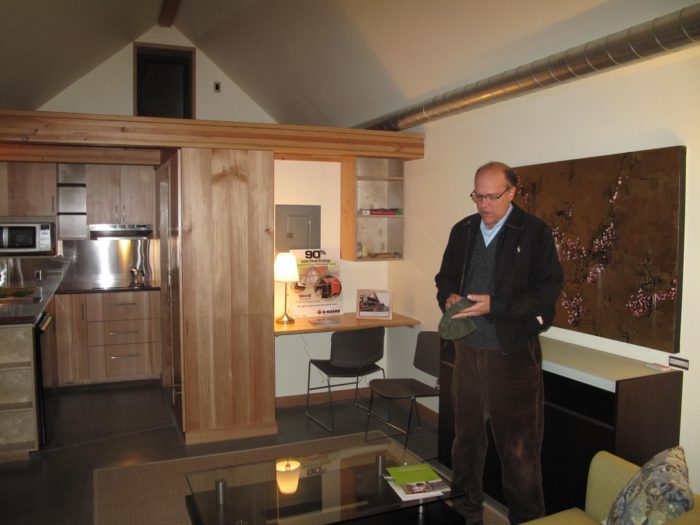
Image Credit: Martin Holladay
On March 16, 2011, I flew to Seattle for a three-day visit to Washington state. Although the main purpose of my visit was to attend the spring conference of Passive House Northwest, I devoted a day and a half to visiting Passivhaus buildings and construction sites in Seattle and Olympia. With the help of my gracious hosts, Dan Whitmore and Albert Rooks, I was able to see four Passivhaus sites and a large workshop where Passivhaus wall panels were being assembled indoors.
Because I packed in so many site visits and interviews in my short visit to the Northwest, it will take at least two blogs to report on my trip. Here’s the first installment.
Visting the Mini-B Passivhaus
Dan Whitmore is a Seattle builder who kindly volunteered to pick me up at the airport and offer me accommodations for my first night out West. On the way back to his place, we swung by the Phinney Neighborhood Association in Seattle to visit the Mini-B Passive House, a tiny cabin that now sits in a parking lot until the modular building finds a permanent home. The architect of the Mini-B, Joe Giampietro, met us there and gave us a tour.
The Mini-B — short for “mini bungalow” — was designed to meet the “detached accessory dwelling unit” requirements of Seattle’s building code. The city allows homeowners to install these small backyard buildings for use as guest rooms or mother-in-law apartments.
Giampietro wanted his Mini-B prototype to meet the Passivhaus standard. As he dove into the design process, he learned first-hand that the Passivhaus standard is much easier to achieve with a large building than a small one. Fortunately, Seattle’s climate is relatively mild, and Giampietro was able to achieve his goal — even though the Mini-B measures only 300 square feet.
Since high-performance…
Weekly Newsletter
Get building science and energy efficiency advice, plus special offers, in your inbox.
This article is only available to GBA Prime Members
Sign up for a free trial and get instant access to this article as well as GBA’s complete library of premium articles and construction details.
Start Free TrialAlready a member? Log in
34 Comments
Passivhaus Insulation
Its interesting to note that all of the referenced houses used glasswool (fiberglass) insulation in dense pack applications for the sidewalls as well as in the open blows in the attics. The improvement in glasswool fiber technology is starting to be more evident these days. These newer glasswool products yield higher R values and increased air resistance over cellulose at lower installed densities. Plus, most are now produced with significantly increased amounts of post consumer recycled glass (some plants now in excess of 50%). These new fibers are virgin glass (not reground batt products) and contain no binders at all. If the exterior fiber board bellied out under pressure from the glass fiber product, what would it have done if the contractor had tried to densepack cellulose at 3.5# or more? To paraphrase the Oldsmobile commercial of many years ago, "This ain't your father's Oldsmobile". Its evident that the glass fiber industry has stepped it up. Having used both cellulose and glasswool blowing products over the years, the improvement in glass fiber technology is evident in these products.
Denser to a point reduces
Denser to a point reduces convection thereby increasing R value. At a higher than spec density your conduction losses starts to reduce R value. The "pink panther" people have a chart on their website showing this I think.
We appreciate the interest!
Martin,
Thanks for including information about our work in your blog. As readers are learning about our firm, I want to clarify that Tessa Smith is a co-owner of the Artisans Group, in addition to being our design lead.
Randy Foster
http://www.ArtisansGroup.com
Thanks, Randy.
Randy,
Correction noted -- thanks.
Bulging with dense pack
Doug and Chris,
On both Blackbird Builders, and the North Residence, both wall systems reached a full density of 3.5lbs/cuft. by bag count. However these are thick walls with big cavities, so the density was increased. You can see a great discussion on the density topic at: https://www.greenbuildingadvisor.com/blogs/dept/musings/how-install-cellulose-insulation. For fiberglass, the issues are similar.
As you can imagine, the stress on the internal and external sheeting was increased. While this caused the panels to belly out, this was for the most part, planned for. I don't recall a cavity growing by 3/4", but the change in shape was significant. At the exterior, the rainscreen strapping is taking care of the issue. At the interior, Dan Whitmore added strapping, and then drywall.
The North Residence wall system plan included a "service cavity" that took care of the dense pack deformation issue AND place the airbarrier well behind the drywall layer. I can't say enough about adding service cavities in these high quality wall systems.
As far as exterior sheeting goes... Since these wall systems were all diffusion open to the exterior, fibre board or Homosote was used. Yes... It has trouble with the stress of dense packs, but these are really first steps in learning our options and their outcomes.
The solution will be in changing the exterior material. The next options up, and one that I think will be final for diffusion open walls (at least for me), will be two products from the German wood fibre company Agepan. You can find current US information at: http://www.peakbp.net/, and more soon at the smallplanetworkshop.com website. What we are looking at are softwood fibre boards that are diffusion open, but strong enough to handle the stress of the application without deforming. One board is the DWD. It's 5/8" thick, reasonably priced and should do fine if all we need is to keep the insulation inside the box.
The second product that we are looking at is far more interesting. It's called Agepan THD 230 and is available in various thicknesses. We are looking at the 60mm, or 2-3/8" thick boards. They are low density wood fibre boards that are air & water impermeable, but vapor open. Since THD has good thermal resistance at a little under R 3/inch, A 60mm board has an R value of 7. All of these boards are ok for limited exterior exposure since they are wax impregnated. The boards are Tongue and Groove which can negate the need for a housewrap and are VOC free. Import agreements are just being finalized so it's hoped that they will be on a project soon so we can see how they perform.
Response to "Passivhaus Insulation"
O Riversong, where art thou?...
Wow Chris, I think you had seconds when the fiberglass kool-aid was passed around. As a Passive House Consultant I'd never let the stuff near one of my projects, especially in the roof or attic. To be fair, if there ever was an application where “dense pack” fiberglass could succeed, it would be in an airtight Passive House wall assembly. However, in most applications the product's performance falls flat.
Many weatherization contractors here in the Northwest install the "new" dense pack fiberglass products in walls and roofs. I've blower door tested dozens of these homes and the results are simply pathetic. Additionally, some of the worst ice dams and roof failures I have seen were in recently built homes that utilized "dense pack" fiberglass in the roof system (yes they were even vented).
After observing the product repeatedly under-perform in both 10k and 5k HDD climates, I have little faith that the typical installation meets labeled product values.
Could it be that performance claims provided by the same insidious companies that have been pushing fiberglass batts for the last half a century might be overstated? Just sayin.
North Residence
I find the 3/4" bulging of the fiberboard sheathing due to the dense pack fiberglass interesting. How will the drywall fare with this much pressure? Are the wall studs 16" or 24" oc. Fiberglass insulates due to the air pockets within the material, glass conducts, this does not sound right.
WRB over vertical strapping on North Residence
I'm curious about the decision to install the blue wrb over (rather than under) the vertical strapping for the ventilated siding on the North Residence.
Are there advantages beyond the obvious one of protecting the strapping from water damage? Is water damage of strapping really an issue with which to be concerned?
WRB over rainscreen
Devan,
My understanding is the initial wrb that was installed under the battens got a little beat up along the way (as it often does), so they simply added an additional layer of peel and stick wrb for good measure.
Colorful WRB
Devan,
Yes, Skylar is correct. The walls were insulated from the exterior. Mark (in the photos) was concerned about density and did not feel that the insulation contractor (on the contractors first PH job) was getting the levels that Mark preferred. So... more borings to confirm and add insulation. In the end another WRB was added over the existing Tyvek and strapping to be sure that the home did have a intact and effective WRB.
I've read in other GBA blogs that there is a learning curve in large cavity blown in applications for the installers. This project was no exception. The GBA post that I referred to above about dense packing large cavities was both timely and insightful (in my onion) regardless of whether the product is fiberglass or cellulose. Big walls are a different animal.
Thanks Albert and Skylar
Thanks for the WRB explanation.
Cellulose IS Definitely Better IMHO
I'll pass on the fiberglass kool-aid, but I do believe strapping is almost necessary to achieve flat walls with dense pack assemblies. As far as the low perm OSB on the inside and fiberboard on the outside, I think a better approach might be to use a kraft building paper (aquabar , perm rating .7 or equivalent ) behind drywall and use higher perm plywood on the outside, which uses less wood fiber overall and offers solid backing for exterior siding or vertical rain screens.
OSB v. Plywood
Ii think the interior OSB is air barrier layer, fiberboard so wall assembly is diffusion-open. There are a number of reasons to locate air barrier on the interior of a PH (especially w/ service wall - the typical approach in DE) but mostly so that you can touch up any areas easily during blower door tests.
Air Barrier/ Vapor Barrier Locations
I don't think OSB should be considered vapor open, with a perm rating somewhere around 1. I think there are two schools of thought on the best way to assemble a double member wall, especially considering some prefer bearing load on the interior plane and cantilevering the outside plane. As far as material efficiency, I believe drywall is the simplest and most economical way to get interior wall surface, air barrier, and vapor barrier(PVA primer) all in one. I do believe a super insulated structure can perform durably without a vapor barrier, as long as the air sealing details are well executed.
Simple and Economical Air Barrier?
Matthew,
Sounds like you "like" Airtight Drywall Approach (or similar).
Are you using drywall gaskets or sealant or both?
What are your blower door results?
Any idea of what the Airtight Drywall sealing materials& labor costs are for one of your typical homes?
Response to John
I do believe the best improvement I can make to my current approach is better air sealing. I like the Airfoil elec. boxes, but I think that all of the current players in the flanged and gasketed elec. products are leaving too many holes in available products. Airfoil only makes single, double, and a round box, so it starts to add labor to my electrician's bid to try and use these superior products. Caulking the boxes, although inferior, seems to be the easiest way to go in my area, which is not on the forefront of innovative materials and techniques. The Airfoil boxes, are around 5 times the cost of a standard box. The real cost of an ADA approach seems to be the added labor and non-conventional nature of the details, which non- believers discourage by price increases. I have had a hell of a time getting subs to understand, support and not gouge me ($) over better building techniques.
ACH50
Mathew,
What are your blower door test results? Do you project energy costs for your building projects? How much time do you spend air sealing conventional electrical boxes on exterior walls and what is the result when pressure testing? Have you ever used the AIRFOIL product?
ADA and passivhaus
OSB is semi-permeable, the wall assembly is open to the exterior.
you'll never pass the Passivhaus blower door test w/ Airtight Drywall Approach. Plus, it's ripe for long-term failure.
ADA and PH
Mike,
I am working with Allen on his PH project and he is using ADA in combination with high R exterior sheathing. If you feel he is in error you may want to contact him.
http://oneskyhomes.com/content/passive-house
ADA approach
doug,
if allen thinks he can achieve it, then i won't second guess him. i've not seen or heard of anyone hitting sub-0.6 use the ADA approach, though. even if they do, the ADA approach isn't the best for long term durability of the air barrier. homeowner will punch holes in it, future cabinet installation will rip out entire sections of drywall... if it's a belt and suspenders approach w/ ADA and something along the lines of the huber zip system - that would be different. i know a lot of people on GBA are proponents of ADA, and i'm not knocking it as a bad system, but for high performance buildings it just doesn't make much sense to me.
Permeance of Plywood and OSB; They're "kind of smart"
When combined with the meticulous sealing of all seams and penetrations, Plywood and OSB (osb seams are marginally easier to seal) can serve as a nearly flawless air-tightness layer and have been widely used as such on numerous certified Passivhaus projects. I have seen blower door results as low as 0.17ACH50 when utilizing this approach.
As Michael Eliason stated, OSB and Plywood are indeed semi-permeable. Cup measurements (wet and dry) tell us that diffusion coefficients across OSB and Plywood increase with an increasing relative humidity and decrease under lower relative humidity. The attached graphs clearly illustrate this relationship.
It is actually surprisingly difficult to find consistent wet-cup and dry-cup perm ratings for OSB or Plywood. The figures below show some common wet and dry cup perm ratings I have come across:
OSB
Dry-cup 0.7 perms
Wet-cup 2.0 perms
Plywood
Dry-cup 0.46 perms
Wet-cup 4.0 perms
According to Form No. J450 published by the APA (Engineered Wood Association)"...at 50 percent humidity, the water vapor permeance of 7/16-inch OSB sheathing is approximately 2 perms, but the water vapor permeance may be increased to 12 perms when the humidity is increased to about 85 percent."
Notes:
1. Dry cup testing – Conducted with 0% relative humidity on one side of the test sample and 50% on the other side.
2. Wet cup testing – Conducted with 50% relative humidity maintained on one side of the test sample and 100% on the other side.
I hope this helps clear up the discussion.
ADA as backup
Mike and Skylar,
The One Sky Homes project is in San Jose, CA and is exactly as Skylar describes. The exterior sheathing is the primary air barrier and the ADA is the secondary air barrier. They feel the two in combination will meet the .60 ach50.
Protected Air-tightness
I agree with Mike that trying to achieving 0.6ACH50 using the ADA (airtight drywall approach) could ultimately prove to be a risky design choice. A better solution is to seal the exterior sheathing seams (plywood or osb) and rely on the ADA as a secondary air-tightness system. An even better solution would be to seal the exterior seams of the structural sheathing and then throw on some non-load bearing Trus joists or Larsen trusses to serve as a thick exoskeleton (see attached photos) that can be filled with cellulose insulation. With this configuration, the air-tightness layer (the structural sheathing) will be on the warmer side of the wall, while still remaining protected from the building occupants. Another benefit of this arrangement, one that was pointed out to me by Thorsten Chlupp, is that the tapes and sealants used on the structural sheathing will not be exposed to temperature extremes, potentially improving the longevity of the air-barrier system. This benefit is worth considering when building in extreme climates such as Fairbanks.
In less severe climates, locating the primary air-tightness layer at the exterior structural sheathing should produce fine results, especially when coupled with cellulose insulation. To quote the seasoned PH builder Blake Bilyeu, cellulose insulation is a "hygroscopic redistribution highway". The product has the unique ability to safely buffer and redistribute incidental moisture buildup in the wall assembly. This includes moisture that is having a difficult time diffusing outward through any sheathing seams sealed with impermeable tapes (For safe measure I wouldn't go wider than 4" with impermeable tapes).
Taped OSB or taped and
Taped OSB or taped and floated drywall joints, your air leaks are penetrations and terminations. I think there is a fundamental difference in the way some of us are "seeing" structures. The truth is, many things we are experimenting with could be potentially headed for premature failure or lesser durability. I personally won't touch OSB for this reason. If you are trying to create air barriers with both interior and exterior surfaces, you must have deep bank accounts and a penance for redundancy, or no penetrations or terminations on the exterior.
"Seeing" the wall
HI Matthew,
I agree, they are totally different approaches.
What Mike and Skylar are pointing too is a fairly common wall assembly in Europe. We've all heard about the 300 year wood structures that they build in Central Europe. This is the wood frame approach to those structures.
Most of the homes built in CE are Massiv Construction. Essentially masonry with continuos exterior insulation. They tend to avoid foams and rely on diffusion open materials from the masonry out. At the exterior face of the interior side of the masonry is a service cavity (2"-3"?) for electrical etc. The air barrier is placed on the face of the masonry and therefore protected for the life of the building by the service cavity.
The wood, or timber frame as it's called, is a similar system: The entry level is approximately our 2x8 frame with a dense insulation like cellulose, mineral wool or glass. The exterior of the frame is generally vapor open sheeting so the wall, and it's layers, dry to the exterior. Ventilated rain screens are common.
The OSB is placed at the interior of the frame and serves a triple function:
1, Shear loads. The exterior material often can't deliver this because it's chosen for diffusive and insulative properties that make it a poor structural material.
2, Primary air barrier. This layer is taped (or whatever... ).
3, Vapor barrier. Since it's airsealed, it makes an easy vapor control point. As OSB is around 0.7 perms. This is enough to stop large amounts of interior vapor penetrating the cavities. And... it's still just open enough to let things dry to the interior when the levels are higher in the cavity than the interior. Its a failsafe feature.
As with Massiv, a service cavity is placed over the osb and the finished wall over that.
You can see that the walls system is really high quality and very durable. Short of structural damage by some kind of impact or earth quake, the only thing that will bring a wall down like is water and they've got that managed very well in both liquid by the rain screen and vapor intrusion from the exterior and the interior.
As I said, this is a high class and durable wall. You will also see occasions where the interior OSB is moved to the exterior sheeting and replaced by poly or a membrane. This is more of a code level wall and not a high performance wall. However in both cases, the layers are pretty well (they have their hackers too!) airsealed and are behind a service cavity with finished drywall outside of that.
Once you make the leap from ADA to a service cavity, The likelihood of the airbarrier remaining intact for the life of the building exponentially grows. Especially when it's a long term building.
Air Barriers and Heat Sources
First let me start by saying I've never installed ADA, but I do have serious concerns regarding it's long-term effectiveness and potential to be an avenue for structural damage.
One of Drywall's strongest traits is it's malleability. It's also inexpensive, easily cut & readily repaired so it's ripe for occupant degradation. It's very rare to see even a 10 year old structure that hasn't seen a healthy amount of poking, drilling & such. When such holes are created in an air-barrier they can become significant conduits for air flow which of course can carry vapor into the previously sealed cavity. There are significantly fewer holes cut in the exterior of most every building, during construction and during occupancy.
Not having completed an ADA installation, I can't compare first hand notes, but by rough estimation using plywood with taped seams on the exterior might not be significantly higher in cost. Yes this would be on the framer (or a specialty crew) but the following trades wouldn't need to be as closely monitored nor as likely to ask for premium pricing.
On another note, regarding my heating method of the above house my calculation are a little different than Martin's. Per PHPP the peak heating load (PHL) for the building is 5691 BTU/hr. Also per the PHPP my ventilation needs are 89cfm and the inlet water temp to the heating coil is 126Deg F. Using Ultimate Air’s performance chart for their Water-To-Air Coil (3585 BTU/hr @ 120 DegF water & 100 CFM air flow), I calculated the coil to put out 3350 BTU/hr. Definitely below the PHL. However, since the building has 2 living units ( a main 3 bedroom with an attached apartment) city code requires a separate controllable heating source in each unit – the Mother-in-Law would be rather upset to have the thermostat set at 50 F and behind a locked door while the kids are away on vacation.
Since PHL here in Seattle is rarely reached, generally less than two weeks of sub-freezing daytime temps per winter, my calculations were that the coil would meet the standard heating load and the elec. resistance units would give the building an extra boost when needed and meet the code requirements. Were a larger coil to have been affordably available I would have happily gone there (but I still would have needed a second source) but budget has been a main driver on this project.
Thanks for inaugurating the place, Martin!
Calculating the heat output of the hydronic coil
Dan,
Thanks very much for sharing your calculations for the heat output of the hydronic coil. It seemed to me that the heat output would have to be less than the design heating load, which you have confirmed. But since you have wall-mounted electric resistance heaters in addition to the hydronic coil, I'm sure that the building will perform well.
Thanks again for you hospitality. It's a great building.
Bensonwood before Passivhaus America
I understand the service cavity idea, but I don't think it guarantees any less possibility of air barrier compromise. Bensonwood timberframe homes were the first American builder to implement service cavities, but I don't think they are airtight. They installed these for future renovation probabilities. Remodeling is due mostly to aesthetics, and judging Passivhaus buildings on this, these buildings will be remodeled for sure. This will most definitely interrupt the service cavity and the whole wall in general, but the whole idea that a building will be airtight is false, no matter how you build it. I haven't seen any building with an ach of 0, and these tests are performed with the building in a state of closure that I am sure will not remain in daily use. As far as I concerned, any cutting and patching done in drywall is then taped and mudded, thus air sealing it once again. To imply that Passivhaus' in America will not be remodeled, thus air barrier temporarily broken, is utterly ridiculous. As much as I respect the way many things are done and designed in Europe, this is where I say there is more than one way to get to Denny's.
The best way to Denny's
Matthew,
with a lot of interest I follow the discussions on this blog. I agree with you that there is more than one way "to Denny's", but: The building technique in the german speaking countries has developed within the last 20 years in terms of air sealing and ideal design for a durable tight and performing envelope. One of the crucial details is the service cavity. Protect the air barrier against penetrations caused by installation or later by the occupants! The cost difference for this additional layer is usually not significant.
I have been visiting a job site of Bensonwood 2 weeks ago, it was a regular house with their "standard"-design and they have reached 0,76 ACH50. They really do a great job at Bensonwood and have developed a outstanding wall design.
However as Siga Product Manager I see a lot of different approaches to air sealing, but I can tell you for shure that you will find more and more constructions with interior air barrier and service cavity in North America.
Hello Martin, Albert, Dan and Randy, I am happy to finally join this discussion!
So how low can you go...?
Matthew,
Regarding how tight is tight, and how long it's going to be that tight; I thought I'd share what I've seen so far.
I've been in 3 passivhaus blower door tests this year. All 3 were an OSB interior airtight layer. Two of them on Larsen Truss and one a double stud wall. All 3 tested from .38 to .50 ACH50. Excellent results! In all 3, we went around the room looking for the leaks with smoking candles and IR camera's. What was found in 2 of the three cases were fenestration leaks. These leaks were within the window and door, not at the joint to the building. We could not find any leaks in the wall systems, base joints etc . The third had really really good pazen windows, was missing a door and leaking through the tyvek in it's place, and therefore inconclusive as to the total envelop.(even though it was still less than .5ACH50
2 of the three have a 3.5" service cavity over that OSB layer, with a drywall face. The thing I appreciate about it, is that looking into the future, as uncertain as it is, I think it's likely that protected OSB will remain undisturbed far more so than the finish drywall layer.
As you point out, if a remodel happens, then all bets are off. I can only hope that a new high quality house like this isn't going to be remodeled too soon. But if it is, my hope is that discussions like this will raise the appreciation of air barriers to the point that when the remodel does happen, the air barrier is protected and treated with the same care that a reclaimed hardwood floor would get: It's covered, protected, and modifications are done in a way that ensures it's continuity.
That goes for ADA or what ever the construction is. Hopefully as air barriers become common building language outside of GBA, and the high performance community, remodelers will have a process: 1, Identify the air barrier. 2, ensure it's continuity throughout the project. 3, Close the project with a successful blower door test. Pick your number for what a "successful" test is. Hopefully the "standard" number gets smaller as the years progress and the airsealing process gets easier.
As for no house being zero... Here's one for the "nerd file":
I was at a workshop in Switzerland and met another Passive House consultant. (I should say at this point that I'm not a PH consultant, builder or rocket scientist, just a building materials and systems nerd.) He was from Belgium and purported to have built the tightest house in the world. Or... at least the "tightest" recorded that he could find. (I hear Martin's skepticism already... ) The project was in iceland and was a home in the shape of an octagon. He could excitedly go on about how much air passes through 3/4" thick Plywood vs. OSB. They had first hand knowledge at the end. He said OSB is tighter than plywood. He was quite pleasant and we were both in a professional airsealing workshop, so I'm taking him at near his word. He said the blower door test on the project was 0.08ach50. That's almost a factor of ten times tighter that the 0.6 ach50 for Passivhaus.
Remodels
Like I said, as a builder, I know remodels are mostly due to aesthetics, and judging by these structures, they will be remodeled. Nothing lasts forever. Plumbing waste stub outs, water supplies, and vents, are just a few things that penetrate that "perfect" air barrier right from the start. I would never argue that windows and doors are air leaks, as hinged doors are especially impossible to make airtight.
Passive houses and ERVs
I've been reading through your blog here martin. Great of you to take the time to see the projects while in WA.. sorry i missed it this year. My passive house project (www.sustainablepath.us) is getting close to complete. Unusual envelop I guess... ICF plus an inside stud wall.. lots of dense pack cellulose. First blower door was 1.0 ach50... some leaking around the window installation. This was before drywall too. Installed my Ultimateair Unit just a few weeks back. It is tied to some earth tubes, and I am going to posting some data on their performance - in conjuction with econocool from the recoupaerator. Keep up the good work!
Response to Jason
Jason,
Thanks for the update, Jason. Good to hear from you again.
I'd love to hear information on earth tube performance, so keep in touch.
Mamaroneck, NY. Passivhaus project announcement!
I am proud to announce the start of another passivhaus project in Mamaroneck, NY. We are finalizing the design and materials. This is my second passive project. We're really taking our time on this one and the home owner is a driving force behind our efforts to achieve a great result. This will be a remodel which only increases the difficulty, but bring it on! Can't tear'em all down! The website is underway...
Our goal will be to not only achieve passivhaus standard but to do it with the most sustainable methods and products that fit into our budget. Anyone have any thoughts about what it means if we all used EPS or poly-iso foam for everything? We'd be drowing in toxic off gasing chemicals would'nt we? That should not be acceptable! So i challenge everyone reading this to incorporate the use of non-foam based insulation in their respective projects. It should be considerd cheating in my opinion. I recently saw the mushroom guys are making progress can we get a major story about them again?
Thanks to all who share their info and best wishes to everyone who endevours to take on these projects!
Log in or become a member to post a comment.
Sign up Log in