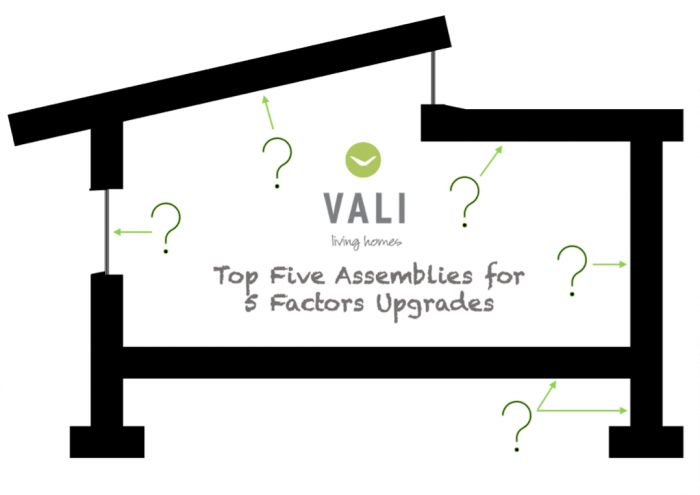
EDITOR’S NOTE: This post is part of the Expert Exchange series, an editorially directed and expert-driven platform for information and discussion around leading-edge building science principles and projects. The fourth quarter topic—made possible with support from our sponsor*, Rockwool—is “Choosing Products and Materials for a Green Home.” View the related webinar featuring the experts who have contributed to this series.
In my previous article, Five Factors of Good Building, I provided an overview of my firm’s design and construction philosophy. Put simply, the data show that building materials and how they are used (and sourced) greatly impact a building’s performance rating. For too long, we have narrowly defined good building through the proxy of energy efficiency as the primary, or sometimes only, metric of success. I argue the definition of success needs to be expanded to include at least five factors: Efficiency and Renewables, Durability and Resiliency, Comfort and Health, Lifecycle Carbon Impact, and Social Justice.
In this article, I will explore how changing a few key strategies in five different assemblies can make a big difference across all five categories. To make this complex subject as digestible as possible, I will focus on five areas of critical detailing in high-performance homes: unvented pitched roof, unvented low-slope roof, exterior wall, foundation and floor system, and windows.
The analysis below is my attempt to present an “average” residential scenario that could be found in a retrofit, addition, or new construction. I am drawing from two decades of building science experience across thousands of buildings. The analysis focuses on varying insulation materials and does not include the materials that stay the same in both scenarios, such as the wood framing and finish materials. It uses commonly accepted numbers for R-value, embodied carbon, and other factors. It is worth noting that these numbers are accurate enough for meaningful analysis, but there is work to be done to make the numbers more precise.
For the more qualitative of the Five Factors paradigm—social equity, durability, and health—an index system of 1-10 will be used with 1 as worst case and 10 as best practice. For efficiency, I will use R-value as the metric and for lifecycle carbon; I will use upfront embodied carbon (EC), which is also known as Material Carbon Emissions (MCE). R-value will be kept as consistent as possible to focus attention on how much MCE can vary, while achieving roughly the same performance.
Embodied carbon data
Most of the embodied carbon data used in this analysis draws from this GBA article by Brian Just. He found and averaged Environmental Product Declarations (EPDs) for the insulation products summarized below. However, since kgCO2e/m2 RSI-1 is not a clear and effective unit for discussion, I converted the data into lbsCO2e/CF. A cubic foot (CF) is roughly the size of a basketball, so it is easy to visualize lbsCO2e/CF as how much each basketball would weigh. And yes, some basketballs would effectively have negative weight, which is what happens with carbon-storing insulation materials.
The EC3 database has publicly available EPDs and is the best source I’ve found for trying to reduce the carbon impact of concrete; the concrete numbers here are drawn from this source.
The Building Emissions Accounting for Materials (BEAM) estimator from Builders for Climate Action is a valuable new resource for estimating the upfront carbon impact of residential construction. In my opinion, a BEAM analysis should be required to permit any new home or energy retrofit. (Some of the MCE data from BEAM was used for the analysis here.)
It is worth noting that EC numbers have a significant degree of variability between specific products within categories. However, the average for a product category is accurate enough for meaningful analysis. Over time, as data improves, lifecycle carbon analysis will become more precise.
For example, XPS rigid board with HFC blowing agents has the highest embodied carbon per cubic foot of insulations in the above chart. The XPS with HFO blowing agents has significantly reduced carbon impact, but still has some of the highest carbon impact per cubic foot.
OK, now for the aforementioned five common assemblies . . .
Unvented pitched roof
Unvented roof systems are popular right now, especially among high-performance home builders. This assembly can prove to be either in line with best practices or a nightmare scenario. Success across the Five Factors depends on upgrading from basic materials to good materials. (Another key component for success is a ventilation channel between the roof and exterior insulation, which reduces conductive heat transfer and allows for better drying in any roof system.)
In the basic scenario, the foam-based insulation materials create decent energy efficiency levels, but they come with significant upfront carbon emissions, and rank poorly in the categories of health, durability, and social justice.
In the good scenario, the natural insulation materials result in roughly the same energy efficiency, as well as carbon storage, a healthy interior environment, durability, and a supportable social justice profile.
Low-slope roof
The low-slope roof is a risky roof system due to poor drainage combined with high exposure. However, people love “flat” roofs, so we need to solve for them. Unfortunately, such assemblies often force the use of less desirable materials, such as rigid foam board for exterior insulation—although, a reduction in embodied carbon can be achieved by using EPS instead of XPS. Similarly, upgrading interior insulation from closed-cell spray foam to loose-fill natural insulation with a vapor-variable membrane can result in upfront net-carbon storage.
Exterior wall
Continuous exterior insulation can deliver much better comfort, health, and efficiency. However, if using vapor-closed, high-embodied-carbon insulation like XPS rigid board, there is the potential for increasing the moisture-related failure risk and lifecycle carbon impact. On the other hand, vapor-permeable, carbon-storing exterior insulation options, like cork or wood fiber, can be expensive and time-consuming to install. For these reasons, at my company, we are experimenting with a new exterior wall system comprising BareNaked Tstud framing with natural insulation, Red List–free control layers, and vented cladding.
Foundation and floor
This example, which illustrates 2700 sq. ft. of conditioned floor area, and 440 sq. ft. of stem wall surface area, is intended to illustrate the importance of reducing concrete use. It makes a big difference if stem walls can be thinned from 8–10 in. down to 6 in. In addition, using fly ash concrete can also reduce upfront carbon emissions by around 30%. This example also demonstrates a common “carbon miscalculation,” which comes from failure to account for how a thick exterior wall forces the use of a much larger volume of concrete for stem walls. There are many good reasons to select a double-stud wall, but one needs to consider how much more concrete will be required for a 10-plus-in. stem wall to support the double-stud walls.
Due to the termite threat, we see mostly slab-on-grade construction here in Arizona. However, there are some improvements to be made across all five categories by using a raised-floor system with good materials. We are in the process of figuring out how to do that properly in the Southwest.
Windows
Windows are expensive and both the basic and the good options shared here have high-embodied carbon. So, it is critical that we do everything in our power to make windows last for many decades. At my company, we separate window detailing into two stages: 1. rough opening preparation, and 2. window integration. The rough opening preparation stage focuses on creating an airtight, waterproof, and mostly vapor permeable opening (the sill is typically vapor closed unless it has a high degree of slope). The second step is integrating the window to the prepared rough opening.
In basic construction, there is typically little rough opening preparation beyond a butyl-asphalt window-sill tape. Then the windows are integrated with caulking and foam, which introduces toxicity and decreases durability of waterproofing and airtightness due to inferior products. Window details with basic materials will need frequent maintenance and often need full replacement in roughly 10 years.
For good window detailing, I recommend using Red List free sealants, natural insulation, and proper flashing at the head and sill. An example would be sheep wool stuffed into the shim space with Red List free air-sealing tape on both sides. A good window detail like this should last for decades with very little maintenance.
Applying the Five Factors of Good Building
Some key points apply to all these assemblies, and they can summarized using our “Five Factors of Good Building” analysis:
Efficiency and Renewables
Good materials typically create a higher degree of efficiency, while also being made from renewable resources. This is especially true of insulation.
Durability and Resiliency
Generally, good materials lower the risk of an assembly’s failure by being vapor permeable, which supports drying potential. When installed properly, they are protected by air-sealing and waterproofing membranes, ensuring greater durability. Basic materials tend to be vapor closed, which means they can encourage wetting and discourage drying. Water accumulation is one of the biggest risks in a building, so basic materials should be approached thoughtfully.
Health and Comfort
Good materials can provide greater comfort and better indoor air quality. Natural insulation materials help modulate humidity levels, which can be as important as air temperature in terms of occupant comfort. In addition, natural insulation materials tend to regulate temperature better than synthetic materials; they also manage sound well.
Lifecycle Carbon
The combined carbon emissions of the basic insulation materials are roughly equivalent to the embodied carbon of an entire home being built. However, if we switch to using good insulation materials, we can store tons of carbon upfront. (In my opinion, the carbon-storage capacity of healthy, natural, high-performance insulation is our hidden weapon for battling the climate crisis.)
Social Justice
There are a few key requirements to count as a good material in terms of social justice. First, the communities where materials are sourced cannot be harmed. Second, the workers who manufacture the materials must not be exposed to toxic materials with any frequency, nor the workers who install the materials. Third, all communities and workers must be fairly compensated for their contributions. Lastly, materials must not expose building occupants to toxicity.
Highlighting carbon
Carbon impact is an urgent issue that can be quantified better than ever before. While energy efficiency is still critical to reducing operational carbon emissions, it has become clear that the more meaningful carbon reductions occur during the production phase of materials. In other words, we need to use low-carbon materials, especially for insulation, if we are to commit to low-carbon construction.
The chart below summarizes how the basic and good materials scenarios compare, and averages upfront embodied carbon of a single-family home, which is roughly 100,000 lbs for all systems including foundations, framing, insulation, and finishes. For the two scenarios explored in this article, only insulation and concrete are included in the “total” impact.
The key takeaway here is that using basic materials to build a high-performance home can result in a high lifecycle carbon impact. Energy efficiency reduces a building’s operational carbon but the upfront carbon emissions resulting from what’s needed to achieve that efficiency need careful consideration.
*Sponsors are not offered the opportunity to review articles before publication or to edit our authors’ words.
_______________________________________________________________________
Lucas Johnson, MESM, BPI BA, CPHT, is Chief Building Nerd at Vali Homes. Images courtesy of author.
Weekly Newsletter
Get building science and energy efficiency advice, plus special offers, in your inbox.
One Comment
Excellent, practical article for builders everywhere. Well done, Lucas!
I am curious, do you (or anyone) have links to the studies upon which much of these estimates are based? The links to the actual studies never appear to work.
I am really curious to read exactly how they arrive at negative Co2 figures for Cellulose, Wood Fiber, and Sheep's wool. I can understand fast growing Hemp or Straw-bales.
But these are my questions for those that I have researched this more than me:
1. Cellulose: are they accounting for the declining % of recycled content? Virgin paper stock can be energy intensive.
2. Wood Fiber: I've read that younger trees sequester far less than older trees? Trees harvested for Wood fiber must have some kind of carbon pay-back period? Wouldn't this prevent the up-front negative carbon figure? Also, many of these products are like 5%-11% or more paraffin wax or binding elements. Are these petroleum products factored in? How do these chemical elements compare to something like Benzene and Ethylene in EPS, in terms carbon foot print? Are the binding elements by weight or volume? If by weight, then these may have about half as much petroleum content as Type I EPS.
Sheep's Wool: I am curious to see how they account for the energy needed to feed and hydrate sheep. How are the pasture lands assessed? This just seems really energy intensive to me.
For the record, I love cellulose and Wood Fiber. (No experience with Sheep Wool). They have exceptional benefits beyond their low carbon foot print.
Log in or create an account to post a comment.
Sign up Log in