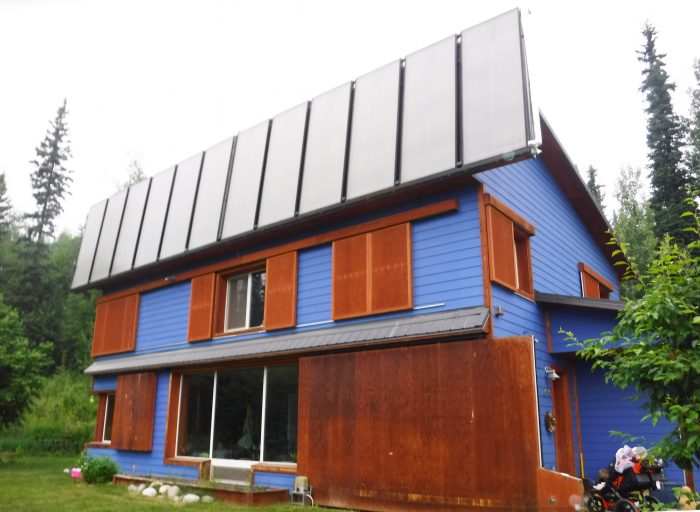
Longtime readers of Green Building Advisor will remember reading about a Passivhaus residence in Fairbanks, Alaska, called the Sunrise House. Designed and built by a contractor named Thorsten Chlupp, the superinsulated house generated widespread interest from journalists and energy-efficiency experts. The home has an elaborate hydronic heating system that includes a dozen solar thermal collectors connected to a 5,000-gallon insulated water tank. The backup heating system consists of a wood-fired masonry heater with stainless-steel heat-exchange tubing that transfers heat from the wood fire to the large water tank.
In 2011, GBA published a news story on the Sunrise house. That same year, Chlupp posted several comments in response to a Q&A thread about his house.
And a few years later, in 2015, GBA published a report on a presentation given by Chlupp at an energy-efficiency conference in Vermont.
A serendipitous meeting
During the summer of 2019, when my wife and I were visiting friends in Fairbanks, we accompanied our host one evening when he delivered some construction equipment to a job site in the Fairbanks suburbs. Looking out the vehicle window, I realized that we were driving past Thorsten Chlupp’s distinctive house, which I recognized from the photos published in GBA. “Let’s stop and see if Thorsten is home,” I said.
When I knocked, a stranger came to the door. “Is Thorsten home?” I asked. No, the stranger answered. Then he introduced himelf: “I’m Andrew McDonnell. I bought the house from Thorsten.”
After exchanging a few pleasantries, Andrew graciously agreed to be interviewed about the performance of his home. I told him I’d give him a call when I got back to my office in Vermont.
Busy with other articles, I neglected to call Andrew for several months. Recently, however, we had a long telephone conversation about…
Weekly Newsletter
Get building science and energy efficiency advice, plus special offers, in your inbox.
This article is only available to GBA Prime Members
Sign up for a free trial and get instant access to this article as well as GBA’s complete library of premium articles and construction details.
Start Free TrialAlready a member? Log in
7 Comments
A fascinating follow-up. Thanks very much for this article.
Kudos and thanks to Chlupp and the following home owner for sharing the experience of their extreme home in an extreme climate.
Considering the tremendous insulation (R80 walls - R120 roof -12 tons of cellulose!) the use of the 3 cords of wood/season (70 to 75 million BTU) seems rather high for a 2300 sq ft house, even with Fairbanks 14,000 heating degree days. Then it occurred to me that there is a wood masonry heater that’s likely leading to high ACH, bringing in a large amount of cold air. It also seems like it would make the indoor air very dry on the coldest days.
With under 5 hours of daylight in the depth of Winter, no matter the U-value and South facing orientation, the large windows (and ineffective shutters) must also lead to some serious net loss. Although I can appreciate how they would contribute to the resident’s happiness.
I am a little surprised at the original builder’s attempt to build seasonal thermal storage with a 5000-gallon tank. I once looked into long term thermal storage for the North East in a climate that’s less than half as cold (6000 HDD). While assessing that plan, I found out that a gallon of water can only store about 500 BTU for practical hydronic-heating use. Given that a typical energy efficient home anywhere North of Kansas will still require 5 to 10 million BTU in January for space heating alone -and not much solar replenishing- I quickly got over that idea. But I am still grateful that someone with a lot of determination was willing to give it a try and and give us an honest report of how it turned out!
To clarify "solar thermal systems" ... the article is referring to collectors which store solar heat in a circulating fluid, which is pumped to a tank, storing the fluid warmed by solar energy. In the old days, we called this "active solar", since it requires pumps and energy to operate. It also involves circulating fluids, which can be problematic. Leaks, maintenance of pipes, or in this case custom storage tank liners. And generally all of this equipment serves only a single purpose: Collecting and storing solar energy.
Passive solar refers to systems in which glazing allows solar energy to enter the home, strike surfaces inside the home, which transforms the light energy into heat energy. This heat energy is inside the home's thermal envelope. Some high thermal mass materials (concrete, stone, brick, or more problematic water) can absorb heat energy when the interior space becomes warmer than the thermal mass. So the thermal mass soaks up heat when the interior gets too warm (e.g., sunny afternoons), and radiates heat back when the interior temperature is cooler than the thermal mass (e.g., overnight or early morning before sunlight can contribute to heating). When designed well (quantitative modeling required), the elements to provide a passive solar system may cost very little, since a home has windows to collect solar energy, and could have polished concrete slab floors, or tiled/stone/brick floors or walls on the main floor, etc. to store thermal energy and reduce interior temperature fluctuations. So the costs to provide the PASSIVE solar heating could be negligible or low. That's not true about the active solar collector systems, especially after considering all the maintenance headaches of active, fluid-based systems.
For an example of a well-engineered passive solar home in a sunny cold winter climate, see:
https://www.greenbuildingadvisor.com/green-homes/a-passive-solar-home-from-the-1980s
Of course Alaska is an extreme example, with bitter cold winter temperatures and very little solar energy shining on a building during mid-winter, when you need heating. I'm guessing that's why Chlupp wanted to do the impossible: Attempt to use the meager solar energy available in Alaska to heat a home located in the extreme cold winter temps of Fairbanks. Certainly not a good climate for year-long solar space heating or hot water heating. His system did work effectively in the Fall and Spring, though not cost-effectively (active solar costs) and couldn't store enough heat for months to handle the extreme winters. For more detailed information on solar energy for space heating and US climates, see:
https://www.greenbuildingadvisor.com/article/a-quantitative-look-at-solar-heat-gain
Very thorough review. Feel a bit sorry for the new owner - I bet there's been more than a few moments of buyer's remorse trying to nurse all the Rube Goldberg systems along. And to learn it's now a rental? Yikes. I'd bite the bullet, rip it all out and install a low-cost conventional system and not dread calls from my renters.
Several improvements could be made to make the solar thermal contribute a lot more to heating and quite reliable.
1. 5,o00 gallons of storage is WAY WAY WAY too much! The rule used to be 2 gallons of storage per 1 SF of collector; but in this case it is 5,000 gal to 480 sf or >10:1 (UGH)). The problem I found is that a system with so much storage is essentially non-responsive to input of several hours of winter sun. That is, tank temp may rise from say 84F to 89F with 4 hours of winter sun. That is not use-able heat. I have removed large storage tanks on many homes and reduced the the storage volume dramatically to 1:1 or less. I have had great success using as little as 100 gallons on eight 4x10s (100gal to :320 SF). This way we get usable heat that can be transferred when it is generated!!
2. Overheating. Use STEAMBACK passive overheat protection on glycol systems (Drainback is also used on "open-loop" systems). This eliminates overheating. Period. I have dozens of systems that work flawlessly on steamback including the one on my own home. Relatively simple retrofit on existing systems.
3. Sensors. Yes they can fail occassionally. $20 each for part. Now I install one spare sensor on each rooftop array on new systems, so the repair can be made in a few minutes without going on roof. A sensor typically last 5 to 20+ years.
I would be happy to answer questions: Todd at [email protected].
FYI I often advocate solar electric or heat pumps over solar thermal, but solar thermal (properly installed) has it's place, and can be modified if it was poorly designed.
Martin, I had no idea this follow up existed, and I'm very happy you published it here as I have reviewed all of Thorsen's videos etc on his builds and it all looked very promising. The thermal stratification work he did with regard to vertical tank mixing was very interesting.
After building a solar pool heating system (with automation and data monitoring) I actually pondered how the Sunrise House was faring, I watched daily how much the water temperature dropped overnight, and then how much energy was being used daily to recover and heat it with a 100K BTU solar system on the roof. ...during hot summer days. I also graphed daily the BTU performance of the system and noted the relatively short daily period of system "max" performance, and how that even changed during the summer with solar azimuth. Yes, I am using un-glazed collectors (320 square feet) in a cooler climate, but that's what you need for raw BTU output (along with very low temp delta and high flow) for this application.
It occurred to me that in order to heat a home with BTUs stored in water, you'd need a much, much larger reservoir to cover those "dark" days of winter they see in Alaska. Furthermore, putting it inside the house would be a massive challenge for all the reasons the new owner cited. All this using water, which is considered a pretty effective way to store heat...and much easier to accomplish vs ground storage.
I also had the opportunity to design and build a full commercial retrofit to create a very efficient building (9000 sq/ft) here on the 49th parallel. The mechanical budget on that project was over $250K and included insulating an existing 4800 sq/ft slab and installing radiant over top.
I would echo a lot of recent comments/blogs from Martin Holiday and Joe Lstiburek's (top 10) interview, here with regard to envelope, radiant heat and simplicity. We used a furred air space assembly (adding 2" EPS on the inside of 2x6 walls) and found this wall system pretty amazing as all electrical plumbing penetrations were in the "warm" envelope. This building passed all fire code commercial requirements, but also was very easy for untrained trades folks to do electrical, HVAC and plumbing without messing with the envelope. Heating costs for this fully occupied commercial building were less than our small home, with average monthly temps at -20C in February.
All the money spent on the radiant portion of the heating system was questionable. We needed 5 air handlers, AC, and two commercial HRVs (on top of radiant) to cool and supply fresh air. I also had 9 ecobee stats with about 20 remote sensors and quickly realised that the radiant system, although very nice for staff on the main floor, was not the key to effective cold climate temp setbacks..the air handlers were more than enough and had to run daily anyway for fresh air delivery. Insulate the slab, yes. Add radiant...no.
The building used automation and the existing Ecobee sensor network to manage night pre-cooling of the building, and temp setbacks for unoccupied spaces which was well worth the effort, although the automated clerestory windows etc. were all connected to an automation hub. This requires management to make sure batteries in the remote sensors were changed every 18 months, firmware updates etc. so was not trivial to maintain.
Back to this blog entry. I'd 1000% echo the comments on spending your cash on envelope and windows. Working with an efficient envelope means you can dial back a lot of other ongoing expenses. KISS, KISS and KISS is consistently what works..and that takes even more design thought than adding sensors all over the place and adding automation (which I enjoy doing, sadly).
Thanks again for taking the time to write this follow up. Thorsen's efforts were amazing, and the follow up completes the learning curve so we can learn from his work.
Dennis,
Thanks for sharing your experiences and perspective on this.
Log in or become a member to post a comment.
Sign up Log in