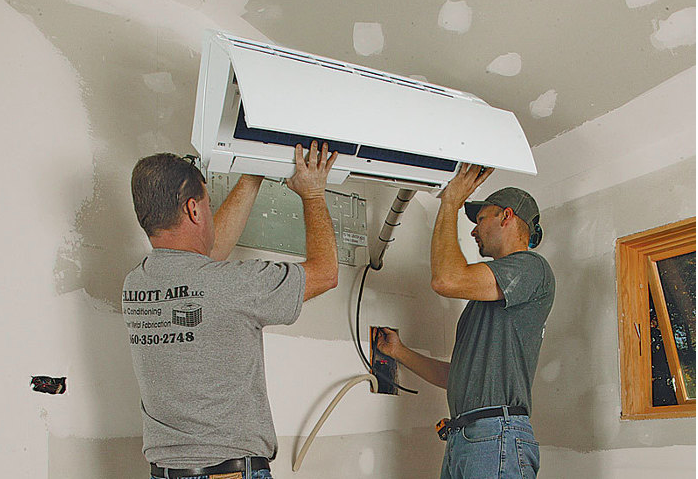
During my time as a contractor, I learned that it was important to double-check trade contractors’ work, and to learn as much as possible about their products and installation methods to ensure the quality of their work. We can’t all know every detail of each trade’s work, but it is important to understand enough to make sure things are done right. Whenever a problem arose, it led to an analysis, a (hopefully) straightforward solution, and information that could be used to avoid the problem on future projects. Sometimes it was a product issue but more often than not, it was the installation. In most cases, it was a matter of the installer not following instructions properly, or not reading them at all. Each problem was a learning experience, and usually led us to developing a process to make sure it didn’t happen again.
If we all had the time, we would carefully read instructions on all products, review the installation with the individual doing the work, and check the quality at each stage. Unfortunately, construction is a cost- and time-driven industry, and there is rarely enough time for that kind of careful attention to detail on every project. We want to trust professionals to do their work properly, and very often they do. Unfortunately, it doesn’t happen all the time, and mistakes lead to ongoing and costly problems.
My most recent personal experience with this was on the construction of my new house several years ago. As anyone who has read my posts on the project knows, I used ductless minisplits for my HVAC. One head on the first floor and two on the second floor condition the house well, however there were installation issues from the beginning. Although I thought they were resolved at the time, I have since learned that the original installer made some poor decisions that resulted in recurring problems.
The main issue was the location of the linesets. At the rough-in stage, the installer placed them on the right side of each unit rather than on the left side, where the connections are accessible. When the heads were installed, he had to cut open some drywall to complete the installation. At the time, I didn’t pay too much (certainly not enough) attention to the issue. There was a lot going on, and a few drywall repairs did not seem like much of a problem. The error became apparent when one of the indoor coils failed, requiring replacement. Because of the lineset location, the connection to the unit was in the wall instead of inside the head, which necessitated opening up the drywall to make the repair. At this point, I figured out the issue and, after reviewing progress photos, I realized that the installer would have been able to put the linesets in the correct location, had he been aware of the need to do that.
I now have a second leaking coil (2 out of 3 so far, but that is another story) on another head that will also require the removal of drywall to make the repair. The plan is to extend the lineset to the proper location so any future servicing can avoid wall repairs. Any future repairs on the other heads will include the same changes.
It is clear to me now that had I carefully read the unit installation instructions and paid more attention to the original installation, I may have identified the problem. The question is though, is it the job of the contractor to double-check every trade contractor to make sure their work is done correctly? I don’t know that it should be, but the fact that it isn’t leads to frequent problems on construction projects. In my company’s work certifying single and multifamily buildings, we often end up being the primary quality control. We inspect and advise on corrections, many of which could have and should have been identified by the project management team or the installers themselves.
In the case of my house, I could have taken the time to investigate this particular issue. I had not run into it previously, so it did not occur to me that the installer did not have the necessary knowledge or experience, nor did I have the inclination to read the product instructions. I expect that people with more experience would have learned this lesson, as I now have. For me, the bigger lesson is that managers must understand trade contractors’ work as thoroughly as possible, and take the time to inspect it at each stage to make sure it is done properly.
_________________________________________________________________________
-Carl Seville is a green builder, educator, and consultant on sustainability to the residential construction industry. After a 25-year career in the remodeling industry, he and a partner founded SK Collaborative.
Weekly Newsletter
Get building science and energy efficiency advice, plus special offers, in your inbox.
2 Comments
Great article.
As noted in the article, installer lack of knowledge or lack of experience are two possibilities. A third, and in my experience more common, is installers (and often GC's) lack of concern for long term implications of installation decisions. For them, the best solution is the path of least resistance, and that usually equates what is most convenient at install. It can be influenced by factors as mundane as materials on the floor on one side of the unit during installation, so it was easier for the installer to set a ladder on the other side, and that is how something ended up installed where it is.
Until residential either contractually or code wise can cause coordination and attention to such detail to be the path of least resistance, it won't change. Commercial and larger multifamily residential projects have started to see some traction in this area, as evidenced by Carl's note that his firm often has the opportunity to contribute QA/QC comments. I hope most of them get acted upon. Commercial and larger multifamily have distinct advantages in this area over residential - they have the budget and perhaps even code mandate to hire firms such as Carl's, they have owners educated in how building construction impacts operations who can require these issues get addressed as a condition of payment, they have more detailed contract documents (plans & specs), contract agreements to contractually/legally require this type of coordination, economies of scale that make some of the coordination more affordable (a precon meeting to review 9 install conditions for 250 minisplits is far more affordable than the same meeting to review 3 install conditions for 3 minisplits) the quantity of projects is fewer and profitable enough to cause subs to compete for the work both in cost and in performance, and the inspectors are more knowledgeable.
Until the residential market as a whole has a willingness to not only fund, but enforce performance and quality across the industry, and the supply of residential subs grows to meet demand, there will always be another project a sub can go to with less hassle and thus higher profit margin and they will abandon projects that enforce QA/QC to the level it should be enforced or charge incongruous premiums, just to do the job properly. It's sad to say but the most effective path to improvement in the residential industry seems to be code mandates.
Glad you liked the article. One other issue that I figured out long after the project was complete was that the installers ran the first floor refrigerant line along an exterior wall, drilling through about 20 feet of studs to get to the condenser. I realized later that they could have run it up into the ceiling, through a joist cavity, and down and exterior wall, drilling out only the top plate. They created a lot of extra work for themselves by doing this. Your point about the economics of preconstruction coordination are well taken. Single family residential construction is chronically underfunded, rarely allowing for the time and effort to properly think through processes.
Log in or create an account to post a comment.
Sign up Log in