With EPS, those beads are fused using steam (H2O). With XPS the beads are melted and expanded using a blowing agent. Polyiso is very similar to spray polyurethane foam, except the blowing agent is a pentane compound.
To accurately compare the embodied energy of one insulation product to another, I believe it should be done by effective R-value, rather than by weight. The weight will of course be a part of the calculation to determine the embodied energy, but listing the embodied energy relative to R-value allows the designer to understand what insulation material has the advantage in regards to the embodied energy.
Interesting discussion, but leaves out one of the big issues in building a new house in the USA - do you have a vented or unvented attic? Of course the unvented attic requires foam. I am getting ready to build our "forever" house in East TN (climate zone 4). I would like to do the unvented attic, but I can't find a straight story anywhere whether it is the right thing to do, and if so, what are the necessary steps that one should take to do it right (e.g. diffusion vents, dehumidifiers in the attic, impermeable membrane under the sheathing, etc) I don't want to just trust the foaming contractors. Most contractors avoid it, either because of high initial cost or fear of the unknown. What's a guy to do? Any wisdom out there?
you could start here if you haven't seen it: https://www.greenbuildingadvisor.com/article/how-to-build-an-insulated-cathedral-ceiling
spring board off that.
Thanks for the comment. So I did get that article, and Holladay says (I'm quoting only the first sentence, but it makes the point):
To summarize, there are four ways to build an unvented roof assembly:
1. Install closed-cell spray foam against the underside of the roof sheathing, and no other type of insulation.
2. Install an adequately thick layer of continuous rigid foam insulation above the roof sheathing and air-permeable insulation between the rafters.
3. Install an adequately thick layer of closed-cell spray foam against the underside of the roof sheathing, and fill the rest of the rafter cavity with an air-permeable insulation.
4. Install a vapor diffusion port at the ridge.
Now I’m really confused because everything else I’ve seen says you can only use open-cell foam for the roof deck, for the reason that if you do have a sheathing leak, it can be seen. What am I missing?
lesrice,
The reason open-cell foam might be better if you have a roof leak is that it is relatively vapour open - that is, it lets water vapour move though it, and would allow the sheathing to dry out. The chances of the leak becoming visible before a lot of damage has already been done is vanishingly small.
The problem is that same vapour-open quality also allows moist air to move through open-cell foam and reach the roof sheathing, which can lead to rot. A much more likely cause of roof failure than a leak.
Thanks for the comment. Is closed cell now the widely accepted solution? Can de-humidification mitigate the issue? One of the builders I talked to said he would use open cell foam, but put a small dehumidifier ($200-300 Home Depot type)in the attic
My opinion on the subject is partially shaped by heating with oil for decades, and then seeing the spray foam guy show up with two 55 gallon drums of material to do his work..
Yes the GWP is an issue but so is burning excess amounts of oil year after year after year.
Various insulations have their upsides and downsides, and they should be considered carefully, and in my opinion, not rejected out of hand for a single issue
Hello, 1st timer here...schwing. As a new homeowner, I'm (all in) for a GREEN way of doing things. One concern of mine is the RED world....the world of home fire. It's always some New York minutes away. The subject of insulation combustion is not discussed here and I may be off base for bringing it up, but it is a concern to me....just sayin' my say. Thanks.
Michael, thank you for the education and piquing my curiosity further, to know the fate of the pentane used in particular .
Marta, I agree, life cycle embodied energy and life cycle GWP are accurate assessments that aid an informed decision. A “per R” evaluation may over simplify, but is very useful in the selection process.
Keith, I hear you , and I hear the oil spray, the roar of the dinosaurs’ flame, each time it ignites. Your closing thoughts triggers the question of whether the GWP comparison of XPS to Polyiso or EPS is consistent with unitized heat resistivity, say “ per R sq ft”. It is the story I have told myself and that makes use of XPS a 200 (or so ) fold greater sin than EPS. Probably the multiplier is smaller if Type 9 EPS is being Considered.
Civil6, Yes the fire resistivity of an EPS stuffed wall is of significant concern and is a consideration. Polyiso and XPS both can figure into 1-hr exterior rated walls while EPS does not. It is a risk analysis, and insurance rates reflect this in large projects where the choice tends to be XPS polyiso- or mineral wall or fiberglass board.
Lesprice, The stories I have read suggest an unvented roof involves provisions(Which you’ve identified) to keep moisture from getting to your sheathing, and those provisions have to be successful. Where ever it fails, It seems your sheathing is at risk. There is a disturbing 53 minute YouTube video in which Joe Lstiburek takes the viewer on a hazards tour of just this sort of situation. I heard there is a new study as well, And I am looking for it, but I haven’t found it yet.
I've read many articles about insulation, and they all run through the same drawbacks to foam without really examining the assumptions made in the evidence that is offered. This is best illustrated in the case of XPS foam. By far the worst sin of this material is the blowing agent, which has a vastly higher global warming potential in comparison to CO2. Instead of just shaking this stick at XPS perhaps we could look at the context. First, what is meant by "potential" . Does this refer to the uncertainty about the behavior of the molecules themselves in the atmosphere, or to the uncertainty about how much of these chemicals will escape into the atmosphere? If most of it stays captured in the foam it becomes a potential threat only in the same way as methane hydrates which could push global warming into turbo mode, but are so far stored in very cold parts of the deep ocean. But even more problematic is how much of this chemical is represented in each cubic foot of XPS? Even with a GWP of 1400 , how does that compare to the amount of CO2 produced by burning a gallon of gasoline? Does your truck represent more GWP on the drive to work than the XPS you are putting under the slab you are pouring that day? You know that the CO2 from your truck is going straight into the air and won't be spending at least part of it's life captured in foam. Perhaps focusing on fuel efficiency and driving the speed limit will spare the world more GWP than all the XPS you use in a year even at the rate of 1 to 1400. How much CO2 does the foam save in more heating efficiency for the life of a building?
I would also like to know how the carbon footprint of manufacturing, transporting, and installing a given material is calculated. This must involve so many assumptions that it can only represent the most approximate values, which in any given situation might be a magnitude off.
This is not to defend or condemn any choice. This is to point out that the best we can do is build well with lasting materials. The truth is that any of these calculations become meaningless in a world where the most egregious climate threats go on unaddressed decade after decade. If I happen to choose XPS , which I seldom do, I don't loose any sleep.
It helps to put CO2 into $ terms and then compare to alternative ways to reduce CO2. But XPS is truly horrible - there is variability, but I get $15 of Co2 per 2" 4x8 sheet. Now if only someone would collect that cost to society - nobody would use XPS because it would be too expensive.
Brian,
These are great questions but I am a little puzzled that you proceeded to draw conclusions based upon answers to your questions that were seemingly never provided or researched.
I am thankful for the people of GBA and Building Green, etc for the work that they have done in reporting/calculating the global warming impact of insulation. But, the data is meaningless to most of us. Stop a person on the street and ask them: "Is 2,500 Kgs per M3 of Co2e bad for the environment?" What do you think they will say? Building Science nerds are great at science but terrible with messaging. Don't get me started on "Pretty Good House"... It should be called the DAMN GOOD HOUSE. :-)
Anyway, back to XPS.
Lets say you are building a two story 30'x42' house in New England. You decide to wrap the exterior walls with 3" of XPS and put 2" of XPS under your slab. This adds up to about 800 Cubic feet of XPS or 22 Cubic Meters of XPS.
XPS loses most of its blowing agent in the first couple of years. It is definitely not "captured in the foam". This blowing agent, combined with the underlying material, result in 2,500 kg of CO2 (equivalent) per cubic meter. So, in our house above, we released about 55,000 Kg of Co2. Converting this back to Imperial, about 122,000 pounds of Co2.
Burning a gallon of gasoline releases 20 pounds of C02. So, our house with XPS resulted in the equivalent of burning about 6,000 gallons of gasoline. ***If your truck averages 22 MPG, then it could have travelled 132,000 miles and released the same amount of Co2***.
EPS is a much better alternative. In this example, if the same house had used Type II Eps instead of XPS, then it would have equated to only 11,000 miles driven in your truck.
***To put it another way, I could cover the home in EPS and then burn 5,500 gallons of gas in the front yard. Or I can cover the home in XPS. The environmental impact is the same!*** Oh, and the R-Value would be the same for both homes.
I don't know where building a house ranks in terms of contributing to climate change. On its own, it is likely very tiny and, to your point, not worth losing sleep over. But for me, the question is, what can I do to minimize the impact? Switching from XPS to EPS would make an enormous difference. Switching to wood fiber boards over foam would actually work to combat climate change in its own small way. This is reason to sleep WELL! :-)
Rick,
Your two posts are a really helpful articulation of the issues. Thanks!
Thanks Malcolm!
Thanks for offering an explanation, but I'm afraid I'm not convinced. Perhaps I would have to see your worksheet (thee are 27 cubic feet in a cubic yard for instance) and have a way to verify the many figures you are starting with. References would help for technical data. This sort of detail, to my first point, is always missing. Perhaps you could write such a paper and henceforth questions like mine could be linked to it.
I don't dispute that there are much better insulation choices environmentally speaking, but they have there own limitations. As I've said here in other places, EPS is simply not available in most places without special order in quantity and it costs way more for the same R value, and it is bulkier for the same R value. I don't have the luxury of stockpiling a large amount of it in different thickness' hoping I'll find just the right place to use it. In other words, EPS is not market ready. I don't know why this problem can't be solved, but the industry doesn't seem very concerned about it.
I do use cellulose which even the big boxes often have, and I don't mind having lots of bags on hand since it's easy to store and fits into any space. I haven't done research to get the details on it's carbon footprint, but it can be more easily manufactured with simple quality control and with very easily found technology and materials, making it more readily produced close to a market.
But the most important point is my last one. Moral purity may feel good, but it doesn't solve problems. I have been well informed about climate change for over 30 years. I am aware that no meaningful change has come about in that time. I don't see a change in that situation in the future. It is beyond pathetic that climate change only became a debate topic in the Presidential election this year. In other words, moral arguments are not effective.
My take on this Brian is that if/when policy—or what have you—takes this to the needed next level, the building scientists and GBA-type folk will have provided some knowledge base and examples of 'what is possible' for policy decisions to be based on.
In other words, I think you are right that it needs to go beyond individuals making 'moral' choices. And I've also been continually disappointed that EPS isn't readily available locally. It feels hard to justify the special order and extra trip. Is it actually more efficient if it doesn't fit in with the standard bulk procedures for manufactures, distributors, and builders? There seems to be a certain level of inefficiency with 'special ordering.' I have not ran any numbers, but based on Rick's 'miles driven' calc, it sounds like EPS might still come out ahead though.
Perhaps trends and/or policies will someday reduce XPS's stronghold on the market.
Tyler,
I think there are already some big regional differences. EPS is the only product my lumberyard stocks in varying thicknesses for under slabs. Home Depot has faced EPS in as many variants of thickness as they do XPS. It's a readily available commodity here.
Similar here in SE Michigan. EPS is readily available and slightly less expensive per R if you apply an appropriate de-rating for age to XPS. Polyiso is a better choice if R/inch is important.
Hi Brian,
I forgot to add the source for the Co2 figures for XPS and EPS. Thanks for mentioning this.
These numbers were developed by David White in conjunction with BuildingGreen in 2010. It would be great to hear from Alex Wilson or others at Building Green to learn if they have any updates regarding their initial calculations.
Here are the links to the webpage and the excel calculator:
Calculator: https://www.buildinggreen.com/sites/default/files/articles/insulation_gwp_tool_v_1-2.xlsm
Webpage:
https://www.buildinggreen.com/blog/global-warming-potential-insulation-materials-new-calculator
“[Deleted]”
“[Deleted]”
Just a quick comment on EPS being readilly available. I am currently building a house for myself in stewartstown pa . I am using 350 4x8 sheets 2 and 1/8" thick treated with NEOPOR, a graphite additve created by BASF to end up wit an R value of 10. The foam density is a minium of1.15# You can go directly to a plant and have your order made. There are many plants across the country I ended up using one in latrobe Pa about 180 miles from the build site. the final cost per sheet with freight $ 1000.00 and 6% sales tax was 21.07 per sheet
First used closed cell on a project back in the late 80's after college -- was rehabbing an 1810 federal in Philadelphia. Not common around me back then --- builder thought it was a good way to solve the many tight irregular spaces found in the house. The results were nothing short of amazing. Have used it in every project since.
Have done an old PA stone farmhouse .. also a PA barn conversion. 1900 Firehouse in the city. 1800's stone church. Nothing would have worked like foam for those projects. It seems that the foam part gets pulled out as a problem w/o looking at all the other manufactured products going into construction today. Also -- while some of the other ways of building look interesting (double walls and thick outside insulation) they pose problems from the start .... just getting the details correct as you move through the building process. Most contractors have no idea how to do it and frankly ... double walls use so much material and lower interior sf and add to constructions detail problems at every turn.
Typical 2x6 wall and common roof rafter construction .... plywood exterior with foam. Not much that can get screwed up. I question rigid foam on the outside of ZIP ... it looks like a water trap to me. Plastic VB looked like a good idea as well back in the day .
How do we calculate 50 years + of energy savings ? What do all the manufactured wood products add to the climate change scale? One of the big problems I have had with foam is getting HVAC people to install the proper equipment --- 1K plus per ton AC .. installing the smallest heating equipment.
I need your help and advice.
Long story
I have an 8 year old shingle roof on my vaulted ceilings.
One area there is an alcove and there is a lot of moisture.
The moisture was running down the poly membrane and the insulation above it was damp and the wood was wet
Roofers came and reflashed things and no better
Then one young fellow came and said the problem is ventilation.
there is not enough ventilation and so the condensation is building up under the wooden OSB and dripping down on the fibre glass insulation and running down the plastic sheet
there is a lack of soffit ventilation in that area and some are blocked by insulation
Also the insulation is so high that is not enough room for air to go over it. Makes sense. The nails are rusted in side and not the heads
ie construction defect.
His solution is to :
remove the shingles
make cross bracing to make more room for air to pass
add soffit ventilation
remove wet or damaged insulation
and then put a new roof on. he suggests metal
It all makes sense though it will nearly bankrupt me!
1) Does it make sense to you guys
2) Can you put a metal roof onto a vaulted ceiling or will the noise be too much from the rain. We sleep right under it
3) should I change the insulation from fibreglass to solid foam to reduce condensation
4) Maybe this little alcove is part of the problem as it lets moisture into the area and once the new roof is on I will need to seal this area properly with a plastic sheet ?
Thanks
I live in the cold wet pacific northwest
Fish, you are dealing with a construction defect, and the solution you've been offered is an expensive boondoggle that will not fix the problem. You haven't mentioned airtightness, which looms as large as insulation defects in finding and fixing vaulted ceiling problems. I see you're already a GBA member, which gives access to this article: https://www.greenbuildingadvisor.com/article/how-to-build-an-insulated-cathedral-ceiling
There are numerous links to other articles, plus check out the numerous past Q&A threads that deal with this topic. Once you're educated on the physics and building standards, you'll be able to deal with contractors more effectively. You can also post your own Q in the Q&A section (a better place than here) if you still need to clarify things for your particular situation. Unfortunately, this problem is as common as it is destructive. GOOD LUCK!
plastic can be a problem as it traps any moisture that gets into an assembly -- any lights or other penetrations ?
I always do full taped drywall prior to installing a wood ceiling -- if just wood you have all the moisture going into the roof assembly
Yeldog,
Plastic only traps moisture in an assembly if it is the way of the drying path. Fishonhook is proposing to add a ventilation channel to the roof, so I don't see what problems plastic would cause.
What about insulation on the room side? Some taped polyiso would give added insulation and would be airtight, keeping moisture out of the outbound assembly.
Log in or become a member to post a comment.
Sign up Log in