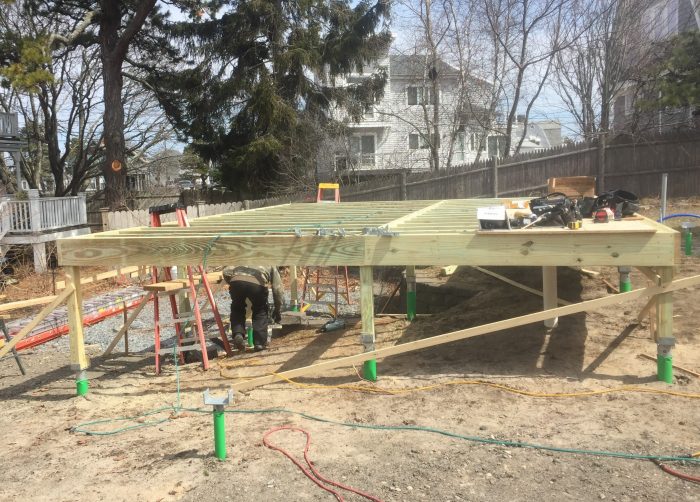
By now, most builders know that in all but the warmest climates, foundations need to be insulated. Whether your house has a basement foundation, a crawlspace foundation, or a slab on grade, foundation insulation is usually a good idea (and is often code-required). Insulating a basement, crawlspace, or slab-on-grade foundation usually requires either rigid foam insulation or spray foam insulation.
But some green builders want to build a foam-free house. (For more on this topic, see “Building a Foam-Free House.”) The cited reasons for avoiding foam insulation vary. Some green builders worry that some foams may be toxic; others don’t like to use any materials derived from fossil fuels.
In this article, I’m not going to debate the merits of these concerns; rather, I’m going to focus on all of the different ways to build a house with a foam-free foundation.
Can your foundation be uninsulated?
In most U.S. climates, building codes require foundations to be insulated. In the 2018 IRC, foundation insulation requirements can be found in Section N1102.1.2 (R402.1.2).
If you are building a house in Florida, or a state with a similar climate, you may be able to build your house on an uninsulated slab. That said, in most climates, slab-on-grade foundations need, at a minimum, some vertical insulation at the slab perimeter.
For more information on ways to insulate a slab-on-grade foundation, see “Determining Sub-Slab Rigid Foam Thickness.”
If your house has a basement foundation or a crawlspace foundation, insulation is usually installed on the basement walls or crawlspace walls.
Is it possible to substitute semi-rigid mineral wool for rigid foam?
Green builders who want to avoid the use of rigid foam or spray foam insulation may be able to substitute semi-rigid mineral wool for rigid foam. This approach works in the following…
Weekly Newsletter
Get building science and energy efficiency advice, plus special offers, in your inbox.
This article is only available to GBA Prime Members
Sign up for a free trial and get instant access to this article as well as GBA’s complete library of premium articles and construction details.
Start Free TrialAlready a member? Log in
31 Comments
Page not found on the "Pier Foundation" link as it ties back to GBA.
Joe,
Thanks very much for letting me know. Sorry for the problem. I've fixed it.
Hi Martin:
I'm a bit confused, why can't mineral wool board products be installed on the inside of a concrete basement wall? Yes, the insulation is air permeable but if it is adhered to the concrete, that wall can serve as the air barrier and it won't trap moisture.
I'm looking at $10 for a 2'x4' 1.5" (R-6) thick rock wool board for an unfinished (conditioned) basement in CZ 3A (continuous R-5 is code for basement walls here).
Other than cost of $1.25/ s.f., am I missing something as to why this won't work?
Thank you, mikeb
Mike,
During the winter, a concrete basement wall is in contact with the cold outdoor air and the relatively cold soil. That makes the concrete colder than the indoor air. At the same time, the air in a basement is relatively warm and humid. That sets up ideal conditions for condensation: the cold concrete is the condensing surface, and the warm indoor air is the source of moisture. This type of condensation can lead to drips and puddles -- or even a band of frost at the top of the basement wall.
That's why interior wall insulation in contact with a basement wall needs to be air-impermeable. Good choices include rigid foam (polyisocyanurate or EPS are preferred by green builders) or closed-cell spray foam. For more information on this issue, see "How to Insulate a Basement Wall."
All of this said, the risks are greater in cold climates than in warm climates. In Zone 3, you will have fewer hours per year with condensation risk than would be the case in a colder climate. Still -- why take the risk?
Understanding the science of condensation; but rather than foam, could a liquid applied membrane (ex. Visconn, Partell VaraFluid, SIKA LAM, or even UGL Drylock) be used then rockwool affixed on the interior of concrete/CMU walls?
David,
Applying a membrane to the concrete doesn't help, because the source of the moisture is not the concrete -- the source of the moisture is the indoor air. The only way to avoid a cold condensing surface is to install an air-impermeable insulation like rigid foam -- something with R-value -- directly against the concrete.
Great article!! Pier foundations make a lot of sense, particularly if they can be accomplished with no concrete ( I love concrete as a building material but the imbedded energy/c02 is too great). It makes little sense building an efficient house of the embedded energy is too great. Helical piers are great as are wood pilings or posts. I have a house at the jersey shore built on a combination of helical piers and wood pilings. There are thousands of big beach homes on treated wood pilings driven into the ground that have lasted generations through hurricanes etc. The key is to use wood treated for direct burial, not just ground contact. Same is true for the thousands of pole barns in mostly rural areas. If you use the right treatment it works ( you can also get pilings costed with vinyl and fiberglass pilings).
If you build a raised wood frame, think about using floor trusses with open webs and fill the floor with blown fiberglass or cellulose. This reduces thermal bridging that you get with solid wood joists. Also the chase for water lines should be carefully detailed and sealed well all the way to belie frost line to avoid winter freezes.
Added bonus of raised floor: easier to keep out radon and pests!
Any way to build using helical piles, but to insulate like a crawlspace (ie on the perimeter rather than the floor joists?) Seems that plastic vapor barrier across the floor and up a hanging wall extending down from the joists into the dirt might possibly be done? Maybe concrete board with semi-rigid rockwool on the inside or out?
I think the latter makes sense-Hardieboard skirts with rock wool inside should work. What would be the reason to do this instead of leaving it open? If you are worried about wind, perhaps you could install louvers (1x6's on 45 degree angles) all the way around or on the windy side
James,
Q. "Any way to build using helical piles, but to insulate like a crawlspace (i.e. on the perimeter rather than the floor joists?)"
A. Yes. I wrote an article on the topic: “Crawl Spaces vs. Skirts.”
James,
You can, although I'm not sure it's a good idea.
The starting point is that from a building code perspective there is no middle ground. Once you enclose the area under a building constructed on piers with a skirt, it becomes a crawlspace, with all the attendant requirements that come with that (Ventilation, heat, insulation, radon mitigation, drains, access, etc.).
So you need to figure out how to provide all the things a crawlspace requires without the protection a concrete foundation affords. (Cladding, sheathing, framing, insulation, air barrier, etc.) to the frost depth.
If I was going to attempt it I'd try to detail it like a pt. wood foundation. I suspect what you end up with is a crawlspace with a lot of compromises.
My question is why would you want to do this-what benefits does a crawlspace afford over just leaving it open? You can keep animals out by sealing it up with mesh fencing material and it is not hard to insulate the plumbing chase... seems like a lot of wasted concrete or wood......
Nick,
Q. "What benefits does a crawlspace afford over just leaving it open?"
A. There are many: (1) A crawlspace does a better job of keeping pipes from freezing -- and doesn't require electrical heat tape to do so. (2) A crawlspace provides a location for your water heater, horizontal furnace, or limited storage. (3) Done properly, a crawlspace will probably be more attractive to a buyer than a house on piers, if you ever sell the house.
Fair enough...Most of my experience is in flood zones where you cannot put mechanicals in the crawl space. Also, Aesthetically you can cover the open space with lattice work panels that look pretty nice depending on the style. As for the plumbing chase they are pretty easy to make with hardieboard and rock wool or foam board.
My point is that as I consider the world we live in I just can’t justify using concrete where there is a viable alternative. As much as I love masonry work, for single family construction if we can do without, do without.
Thanks for this Martin.
I’m seriously considering and slabless slab (Michael Maines style) but using a Perment wood foundation for a stem wall. Any thoughts on this. Any examples out there.
Andy,
If you are building a Permanent Wood Foundation (PWF) for a crawlspace, you have to follow the PWF details to prevent the bottoms of the walls from being driven inward by soil pressure. Options include deeply buried stemwalls or anchoring the bottom plate of the stemwall to a concrete footing. See details in the illustration below. (Click on an image to enlarge it.)
Thanks Martin. I should have said Grade Beam like Michael did below. These would end up deeply buried, nearly entirely.
Andy, I've been thinking about the same thing, a raised "slab" design using a pressure treated wood grade beam. Martin's advice is right on for a crawlspace, but I don't know of any details available for using wood as a grade beam. If you come up with proposed details, a creative structural engineer would be able to sign off on them (possibly with changes). If I do it first, I'll publish my results.
Thanks for the reply. I'll stay in touch, I'm ready to be a prototype if I have to.
As I see all of us still struggle with what to call these things, something just occurred to me. The site for this build I'm planning is a infill lot with a tear-down shack on it that I bought. When looking at it, I had to inform the realtor that it was not a slab-on-grade but more of a "frame-on-ground" as I called it. (it's a disaster) I am now realizing that what I'd like build is actually going to be a kind of frame-on-ground as well. So, I'll formally propose "Frame-On-Grade" as a potential term. Thoughts?
A thickened edge concrete slab is basically a slab attached to a grade beam. If the drainage and the radon and waterproofing are well done I don' t see why a wood beam and a triple layer of OSB could not be substituted for the concrete. And called a slab with a grade beam. According to my calculations on my plan the wood slab on grade idea material costs are between one quarter and one third the material costs of the same thing in concrete
Andy, I just noticed I hadn't responded to your proposed term--I agree that frame-on-ground is an accurate description. Last year at the FHB Summit I presented a few details for concrete-free floor systems, including one that Elizabeth DiSalvo of Trillium Architects (this year's FHB House designer) has done a few times, placing open-web wood trusses in a foam "bathtub," which I called a frame-on-grade, so we're thinking along the same lines.
We also talked about this on a recent BS + Beer Show. My only concern is that if the framing cavities are not insulated, being an interstitial space, there is a chance that moisture could accumulate in certain conditions. Steve Baczek suggested adding a few floor registers and a small heating source in that floor space, which would obviate any concerns.
One of the things I recall from using helical piers is that due to the lack of cross section width they have relatively little resistance to lateral forces. I recall moving the shafts around by hand. Often this was addressed by having them imbedded in a concrete grade beam; but if the goal is to eliminate concrete and use them as piers to hold up a wood beam like the Ecocor example, the steel bracket connection to the beam becomes very important and must be robust. Also, the joists should be tied into the wood beams rather than merely toe nailed to reduce side to side movement of the entire platform. Larger Simpson hurricane ties on every joist to beam connection or even steel straps may be needed, but then sealing the bottom of the floor becomes a little more difficult as you have to work around the ties or straps. I would be curious to see how Ecocar addresses these critical connections.
Nick,
I didn't end up using them, but the manufacturer I was in contact with supplied cross-bracing if it was required as part of the engineering package.
http://helipile.com/helical-piling-technical-specifications
Yes, I built a shed on helical piles in expansive soils. In late summer, when everything was bone dry, the dirt pulled away from the ground level of the piles and there was significant sway.
And that is with joists running across the top of two beams (so exactly as you suggest avoiding!). It's definitely an issue and quite disconcerting
When rain came back things locked up again (but this is a tiny one story building). No way I'd do something larger without locking the piles together without cross bracing (installers said they pour a concrete beam for larger places, although the soil movement would almost certainly break that). I am joining to join the ends of the beams with a vertical 2x12 to offer some resistance.
Not sure how much above grade height the cross bracing requires, but it certainly seems something to design for (see Malcolm's link below).
I can imagine. I have been in shore houses high up on pilings during hurricanes and you would be amazed how much a house can sway!!
A deep ( tall) grade beam with a lot of rebar is one way to deal with that type of situation. When 18” or more of the shaft of the helical is imbedded in the grade beam it drastically reduces the sway. Cross bracing as mentioned by Malcom Taylor also helps and may be required if the structure is high enough off the ground. Another approach is to run helicals on 45 degree angles in threes and even fours, creating a stool like effect (more common in large commercial structures or utility towers and the like).
There are also these used mainly in areas with permafrost: http://multipoint-foundations.com
This looks like a very interesting solution! I wonder about cost and whether this much steel has a smaller CO2 footprint than concrete..but it is an amazing solution to a lot of foundation problems.
I don't mean to intrude on such a dated comment, but I have been researching these articles regarding helical piers trying to decide whether to insulate the floor system or the "skirt". Along the way I've witnessed the hesitancy and concern over lateral bracing but you're the first to mention the use of them at 45 degrees. I just wanted to testify that an engineer at Techno Metal Post proposed just that for a deck and screened porch I designed and built and it work perfectly, not to mention its a rather strong structural articulation which looks pretty cool on full display. Anyway, nice advice! Thanks
As usual, great article, however I am confused by your prohibition on air permeable insulation. It would seem to assert that air barriers cannot be built. As sheet foam however impermeable is not itself an air barrier system, it can only be part of an air barrier when installed with standard air barrier details. Since it sounds like you are saying they won't work, that only leaves us with spray foam, of the right type and thickness. Since there is also a problem with moisture ingress through the concrete (over the life of the wall), moisture mastering mineral wool would seem to offer some advantages?
Peter,
I assume you are talking about the best type of insulation to use on the interior side of a concrete basement wall or a concrete crawlspace wall. As I wrote in my article, air-permeable insulation like fiberglass or mineral wool is inappropriate in this location. Better choices are air-impermeable insulations like rigid foam with taped seams or closed-cell spray foam. For more information on this topic, see "How to Insulate a Basement Wall."
Peter,
Here's more information on air barrier integrity at this location: With closed-cell spray foam or rigid foam with taped seams, there is almost no air to worry about. With fiberglass batts or mineral wool insulation, however, the insulation consists of lots of air between the fibers. Even if you try to create an air barrier between the batts and the interior of the basement -- not impossible, but difficult, assuming you are using either polyethylene, a European air barrier membrane, or drywall -- you still end up with trapped air between the fibers. That trapped air is indoor air (in other words, moist air), and, because of daily temperature and pressure fluctuations that normally occur, there is always the possibility of a long-term "pumping" cycle whereby the air between the fibers is exchanged with indoor air, bringing more indoor humidity between the fibers. (It takes only a very small hole in the air barrier for this pumping cycle to occur.)
Eventually you end up with condensation, and eventually, the risk of mold or rot.
Log in or become a member to post a comment.
Sign up Log in