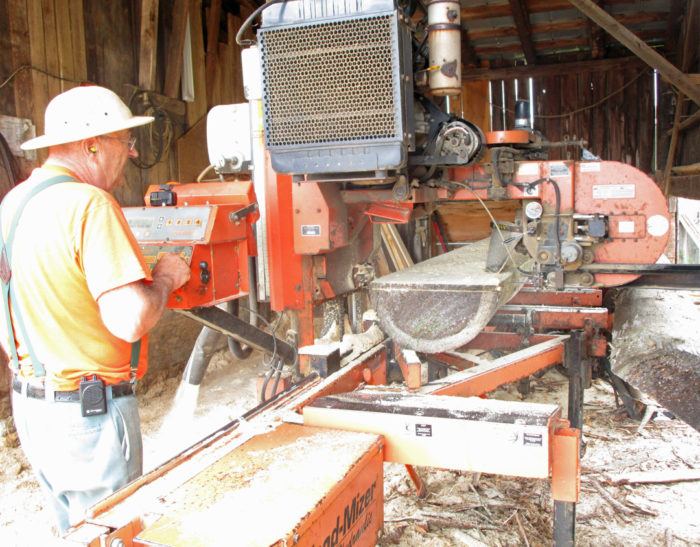
Image Credit: All photos: Martin Holladay
Let’s say that you own a piece of land and you want to build a house. If you live in a forested region, the first step is to cut down enough trees to create the needed open space for your foundation, lawn, and driveway.
As you’re cutting down the trees, you may think to yourself, “I’m going to need to buy lumber to build my house. I wonder if these logs can be milled into 2x6s and 2x10s.” The answer is: they probably can.
If you live in a rural area, someone in your town probably owns a portable bandsaw mill. This type of mill can be transported to your site, and in just a day or two, the mill will transform your logs into piles of framing lumber and boards.
Local lumber for local needs
Over the past 40 years, my friends and I have built lots of buildings with green lumber, including homes, garages, barns, and sheds. Many of these buildings were framed with lumber milled by Leslie Ham.
When I moved to this corner of Vermont in the mid-1970s, Leslie ran a local cabinet shop. In 1995, Leslie decided to switch careers, and he bought a Wood Mizer bandsaw mill. He’s been a sawyer ever since.
Leslie is hard-working. He thinks before he speaks. Like many older Vermonters, he’s inclined to be thrifty with both money and words.
According to the old saying, when a farmer slaughters a pig, nothing is wasted: the aim is to use “everything but the squeal.” Leslie applies the same philosophy to trees. His sawdust is bartered or sold for bedding. Leslie has a sugaring operation, and his two vocations are complementary. All of the slabs (the outer edges…
Weekly Newsletter
Get building science and energy efficiency advice, plus special offers, in your inbox.
This article is only available to GBA Prime Members
Sign up for a free trial and get instant access to this article as well as GBA’s complete library of premium articles and construction details.
Start Free TrialAlready a member? Log in
9 Comments
Thanks Martin
Thanks Martin, this was a wonderfully written look at a craft that should be close to every woodworkers heart!
When I built my first house in 1976 I took all of the cleared trees (pine, maple and cherry) to be milled at an old sawmill that was nestled in the woods near the village where I lived - and run by someone just like Leslie. I coveted the wood and for over 40 years I seem to have been moving it around and waiting for just the right project - which has finally arrived. It will be used for the kitchen cabinets and counters in the house that I am currently building. There is something very circular about the whole thing and the wood feels right for the task at hand!.
One thing that you didn't mention is the magic of cutting into the wood and revealing whatever lies therein. I currently own a very small portable bandsaw mill (you can pick it up and load it into a truck) and I never tire of milling wood - every board is like a gift.
Garland Mill
Martin,
In some ways the opposite of a portable bandsaw mill but in other ways very much a blood brother, in Lancaster NH there's a water-powered sawmill operated by the Southworth clan on a commercial basis (http://garlandmill.com/the-mill/).
If you've never been there, it's well worth a trip (and maybe even a companion piece to this one). When I first visited there I kept thinking I was in the Shire.
--Paul Eldrenkamp
Rob
"Every board is like a gift". That rings true for me too. There is something immensely satisfying in building with wood that has come from a mill on site. We are lucky to have several portable ones nearby , and several mills that can supply larger pieces in our local community. They aren't water-powered like the Garland mill Paul writes about, but are still fascinating places to spend a bit of time poking around in.
Response to Rob Myers
Rob,
I smiled when you recounted the story of the 40-year-old boards that you've been air drying, awaiting the right project. I have stored lumber, too -- some of it decades old: cherry boards waiting for a furniture project, and lots of sugar maple boards, perfectly dry, awaiting a future floor. What project? What floor? I don't know.
Over twenty years ago, I decided I needed a new dining room table. I wanted to see how much of the work I could do myself. I went into the woods with my chainsaw and an Alaskan chainsaw mill -- a simple jig that cost me about $100. I found a very nice maple tree, and turned it into lumber about 2 1/2 inches thick. The chainsaw chews up a wide kerf, of course, but it was fun to do it myself.
I stickered the lumber for a couple of years, and I managed to finish the project about 3 years after I felled the tree. Our family has been eating off that table ever since. Projects like that are very satisfying.
Response to Paul Eldrenkamp
Paul,
Ben Southworth has been inviting me to visit his mill in Lancaster for several years, and it's been on my to-do list. I haven't made my way over there yet, however.
GBA readers will know Ben Southworth. He's a sawyer, designer, and Passivhaus builder who's been involved with several projects we've reported on (and who is active with NESEA):
Two Single-Family Passivhaus Projects in Maine
A True Net-Zero Gut Rehab, New England-Style
A Leaky Old House Becomes a Net-Zero Showcase
The photo used to illustrate one of Stephen Thwaites's articles shows a Passivhaus that Ben Southworth built for his parents.
You're right that living in northeast Vermont or northern New Hampshire is like living in the Shire. Most of us who live here have feet with leathery soles, and we all like to eat two breakfasts.
Live edge slabs for siding
Hi Martin,
I am new to milling and building and could use some advice. We are starting to mill white pine slabs for live edge board on board siding (don't worry, we'll be incorporating a rain screen as part of the wall assembly!). What's the best point in the process to remove the bark? Pre milling, post milling but pre-drying, or will it just fall off after a year of outdoor drying? The slabs are 7/8" or 15/16" thick.
Thank you!
Adirondack Siding
dayna...around here they call that Adirondack siding (http://hanklelumber.com/adirondack-siding.html). I've dreamed of finishing my house that way... What species of wood are you using? How are you treating the wood?
Response to Dayna Burtness (Comment #6)
Dayna,
You'll probably have to seek local advice; I don't have enough experience to help you. My only experience with removing bark from softwood logs concerns spruce and fir, not pine -- and every species is different.
Here's what I know about spruce and fir: When these trees are cut in the fall or winter, the bark is tenacious and hard to remove. When cut in the spring, during the season of growth, there is a wet layer between the wood and the bark that allows the bark to come off easily.
If you intend to leave the bark on the slabs and want to let the bark dry (and possibly curl) on its own schedule, I guess you don't have to do any work. Note that you risk insect infestation with this approach -- several species of insects live between the wood and the bark, and they are more likely to start chewing if you leave the bark on the logs.
If you intend to remove the bark from the logs, this work is easier to perform before the logs are milled than after. I've used a drawknife to remove bark from logs in the past.
Re: comment 7 and 8
Ethan -- I like that look! I was thinking vertical reverse board and batten siding with live edges but will have to see how I like using it on a small shed project first before committing to use it on the whole house in 2019. We have about 6 acres of 35 year old white pine and a Woodmizer LT10.
I am still researching ways to treat the wood. There are some timber framers here who have used untreated pine to side their homes and have had zero issues 15 years in.
Thanks for the feedback Martin. I will ask locals about strategies for dealing with white pine bark.
Log in or become a member to post a comment.
Sign up Log in