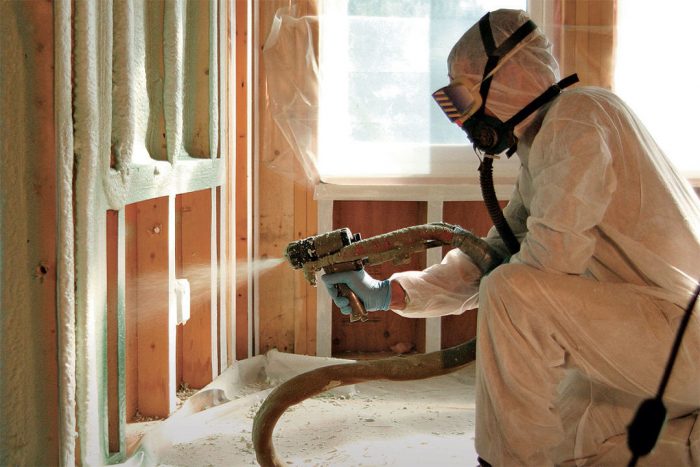
Closed-cell polyurethane spray foam is amazing stuff. It’s a great insulator, with a higher R-value per inch than almost any other commonly available material. (Polyisocyanurate foam can be equivalent, but it varies with product and temperature.) When installed at least an inch or two thick, it essentially blocks water vapor and air movement. It even has some structural benefits: It’s good at adhering sheathing to framing, and it also enhances racking resistance. Thanks to these qualities and more, including strong marketing from the industry, closed-cell spray foam is only getting more popular. Unfortunately, it also has some serious issues that aren’t typically discussed outside of green building circles. Understanding these drawbacks may convince you to limit its use to those special situations in which it makes the most sense, or even to avoid it entirely.
Polyurethane spray foam starts as two containers of liquid chemicals, referred to as the “A” side (isocyanates, the primary component of the solid foam) and the “B” side (a blend of resins, catalysts, a blowing agent, a flame retardant, and other compounds). When combined during installation, the chemicals react to create a polymer filled with tiny bubbles. The bubbles, or cells, are filled with a blowing agent and provide the insulating value of the material, while the polymer forms the cell walls.
The ingredient that makes closed-cell foam special is the blowing agent—typically HFC-245fa—but that’s also its biggest drawback.
HFC-245fa is a hydrofluorocarbon refrigerant and a persistent greenhouse gas; it goes up into the atmosphere and stays there, preventing heat from escaping the earth. Carbon dioxide is commonly used as a measure of the damage a greenhouse gas can do, and HFC-245fa is considered 1030 times worse than CO2. The only common building product more potent is the…
Weekly Newsletter
Get building science and energy efficiency advice, plus special offers, in your inbox.
This article is only available to GBA Prime Members
Sign up for a free trial and get instant access to this article as well as GBA’s complete library of premium articles and construction details.
Start Free TrialAlready a member? Log in
29 Comments
“[Deleted]”
Thank you Mr. Maines.
This is an excellent and very informative article. It is very nice to see the numbers and learn about alternative blowing agents.
Thanks Cory!
Hi Mike,
It seems that you might be the most familiar with Matthews Brothers Windows and I would like your advice/opinion. Gut reno in CT using dense packed double stud wall w rain screen assemble and 18" I beam roof. I was sold on MB triple pane casement Sanford Hills windows (supposed U18) but builder seems to be trying to disuade me. He has mentioned Harvey (which may be fine - but I cannot see them in person). Now I find myself concerned-and looking at Logic and/or Wasco/Access window tilt/turns instead. I was going to use Access entry and slider doors anyway since MB doors are not as efficient as their windows. Wondering if you had any thoughts on this dilemma. Thanks so much.
Andy
Andy, I have some experience with Mathews Bros windows but not a lot. I recommend asking this as a stand-alone question since it doesn't really fit the theme of this thread.
Great piece, Mike!
Thanks Dan!
Mitigating the tragic Supreme Court decision, six states have enacted legislating with similar rules to those that were dropped federally: California, Washington State, New York, Maryland, Vermont and Connecticut. This should at least make alternatives more readily available in other states as well--it will be interesting to see how the industries (XPS in particular) respond.
There's also a bill in the Senate to reinstate the rule that was struck down, which according to the article below, has "growing support".
https://www.coolingpost.com/world-news/support-grows-for-us-phase-down-legislation/
Charlie, that is great news and I had not heard that six states were moving forward with outlawing HFC refrigerants/blowing agents. Thank you for sharing.
For more on the court's involvement in rescinding the EPA rule: http://r744.com/articles/8605/u_s_supreme_court_won_t_hear_hfcs_case
A very compelling article, but what can I do instead for an insulated cathedral ceiling that must be insulated on the inside?
How else can I air seal the rim joist and bands between floors?
NJ, Martin covered the topic of cathedral ceilings thoroughly here: https://www.greenbuildingadvisor.com/article/how-to-build-an-insulated-cathedral-ceiling.
There are various methods for insulating rim joists. One that I like is to inset the rim by 1 1/2" or 2" and fill the space with rigid insulation (ideally wood fiber, but mineral wool, EPS and polyiso also work) to control the dewpoint location, then add batts at the interior. Sometimes we'll dense-pack the rims with cellulose then install and air-seal solid blocking. Sometimes it's a batt of mineral wool or Havelock wool with a variable-permeance membrane sealed at the interior. Often I just spec HFO-blown foam for those locations because I need to pick my battles and foaming those locations provides a decent bang for the buck.
>"There are various methods for insulating rim joists. One that I like is to inset the rim by 1 1/2" or 2" and fill the space with rigid insulation (ideally wood fiber, but mineral wool, EPS and polyiso also work) to control the dewpoint location, then add batts at the interior."
A couple of things...
1: Neither rigid mineral wool nor wood fiber insulation are sufficiently vapor retardent to protect the band joist or sheathing from interior side moisture drives. Rigid mineral wool is also too air permeable to ever be considered the "first condensing surface". While some rigid wood fiber can be dense enough to be the first condensing surface, it's still WAY too vapor permeable for some applications.
2: Dew point is an air temperature, never a "location". While the seasonal average anticipated indoor dew point is an important consideration when designing building assemblies and the placement within the assembly of the first condensing surface to avoid or limit seasonal moisture accumulation, the placement of that surface isn't a "dewpoint location".
"Neither rigid mineral wool nor wood fiber insulation are sufficiently vapor retardent to protect the band joist or sheathing from interior side moisture drives."
Is the issue here that a wall of similar construction would have some drywall with vapor retarding paint (or some other vapor retarder) on the inside?
I didn't realize there was need for vapor control with sufficient exterior insulation.
Tyler, when the ratio of interior to exterior insulation is anywhere near code-minimum "safe" levels, you still need to slow air and vapor from getting into the assembly--the IRC assumes a 45°F surface is safe, but 70°F air at 40% RH will condense on a 45°F surface. If the condensing surface stays above 55°F, air would need to be 70°F and 60% RH to condense; that requires a higher ratio of exterior to interior R-values.
Reply to Tyler, #19:
>"The way Dana mentioned that exterior mineral-wool/wood-fiber is too vapor open in that location makes it sound like the assembly needs more vapor retardancy, regardless of location? Or does it have to be on the inside? If it can be anywhere, I'm not sure I understand, and in fact in seems like an insulation with more drying potential to the exterior would only be an improvement."
I understood Dana to mean that mineral wool or wood fiber at the INTERIOR would be too vapor-open for a safe assembly, which I agree with. If installed on the exterior, vapor-open or vapor-closed does not matter a lot as long as the R-value ratio of interior to exterior is enough to provide dewpoint control. (Qualified with "does not matter A LOT" because in cold climates assemblies that can dry to the exterior are more resilient, in my view, which does not follow standard GBA opinion.)
>"Would rigid foam in place of mineral wool (in the location you mentioned, exterior of rim) be an improvement, or is it that the interior needs the retarding layer? Some sort of drywall, ply/osb, membrane interior to the fluff and sealed well."
As long as the rigid foam has enough R-value compared to the interior to keep the condensing surface (or condensing surface of interest, in case Jon R. is reading) at a warm enough temperature to prevent moisture accumulation, it should work fine. If the R-value of the exterior insulation is too low compared to the interior, moisture can accumulate. If the exterior insulation is vapor-permeable the assembly will dry out eventually. But it's better if it doesn't get wet in the first place.
Don't feel bad--this stuff is hard to explain, and I've found that the vast majority of architects, builders and even many engineers don't fully understand it. (I sometimes say something stupid but Dana keeps me in line.)
Dana,
1. It may not be clear but I'm saying that I sometimes add exterior insulation at the rim joist so the condensing surface stays warmer. I never leave batts or other vapor-permeable insulation uncovered.
2. Good point; I answered in haste. I usually say "dewpoint temperature" to make sure people understand the same thing you are saying. "Dewpoint location" obviously relates directly to condensing surface. I'll stop using that shorthand to avoid confusion.
The vapor stuff still confuses me a bit. Just to be sure I understand:
The way Dana mentioned that exterior mineral-wool/wood-fiber is too vapor open in that location makes it sound like the assembly needs more vapor retardancy, regardless of location? Or does it have to be on the inside? If it can be anywhere, I'm not sure I understand, and in fact in seems like an insulation with more drying potential to the exterior would only be an improvement.
Would rigid foam in place of mineral wool (in the location you mentioned, exterior of rim) be an improvement, or is it that the interior needs the retarding layer? Some sort of drywall, ply/osb, membrane interior to the fluff and sealed well.
>"It may not be clear but I'm saying that I sometimes add exterior insulation at the rim joist so the condensing surface stays warmer."
That makes more sense. Since the discussion was about closed cell spray foam, which is only rarely applied on the exterior, almost always on the interior, it's not apples to apples, especially for what's most likely to be a retrofit that a new design/build, inferring that from nj_homeowner's:
"...insulated cathedral ceiling that must be insulated on the inside..."
But sure, if starting the design tabula-rasa exterior mineral wool has some advantages over foam board or 2lb spray foam ($/R NOT being one of them).
I actually think "dewpoint location" is a useful term that should be coined and attributed to Michael. Defined as: the point in a building shell assembly at which the seasonal average anticipated indoor dewpoint will occur when at 99% design temperature conditions. Or something like that, I'm open to a better definition from someone smarter than I am but this is a theoretical location in an assembly we're all picturing in our minds it ought to have a name.
Thank you. I have read Martin's excellent article, but as I said I need to insulate from the inside. We have missed the opportunity for insulation on the exterior. I believe the only approach Martin finds acceptable in such a case is spray foam, hence my question.
>"I need to insulate from the inside. We have missed the opportunity for insulation on the exterior."
With more particulars about your roof construction it's possible to come up with what makes sense and what doesn't. Any unvented insulation approach from the interior may need some amount of closed cell spray foam to be a resilient long term solution, but simply blasting 7-8" of closed cell foam to hit 49 to call it "done" is a crime against the planet (and your wallet).
Using any more closed cell foam than is necessary for dew point control at the foam/fiber boundary of a hybrid stackup is environmentally & financially expensive. Putting it between framing it's higher R value per inch is largely wasted by the thermal bridging. Do the math:
https://www.finehomebuilding.com/2017/07/10/closed-cell-foam-studs-waste
In most of NJ, 2" of HFO blown closed cell foam (R14) would be the maximum that would be rational from a cost/benefit point of view (balancing environmental & financial aspects) which is sufficient for dew point control on an additional R30 of fiber insulation. In the climate zone 5 counties in northern NJ it would take just 3" (R21-ish) to cover R30. See TABLE R806.5 of the NJ building code:
https://up.codes/viewer/new_jersey/irc-2015/chapter/8/roof-ceiling-construction#R806.5
Those numbers are for a presumptive R49 total, but it's the ratio of the foam/total that determines the average temp at the foam/fiber boundary, when the fiber insulation is snugged up to the underside of the foam. (In most locations ~R38 total would even be accepted as a retrofit, which could be 2" of HFO blown foam + R23 rock wool batts in a 2x8 rafter bay.)
HFO blown 2lb foam is NOT green. It has more than twice the CO2e impact of fiberglass batts per R, but it is sometimes the lesser evil in retrofits.
https://materialspalette.org/wp-content/uploads/2018/08/CSMP-Insulation_090919-01.png
One pound density rigid polyisocyanurate (not shown in that chart) has about half the impact of HFO blown closed cell spray, making it somewhat comparable to mineral wool or fiberglass, but with rigid foam it's far better to put it above the roof deck.
Thank you for these thoughts. It does appear that spray foam is unavoidable for us at this point.
The insulator is proposing 3" Demilec HFO for R22, then fill the cavity with R19 fiberglass batts, for about R41 total.
We are in northern NJ, Morris County, borderline Zone 5, so 3" seems prudent.
What do you think?
Hi Micheal,
You touched on it briefly under 'Stickyness and Structural Qualities' but I think it may be worth highlighting a bit more-- you mentioned that it makes everything it touches ruined and makes renovations more difficult. I often tell my clients and others in the AEC industry that by using foam in a wood assembly you are encapsulating perfectly good wood for essentially an eternity that could otherwise be re-used in the future, repurposed or composted. There are plenty of situations where the benefits of foam outweigh other options; in particular in existing basement renovations and in cold climate vaulted roof assemblies that one could substitute rigid foam board. At least this material could be repurposed in the future and doesn't encapsulate perfectly good wood from a cradle to grave perspective.
Thanks for the research and great article!
Joshua, all good points. While I prefer to design for disassembly and re-use, I've done a lot of remodeling as both a designer and a builder and the reality is that on the vast majority of projects the materials are sent to the landfill, and the components that can be burned will be burned. At least that's the case today in my area. But you're right.
In existing basements, I grill clients on how they plan to use the space. If it's a New England rubble foundation, there is a good chance that the basement will always be a utility space, and simply spray foaming (with HFO-blown foam) is the simplest approach. If it's an existing basement with concrete walls but they plan to use it as utility space, I spec white Thermax brand polyiso as a finished-looking, code-compliant, one-step insulation. If it will be finished space, we either do regular polyiso with strapping and drywall, or frame a stud wall spaced off the foundation and spray foam the cavities. Or frame a stud wall in front of a layer of rigid foam, with or without batt insulation in the cavities.
>"The insulator is proposing 3" Demilec HFO for R22, then fill the cavity with R19 fiberglass batts, for about R41 total.
We are in northern NJ, Morris County, borderline Zone 5, so 3" seems prudent.
What do you think?"
I think 3" of HFO blown foam is probably overkill, but meets the R20 min code prescriptive. R19 batts are pretty junky- more of an air-filter than an air retarder or insulation. If you're going to do 3" foam, use R21HD fiberglass or R23 rock wool for R43-R45, which still has plenty of dew point margin at the foam/fiber boundary in zone 5.
The stackup implies 2 x 10 rafters? ( 3" foam + 6.25" R19 batt= 9.25").
A cheaper version that would deliver almost the same whole-assembly R would be 2" of HFO blown foam (R14), leaving enough space for an R25 fiberglass batt (8" nominal loft), which delivers R24 when compressed to 7.25", for R38 total, and R14/R38= 37%.
That's below the ratio of the IRC prescriptives, but close, should good enough on the warm edge of zone 5. The roof deck is fully protected by the low vapor retardency of the foam- the only issue is whether it's cold enough long enough to wet the fiberglass using only latex paint as the interior vapor retarder. (At the recent rate of climate change in less than 25 years that part of NJ will probably be in zone 4. :-( )
Vapor barrier latex paint or a layer of MemBrain "just to be sure" (and to meet code for vapor retardency) should be cheaper than the third inch of foam, even after factoring in the upcharge for R25s instead of R19s. The R3 difference in center cavity R translates into about a 5% difference in heat loss for most roofs (depending on actual framing fraction and framing species). That would be about an 8% increase in heat loss at center cavity, but pretty much identical loss through the framing fraction.
Thank you Dana for these interesting ideas. The insulator says he will not install 2" in the roof because "it's not enough." We do have 2x10 rafters.
I like your suggestion of upgrading the batts but is it really worth it? I have a feeling it's going to be expensive, because his price for insulating the walls with mineral wool instead of R15 and R21 Kraft-faced fiberglass was more than double.
I like the idea of mineral wool insulation but that is a crazy premium to pay for apparently modest benefits. Am I missing something?
R21 fiberglass is usually pretty cheap compared to R23 rock wool, and it's about the same air-retardency. In your stackup unfaced is fine, but if it's any cheaper, kraft faced is also fine.
Alternatively mid-density R20s should be DIRT cheap, since 2x6/R20 is the current code min, and it's being manufactured in high volumes, always in stock a distributors. The air retardency of R20s in 2x6 framing is about the same or slightly better than R13s used in 2x4 framing.
R19s in 2x6 framing have substantially WORSE air retardency than R13s or R20s, and when compressed to 5.5" it's only performing at R18. The weight per square foot of an R19 is identical to R13s, and when compressed to 3.5" in a 2x4 cavity it performs at R13- it's essentially a fluffed-up-stretched-out R13.
Despite the only marginal difference between R20 and R19 on paper, don't install anything less dense than an R20.
So just to clarify... You are saying that I should insist on batts that are greater than R19, which are far superior but should cost very little extra money?
Thanks for raising awareness about some important environmental and health concerns around spray foam insulation.
Unfortunately there's another issue that the article leaves out. To my mind it's actually the most concerning. The chemistry of flame retardants used in various kinds of plastics, including spray foam, has long been a source of concern to scientists who study this stuff. Halogenated and brominated flame retardants are known to be persistent, and bioaccumulative, and studies suggest they exert worrisome low dose toxicity effects, including endocrine disruption and interference with fertility.
As far as I know closed cell spray foam usually contains 5-10% flame retardant by weight (and open cell much more--20-25%) , so a typical spray foam job might use hundreds of pounds of a chemical that never breaks down, accumulates in living things, and has serious effects in the parts per million range. And because manufacturers don't list ingredients (the MSDS simply says "flame retardant"), it's hard to know what exactly you are getting.
More information here: https://greensciencepolicy.org/topics/healthier-insulation/
It's odd to me that we keep putting this stuff in our homes, especially when there are almost always good alternatives.
This must be at least partly due to the fact that cellulose manufacturers don't have the marketing and political clout that big chemical companies do.
Log in or become a member to post a comment.
Sign up Log in