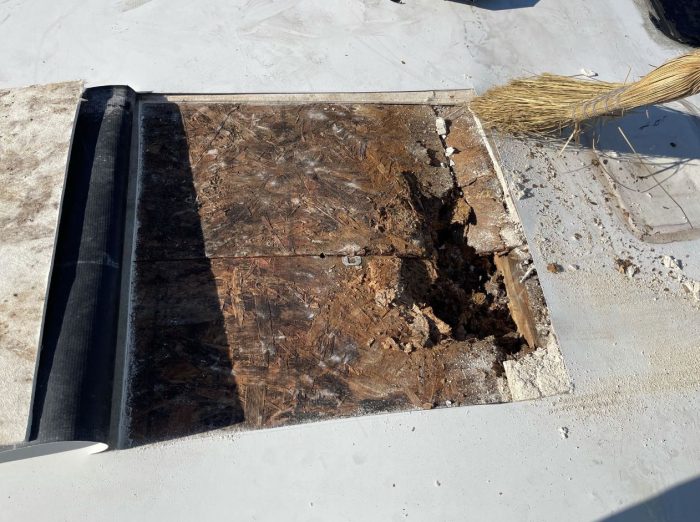
It’s not particularly surprising to learn that many designers and builders don’t read Green Building Advisor. But here’s what is surprising: many American designers and architects still don’t know how to design a low-slope roof. According to a Michigan envelope failure consultant, Matt Dupuis, hundreds of relatively new buildings, most completed within the last 3 to 10 years, have rotting low-slope roofs—roofs that are in such bad shape that they result in litigation over repairs costing hundreds of thousands of dollars per building. The designers of these buildings committed elementary design errors that any GBA reader would have easily avoided.
Dupuis is a licensed professional engineer; he’s also the president of Structural Research Incorporated (SRI), a consulting firm in Waunakee, Wisconsin. In early August 2023, at the Building Science Summer Camp in Westford, Massachusetts, Dupuis gave a fascinating (and chilling) presentation on a growing cluster of failed low-slope roofs.
Install the insulation on the exterior side of the roof sheathing
The traditional way to build a low-slope commercial roof is to install a continuous layer of rigid foam insulation on the exterior side of the roof sheathing. This insulation approach results in a so-called “hot roof”—that is, an assembly designed to keep the roof sheathing warm enough in winter to avoid moisture accumulation or condensation.
Dupuis reports that around 10 years ago, some cold-climate designers who were looking for ways to lower construction costs decided to switch to a “cold roof” approach—a cost-cutting measure that Dupuis blames on the value engineering. While the concept of value engineering—basically, using contractors’ experience to find ways to cut construction costs—makes sense in theory, it only works if designers avoid risky assemblies. In the flat-roof fiascos described by Dupuis, the designers didn’t know much about cold-climate roof assemblies, so the…
Weekly Newsletter
Get building science and energy efficiency advice, plus special offers, in your inbox.
This article is only available to GBA Prime Members
Sign up for a free trial and get instant access to this article as well as GBA’s complete library of premium articles and construction details.
Start Free TrialAlready a member? Log in
8 Comments
For architects or designers, the solution to this and other similar problems is easy: Make a list of climate related risks for where you work, and design assemblies that mitigate them. That might include deep roof overhangs in the PNW, and none in hurricane areas, or things like excluding the use of exterior foam in regions with termites or carpenter ants. In single family dwellings, low slope roofs are almost invariably included for purely aesthetic reasons. A good designer should be able to achieve the look you want without resorting to risky assemblies.
A new apartment complex near us. The sloped shingle roof is almost unnoticeable.
And you have to protect the rest of the building while you're doing the repair!
That is good idea for another GBA article.
A few weeks ago I did a 5k mile road trip to MI, MI-UP, WI and down to TX. I got to visit my ol' stomping grounds around Novi, Ann Arbor, Detroit, Cobo Hall (yes, it was name after ME)🤪... Now that I'm somewhat knowledable in BS, I got to realized how many northern climate buildings are built with flat roofs, and many of them where really old buildings.
I question whether it was/is cost savings? Using snow accumulation as insulation? Knowledge or lack of it?
I imagine most of the old roof assemblies were cold roofs, and the unsealed and uninsulated assemblies had chances to dry if they got wet. Once folks started remodeling with insulation and some level of airsealing, many problems started showing up.
Designing and building cold roof assemblies in NM for years has been very forgiving with very low humidity, no rain and little snowfall... and yet, most houses today are build with warm flat roofs.
Last month I received a call for a roof like this from a forensic engineering firm who asked me to estimate making 10 or 12 investigative cuts up thru the ceiling. It was at an assisted living facility here in CT and the flat roof sheathing was collapsing and causing ponding.
The assembly was a finished GWB ceiling, a Utility chase for duck work etc. then a double layer of GWB above that and then an insulated cavity filled with either cellulose or fiberglass. No insulation above the roof deck. In the end I could not meet their schedule, so we did not do the job, but it sure sounded interesting.
Most of the urban residential buildings in Montreal and Quebec City (cold-weather climates similar to northern New Hampshire and Vermont) have very similar roof assemblies, without issues, due to a few important details. They are vented - these days typically with this type of vent: https://ventilation-maximum.com/en/ - in at least two locations on a standard 25 x 45' roof. This keeps the air space between the top of the blown-in insulation and the underside of the sheathing cold. It's critical. In retrofits and new construction, there will typically be furring on top of the open-web joists to allow for increased continuous ventilation under the sheathing (Canadian code requires about 2.5 inches of ventilation space). As an architect, I do not put ducts in the ceiling unless we are sure they are going to get good insulation coverage above them. If we do, they are 4" high max and have at least 8-10 inches of cellulose above them. And we install continuous board insulation (R4) minimum with an integrated vapour barrier below the joists.
Yesterday I saw a really smart roof design on a five storey apartment building under construction in the town near us.
The roof is pitched, but has a flat section about 25 feet long near one end, then the pitched roof continues for another 25 feet or so at the gable end. Access is from the end of the apartment corridor, the flat area has railings so no fall protection is necessary when servicing the roof top equipment mounted there, and you can continue on into the mechanical room, which is isolated from the rest of the building. Seems like the best of all worlds.
Would love to hear how these recommendations might change with a SIP low slope roof.
Log in or become a member to post a comment.
Sign up Log in