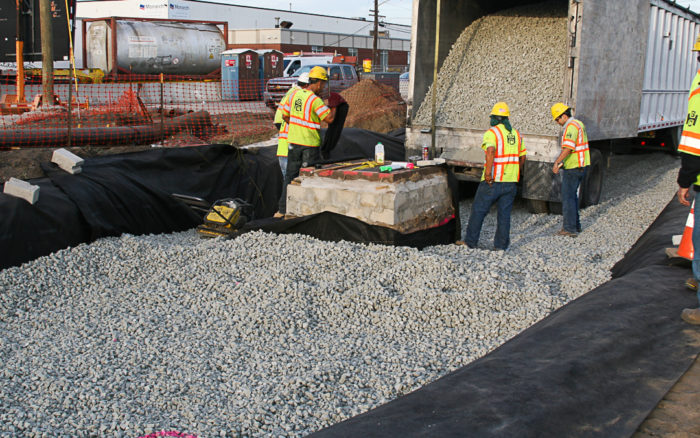
Two companies in the Northeast are seeking to expand the market for a lightweight, insulating fill made from recycled glass that can take the place of stone aggregate in several residential applications, including subslab fill.
AeroAggregates of Eddystone, Pennsylvania, announced this week it has opened a second kiln as it increases production of the foamed glass aggregate it now sells in parts of the Northeast. The material is made of post-consumer recycled glass and a foaming agent and, according to the manufacturer, can act as both a drainage and insulating layer.
In Vermont, Burlington-based Glavel is currently importing foamed glass from a German manufacturer but plans to open a 12,000-square-foot plant in St. Albans, Vermont, next year as it sees increased demand ahead.
In a telephone call, AeroAggregates CEO Archie Filshill said that he and a colleague were introduced to the technology in Norway six or seven years ago. After a round of testing in 2016, AeroAggregates began producing foamed glass in 2017 and now distributes it in an area from Massachusetts south to Virginia Beach and west to Pittsburgh.
One of its chief uses is as a replacement for the Styrofoam used for soil reinforcement, stabilization and backfill in infrastructure work — highway, rail and bridge projects. Interest among state transportation officials grew when they realized the material, unlike polystyrene, wasn’t flammable and wouldn’t melt when exposed to gas or diesel fuel, Filshill said.
Later, Filshill saw potential value in the use of foamed glass as backfill on construction sites. Because it’s lighter than stone, it’s easier and less expensive to transport, and it can be used as a replacement for the rigid foam and crushed stone that’s now used under concrete slabs by many builders.
“It’s acting as a drainage layer, a capillary break, and as an insulating later,” he said.
Among its biggest customers are New York City contractors who specialize in green roof systems, Filshill said. Foamed glass is 80% to 90% lighter than stone aggregate — between 10 lb. and 20 lb. a cubic foot — and can be placed on a 1:12 roof slope without any reinforcement.
In residential construction, Filshill said, builders who are now using rigid polystyrene insulation and crushed stone under slabs could switch to foamed glass for about the same cost.
“This gets placed like gravel so you replace your gravel layer with this and that would also act as your insulation layer. So you’re getting a two for one replacement. It’s easily put in, and there’s no waste.”
Filshill said the insulating value of 12 inches of foamed glass ranges from R-11.5 to R-15.7. Costs run between $70 and $80 per cubic yard.
“There is also a slight savings on installation,” he added, “because the material just gets dropped and plate-tamped, which you’re going to have to do with your stone base anyway.”
Filshill said foamed glass also could be used as backfill around foundation walls, and as a free-draining fill behind retaining walls and under patios.
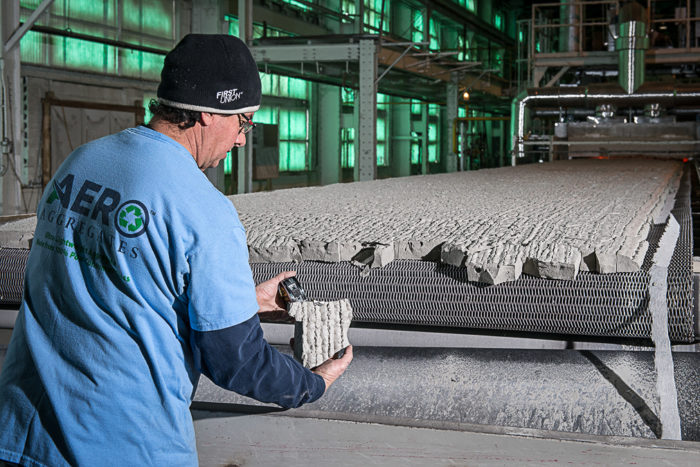
Foamed glass is manufactured in a gas-fired kiln under license from its European developer. Powdered glass is mixed with a foaming agent and when heated to 1,800°F the soft glass becomes infused with bubbles. Although the kiln is gas-fired, Filshill said, foamed glass has half the carbon footprint of polystyrene and expanded shale, another lightweight aggregate option.
Welcomed by advocates of foam-free construction
Glavel’s website lists many of the same benefits as AeroAggregates, including high compressive strength, light weight, low thermal conductivity, and cost effectiveness.
Company CEO Rob Conboy said Glavel grew out of a Passive House conference he attended in Germany in 2016. He was scouting for European technology that could be used to lower the cost of energy-efficient construction in the U.S.
Foam glass is used extensively there, he said, but is not widely known in North America. But interest has been strong among builders who are looking for foam-free products.
“We’ve got some fairly good sized roof projects as well as some folks who are foam-free practitioners looking to use the product,” he said. “We’ve had multiple conversations in multiple channels about how do they look to standardize foam glass gravel in their construction specifications.”
Glavel sells for between $85 and $100 per cubic yard on the east coast (orders have gone as far as Seattle). When you calculate the installed cost of XPS or EPS with labor and gravel, Conboy said, “we are very cost-competitive and in some cases we might be cheaper.”
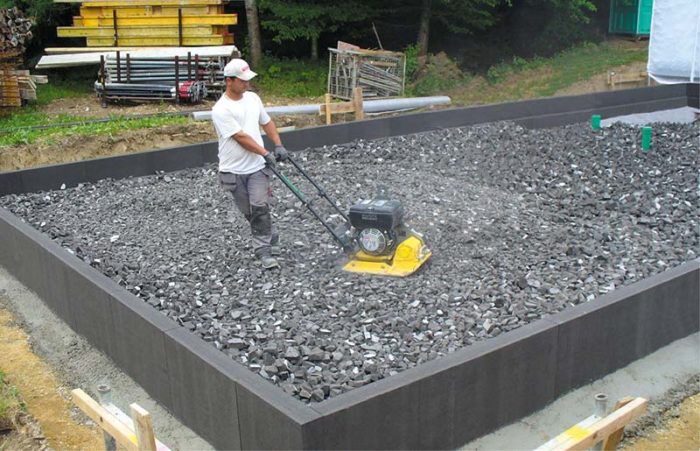
Compaction is key to performance. The material offers thermal performance of R-1.7 per inch, but only after it has been compacted by about one-third. So, Conboy said, a subslab layer performing at R-10 (equal to 2 inches of XPS) would require between 9 and 10 inches of loose glass foam that would be mechanically compact on site.
Glavel’s two production lines will use some 15,000 to 17,000 tons of recycled glass to produce 140,000 cubic yards of foam glass per year.
“We think there’s a bright future for foam glass gravel,” he said. “We love the fact that we’re going to be taking something of little or no value and turning it into a product that’s good for the planet and an amazing alternative to a petroleum-based product that’s laden with lots of chemicals, and do some good.”
Talking with potential retail partners
Both AeroAggregates and Glavel are of interest to 475 High Performance Building Supply, a New York-based retailer specializing in foam-free building products.
“We’re very bullish on it in the long term,” said Chief Operating Officer Ken Levenson. “We think it’s a win-win-win once you’ve got the supply chain and the manufacturing together. You’re taking recycled glass and upcycling it into an insulation product for buildings. It’s one of the few products that has this magical, virtuous cycle — how we can build and not just minimize our impact but have a positive impact.”
Foam glass is especially interesting because it serves two purposes — drainage and insulation — and that ultimately simplifies the construction process, he said.
“The big issue obviously is cost, and that’s really about having demand at scale and production that’s local,” Levenson said. “It’s not like you can just build a factory in Indiana and ship it all over the country and compete.”
The company has been talking with both AeroAggregates and Glavel and trying to help them introduce foam glass to more potential customers. But for now, 475 isn’t listing the product on its website.
“It’s a product we want to support and see how we can help it grow,” Levenson said.
Weekly Newsletter
Get building science and energy efficiency advice, plus special offers, in your inbox.
33 Comments
I hope this works out and becomes widespread. The glass we recycle here gets landfilled anyway because there is no demand.
I'm not sure I'd be comfortable working with a substrate I had to compact by 1/3rd to get adequate insulating value and good bearing. That's a huge amount.
Good point. Plus I don't want to be the guy operating the vibrating compactor for hours and hours to get it to 1/3 compaction.
Could this be used as free draining, residential house backfill? It seems that would be an easy to way to place exterior insulation on the basement walls. Even if its performance was degraded without 1/3 compaction (ie. say R-1 instead of R-1.7 due to subpar compaction), that's still significantly better than soil. It would also be useful for insulating sewer mains lacking frost cover.
The biggest obstacle, as they point out, is that it is a manufactured product. All the fill and aggregate that goes into one of my builds comes from pits within ten miles - and even then the trucking is a large part of the expense. Getting this stuff from where it's made to where it's needed is a problem.
You could imagine a scenario in which there are small plants scattered as widely as gravel pits and recycling centers are now, leading to similar distance trucking with lower fuel consumption. And to the extent that this replaces foam as well as gravel, the distance the foam is trucked is typically pretty long. So in that sense, the obstacle is getting the usage up to the point that it becomes common enough to approach that scenario.
I'm curious to know what they're using as a foaming agent for this glass. Anybody know the nature or chemical classification of those agents?
“[Deleted]”
I don't know about these particular materials, but I found an article that generally describes the options in two paragraphs quoted below; in summary it's probably CO2 from burning some carbon added to the mix.
"It is generally accepted that foaming agents are of two types: neutralization and redox agents. The first group in-cludes salts (as a rule, carbonates), which in heating decompose with emission of gases (CO2). Intense gas release during their decomposition breaks the walls of individual pores, which merge and create a maze-like system of cavities in glass. Such foam glass has high water absorption and elevated soundproof parameters.
"Redox gas-forming agents are used to produce heat-insulating foam glass, i.e., a material in which sealed pores prevail. Such gas-forming agents are carbon-containing materials: coke, anthracite, soot, graphite, less frequently silicon carbide. The reason for gas emission in these materials is the reaction of oxidation of the foaming agent by gases dissolved in the glass melt. Such gases are primarily oxygen and sulfuric anhydride."
That's from Spiridonov, Y.A. & Orlova, L.A. Glass and Ceramics (2003) 60: 313. https://doi.org/10.1023/B:GLAC.0000008234.79970.2c
Also, it's a lot like foamglas, and they have a page that describes adding carbon powder added before it goes in the furnace. Foamglas does clearly state that no HFCs, CFCs, or HCFCs are used on another page.
int.foamglas.com/en-gb/products/foamglas-the-product/production-fabrication
For a while, Foamglas was available for building insulation in the US, in board form. It was rapidly becoming a favorite replacement for foam: insect-proof, low GWP, non-flammable, no toxic flame retardants added, waterproof, high compression strength ... Then Owens Corning dropped it as a building material in the US--it's now sold in other countries for building insulation and in the US for industrial use only.
This seems like the same concept, but broken into bits as it comes off the line. I can see how there are some applications where the crushed format is useful, but I would think that boards would be preferable for insulation applications, having higher R-value per inch and not needing compaction to get there. I hope that some of the makers of this stuff can tweak their lines and sell boards as well.
It seems like it has good potential to work for a FPSF (frost protected shallow foundation), either in the crushed format or the board format. But I do wonder about the long term properties in that sort of application. For example if silt gradually washes in and fills between the grains, will that reduce the R-value? The wouldn't happen under a slab, but it might for perimeter insulation.
Love to see this used under Porous Parking Lots and Porous Roadways, makes a great idea even better with recycled glass. Looks like a great product all the way around.
Folks like the guy with the plate compactor on this stuff need a mask to avoid Silicosis, which is a fibronodular lung disease caused by inhalation of dust containing crystalline silica.
Relatedly, I'm planning on using lava rock as my under slab drainage layer. Here on the west coast it's cheap and readily available from rock yards. Our lava rock is mined from Northern California from what I understand. It's R value is around 1.5. Pumice is also available here too but more expensive and potentially less compactable. One advantage of these naturally 'foamed' stones is that presumably they have a lower embodied carbon depending on shipping distances.
This seems like a cool product...fancy lava rock!
A lot of great comments and questions. There are several types of foamed glass based on various production methods.
AeroAggregrates website contains more detail and a technical library for additional information. Feel free to email technical questions to [email protected]
Looking only at R value, I calculate EPS to be 1/3 the cost.
At material face-value alone, maybe. But with this, you can remove the cost of cu. yd. for gravel sub-slab, remove the cost of purchasing and laying two layers of rigid foam board. The compaction of aggregate will be part of any install, so that labor aspect stays no matter the material.
On a current project in California, we have $3000 worth of gravel being delivered to the site and another $2500 in sub-slab foam and install. The cost for Glavel delivered to the jobsite will be $3700.
Aggregate and foam-free R7 in one shot for $3700? Yes, please.
(Wrote wrong number there first time! Fixed it!)
Mike, Aero Aggregates is currently shipping several projects to California from Philadelphia if you are interested.
I would guess foamed glass would outperform EPS foam board across the board, considering it performs two functions.. And the fact Insects wont dare tunneling in glass and it wont shrink and turn to dust long term.
Glavel says domestic manufacturing will be operational by November 2021. With reduced lead times and pricing that is reduced 25% from imported prices.
To bad foamed glass board isn't available for FPSF. I dont think silt could gradually washes in and fill up the material because Ive read it's "Closed Cell".
Aero aggregates says once delivered, foamed glass aggregate is placed in 2-foot lifts and does not require a roller for compaction. This further reduces the carbon footprint due to speed of construction and less equipment required to place and compact.
Neat stuff considering that otherwise the glass would be disposed of in our landfill.
Mike,
I'm interested to see if it gain market share too as it seems like a good product. The two areas I think may be problematic are:
- Sub-slab plumbing. How easy is it to run drains among bags of fill?
- Foam leaves you a completely level base under a slab. Something that reduces the amount of concrete necessary, makes installing rebar easier, and allows the slab to move seasonally reducing cracks.
When the Glavel aggregate was compacted - 2,500 SF of conditioned slab area took us all of four hours to dump and compact (myself and a 24 year old architect who said she didn’t think it could have been easier), it was all pretty level. It compacts easily, fills voids, our structural engineer loved it. So did we. We do have videos of the install process but can’t post them here.
I attached two photos of foamed glass being used for under slab applications. One is for the Hilton Garden Inn that was leveled and steel mesh placed above vapor barrier and the second show utilities be placed for the US Tennis Association's new broadcasters building at Flushing Meadows
475 Building Products is selling this now. Wish I would have known about this before I placed 8" of EPS below my slab.
Interesting, 475 claims a much higher r-value than the article (1.7 vs ~1.2). Still, you'd need 19" at least to get the same r-value ad you have.
Having read the article fully, they've got conflicting values. At one point it says 1.7 per inch, but elsewhere it says 11.5-15.7 for 12 inches, which is a range of 0.95-1.3.
The R-value per inch goes up as it's compacted, similar to any fluffy insulation.
I don't believe the r-value will go up by 70% when it's compacted less than 1%.
Trevor, I'm not sure where you got "less than 1%" for compaction. I'm going by this caption from the article: "When compacted to about two-thirds of its original loose depth, the insulating value of foam glass aggregate reaches about R-1.7 per inch, according to its Vermont importer. (Image credit: Glavel)" Insulation companies often exaggerate test data, so I wouldn't be surprised if R-1.7/in is on the upper end of what's possible. In the article they state a range (I'm assuming loose-filled, though they don't say) for 12" Aeroaggregate, which translates to R-1.0 to R-1.3/in.
That's not a universal thing. If you compact fluffy insulation too much, the R-per-inch starts going down again. There's an optimum density that gives you the best R-per-inch.
Charlie, while you are technically correct, the optimum density for fluffy insulation is pretty darn dense. As an example, 9 1/2" fiberglass is R-30 at its full depth, or R-3.2/in. Stuff it into a 7 1/4" cavity and it goes up to R-3.4/in. Cram it into a 5 1/2" cavity, if even physically possible, and you'll have R-3.8/in. The "cost per R" goes up along with R per inch, of course.
Yes, you have to work hard to compact fiberglass enough to round that corner. Enough that it's not a practical problem for fiberglass. ASHRAE Fundamentals has a plot showing that it is around 3 lbs/cu ft. where it turns the corner. This stuff in in the 10 to 20 lbs/cu ft range. So at face value, it might already be in the density range where more density makes for worse performance.
But still, it might get better with compaction, because the big air gaps between chunks might allow large-scale convection loops. I'm not sure whether the testing that has been done reflects the real-world effects like that and really gives an accurate prediction of performance in an application.
Reply to Charlie, #26--yes, Fig. 1 on p. 26.2 in my 2017 copy shows anywhere from 2.0 to 4.0 pcf as the turning point, depending on material type. Figure 2 shows that as fibrous insulation fibers get larger, the optimum density gets higher; I'm not sure how that relates to foamglass since both the "solid" aggregate and the voids between aggregates are insulative.
Pretty Good House 10-20-40-60 is fine for most.. 8" of EPS at R-32 is overkill IMO and it's proven the best bang for the buck is air sealing.
There are two types of foamed glass used for under slab insulation, wet process and dry process.
The dry process (Aero) is a stronger material which requires less compaction (1.2) and the wet process (Glavel) which is lighter requires more compaction (1.3). Once compacted both material should provide an R-value of 1.7 per inch.
Did you folks know Owens Corning makes foamed glass board called foamglas?
Foamglas T4+ insulates to R-3.44 per inch
https://www.owenscorning.com/en-us/insulation/foamglas
What would be great, is a article comparing Owens Corning foamglas to Rockwool comfortboard.. The only two insulating boards Id consider.
For a couple people asking, we did have to cut into our slab in order to process a change order requesting a kitchenette (and drainage) be added into a guest room. Couldn’t have been any easier.
Foam glass is very popular these days in commercial (esp flat roof) applications. It provides a really redundant water barrier under surface roof membranes s that are used on such roofs- anyone considering a modern house with a flat roof - needs to look into such commercial products (as well as Kemper products liquid membrane system . I could also see this as very useful for exterior basement wall insulation (lo compressibility, impermeable to water , hostile to bugs/rodents/termites
Log in or create an account to post a comment.
Sign up Log in