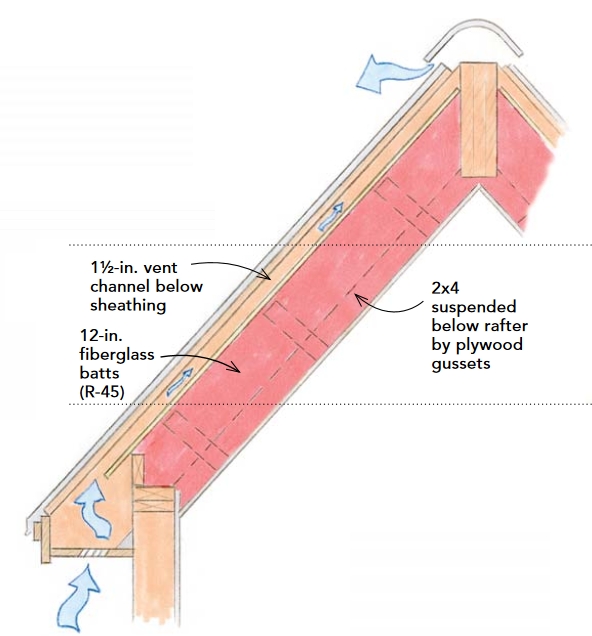
When I began working at the Journal of Light Construction in 1999, I was assigned to edit the magazine’s Q&A column. At all of my various jobs since then, I’ve been called on to help answer questions submitted by residential designers and builders.
Over the last twenty years, I’ve been asked the same three questions again and again:
- How do I insulate a cathedral ceiling?
- How do I insulate the interior side of a basement wall?
- Why is my HVAC contractor specifying oversized equipment?
No matter how many times my colleagues and I try to wrestle with these issues, the questions persist. I feel a little like Phil Connors in the movie Groundhog Day. If I was effective at my job, you might think that these questions might taper off in frequency — but they don’t. These stubborn questions return again and again, and experts’ efforts to answer them are ineffective.
So why are these questions so thorny? As I began to ponder these issues, I wondered:
- How can energy experts do a better job of answering these questions? Should our advice change?
- Can we envision code changes (or changes in manufacturers’ advice) that might help builders understand these issues?
After mulling these issues, I realized that I don’t have any simple answers. But it’s worth untangling a few threads to figure out what’s going on.
We need to raise the bar
These problems elicit a variety of reactions from builders, including some shoulder shrugs. But these aren’t trivial problems. Imperfect knowledge can result in expensive mistakes — and these are not victimless mistakes. Every month of the year, GBA hears from homeowners facing $20,000 and $30,000 repairs for avoidable problems.
The residential construction industry inexplicably accepts a high rate of defects — defects that…
Weekly Newsletter
Get building science and energy efficiency advice, plus special offers, in your inbox.
This article is only available to GBA Prime Members
Sign up for a free trial and get instant access to this article as well as GBA’s complete library of premium articles and construction details.
Start Free TrialAlready a member? Log in
30 Comments
A bit cranky this morning, are we? Perhaps cabin fever has set in already because of the new snow? The word "curmudgeon" springs to mind. I think we can all imagine Martin out shoveling his deck, muttering about missing vent baffles and crimped flex ducting.
The article is right on point, of course. You have hit the proverbial nail right on the top of its shiny little head.
But how do we provide advanced education to the building trades, when even basic education isn't required to enter the business? I agree that licensing might be one solution, if it comes with a meaningful education component. One could argue that plumbers and electricians generally do a competent job because apprenticeship and continuing education are generally a part of their licensing requirements. I have always believed that trade schools are the answer, but that's not at all sexy. When I started in my current gig, I worked with a German mason. He had a Master's degree in masonry from a German technical college. Imagine that! An actual college-level master's degree in masonry. This guy didn't just do beautiful work - he knew how and why. He knew what kind of mortar to use, and when, and how to mix it, and how long to mix it, and how the weather affected curing, and....everything. He knew about reinforcement and where to place it. He could design reinforced concrete structures on the fly better than most civil engineers. He was a Master by any definition. Why can't America, with all of its vaunted knowledge and its "highly skilled workforce" figure out a way to provide even the most basic education for its trades?
Peter,
You raise a good question, it is all about money. We have decided over the years that building homes does not require skill or experience and boy does the lack of both show. Everyone is looking for a deal, new home or remodel. The dutiful builder offering a quality product can't begin to compete in price with the hit and run contractor. I am finding here in the Twin Cities a return to the demand for quality in some cases, folks have been burned looking for bargains and are now seeking quality workmanship.
YES! We need trade schools to develop knowledge-based skills and craftsmen. We need our educational system to stop demeaning students who want an alternative to a liberal arts degree. Competent builders and trades people are in such short supply and are a barrier to building the types of structures this publication promotes. It would also be an asset to have architectural schools require some building experience of their students so there is deeper and pragmatic understanding between architects and builders.
Excellent article Martin. I've been lurking here for about a year as we are preparing to build a home in 2020. Each of these three issues have been our primary head-scratchers between myself and our builder. We've had the following experiences with these:
Cathedral Ceiling Insulation - We're still trying to identify the best method for my simple cathedral ceiling. It's just a simple roof with no valleys, dormers, etc. and we're still puzzling over what is the "right" combination of performance and budget for zone 4.
Basement Insulation - Oak Ridge National Lab created a foundation handbook that includes detailed drawings that I have shared with my builder. This has been a real problem solver as he has a definitive guide to follow.
HVAC sizing - My builder recommended paying for a Manual J calculation from a third party, then using his normal, preferred installer. The service is very cheap and I have no way of knowing the value of this service.
To make matters even worse, regarding the code related solutions, many areas like here in rural Tennessee do not have building codes. The majority of Tennessee, outside of cities and large towns, have an "opt-out" scenario for building codes. This creates a situation where there is no regulatory framework to promote good building practices and builders have no incentive to learn or implement new methods, materials, etc. Eliminating loopholes like this would go a long way toward large scale impacts in residential construction.
Thanks again, I've learned a tremendous amount from GBA posts and articles like this.
Cory. We used raised heel scissor trusses for our cathedral ceiling. Insulating was simple, as cellulose was blown In from the gable ends. Prior to insulating, an air barrier membrane was stapled to the underside of the bottom truss chords. Then strapping, then drywall. The cellulose was then blown on top of the membrane. The roof was vented.
Great piece. I'd add BuildingGreen to your list of sources we should support (and, of course, I subscribe to it and the others on your list).
Dan,
You're right. It's done. Thanks.
"I feel a little like Phil Connors in the movie Groundhog Day"
At least you are fighting the good fight.
@ Peter Engle. I was kind of thinking Martin is turning into the Andy Rooney of the building world. I always enjoyed watching old cantankerous Andy complain and complain. His points were usually valid however mundane his diatribe of the week would be.
I thought this was a great article. I bought my first house in NH over a year ago. My wife and I bought it cause we liked the cathedral ceilings. At the time I was building science illiterate (I’m an MD by profession). We had a dreaded winter last year with severe water damage by ice dams. With drywall coming down soaking wet we realized after reading GBA our roof lacked 1) air tightness 2) adequate installation of fiberglass 3) adequate venting. 4) minimal application of water ice guard
For months I tried hunting down a contractor willing to do the foam over-roofing at an adequate thickness. Most contractors thought it was insane or unreasonable. Any contractor that commented my ice dams were from gutters I immediately discredited.
After spending the entire spring and early summer trying to find a contractor I lost hope. With that I bought a tool belt and went at it on my own with the help of my uncle (a retired post and beam contractor).
We only got half the roof done for winter but I’ve already seen a difference. The finished half develop no icicles with our recent snow and the batt insulation isn’t even in yet. As for the other side it’s already started to form ice dams. I know I’ll be up on the roof again this year breaking off large chunks of ice again
To be honest, I agree with the article that there is misinformation out there. But I think people build the way they do out of laziness. It’s not easy to build houses how GBA recommends. It takes more effort to do. I believe that is why builders fall prey to false manufacturer advertising.
I’m sad to say this happens in all professions and We all fall prey to it. The reality is we have to follow the science!
Erik,
Thanks for sharing your story. The various elements of your tale are classic -- and unfortunately, I've heard the story many times.
My guess is that when you were in medical school, you never dreamed that you'd have to do your own roofing, because our economy fails to produce enough skilled roofers to meet the nation's needs.
Good one, Martin, thank you. I agree with "the residential construction industry is failing to consistently build good houses. We need a paradigm shift.", and your suggestions for addressing the issues. But I think items #2 and 3 deserve further investigation to get to that paradigm shift. Education is expensive and time-consuming for builders, but code advancements alone are making it necessary. I'd like to see a return-on-investment study for states providing free training in exchange for licensing; ideally the cost of education will be offset by savings to homeowners and to builders' insurance... I'm not that familiar with how they do it in Germany, as you reference, but think we need a program ASAP. If we're going to tackle energy reduction, we need the majority of builders on board.
Tom,
While it's possible that lowered repair costs for homeowners might exceed the cost of builder training, your proposal would leave states responsible for the cost of the builder training. Since the theoretical savings would go into homeowners' pockets (and perhaps builders' pockets, if their insurance costs dropped) rather than into state coffers, I see political hurdles in the path of your proposal. It would be necessary to raise state taxes to pay for your proposal, and that is never an easy political sell.
I have a cathedral ceiling that includes an octagonal section and thus hip roofs. I do not see that I will have a ventilation problem. I'm planning on creating ventilation baffles by using some sort of sheet goods (plywood, OSB) on top of the rafters and then placing 1-3/4 to 2 inch spacers on top of the rafters to which the actual roof sheathing is attached. When I look at the cost of any ventilation baffles running all the way from eave to ridge, this seems as good an approach as any. I also think there are multiple advantages to this approach. For one, since the ventilation spacers are mainly spacers and not providing structural support for the roof, then the spacers can be laid out in a pattern that allows air to flow from the hip roofed portions up to the ridge. Also since the ventilation baffle is created essentially a single plane, it could become an air barrier by taping the joints. Or maybe I'm missing something while contemplating this approach???
Dennis, I think there are a couple things to consider with that approach: first, check with a structural engineer if you use a non-structural sheathing as your lower sheet; if you separate the structural sheathing from the rafters by a few inches, you'll have to be careful about fastening to be sure you're transferring lateral forces. Second, careful of the permeability of the lower sheet: if it's not very vapor-permeable, it could be too slow to vent. Another approach we used was to put 1.5" blocking at the top of the rafters (or use the lip of a TJI, in our case) and attach 1" thick rigid EPS insulation (perm rating of 5) to the underside, then insulate up to that from below. That way you can have your structural sheathing attached to the rafters. OK, put that out there, let's see if Martin schools me on this one...
Tom, good response, you raise exactly the same issues that have concerned me. I haven't built this structure yet, but will in the next couple of weeks, so I certainly want to know if I'm off track. As it turns out, it seems that the most cost-effective material might be some decent 1/2" plywood or OSB, in which case it would supply the same structural bracing as roof sheathing fastened directly to rafters. I wouldn't suggest using something thinner. I would also think that if the spacers are fastened with the same nailing schedule as a double top plate, then this should be an adequate substructure for the actual roof sheathing.
I have also wondered about the permeability of this sheet. However if the ceiling below includes air and vapor barriers, then the ceiling shouldn't have a moisture issue, right? So if the permeability is low, limiting vapor entry, then I would think it is also adequate to let that vapor leave. I'm still thinking.about this.
The main appealing feature in my approach is being able to vent hip roofs above a cathedral ceiling -- which I need to do for our half octagon sunroom. Having sheathing nailed to rafters makes venting the hip roofs nearly impossible. But adding a vent channel seems to make it easier and thus worth considering. But again, I'm open to correction, and the sooner the better.
Dennis,
Your proposed method of venting is discussed in my article, "How to Build an Insulated Cathedral Ceiling." (Scroll down and look for the bold heading, "Creating vent channels above the roof sheathing," and read the paragraphs that follow the heading.)
In addition to potential structural problems (the potential problems mentioned by Tom), you have to worry about the permeance of the OSB or plywood. Both materials are vapor retarders. Potentially, the roof sheathing is increasing in moisture content from below, but the ventilation is happening on the wrong side -- it's happening on the dry side of the sheathing rather than the damp side of the sheathing. Whether or not the rate of drying is adequate to handle the moisture accumulation becomes a complicated equation, since the permeance of the sheathing is a factor in its ability to dry. In other words, you've added a new risk factor.
Installing an adequately thick layer of rigid foam on the exterior side of the roof sheathing is a safer way to proceed.
So another reason why questions get asked over and over is because sometimes answers seem inconsistent. Martin, maybe we are misunderstanding each other, because it seems like the article "How to Build an Insulated Cathedral Ceiling" pretty much "blesses" the venting arrangement I have described. Perhaps a sketch would help explain my confusion. What is the difference between solutions described in the article (under the heading "Site-built ventilation baffles") and what I describe? Both are airtight assemblies and also have airtight ceilings below and seem virtually identical to me except that one includes the vent channel between the rafters while the other provides the same channel in a layer above the rafters. But why would they not perform the same? And thanks for all your replies to these articles and repetitive questions.
I do have another question and that is "what moisture are we trying to control by venting the roof?" When I did a reroof on my house a couple years ago I actually read the shingle manufacturer's literature and they said it was important that the underside of the sheathing gets air. It seemed they were saying that moisture may, or will, get past the shingles so that the sheathing might need to dry from below. And then there's also any moisture coming from the interior of the house. But if we are airtight and retard vapor flow, that shouldn't be a problem, right? And that any significant moisture from the house would mostly be through bulk leakage and not through diffusion. Am I understanding that correctly? Thanks again.
Dennis,
Briefly, the purpose of the vent channel is to remove moisture that tends to accumulate on the underside of the OSB or plywood roof sheathing. The source of the moisture is almost always interior air -- exfiltrating humid air. A secondary source of moisture is wintertime diffusion from the interior to the exterior.
You are absolutely correct that good building practices (airtight methods and the use of a vapor retarder) limit worrisome moisture flows. That said, experience shows that no builder is perfect. The vent channel is a type of insurance that covers inevitable job site mistakes.
You are wondering why it's permissible to use plywood and OSB -- materials that aren't particularly vapor-permeable -- as ventilation baffles. I address that question in one of my articles, "Site-Built Ventilation Baffles for Roofs." In that article, I wrote:
"Do baffles need to be vapor-permeable?
"One of the reasons that builders install ventilation channels is to help damp roof sheathing dry out. Researchers now realize that ventilation channels can help a little bit at this task, but not as much as some people think. (In fact, during the summer, ventilation channels can actually add moisture to roof sheathing rather than remove it; for an example of this phenomenon, see Image #4, below.)
"The most important way to prevent the migration of moisture from the interior of a house to the roof sheathing is have a good air barrier at the ceiling. The reason is simple: the usual transport method for this moisture is air leakage, not vapor diffusion. Because of this fact, installing ventilation baffles that are airtight makes this type of roof assembly more, not less, robust.
"What if interior moisture is able to reach the underside of a ventilation baffle — isn’t it possible that the moisture might condense against the baffle (especially if the baffle is cold)? If so, isn’t this a good argument in favor of using vapor-permeable materials (for example, fiberboard, cardboard, or thin EPS) for ventilation baffles?
"The answers to both questions is a qualified yes. Anyone worried about this possibility should probably make their ventilation baffles out of a vapor-permeable material.
"That said, there really aren’t any reports of failures or problems resulting from the use of vapor-impermeable materials — for example, polypropylene, vinyl, or foil-faced polyiso — to make ventilation baffles. The main reasons:
∙ Not much moisture manages to make its way to the ventilation baffles (especially in homes that pay attention to airtightness);
∙ The air in the ventilation channels is often warmer than outdoor air, a fact which limits condensation; and
∙ Any moisture that does make its way there seems to be incorporated into the rafters via sorption. The ventilation channels are able to remove a limited amount of moisture from the rafters, and it appears that the rate of drying exceeds the rate of wetting."
So then it seems my proposed system is OK after all. Airtight ceiling, airtight ventilation baffle system. My ideal material for the baffle would be something more permeable than plywood or OSB, but these materials are OK if the airtight construction is done (and maintained) properly. Both ceiling and baffle are vapor retarders so there will be some drying capability in both directions. But the main thing is to keep the moisture out in the first place with airtight techniques.
Dennis,
In the case of the ventilation baffle, high moisture tends to raise the moisture content of the rafters -- and the rafters have contact with the ventilation channel. In that way, the rafters act as moisture buffers, redistributing excess moisture until the moisture is removed by ventilation drying.
In the case of vent channels installed on the exterior side of the roof sheathing, the system lacks the beneficial moisture-buffering capacity of the rafters. You end up with a system whose success or failure depends on a comparison of two rates: the rate of wetting and the rate of drying. (The rate of drying is slowed by the OSB or plywood, neither of which is particularly vapor-permeable.) If the rate of drying equals or exceeds the rate of wetting, the system is safe. If the rate of wetting exceeds the rate of drying, failure is still possible.
I suspect that one reason why some questions get asked over and over year after year is because there are multiple answers based on whether you live in Florida, the southwest desert, a hot humid marine climate, the damp winter northwest, or the cold New England states. So even if there are clear solutions for those places, there are still questions for people who live in between. We can even understand the concepts but not know if our climate is humid enough to deserve the Florida treatment or cold enough to merit the New England approach. So we're unsure and continue to ask the same questions...
Dennis,
You're right that climate often plays a factor in determining specifications for cathedral ceilings or basement insulation. That said, some methods are robust in all climates. For example, installing an adequately thick layer of rigid foam on the exterior side of roof sheathing works in all climates (although the minimum thickness of the rigid foam is climate-dependent), and installing rigid foam on the interior side of a basement wall works in all climates.
You can't make the same statement about fiberglass batts. So if we're worried about how climate affects our advice, we can advise builders to use robust rather than risky insulation approaches. If we follow this path, our advice becomes more universal.
Appreciate your comments Martin. Yes, some approaches to problems can be universal. I'm just saying that some of the reason for the same questions being asked is maybe because if someone like me wants to fully understand how things work, we need to learn how those universal solutions actually work in all climates and what factors need to be considered in different climates if you do not want one of the universal solutions, like fiberglass, as you said.
This is why we side-stepped using a general contractor. However, our experience with subs has been very good. For example, our roofer understood why we wanted polyiso on our exterior roof sheathing and our concrete contractor loved our waterproofing and insulation system for the basement. We had to do the leg work to find the right products. Demystifying building homes and empowering owner-builders is part of this website does well. Lisa
Lisa,
Thanks for sharing your experience. I'm glad you did your homework (by reading GBA) and am glad that you found competent subcontractors. Your experience, unfortunately, isn't typical. Other owner/builders who have chosen to act as their own GC haven't had as positive an experience.
The bottom line is that subcontractors' skills vary widely. In some regions of the country, it's easier to find skilled subcontractors than in other regions. As I said, I'm glad that your project has been such a success.
as always a great article and deep wisdom behind. We are all thankful for your wisdom here Martin.
A suggestion: For building contractors who work with these roof designs and variations a lot this article and the referenced articles for cathedral design are excellent-- as far as the text goes.
Next is an edited version from my original post. . .
However, it would be great if you put together a cross-section design, in detail, of your ultimate, closed-cell air tight cathedral structure giving all the specs in the drawing. That is, similar to the image at the start of this article, but with even more detail / specs and for the AIR TIGHT concept. The idea being to use the concept you allude to in this article as most effective. I assume, therefore, that you are eschewing the natural air convection under the roof concept for closing everything up tight and also assume, wrongly(?) that the best way to attain a real seal is to use foam, closed cell . . .
Brian,
I'm not sure what "my ultimate" cathedral ceiling would look like, but unlike you, I probably wouldn't use closed-cell spray foam.
GBA provides many details for cathedral roof assemblies insulated with closed-cell spray foam (even though I rarely recommend this approach). Most of these are in the GBA detail library, which is available to GBA subscribers. The first two images below are from the GBA detail library -- a taste of what is available there.
I am also sharing an illustration (the colored illustration) from one of my articles, "How to Build an Insulated Cathedral Ceiling."
Thanks for the drawings. I edited my original post pointing out mostly that you appeared in this article to lean away from the natural air convective concept towards the AIR TIGHT concept. . .
By the way, I am not necessarily saying foam is the "ultimate" way to go. It seems as a means to seal tightly nothing else approaches it. My own bonus room attic above my garage has me thinking on this . . . Present concept in my mind is to foam an inch or so directly on the underside of the roof sheathing and embed a 3" thick Styrofoam board (1/4" clearance to rafter faces) against into it, attach a 2nd 3" board using Great Stuff or a simple fastener of sorts, etc. then, foam the 1/4" gap. This would produce a 1" closed cell foam + 3" Foam board + 3" foam board inside my 2x8 rafter. Then sheet rock with high permeable white primer. So, if concerned about being "green". . . yeah, this likely would not pass muster on this website but it seems it would go a long way towards your goal of keeping things tight while mitigating a bit the use of spray foam in huge thickness! Just an idea.
Hello,
My new home was built with an unvented cathedral ceiling, just finished 3 months ago. I live in Climate Zone 5. The insulation R value of the roof is R38, however, the insulation contractor only used 1.5" of closed cell spray foam with R30 fiberglass batts between the closed cell spray and the drywall of the ceiling, instead of the values that I am reading in your article "How to Build an Insulated Cathedral Ceiling." There are no recessed lights in the ceiling but there are surface mounted fixtures and hanging pendants that in a few places have not been detailed well and there is a small sliver of rough drywall exposed, would that lead to an air leak?
Now I am extremely concerned (read: freaking out and can't sleep at night) that I am going to have problems with my roof sheathing rot or mold in the ceiling. The roof is a metal shingled roof over regular WRB and ice and water barrier. There does seem to be some air gap between the metal roof and the WRB/sheathing because of the profile of the shingle, which are formed to resemble a wood shingle, but not as much as if it were installed over furring strips. The roof has a simple geometry, with no hips or valleys or dormers, just some flashing around the chimney.
Is there anything that can be recommended I do in this situation, is the only remedy taking down the drywall or the roof?
Log in or become a member to post a comment.
Sign up Log in