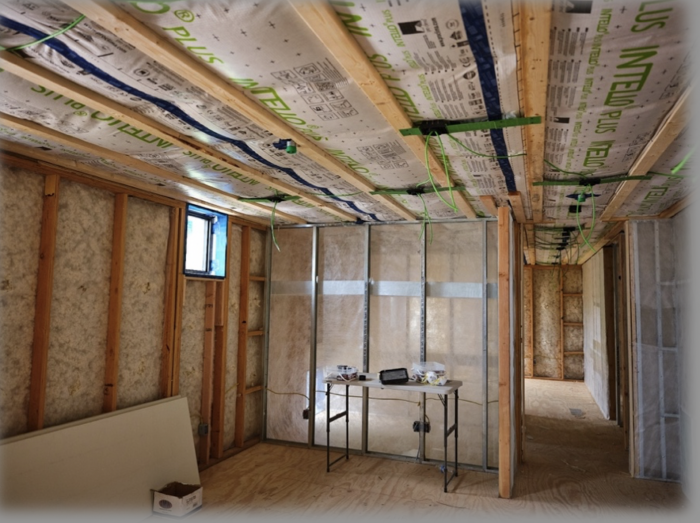
EDITOR’S NOTE: This post is part of the Expert Exchange series, an editorially directed and expert-driven platform for information and discussion around leading-edge building science principles and projects. The fourth quarter topic—made possible with support from our sponsor*, Rockwool—is “Choosing Products and Materials for a Green Home.” The series will culminate with a webinar panel discussion among contributing experts on Dec. 7 at 6pm ET. Click to register.
Construction is a lot like cooking. Life-sustaining results are achieved when good ingredients are transformed by passionate professionals. Beauty is created, people are nourished, and the health of communities and our planet is protected. By the same logic, good buildings need good ingredients. The materials we use have impact. Regardless of the skill of the team using them, there’s no removing embodied carbon or embodied injustice (more on this later) from certain products. A hyper-efficient Passive House, for example, can have a 300-plus-year carbon payback period, if using synthetic insulation to achieve that performance level but the side effects of synthetic insulation can include increased toxicity and moisture-related assembly failure.
There is no intent to blame or shame anyone here. There are many well-intentioned people working on very respectable projects who want to be doing the right thing for their clients and the planet. However, otherwise good projects often fall short due to a few bad “ingredients.” I’ll offer a few hypotheses for why professionals in the green building sector continue to use bad-to-less-bad materials.
First, there is legitimate concern about the cost and complexity of using new products. However, many good products and assemblies are lower cost, already commonly used, and can deliver high performance. An example is dense-pack cellulose with a Red List Free air and water control membrane, such as these products from manufacturer Henry, as a good alternative to closed-cell spray foam.
Second, good is often confused with less bad. Good is a fundamental shift in material composition, whereas less bad is incremental. For example, this new generation of XPS rigid foam board is less bad than previous versions, but it is still made of foam, and it still has a high lifecycle carbon impact. I argue that a good product is made of carbon-storing natural resources like wood or cork.
Third, energy efficiency became a proxy for our better-buildings goals of low carbon, healthy, and durable. However, data has shown that design focused purely on energy efficiency often fails to achieve these other objectives. Efficiency doesn’t require changing materials; efficiency typically encourages using higher volumes of the same bad-to-less-bad materials such as synthetic insulation. I call this the “efficiency trap.”
The efficiency trap has led to a convergent crisis. Our attempts to solve everything through the lens of efficiency has led to higher building costs, Sick Building Syndrome (SBS), and a built environment that continues to generate over 40% of carbon emissions. How do we change this pattern? The answer begins with taking a holistic perspective of the lifecycle impacts of a building with a deep exploration of the products used.
Making a good building
I’m naturally optimistic, but a few decades of building science can make anyone a bit jaded. I’ve heard every excuse in the book about why “green” or “high-performance” or “efficient” building isn’t a goal. But I’ve never once heard someone say they don’t want a good building. I have found that framing the conversation around “good” creates an apolitical and reasonable goal. So the question then becomes how do we define good building?
The people behind The Pretty Good House standard have created a fantastic set of criteria to define good at the whole-building level, but at my company, Vali Homes, we were looking for a tool to help us quickly select quality materials. By combining our team’s experience across thousands of projects built over a few decades, our “Five Factors of Good Building” concept was born.
As stated, the primary point is that a good building must be made of good materials. This means specifying materials that are healthy, low-carbon, and long-lasting. Good materials should be used to deliver the highest levels of performance when the budget is available. If the budget is limited, good materials can result in a high-quality code-minimum home.
At my company, our process centers around product specification. After finding a project site and understanding the local climate, we create a collection of materials that can be turned into a design and structure that fits the client’s objectives. The most important part of our material specification process is creating a “Do Not Use” list. This list typically includes materials like synthetic insulation and products with toxic glues or coatings. Some examples include spray foam insulation, XPS rigid board insulation, and membranes treated with PFAS chemicals.
As noted, every material specification must also be understood within the context of a given building in a specific climate. Our first step is to ensure products have minimal carbon impact, low to no toxicity, and built-in social equity. Then we determine if those products can deliver optimized comfort, efficiency, and durability for the given design in the given location.
1. Comfort and health
We design for comfort first—over energy efficiency. And health is an integral part of comfort since it is impossible to be comfortable if you aren’t healthy. Oftentimes healthy building gets discussed through the limited lens of nontoxic approaches to construction. This is problematic since nontoxic doesn’t really exist. Everything can be toxic at the right dose and even truly good materials, like sheep wool insulation, can be problematic.
Furthermore, nontoxic would simply be the elimination of bad material ingredients, whereas healthy building is a more comprehensive goal. Health is tailored to what works best for the occupants of a given building. Health also requires selecting materials that not just avoid toxicity, but also optimize productivity, relaxation, and joy.
2. Efficiency and renewables
Energy efficiency is, by far, the best understood factor in our industry. Certainly, it is a critical element of good building but it shouldn’t be the primary goal. It is also important to end the long debate about efficiency vs. renewables. The answer is we need them both on every project possible. Good building is the combination of efficiency, renewables, and healthy durable low-carbon materials.
3. Durability and resilience
Longevity of a material is highly dependent on the climate zone in which it is being used. Our process starts with site studies and product research. Then we create mock-ups to test potential materials to see how they perform in a given climate zone. Some materials pass with flying colors, others require customization, and some are clearly not a good option.
There are also some basic elements of building durability that should be included on every project. An example is vented cladding—achieved with a rainscreen. It is also good practice to upgrade from window sealants like caulk to window integration tapes that are rated for decades of performance. The tapes move with the building, whereas caulk tends to be torn by differential movement between the framing materials and the window materials.
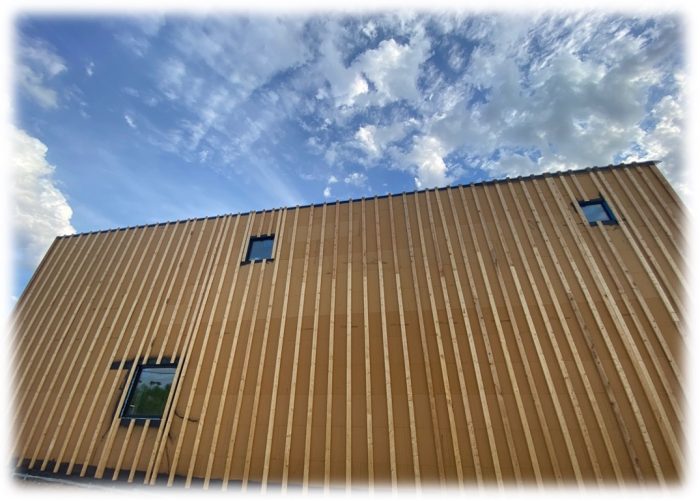
There is a lot more to be discussed on this subject, but in short, these are the questions we try to answer when looking at the durability and resiliency of products: How will the specified materials perform over time in the local climate? What are the best air and water control layers to protect the thermal and structural layers? Will this design continue to meet client goals in an increasingly unstable climate?
4. Embodied injustice
This is the least understood of the five factors, but it is potentially the most important. “Embodied injustice” is a term is used in the social sciences to describe how marginalized communities tend to suffer the worst environmental consequences. We use embodied injustice to summarize the structural violence built into a given product. For example, chemical ingredients and fossil fuel derivatives in spray foam insulation are known carcinogens and others are on the Red List, which includes ingredients known to cause human health issues. (Is it fair to specify products that require workers to wear PPE as if they work for the CDC during an outbreak?)
Another example is membranes that use PFAS as a waterproofing treatment. The documentary “The Devil We Know” shares the story behind a type of chemical often used for waterproofing or to create Teflon for cooking. After many years of litigation, DuPont had to stop using PFOA, but replaced it with PFAS, which is believed to have the same health risks.
5. Lifecycle carbon impact
This factor is becoming better understood. The urgency of the climate crisis is pushing green building professionals to determine the lifecycle carbon impact of a building by 2030. Historically, the focus has been almost entirely on operational carbon, which is how much carbon is emitted during the use phase of the building. Limiting operational carbon is still important, but recent studies indicate that operational carbon is only about 10% to 30% of the lifecycle carbon impact by 2030.
Recent analysis has repeatedly shown that embodied carbon represents 70% or more of the total lifecycle impact by 2030. Most of this lifecycle carbon impact is the Material Carbon Emissions (MCE) from the extraction, processing, and manufacturing of building materials. Leading-edge tools like BEAM and EC3 are useful for calculating material carbon emissions.
Additional concerns with embodied carbon include a material’s transportation, installation, and end-of-life disposal. It is important to perform rough calculations to determine these impacts. For example, consider a shipment of insulation from Germany to Los Angeles on a container ship vs. the same shipment driven on a semi-truck from Los Angeles to San Francisco. The question is: which of the scenarios results in less embodied carbon? The answer should factor into materials specs.
I’ll share two examples of products we’ve run through our Five Factors of Good Building analysis. This is a teaser for an upcoming article, which will outline the top five upgrades we’ve made in our own projects based on the Five Factors analysis.
In sum
The core goal of our Five Factors analysis is to provide a clear and simple summary of how a product performs across multiple categories, which makes the holistic view easier to understand and communicate. The building materials we select have consequences. At my firm, we have found the Five Factor analysis to be the most powerful tool we have for selecting the right ingredients.
*Sponsors are not offered the opportunity to review articles before publication or to edit our authors’ words.
_______________________________________________________________________
Lucas Johnson, MESM, BPI BA, CPHT, is Chief Building Nerd at Vali Homes. Images courtesy of author.
Weekly Newsletter
Get building science and energy efficiency advice, plus special offers, in your inbox.
6 Comments
Very lovely concepts in this Rockwool sponsored post.
Speaking of "built-in social equity"; I wonder how many hours a week, say, a childcare provider, house painter or baggage handler living in my census tract ($40k household income/year) would need to work to live in such a good home? :)
http://www.valihomes.com/mews
Hi Vivian, thank you for your comment. You are correct that making good building affordable has been more challenging than ever in the current market. We find this extremely frustrating as well. At Vali we work on many types of projects covering a large range of costs.
Mews is a very high end project developed to show that good materials can be used in Phoenix and that good materials deliver more luxury than conventional building materials. Our hypothesis was that building something fancy would stimulate conversation in the Phoenix market and we’re happy to see that has been the case.
We also work on retrofits for lower income households that deliver much improved efficiency, comfort, and health. We’ve found these retrofits can be done for $30k or less and that they can be cash flow positive with a loan. This still isn’t as affordable as we’d like to see, but we don’t control material costs.
We couldn’t agree more that it’d be wonderful to see good building become less expensive upfront than conventional. Do you have ideas for how to make this happen?
Lucas, glad to hear that you are also doing some work for less fortunate folks.
I don’t have a magic formula, mostly a combination of tried-and-true components.
It starts with land use; no space wasted for private car storage (AKA off-street parking), multi unit (where each resident only consumes a fraction of the land and building materials), 4-floor wood frame (it can be built inexpensively and without an elevator) and smaller residences. All these elements have the dual advantage of creating the most affordable housing with the least environmental impact.
Obviously, this will work better in some places than others and involves compromises but good design will address some of that. For a lot of folks at the low end of the income scale, I was one of them for the better part of my life, decent housing that doesn’t require a 60-80 hour workweek is #1 priority.
Great to see an article on this topic; life-cycle carbon. I recently completed my own self build; and in addition to trying to design a high performing house, I was super focussed on the embodied carbon. Loose-fill sheeps wool in the cavities; GPS instead of EPS or XPS on the exterior; a high fly-ash mix of concrete to reduce cement use; as well as a pier foundation instead of slab or basement to reduce volumes of concrete; sustainably sourced lumber construction where possible. I tried tracking total embodied carbon but there were a number of products where the footprint was difficult to track (windows, wiring, appliances, paints).
Be great to see the industry focus more on embodied carbon so we see less spray foam etc.
Maybe I'm off the mark here but it's my understanding that GPS is essentially the same material as EPS but with the addition of graphite. I see it claimed as having a higher R value (4.7 to 4.9 per inch) than EPS, but the values I see quoted for EPS (R3.6 per inch) show the low end of EPS values. In fact Insulfoam's Type IX 25psi sheets reach R5 per inch as temperatures drop to 25 degrees fahrenheit.
GPS is definitely a fine material. But if I can achieve the same total R value at a cheaper price with EPS I'll continue to go that route. XPS is definitely still crossed off my list of materials, despite its recent improvements.
All insulation, except polyiso, increases in R per inch as the temperature drops. R-value testing is done at mean 75°F, for better or worse. If you're going to look at the mean 25°F insulating value of one material you need to use the same temperatures for other materials.
GPS is indeed EPS with carbon black added as the polystyrene beads are formed. The carbon particles apparently reflect radiant heat, increasing the R-value of the material compared to EPS by 15-20%. EPS is anywhere from R-3.1/in to R-4.2/in, at mean 75°F, depending on the density and the manufacturer.
Because GPS has 15-20% higher R-value per inch than EPS, but similar levels of embodied carbon, you can use 15-20% less GPS than EPS, thus reducing carbon emissions.
Both EPS and GPS maintain their R-values indefinitely. XPS is about R-5/in when brand new but over time, as air displaces the blowing agent, it drops to between R-4.2 and R-4.4/in. According to the BEAM estimator, embodied carbon emissions for reduced-GWP XPS are anywhere from half to three times that of EPS or GPS, and that's using R-5/in for the XPS. As it ages, its GWP will effectively increase as the R-value drops.
Log in or create an account to post a comment.
Sign up Log in