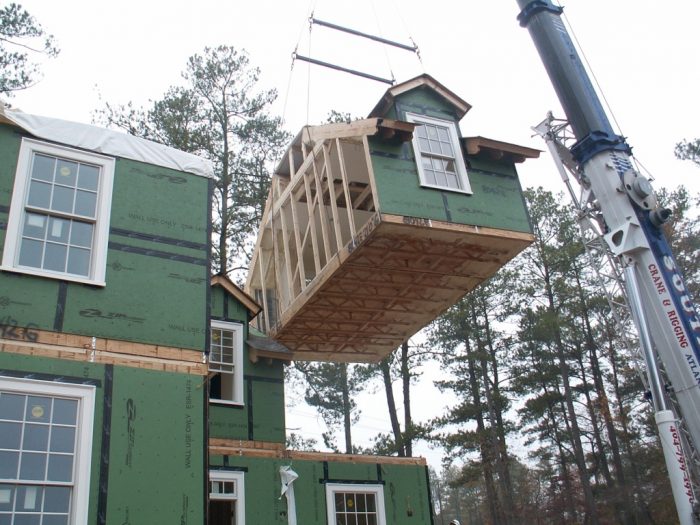
In March, I attended what may have been one of the last in-person industry conferences held for quite a while, the 2020 World of Modular, the annual convention of the Modular Building Institute, a non-profit trade association for the modular construction industry.
I flew to Orlando, Florida, sat in close proximity to others, shook hands, did not wear a mask, ate from buffets, and lived to tell the tale. Unfortunately, several scheduled speakers did not make it to the event, as concerns about COVID-19 were broadening.
The reason for my visit was to learn more about modular construction, my only experience with it having been certifying a few single-family homes back in 2008 to meet LEED, EarthCraft House, and the NAHB Green Building Program standards. Lacking thoughtful planning, these projects attempted to force modular components onto a standard house plan that wasn’t designed to take advantage of the benefits and efficiencies of the process. I always assumed that there was a better way to build modular.
Let’s call it manufacturing
As with most conferences, presentations ranged from fair to excellent. I found the presentation by the folks at Skender to be the most engaging. Skender is an old-line construction company that has made a significant commitment to modular construction.
While still a small portion of their business, their modular operation is intensely focused on collaboration among all their team members from design through to installation. Their standard product is a stackable steel module suitable for mid- and high-rise construction up to 12-stories for residential, hospitality, and healthcare projects. One of their focuses is affordable housing in urban environments where modular can help manage production on tight jobsites with limited space for material storage.
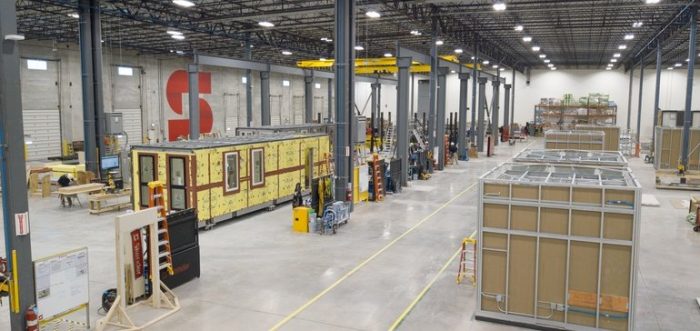
One of the great benefits of modular construction is eliminating the issue of weather for most of the construction process, but that is only the start. We need to think of modular not as construction, but instead as manufacturing, and take advantage of the efficiencies that factories offer.
Skender’s approach is standardization of the majority of their products—they build standard modules, with minimal variations. The modules can be skinned with different finishes, but the core structure does not vary, providing significant efficiencies in production. They work closely with their supply chains to provide prefabricated panels and mechanical systems. In other words, they have a bunch of components, in a kit of parts, to work with, that are assembled into modules following a basic set of step-by-step instructions. This also allows the company to reduce the number of highly-skilled tradespeople needed, and instead to train their own workforce to execute this processes.
Integrated teams are a must
One recurring theme of the conference was the need for integrated teams. Some modular companies have internal design and engineering staff, others work with outside professionals, but two things that are critical to project success are having everyone involved be experience with modular systems and having the entire team work closely together throughout the planning process. While integrated design is important to any project, it is key to the success of a modular project. Siloed teams and poor communication can derail a modular project even more than standard construction.
Low-voltage wiring is on the move, too
At most conferences I enjoy the random off-line conversations that occur outside of the scheduled events, something I will miss at several upcoming virtual events that are replacing in-person meetings for the time being. This was no exception, and in one such conversation I learned about Domatic, a startup that is developing a low-voltage power and communication system for buildings.
The concept behind this company is that most electrical devices, particularly everything from the waist up in buildings, does not need high-voltage wiring to operate. LED lighting, fans, alarms, blinds, and most electronics do not need 120-volts to operate. They can all use low voltage wiring to provide power as well as to control systems.
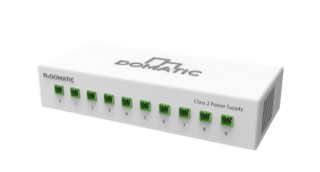
Domatic provides a unique IP address for each piece of equipment, which can be controlled by a device anywhere in the building. The use of low voltage wiring and eliminating the need for individual switch legs to control devices has the potential to significantly reduce the cost of wiring in buildings.
After learning about this system, I realized how many devices we have that require AC adapters to convert to low voltage DC to operate. In fact, a bedside clock I just purchased didn’t come with an AC plug, instead it is powered with a USB cable. It seems to make sense to skip a step and just power them directly. Major system changes such as this are not easy to implement, but I see how they can reduce costs and expand control options.
Let’s build building like we build cars
I came up with this analogy about construction a while back and share it with people periodically: If we bought our cars like we buy our buildings, we would order the parts, they would be dropped on the site, and people would show up speaking different languages, working for different companies, assembling the parts in the rain. After watching a car being assembled this way would you really want to drive it? We need to start thinking about buildings as sophisticated engineering projects and assembly them accordingly. Modular construction, when properly implemented will help move us along this path.
-Carl Seville is a green builder, educator, and consultant on sustainability to the residential construction industry. After a 25-year career in the remodeling industry, he and a partner founded a company, SK Collaborative. Photos courtesy of the author.
Weekly Newsletter
Get building science and energy efficiency advice, plus special offers, in your inbox.
10 Comments
How do modular homes compensate for changes in humidity between factory vs on the site?
Have there been humidity related failures?
John - I have not heard of humidity being an issue. I expect that most factories are enclosed but not necessarily climate controlled, conditions that are similar to site building with the exception that they don't get rain into the structure. Except in situations where the RH swing is dramatic, I don't expect that it causes many problems.
Re If cars were like houses....
I encountered this analogy some years ago in Rick Chitwood's classic book _Measured Home Performance_ Page 13:
"The value of an integrated approach
Imagine if cars were built and bought like most houses. Manufacturers would build each individual car outdoors, without weather protection, in the middle of a muddy fi eld.Each car would be slightly different in design and construction from all other cars. Cars would be designed under different laws, depending on where in the state or the country the muddy fi eld was located. Each component would be bid and installed by separate subcontractors, with different work forces, working under their own supervisors and arriving on semi-dependable schedules. In the rush to complete the vehicle, sometimes the battery or steering wheel would not arrive on site in time, so the manufacturer would tell the owner to “just put it on the punch list’ for eventual installation later, long after taking delivery.
Nobody would test the performance of any component except the car buyer, who would just check if “the upholstery looks nice and the seats feel good.” Prospective car buyers would never drive the car before they bought it, and the manufacturer would never test the car before offering it for sale. The engine, transmission, braking, heating and AC systems for the car would each have been rated separately, by standards set by different regulators. Nor would the prospective owner ever ask about the car’s mileage per gallon because no manufacturer would bother to measure how much fuel the car uses.
Given the way houses are built and bought, it’s not surprising that we can improve them by an integrated approach to retrofit which relies on in-process feedback and measured performance validation for a superior result—similar to the way modern autos are really built."
Norman,
If houses were built like cars we would also live in one of maybe five models, each generically designed with no consideration for the site, or the client's unique demands and desires. The primary consideration of the design would be to market them to various demographics, and the industry would be controlled and power concentrated by a handful of big players. Increased industrialization also ignores the size differential between vehicles and houses. We don't generally build things bigger than can fit on roads at a central location, so the components would have to be arbitrarily broken down into manageable pieces. Industrial production of objects also usually requires inventory storage to manage demand. The would be challenging with houses.
Malcolm, I think you misread? I was only quoting Chitwood in case Carl found the citation helpful. As a custom builder I find the analogy clever and somewhat useful in terms of reframing the notion of performance--why shouldn't your house have a mpg equivalent? Process is something else entirely.
Norman,
Yes, sorry - I used the post to try and think though some of the larger implications of modular construction, and I should probably just do it in my head, rather than on GBA.
Norman, thanks for the reference. I never read that book. I came up with the analogy a while back, I guess great minds think alike.
Thanks for this report from the industry. I seriously considered modular for a project I am working on but found the cons to outweigh the pros in the end. At least where I am (older residential neighborhood in Boston), the cost of land, financing, getting zoning relief, engineering, permits, utilities, excavation and foundation are by far the biggest hurdles. Framing, wiring and plumbing a relatively simple building is the (mostly) predictable, fun and not so expensive part by comparison.
Another aspect of modular is that it typically involves wider interior partition walls which is an issue when every square foot counts. Then there is the high cost and logistical challenges of transporting and installing the over-sized modules.
While modular housing has been touted as the future of housing for decades and can make sense in some cases, it’s never taken a large share of the market and there seem to be good reasons for that.
Modular definitely has its limitations along with its benefits. I agree regarding the lost interior space with double walls, and the tight site issue, although I have seen some situations where it works very well in tight inner city lots, particularly where there is limited space for storage of construction materials. One of the main benefits can be the quality of construction and avoiding water intrusion during the process.
Modular construction is making waves, huh? Totally get the trade-offs, especially with interior space. It's fascinating how it can work wonders in tight city spots, though. Quality construction is a game-changer! Btw, if you ever find yourself on the move, threemovers.com might have some handy tips. Cheers to the evolving world of modular construction!
Log in or create an account to post a comment.
Sign up Log in