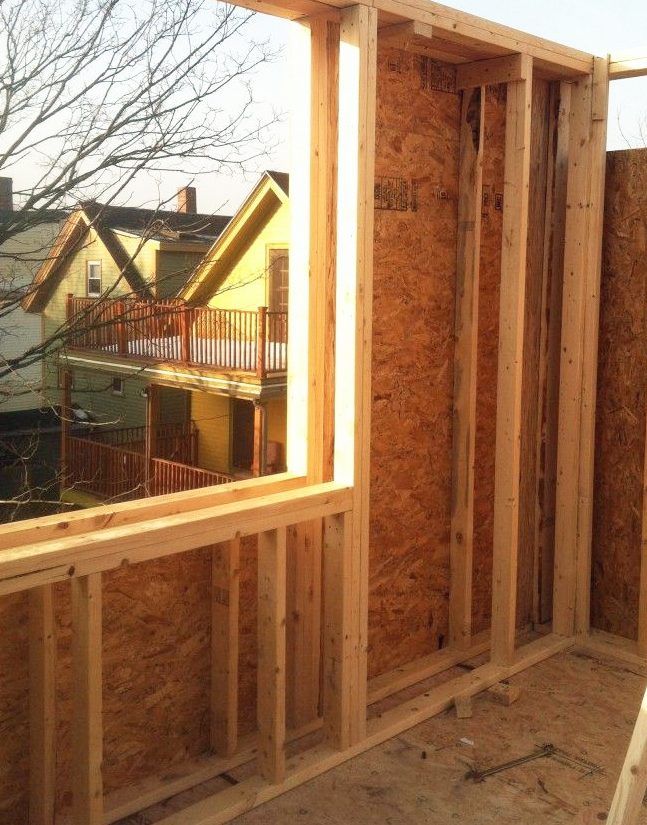
Fully aware that I am engaging in gross oversimplification, I’m going to offer a cartoon version of the History of Vapor Barriers. (I’m not a cartoonist, though, so someone else will have to make the drawings.) Here goes:
Panel 1: In the late 1940s, residential building codes in the U.S. began requiring the installation of vapor barriers on the interior side of walls and ceilings. These requirements had complicated historical origins but were not based on credible building science.
Panel 2: During the 1960s, fiberglass batts were sold with kraft facing on one side. Builders were instructed that the kraft paper should face the interior of the building.
Panel 3: During the 1970s, when U.S. homeowners were hit with steep increases in energy prices, builders began paying more attention to insulation levels. Energy experts began advising builders that polyethylene sheeting was a better vapor barrier than kraft facing. By the late 1970s, most builders in the colder areas of the U.S. — and a significant number of builders in mixed climates and hot climates — were installing interior polyethylene vapor barriers.
Panel 4: During the 1980s and 1990s, building scientists in the U.S. and Canada realized that interior polyethylene prevents walls from drying inward during the summer, and that polyethylene was causing as many problems as it was preventing. As these scientists began studying the mechanisms by which moisture is transported from the interior of a house into walls and ceilings, they realized that the most important moisture transport mechanism was air leakage, not vapor diffusion. These scientists proclaimed, “Vapor diffusion is not the issue! We need to focus on air barriers, not vapor barriers. Code requirements for vapor barriers are misguided.” Led by Joseph Lstiburek, some of these scientists managed to implement code changes that allowed builders to omit…
Weekly Newsletter
Get building science and energy efficiency advice, plus special offers, in your inbox.
This article is only available to GBA Prime Members
Sign up for a free trial and get instant access to this article as well as GBA’s complete library of premium articles and construction details.
Start Free TrialAlready a member? Log in
31 Comments
The Takeaway
Well I'm ready to apply this to real life. I'm convinced that a 12" vapor open double stud wall assembly will be OK even with one layer of sheathing.
From inside to outside:
1. Painted sheetrock
2. 2x4 studs
3. Dense Packed cellulose insulation
4. 2x4 studs
5. 1/2 real plywood sheathing
6. Vapor-open air and weather barrier (https://grace.com/construction/en-ca/Documents/AVB-204A-PAB%20VPO.pdf)
7. 1/4" min. furring strips
8. Exterior cladding
Caveats:
1. The house must be verified tight and ventilated to the 2015 IECC code .
2. The homeowner must be warned not to humidify above 40% RH
Ice Box of the Nation
Zone 7 Northrn MN, 40 below F a few times every winter, 2-20 days every summer 90+F with high humidity. Sort of planning on going with sheet rocked 6" walls with fiberglass batts, osb, 4" rigid foam, airscreen, lap siding. Sounds like I should consider plywood instead of osb?
Reply to Kevin
I am also considering this type of wall. I like the intermediary sheathing idea, but am a little concerned about no sheathing on the outside, just vapor open air barrier and air screen strips?
Response to Kevin Dickson
Kevin,
If I remember correctly, you are in Climate Zone 5. Bill Rose certainly agrees with your stack-up. Joe Lstiburek would like to see intermediary sheathing as a vapor retarder, but not all experts agree with the need for that layer. Joe doesn't mind plywood sheathing in your climate zone, but in colder zones he wants to see fiberboard or gypsum sheathing.
As a former builder, I am always wary of any building envelope details that depend on homeowners to maintain certain interior RH levels to avoid rot and failure. I wouldn't build any wall in that category as a builder -- too risky. I want a wall that can survive homeowner mistakes -- a very robust wall.
I'm not saying your wall isn't robust -- just that I wouldn't want the integrity of my wall system to depend on whether a bath fan is operating correctly. When the bath fan conks out, I don't want the wall to fail.
Response to Steve Vigoren (Comment #2)
Steve,
Design tips for the type of wall you are planning to build (a 2x6 wall with 4 inches of exterior rigid foam) are found here: Calculating the Minimum Thickness of Rigid Foam Sheathing.
The "cold OSB" worries apply to double-stud walls and other walls without exterior insulation. If you have 4 inches of rigid foam on the exterior side of your OSB, your OSB will be warm, cozy, and dry all winter long. So it won't be getting damp in February. There is no evidence whatsoever that you need to worry about the integrity of the OSB in that type of wall.
That said, plywood is a better quality sheathing than OSB. Some builders who take the long view have decided, "I just don't want any OSB in my building."
Response to Steve Vigoren (Comment #3)
Steve,
In Comment #3, you address Kevin Dickson, writing that you are "also considering this type of wall" -- presumably Kevin's double-stud wall -- and that you are "a little concerned about no sheathing on the outside."
But Kevin's proposed wall has plywood sheathing on the exterior.
Exterior Sheathing
Martin - Thank you for a nice review of this complex issue. All referenced people mention plywood, or fiberboard / gypsum in a cold weather situation for exterior sheathing. What about wood boards? In Maine, wood sheathing remains a viable choice. Yeah, it takes longer, but it diffuses well, can be relatively inexpensive, and it does have a long history of success. Why is this traditional material rarely mentioned?
air leakage
The one thing I'm still confused about is the impact of air leakage. Air leakage is evil because it can introduce moisture to sheathing, but as Mr. Rose pointed out, airflow can also help with drying. Clearly, this is nearly impossible to measure or model (if diffusion is difficult to model, I can ony imagine that moisture deposited by convection is unbelievably complicated). But unlike with diffusion I don't have a good grasp of the general principles that would inform when airflow would increase or decrease the moisture load inside a wall...
Response to Kevin Zorski
Kevin,
I'm pretty sure that all of my articles on the topic mention that board sheathing is a good option. This article didn't, because Joe Lstiburek and Bill Rose didn't mention boards.
The main reason that boards aren't used more widely for sheathing is that sawmill boards don't have a grade stamp, and are therefore not approved by most building inspectors. Moreover, most construction workers aren't familiar with the use of boards for sheathing unless they live in a rural area and have relatives who work in a sawmill or who own a bandsaw mill. In most of the country, everything is about plywood or OSB.
I used rough boards from a local sawmill as wall sheathing and roof sheathing on my own house, and have built several other homes with board sheathing. Installed on the diagonal, boards make for a very strong (and of course, vapor-permeable) frame.
Response to Peter Rogers
Peter,
The reason we control air flow through building assemblies has very little to do with whether air flow through the assembly helps dry the assembly or adds moisture to the assembly. The reason that we control air flow through building assemblies is to save energy.
I think most building scientists would agree that uninsulated walls with a great deal of air leakage are the type of walls that are least likely to have moisture problems. Of course, you need a huge honking furnace to heat these old uninsulated houses, and hundreds of gallons of fuel oil.
We need to build our walls, ceilings, and floors to be as airtight as possible to lower our energy bills. Once we do that, we need to develop techniques to keep our materials dry and safe. In the old days, we could rely on the drying effect of air movement through those walls. We can't do that anymore.
Kevin Zorski: I don't know
Kevin Zorski: I don't know what the experts here will tell you, but as someone who lives in a 15 year old house with board sheathing, I'd argue against it. Primarily because of wind washing. There's housewrap on the exterior, but when the wind blows it goes straight through the gaps between those boards. I had to remove a section of drywall recently this winter to repair a leak, and it was shocking how much air blew through the sheathing. I'll also add that it allows ants and other crawlies more access points. to get into the wall.
Response to Peter Rogers
Peter,
Of course every house needs at least one air barrier, and board sheathing isn't an air barrier. A house with board sheathing can use exterior rigid foam as an air barrier -- that's what my house has -- or the airtight drywall approach, or both.
Response to Martin
Thanks for the response, nice to know my osb will be ok. My comment to Kevin was confusing. I thought intermediary sheathing is on the outside of the inside of a double wall, and therefore would be warm. I guess I knew Kevin's sheathing was on the outside. I am interested in that type wall, but like the idea of sheathing on the inside where it will be easier to keep warm
Airflow through the assembly isn't to control moisture?
Martin,
Yes, I'm definitely planning on installing some exterior insulation over those boards, as soon as economically possible!
I think I had misinterpreted Bill Rose's comment to mean that airflow in insulated buildings could help dry them out in certain conditions. Based on your response, I'll assume he was only referring to uninsulated buildings.
So, of course we control airflow primarily to save energy. But airflow also causes all kinds of problems such as moisture accumulation, so it is really correct to say that avoiding moisture issues in assemblies is not a reason that we air seal buildings? I think it's both reasons, not primarily one or the other. (I'm finding this discussion confusing because most of these lessons I thought I had learned from articles on GBA including many of yours!)
I think your response pertains mainly to new construction? With older houses, if we look at the energy savings payback, air sealing is not always all that cheap or easy by comparison with insulating; air leakage can be extremely difficult to access, and therefore time consuming and costly to address. Either that, or it can be made up of thousands of tiny points of air leakage, and people don't want to pay for a tradesperson to spend hours upon hours doing a careful job with a caulking gun. From an energy standpoint, with an old leaky home, it makes way more sense in many cases to ignore the difficult job of reducing air changes (which is also a job with no guarantee of great success, overall) and simply blow some fluffy stuff into the walls and ceilings. But if you do that without paying attention to air sealing, then you can cause huge moisture issues down the road, correct? I come up against this problem every day, and therefore I like to point out to clients that simply insulating without air sealing can cause problems with moisture accumulation, and that it's not all just about the energy savings. Are you saying I'm wrong to give this advice??
Response to Peter Rogers
Peter,
Air movement through wall assemblies can add moisture to the lumber and sheathing, or it can reduce the moisture content of the lumber or sheathing. It usually does both, on alternating days, depending on the weather, the RH of the interior air, the RH of the exterior air, and the rate of air flow through the leak in question.
As building scientists say, "As long as the rate of drying exceeds the rate of wetting, your assembly should usually be OK."
There are some worst-case scenarios for air leakage: when outdoor temperatures are very cold (increasing the stack effect and making exterior sheathing very cold), and when indoor RH is high, air flow through a small hole can easily lead to the build-up of a layer of frost. This often happens in leaky cathedral ceilings. When the outdoor air temperature warms up, and the frost melts, it rains indoors.
So yes -- air leakage can cause problems. But air leakage can also dry out lumber and sheathing, especially when the moving air is dry.
OK, thanks, so I'm not
OK, thanks, so I'm not totally off base. That more or less confirms what I thought I knew on the subject.
Climate still matters
Kevin Dickson's double studwall stackup might make it in zone 5, but it's marginal (ergo the 40% absolute max humidity prescriptive). In zone 4 and lower it should be fine.
But a layer of MemBrain between the studs and interior gypsum would make that stackup quite robust even in colder climate zones, and they wouldn't have to watch the interior relative humidity like a hawk. It's not particularly expensive stuff (on the order of 2x as expensive 6-mil polyethylene) and is more responsive than Intello, promoting faster drying. It has comparable vapor retardency to Intello at 30% interior RH and is still WAY more vapor retardent than standard latex paint at 40-50% RH, but becomes more vapor open than latex paint at 70%+ RH. Think of it as cheap insurance. I have no commercial interest in Certainteed,(the manufacturer of MemBrain), but trust third party test data from tested monitored assemblies- it works.
Wood sheathing
Here on Vancouver Island we form our foundations out of 1"x8"s and then use the stripped boards to sheath as much of the house as we can. That's all well and good, but when you need to rely on the sheathing for shear, the boards have to be applied on the diagonal, and that makes the labour involved considerably higher.
In double wall construction, with an intermediate layer of sheathing, I wonder if it makes sense to apply skip sheathing - say 1"x4" at 16" o.c. - on the exterior. This might make flashings, openings and installing the WRB easier without significant additional labour and material costs.
Response to Dana
Please direct me to the reports that have convinced you that MemBrain reduces vapor diffusion.
The data I have reviewed so far only convinces me that the reduced vapor transmission was due to the reduced air leakage. (A well installed "vapor retarder layer" makes a given wall assembly much tighter). In those tests, air leakage was neither measured nor controlled for. Note, a blower door test doesn't measure the air leakage during the long term test of the sheathing moisture content, only the relative tightness of the assembly.
Also, if the data convinces me that MemBrain is effective against diffusion, it will also convince me that the "condensation pumping" effect is negligible. (MemBrain can't reduce condensation pumping because it produces huge local pressure differences that would force air and vapor around the MemBrain and through the staple holes).
my wall solution
New construction zone 6: 1/2" drywall on 2x6 studs w 5 1/2" rockwool insulation, 3/4" closed cell foam as a thermal break, 5/8" OSB, 30 lb felt, 1/4" Homeslicker rainscreen and finished w 1/2" painted cedar beveled siding. My thought is the stud cavity will dry to the inside and the OSB will dry to the outside.
Anyone see a problem w this?
Response to George LaLonde
George,
Your approach is called "flash and batt." Two comments:
1. Although you refer to your 3/4 inch layer of closed-cell spray foam as a "thermal break," it won't stop thermal bridging through the studs if the spray foam is installed on the interior side of your OSB sheathing.
2. In Climate Zone 6, building codes require those who are following the "flash-and-batt" method between 2x6 wall framing to install a spray foam layer with a minimum R-value of R-11.25. Your suggested layer of 3/4 in. of foam is too thin to meet this requirement. For more information on flash-and-batt requirements, see Calculating the Minimum Thickness of Rigid Foam Sheathing.
To paint or not to paint
I am in the process of building my personal home and read on How to Build an Insulated Cathedral Ceiling (GBA) that it is critical to install an air barrier under tongue and groove on a cathedral ceiling (i.e. drywall) when using "fluffy" insulation and I have done so. I have the code required R-15 rigid foam (for north Georgia) above my roof decking and insulated the rafter bays with roxul mineral wool insulation. I was wondering if I should paint it with vapor-retarder paint as an extra safety feature? My concern is, as Martin pointed out, diffusion works both ways and during the summer via my ac and during other seasons via my ultra air dehumidifier, my ceiling and walls will have the opportunity to dry if necessary. My primary concern arises because the house was framed in 2012 and I have been working on it as I have the money; I did not take out a loan as I don't want to risk ever losing my house to foreclosure and I presume there is a decent amount of moisture via air leaks inside of my ceiling already, which has the sheetrock installed but not yet been taped and mudded. I have the same question regarding my walls which have 1.5" of rigid foam (polyiso) on the exterior and 2x6 walls with roxul mineral wool batts. I could purchase a dehumidifier or portable ac in an attempt to get as much moisture out of the assembly as possible and then paint using a vapor retarder paint but I am not sure how effective that would be. Any thoughts?
Thanks,
Matt
Response to Matthew Seabolt
Matthew,
The reason that you installed R-15 of rigid foam above your roof sheathing was to keep your roof sheathing warm and dry during the winter. In your climate zone, R-15 is enough insulation to keep the roof sheathing above the dew point. If your roof sheathing is warm, you won't get any condensation or moisture accumulation in the sheathing. That problem is solved -- so stop worrying about moisture migration from the interior to the cold sheathing. You don't have any cold sheathing.
The type of roof assembly you have chosen is designed to dry to the interior, so you don't need vapor-retarder paint. It could even be argued that vapor-retarder paint is counterproductive, since it slows the rate of inward drying. For this type of assembly, inward drying is desirable. So don't install vapor-retarder paint.
That said, you always want a good air barrier on the interior side of your roof assembly. It looks like you have that. So relax.
By the way, the same advice I just gave you concerning your ceiling also applies to your walls.
response to 19.# Kevin Dickson,
Kevin Writes:
"Please direct me to the reports that have convinced you that MemBrain reduces vapor diffusion.
The data I have reviewed so far only convinces me that the reduced vapor transmission was due to the reduced air leakage."
Sure:
http://www.energy.wsu.edu/documents/AHT_ComparingTheMoisturePerformance%20Of%20Wood%20Framed%20Wall%20Systems.pdf
You might want to argue that the walls with the kraft facers or paint only were just leakier than those with poly or MemBrain, but these were EXTREMELY simple and small test (4' x 9') assemblies with ONE SHEET of wallboard to air seal, with no penetrations for electricity/plumbing etc. It's doubtful that a broad sheet of poly or MemBrain makes a single monolithic sheet of wallboard appreciably more air tight than just the wallboard itself.
Comparing the moisture content of the wood in similar assemblies with both vented & unvented siding to that of the MemBrain or poly vapor retarder units is useful, and is convincing enough for me.
Air leakage would not explain the difference between Wall 7 (latex only vapor retarder, unvented siding) and Wall 5 (kraft facers + low permeance oil paint vapor retarder), unless they magically made wall 5 a heluva lot more air tight than wall 7, and it's doubtul that the higher vapor permeance of plywood vs. OSB made the difference there.
The MemBrain walls (Wall 2 and Wall 8, both with unvented stucco siding) fared pretty well, despite the fact that the interior RH was maintained at an unusually high 50-55% RH @ 69F, which is a humidity level at which MemBrain isn't at it's most vapor-tight.
Look at the moisture content graphs for those walls. MCc 3 is the sheathing moisture sensor, which stayed well below 20% for all wood in both MemBrain walls. Wall 8 also had R5 EPS on the exterior, and nothing broke 15% moisture content. The peak moisture content of the sheathing on Wall 2 (unvented stucco siding) was about 17% for less than a week in February, and dropped below 15% by March. Wall 1 had a polyethylene vapor barrier, and it too peaked briefly in February, at about 15%.
Wall 5 had kraft + oil paint, unvented stucco, peaking at 20%, but over 15% for months.
Wall 7 had latex only, unfaced batt, unvented stucco, and the sheathing stayed over 30% from the beginning of December to half-past March.
But I'm sure it was just the air leaks... yeah thatzit. :-)
But seriously, ascribing those differences to air leakage in this instance would be a fairly severe insult to the building scientists running the test. MAYBE they're so incompetent that they don't understand the importance of air leakage, but it's a stretch to assume that. Their self-assessment (on page 6) is:
"There are limits to the conclusions that can be drawn from one year of testing. The test walls were
subjected to specific interior and exterior environmental loads. The test walls could have responded
differently to a different set of loads. Several examples to these limitations have already been noted.
Exterior moisture penetration is unlikely, and the transfer of moisture from the interior through air
leakage is unlikely. "
But sure, maybe it was air leaks, but they claim to have built it fairly tightly. The do not mention blower door testing to verify tightness prior to testing, but I'll accept their self-assessment in lieu of evidence to the contrary. YMMV.
Another MemBrain (Smart Retarder) Study
For reference, here's another study on CertainTeed Membrain (polyamide-6 variable permeability vapor retarder), also from a Pacific Northwest climate, which is from monitoring we did 2003-2006.
Field Monitoring of Wall Vapor Control Strategies in the Pacific Northwest
http://aceee.org/files/proceedings/2008/data/papers/1_8.pdf
Figure 6 summarizes it well--shows the sheathing MCs on the wetter wall. In wintertime, from wettest to driest: latex paint, Kraft paper/Smart Vapor Retarder facer (toss-up), SVR sheet, and polyethylene. Basically, the order in which the materials would resist vapor diffusion. Remember, this is the Pacific NW, so we often have interior RHs in the 40%+ range (risky, even with mild winters).
Later on, in disassembling the walls, we figured out that the reason why the SVR facer (i.e., facer attached to the batt) was wetter than SVR sheet: it was the installation method. We were asked to install the faced batt products inset stapled (yes, it filled me with pain). An inset stapled facer creates a great chimney on the interior, and voila--a perfect setup for convective looping to bypass your vapor retarder. Check out the MC map in Figure 8--the bit of damp sheathing right at the top of the stud bay, where the convective loop would hit. Sorry about the poor quality of that PDF--a better version is attached here.
Attachment
Okay, trying to attach that attachment again, which doesn't seem to be showing up.
Response to Kohta Ueno
Kohta,
Thanks very much for the link to your study.
Here are the key paragraphs from the "Conclusions" section:
"Two Class II vapor retarders (Kraft-faced batt and PA-6 [MemBrain]) provided acceptable performance, if the vapor control layer is not bypassed by convective airflow. Both of these materials allow drying of incidental moisture to the interior, if interior conditions are at a lower dewpoint than the assembly cavity.
"A Class I vapor retarder (polyethylene) provided acceptable performance as well in these walls. Although an increase in sill plate wood moisture content was seen in the summer due to an inward vapor gradient, it was well within the safe range. However, the use of a completely impermeable vapor control layer such as polyethylene eliminates drying to the interior; moisture sources could include inward vapor drives from saturated reservoir claddings, and the drying of incidental water leakage."
Forgive me if I’ve missed it but there doesn’t seem to be much talk of vapour-open seam tape for sheathing. E.g. Siga Wigluv. I used OSB on a wall assembly; which necessitates a 1/8” gap between sheets. These are all tapes with Wigluv and primer which allows for outward vapour diffusion. The interior has no vapour barrier, but the wall cavities are filled with sheeps wool which performs very well in humidity - and dries itself out (if it’s not trapped by a barrier). Rigid open cell foam on the outside; and a humidistat HRV control. Climate zone 6.
I opened up the assembly after 3 years for an addition and it’s all dry as a bone.
Would love to hear thoughts…?
andy_c,
Unlike air-barriers, vapour-retarders act as percentage of the area covered. Because the seam tape occupies such a small area, whether it is vapour-open or impermeable doesn't make much difference. There is no mechanism by which moisture in the wall cavities can find that more vapour-open 1/8" gap and flow through it, rather than diffusing through the rest of the wall.
While I get the principle you’ve described, isn’t the jury out on the effectiveness of this. Europeans assign reasonable importance to having a vapour open seam; for keeping wall dry. It’s briefly discussed here: https://www.finehomebuilding.com/membership/pdf/8169/021234046.pdf
While it’s hard to know why the assembly I tested has worked so well (lots of factors at play) I can’t help but think those vapour seams are helping at certain times of year. If only a small amount of vapour needs to escape then these seams should allow it to.
andy_c,
The 1/8" gap between the sheets represents somewhere around 0.1% of the area of the wall. Vapour doesn't know where the impermeable or permeable areas are. It attempts to diffuse through everywhere, but encounters differing resistance. The argument that small gaps can aid drying was behind the early '90s practice of drilling holes in exterior sheathing. When I suggested it here, both Martin and John Straub disabused me of it's effectiveness using the argument I've set out.
Your own assembly also includes continuous open cell foam (which like OSB is around 2 perms), so any drying through the gap and permeable tape is limited by that. The walls work because the exterior foam keeps any moisture in the walls from condensing on the sheathing, so there is no need for any drying to the outside.
Log in or become a member to post a comment.
Sign up Log in