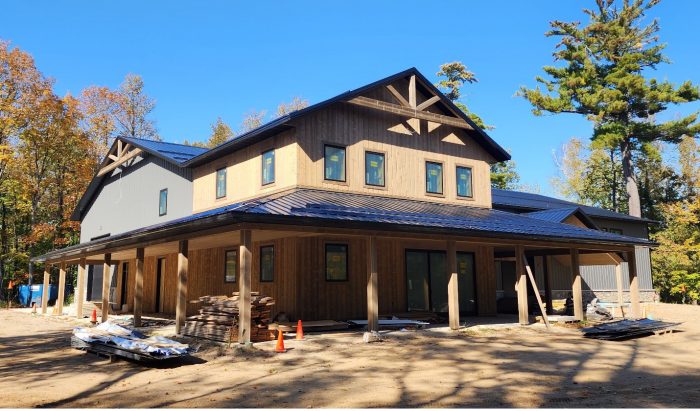
Work on the “barndominium” project is nearly complete after 18 months of construction. (You can read about the full scope of the project by following the links at the bottom of this post.) In this final update, I will discuss the mechanical systems and blower-door test results, along with the challenges and benefits of this type of building method.
Heat loss calculation
Because this project was constructed in a heating-dominated climate (climate zone 7), it was critical to get the heating system design right. We started by calculating heat loss. The heat pump manufacturer performed the calculation using Wrightsoft HVAC design and sizing software. They knew the design, construction type, and insulation levels, as well as the projected airtightness. Their simplified method for calculating air infiltration uses a poor, good, or best range of airtightness instead of using actual air infiltration rates.
Our goal for airtightness of the entire building was 1 ACH50. I don’t believe the manufacturer thought that level could be achieved with post-and-frame construction, which resulted in a much higher air infiltration estimate on the heat loss calculation. (More on the actual blower door–test results later.)
The heating load for the 3480 sq. ft. of living quarters was calculated at 46,767 Btuh at the heating design temperature of -17°F. As you can see by the heating and cooling calculation depicted in Design Conditions chart 1, infiltration rates are projected to be nearly 44% of the heating load with walls and window heat loss accounting for the majority of the remaining losses.
I don’t have the inputs used to calculate the load, but I believe they are oversized by around 10,000 Btuh. Cooling loads for this project are minimal, but part of the system includes a forced-air, ground-source heat pump that is supplying the upper level with heat as well as the…
Weekly Newsletter
Get building science and energy efficiency advice, plus special offers, in your inbox.
This article is only available to GBA Prime Members
Sign up for a free trial and get instant access to this article as well as GBA’s complete library of premium articles and construction details.
Start Free TrialAlready a member? Log in
6 Comments
Randy,
This is really great workmanship on this build, credit to the craftspeople involved. I worked with a plumber, (Al) in Minneapolis some years ago and his work could have been featured in any plumbing how to book. Never saw anything like it before or since in terms of straight, plumb and clean solder joints. Keep up the good work. Those who really care in the building business are very few and far between, a lot of over confidence out there.
Doug
Thanks Doug! My brother's work, he pushed for a larger mechanical room but didn't get it. It took him a lot of time to fit the heat pumps and their associated equipment in the space. In the end, it turned out very clean.
Randy,
I appreciate how diplomatically you have approached your work there. It's clear you had some misgivings about certain aspects of the build, but managed to do a great job with the cards you were dealt.
This is an amazing build....kudos!
If we are worried about sustainability then inbedded carbon is key. I like the idea of eliminating a masonry foundation. I also like the idea of eliminating sheathing if possible, although I see that this proved to raise issues.
For me, I would like to see a post frame construction home with a raised first floor and no slab, no spray foam. This would dramatically reduce the imbedded carbon of the build. As someone who has lived at the Jersey Shore for decades with homes built on wood pilings and an elevated first floor, I know it is doable
I thoroughly enjoyed reading about your project and appreciate all the detail. The lighting load appears to be much higher than I would expect. Considering that a 100 Watt incandescent equivalent LED light bulb requires 14 Watts of power, 6 kW of power equates to over 400 LED lights. I'm guessing that other loads were included or that 6 kW is circuit capacity, not load.
There is high wattage LED lighting that was installed for the shop, storage area, the area with the 18-foot-high ceilings. I believe they were close to 200 watts each and there were almost 2 dozen of them. The owner has the controls set so that only 1/3 of them come on during in the normal setting. If he needs all of them on, he makes an override of the lighting scheme. The 6 kWh was with all lights on, because they are all controlled through the lighting control panel, he has the ability to turn all lights on at once with a single switch on an app.
Log in or become a member to post a comment.
Sign up Log in