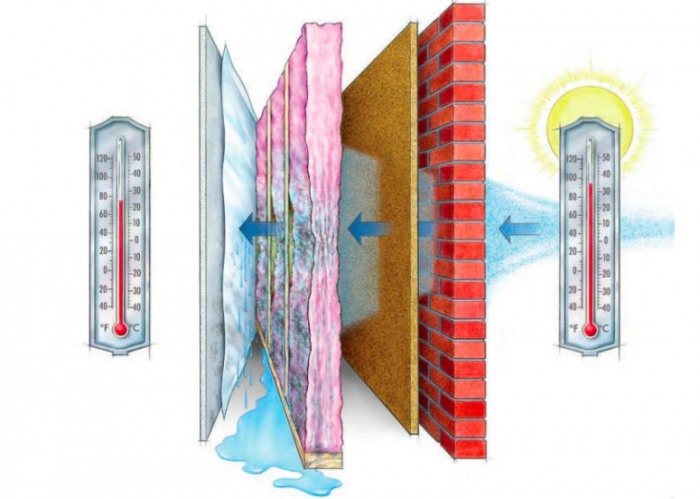
Welcome to this month’s installment of “Ben bumbles an analogy.” This is the place where I attempt to take something that people go to graduate school to understand, chop it into pieces based on half-informed Internet searches and a few well-placed phone calls, and hopefully squeeze out some kernel of shareable knowledge. So hop in, let’s take this ride . . .
Big perm
I’m feeling masochistic this month and going straight for the cliff dive. We’re talking vapor, permeance, permeability, wet cups, dry cups, rates, pressures, oh my! I’m not going to go into why water vapor is something to pay attention to—suffice to say, moisture causes problems—but we’re going to talk about how vapor does its thing. It’s a convoluted and nuanced subject that often leaves me—and, as I discovered while researching this post, many others—flummoxed.
Back to pasta
For a brief explanation of water vapor, I’ll revisit my boiling pasta analogy. Essentially, vapor is the gas form of what we use to cook pasta. The steam coming off the pot is vapor in a concentration so strong we can see it. Ultimately, it spreads out to the point that we can’t see it, but it’s still there—all around us, bouncing off and through everything. Unless we’re in the vacuum of aerospace, there’s water vapor in some quantity everywhere. We measure it with the common metric of humidity, which is a measurement of the relative vapor pressure in a given space. If we put a lid on our pot of pasta, the space under that lid is going to have a higher vapor pressure than the space outside of it—you with me?
Vapor is like a box of bouncy balls
Vapor always wants to move from more to less, it’s one of those laws of thermodynamics, I’m not going to pretend to know which one, nor will I Google it and act like I knew. It’s a fundamental action of nature. In my mind, it’s like this: Take a cardboard box, throw a handful of rubber bouncy balls in it, close it up, and start shaking it. This is what vapor is doing around us all the time. The more balls we add to the box, the higher the vapor pressure. Now, if we make a hole in this box and continue shaking it, eventually some of those balls are going to make their way out. This is permeance. The more holes, the more permeance and vice-versa—sort of.
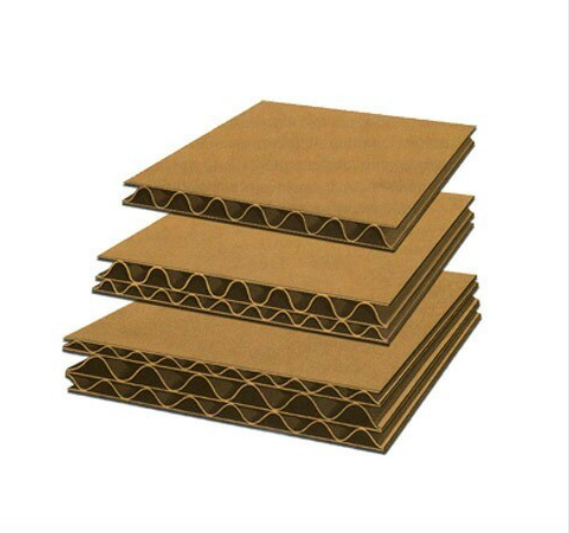
Extra-thick cardboard
So, let’s look at one side of our box (hopefully your imagination has punched a few holes through it). The number of holes in relation to the size of the piece of cardboard is the vapor permeance—think of it like DPI (dots per inch) with printers. The more holes per given area, the higher the permeance. I’m simplifying things a bit; real science would also account for the level of pressure and the length of time vapor is allowed to escape.
Back to the box . . . with the same number of holes and shaken at the same speed, but now imagine it is made of 1-in.-thick cardboard, which means fewer balls will escape. This is permeability—the relationship between permeance (number of holes) and the material’s thickness. A general rule of thumb: As the thickness doubles, the permeability is cut in half. So, a 2-in.-thick cardboard box would allow half as many balls to make it all the way out of the holes, as compared to a 1-in.-thick cardboard box. This proportion isn’t 100% accurate, but it will take someone with the letters PhD after their name to explain why. (I’m looking at you, Allison Bailes.)
Yet another test method
Now, let’s look at how we test the permeance of a material using the ASTM E96 “standard test method for water vapor transmission of materials,” which is commonly known as a wet cup/dry cup test. This method reveals some interesting characteristics about how materials behave.
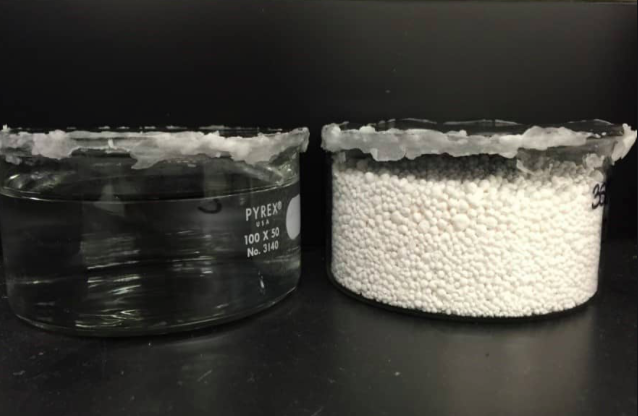
Here are the basics: Two cups or dishes are prepared; one is full of water (the wet cup), the other is full of a desiccant (the dry cup). A sample of whatever is being tested is placed across the top of each cup and sealed tightly with tape, wax, etc. The two cups are weighed and then placed in a test chamber, which is held at a constant humidity level and a constant temperature. Periodically, the two cups are taken out and weighed. What’s happening here is that we’re inducing a vapor pressure differential across the material to see how it behaves. The inside of the wet cup is near 100% relative humidity (a higher vapor pressure than the chamber), and the inside of the dry cup is near 0% (a lower vapor pressure than the chamber). Physics being physics, the wet cup will lose water vapor and the dry cup will gain water vapor. The periodic weighings monitor the rate at which that happens and that is what defines the permeance.
Material valves
So, why do we have a wet cup and a dry cup—wouldn’t either one tell us the rate that moisture moves across a material? It’s time for that ubiquitous building science response: “It depends.” Some materials have a set relationship to how vapor passes through them. Like pouring water through a piece of window screen, it doesn’t matter which side of the screen the water is poured through; it flows at a rate set by the geometry of the material. Not all materials behave like this though. A common phenomenon with some building materials is that they become more permeable when wet—proven by the higher rate of vapor transport across the wet-cup sample. This phenomenon provides handy information, as it means that an assembly will transport vapor faster the wetter it gets. Materials that move vapor rapidly are considered open. Those that move vapor slowly are considered closed. These are our classes of vapor retarders.
The weakest link in the chain
Something to bear in mind when thinking about this stuff as it relates to building assemblies is that the permeability of an assembly is only as open as the most closed component in the system. For example, take a piece of CDX plywood (about 20 perms when wet), and put a piece of Ice and Water Shield membrane on it (1 perm or less)—that assembly is now only as permeable as the lowest perm component.
Don’t do stupid stuff
By now I’ve either bored you to tears or I’ve thoroughly confused you, so let’s get down to simple takeaways.
1. Don’t put closed materials on two sides of an assembly. Vapor is going to get in whether you like it or not, and there better be a way for it to get out.
2. Avoid putting the closed layer on the cold side of an assembly. This is inviting issues with excess moisture and potential condensation. If you’re not sure which is the cold side—or it changes periodically—go with a vapor-open assembly.
3. If you think the success of your assembly depends on the vapor performance of its components, you should probably go back to the drawing board. Any system that evokes concerns over vapor at the time of construction is likely to have major issues as time goes on.
4. It’s easy to treat some of these vapor issues as hard-and-fast rules but they aren’t. There is so much at play in a building that can influence the way moisture behaves that it would be impossible to say exactly what is going to happen. (You could change the entire performance of a wall system by simply cutting down or planting trees near it.)
5. This is confusing stuff for us humans, and big companies—even the most respectable among them—are run by humans. Be skeptical of data you see published regarding vapor performance. There are enough misunderstandings around the subject that bad information slips through the cracks. If it is a serious concern, verify data through multiple sources.
This really is a painfully simplified synopsis of the subject but that’s my goal here. There is a seemingly bottomless pit of questions to ask around this topic. I’m just starting the conversation . . . what say you?
_________________________________________________________________________
Ben Bogie is a second-generation high-performance-building obsessive working as a project manager for BPC Green Builders of Wilton, CT.
Weekly Newsletter
Get building science and energy efficiency advice, plus special offers, in your inbox.
12 Comments
Might I be so presumptuous as to add a takeaway? :)
6. When in doubt, choose the most vapor-open (higher permeance) materials allowed by code for your climate, and install them in the most airtight way possible. Vapor diffusion is more often friend than foe with regard for wetting vs drying of building assemblies. Control bulk water and airtightness first. Airtight plywood, airtight OSB and airtight latex-painted gypsum board can often sufficiently control vapor diffusion in all but the coldest climates and highest interior humidities, such as with greenhouses or indoor swimming pools.
This is tough subject that seems difficult to reach consensus even among experts, so I appreciate the article and furthering of the discussion.
Very enjoyable and witty writing.
Watch out for Big Perm, they're only in it for the curls.
I have no such qualms about googling (embracing the hive mind), so I googled 'why can we see steam' since something struck me as odd about being able to see water vapor. Turns out that what we see is actually vapor turned back into liquid form (small droplets) when it hits the colder air.
This becomes a neat (and loose) analogy for buildings during heating season: inside the building we have sources of moisture and sources of heat which in turn increases the temperature and the vapor pressure of the container, just like in the kettle.
So water vapor is driven from inside the vessel to outside. As it exits, this vapor can condense into liquid phase as it contacts colder objects.
RE the box analogy. It is stated that "the more balls we add to the box, the higher the vapor pressure."
I would change that slightly to say that the more balls BOUNCING around in the box, the higher the vapor pressure. Vapor pressure depends on temperature, and shaking the box is analogous to increasing temperature (adding energy to the system). The balls sitting idly on the bottom of the box can be considered to be in liquid form and won't contribute to vapor drive.
Joe has some interesting things to say here about that elusive thermodynamic law: https://www.buildingscience.com/documents/insights/bsi-021-thermodynamics-its-not-rocket-science
I'm curious about what criteria defines an assembly that is not subject to concerns about vapor (takeaway number 3). Likewise, it was brought up in the recent Q&A about longevity of air barriers that perhaps assemblies that rely on air tightness to survive shouldn't be chosen.
I think these are interesting points; it would be interesting to see a list of assembly types that goes from higher vapor resiliency to lowest.
Obviously near top of the list is an uninsulated yet heated structure, but since most discussions here involve higher levels of insulation, I'm curious how the major assembly types would rank in terms of indifference to vapor profiles and air leaks.
Is it basically any system that keeps moisture sensitive elements warm?
Great article Ben, and you are just starting!
My comment is specifically geared towards cold climates and techniques I've seen used.
This article leaves me if nothing more confused. If this is true all home builders using 4 inches of polyfoam on there outside walls and zip sheeting will have mold fairly quickly. Kudos for the article but then to say at the bottom of the article it all depends on the situation for building really doesn't teach us much in respect to our wall structures. Id also like to know why the wall assembles that seem to break these rules are successful.
There's many article on this very website that state the way to mitigate moisture issues using 3-4 inches of polyfoam on the exterior which breathes almost at 0 at that thickness so are all these articles then flawed? Maybe I'm missing something and I'm really just interested in learning as much as possible about all the different nuances that are discussed on all these topics. I would like to think that at the bare minimum we should be able to form a consensus but then an article like this throws into doubt what I have been reading all over this website and building sciences website. It would be excellent if you expand further on your reasoning and to explain if vapor will react like this then why it doesn't on wall assembles that are completely the opposite of vapor open to the outside.
Thank you for making me think about these things I feel like articles like these create positive conversations that lead to better understanding of all these topics.
Wiscoguy,
What has caused you to worry about the exterior foam causing mold?
I’m not but the article the way it is written leads me to believe that being vapor permeable both ways is necessary. I wasn’t asking. Those questions from an argumentative stand point more like devils advocate. Trying to figure things out.
No knock on Ben, I'm an admirer of his, but I agree the Takeaways bounce around a bit.
#1 answers your concern. You only need one side to be vapour-open.
#2 As a general rule makes sense, but would perhaps of been better prefaced by saying "Unless you are going to compensate by using a thick enough layer of foam on the exterior...."
#3 Might be paraphrased as something like "Marginal assemblies are risky assemblies. Don't use them" . Ben's formulation is a bit confusing because all assemblies rely on the vapour performance of their parts.
#4 I draw a slightly different takeaway from. Rather than caring whether we know what's going on, we should again not use assemblies so fragile they won't work under certain site-specific situations - especially as these can change over the lifespan of a building.
My feeling is that the current confusion and proliferation of building assemblies will shake out in the next few years and each climate zone will end up with a couple of dominant ones that perform well without needing to be customized for each project. That's already started to happen in many areas, driven by building code changes.
Kiley's interview with Ben, featured today, provides some insight into Ben's recommendations.
Thanks Michael,
That fleshes out where he is coming from and explains his comments 0n impermeable exteriors and foam. Everything he says makes sense, I just didn't understand it.
"A general rule of thumb: As the thickness doubles, the permeability is cut in half."
I think this one slipped through the cracks. In fairness, the way permeance vs permeability is discussed nearly EVERYWHERE is really confusing. Does it depend on thickness or not? What does it mean if it does?
Permeability is a property of the material, and does not change with thickness.
Permeance is the ABSOLUTE number, meaning if you didn't know how thick the material was, it would still be useful because it ACCOUNTS for thickness. Permeability is WHAT it is. Permeance is HOW much of that 'what'.
There still are mixed opinions about permeability and solar vapor drive, especially when it comes to reservoir coatings. Thoughts on that?
Log in or create an account to post a comment.
Sign up Log in