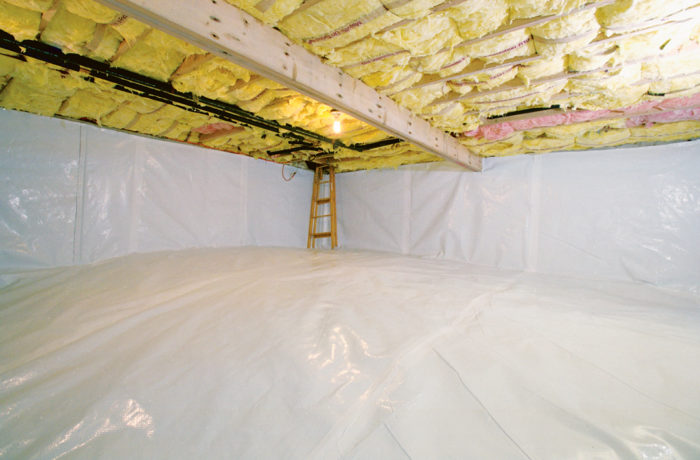
Image Credit: Fine Homebuilding/Harold Shapiro
Andy Chappell-Dick is at work on a house in Climate Zone 5 where the task at hand is to upgrade a crawl space by adding insulation as well as a membrane to block the infiltration of moisture. The catch? The owners want to avoid the use of rigid foam insulation if at all possible.
The floor of the crawl space is about a foot below grade, Chapell-Dick writes in a Q&A post at GreenBuildingAdvisor, and the area seems to be well drained. Foundation walls are made from concrete block (CMUs).
He plans to foam in pieces of rigid extruded polystyrene in the rim joist area. To insulate the crawl space walls, Chappell-Dick wonders whether Rockwool Comfortboard 80, a rigid mineral wool insulation, would make a good substitute for rigid foam. Rockwool Comfortboard 80, according to the manufacturer, is non-combustible and chemically inert, and it’s made from natural and recycled materials, including rock. Rigid foam is a petrochemical.
A second issue is how the waterproof membrane should be installed: should it be run up most of the crawl space wall, or can it be terminated at the base of the wall? And, Chappell-Dick wonders, does this detail have any bearing on the performance of insulation?
That’s the backdrop for this Q&A Spotlight.
This is not the place for Rockwool
The inherent air-permeance of mineral wool insulation makes it inappropriate for this application, writes GBA senior editor Martin Holladay.
“The mineral wool can’t prevent humid interior air from contacting the cold crawl space walls,” he says. “The likely result will be moisture accumulation and mold.”
The best route, Holladay says, is to use an air-impermeable insulation — either rigid foam with seams that have been carefully sealed or closed-cell spray foam.
In theory, mineral wool and a clean cement…
Weekly Newsletter
Get building science and energy efficiency advice, plus special offers, in your inbox.
This article is only available to GBA Prime Members
Sign up for a free trial and get instant access to this article as well as GBA’s complete library of premium articles and construction details.
Start Free TrialAlready a member? Log in
13 Comments
fiberglass stud walls with
fiberglass stud walls with poly in NY basements is code required.
Clarification to all,
DO NOT INSULATE THIS WAY. All I am saying is that in my county they mandate for us to insulate wrong. And so far I have not found one spec of mold in OTHER builders homes that I have gone in AFTER THE FACT to do additional work.
I DO NOT INSULATE THIS WAY PERIOD.
CLEAR I HOPE.
Mold is a living thing!
Mold is alive and it needs food and water to live!
Mold does not grow on clean concrete - water is not enough, it needs food.
Why insulate a crawl space? You don't live there. What will it achieve? Why would anyone spend good money on a space that is unused and unseen?
Insulate the floor, at least this helps keep the room above warm and saves money.
Response to Roger Anthony
Roger,
Q. "Why insulate a crawl space?"
A. Here are four possible reasons:
1. To keep pipes from freezing.
2. To make sure that any ducts are located within the conditioned envelope of your house.
3. To lower your energy bills.
4. To reduce crawl space humidity levels.
For more information, see Building an Unvented Crawl Space.
poly against concrete - new construction
I have been specifying poly under the slab and wrapped up the foundation walls to a point high on the wall where it get taped to Intello or similar air barrier which then forms the continuous air barrier for the above grade sections of the house. There is also a break at the top of the concrete wall to prevent moisture from reaching framing. This keeps the concrete foundation wall and it's inherent moisture to the outside of the envelope. An interior stud wall is spaced out enough from the foundation wall to hold rigid foam in place behind it. (EPS or otherwise) No interior air or vapor barrier in the basement. The stud wall may be insulated or not. Is this a valid approach? With the poly in this location, could I simply build a stud wall and fill it with cellulose and eliminate the rigid?
Response to Robert Swinburne
Robert,
Your approach sounds fine with me, as long as you keep a layer of EPS (or some other type of rigid foam) between the cold concrete and the stud wall.
I would never recommend the use of cellulose in a crawl space, because the chance that the cellulose will get damp some day is just too great. I know that some builders will insulate a stud wall like the one you are talking about with fiberglass or mineral wool (again, with the proviso that there must be a layer of rigid foam between the concrete and the studs) -- although I don't particularly like that approach either, because crawl spaces are subject to damp conditions and flooding.
In short, I'm a "foam only" guy when it comes to crawl spaces. If you want more R-value, just make your foam thicker -- and leave the studs uninsulated.
Anyway, that's my recommendation. If you decide to insulate the stud bays anyway, in spite of my advice, I would use mineral wool, not cellulose.
Thanks Martin
Good answer. I'm actually thinking more along the lines of either meeting the VT energy code for a basement or, more commonly, a house on a sloping site where one side of the basement is open to grade and it is used as living space. I am a big proponent of a stud wall service chase and rock wool if necessary but would rather gain the insulation using EPS. Definitely "foam only" in crawl spaces though.
Good to meet you in person in Portland earlier this week.
Response to Robert Swinburne
Yes, it was good to meet you. Glad we agree on crawl spaces.
Crawl
In the picture the bubble on the floor is likely created by the pressure of outside air infiltrating, but now stopped by the poly film. I watched amazed as the poly in my crawl filled like a big balloon.
My assembly is foam board on top of the poly on top of the concrete wall. A tar tape seals the perimeter of the poly before the top of the concrete. There's moisture under the poly where there is concrete and a pebble floor. Should be OK - yes?
Response to Anthony Papay
Anthony,
I didn't select the photo that accompanies this article -- I don't have any more information to explain it -- and you may be right about the apparent bubble on the floor. I had a different reaction when I saw the photo, however: I assumed that the plastic covered a mound of dirt or a natural outcropping of some kind. (Such features are fairly common in crawl spaces.)
It's hard to get a full picture of the details in your crawl space from your brief description. But if your question concerns the visible drops of moisture or condensation behind (underneath) the polyethylene, you are correct: these beads of moisture do no harm.
I Have Run Into This Too
I have a very green-motivated client building a new home in CZ4 who wants to do the exact same thing. Wants to avoid foam for various environmental and health reasons, wants a sealed crawlspace, found Rockwool Comfortboard.
The Rockwool rep stated that Comfortboard was an acceptable product to use in the specific application of a sealed crawlspace. But, in their literature on ComfortBoard in basement walls, which he directed me to, they are specifying it here only in combination with a vapor/air barrier on the foundation wall (as you do with a sealed crawlspace), then Comfortboard, then a furred 2x4 wall with Rockwool Comfortboard, a vapor barrier over those if needed in your climate zone, and most importantly, drywall over that as the all important air-barrier. Makes some sense for a basement, but is it worth putting that kind of detail into sealed crawlspace insulation for the sake of avoiding foam plastic? Well, maybe. Or could you find a way to cover the Rockwool Comfortboard with some kind of less expensive air and/or vapor barrier as needed, such as Smart Membrain, without going to the extent of 2x4 walls and drywall? Well...maybe.
late to party
Just saw this linked on FaceBook.
For those advocating for just using foam in the crawlspace, you really can never just use foam because the IRC forces you to cover the foam. You can cover it in mineral wool though.
See IRC R316.5.4, I'm looking at 2009.
I have to disagree that foam is the best material here. The likely hood of getting it good and airtight is slim, and adding the operation of taping to the crawlspace work seems like throwing more time after time poorly spent. If moisture gets behind the foam and you get condensation, then its going to have a tough time drying.
There are no good options. At least if you use mineral wool, get the crawlspace buttoned up with a slab on poly, the outside of the wall waterproofed, or at least damproofed, get positive air circulation through the crawlspace just like any other room in the house, then at least anything happening against the wall stands a good chance to dry to the inside.
Other than that, build a slab on grade.
Gypsum board thermal barrier in crawlspace susceptible to mold?
Thank you for all the information posted in this article. For a crawlspace in Boulder Colorado, we are considering:
Seal foundation vents.
Cover dirt floor with impermeable vapor barrier.
Insulate rim joist with cut blocks of 2" Rmax Thermasheath polyiso foam board and Great stuff sealant.
Insulate the crawlspace masonry wall with 2" Thermasheath or two layers of 1" Tuff-R polyiso board with taped seams.
According to fire code, the foam board needs to be covered with a fire protecting layer such as 1/2" gypsum board. I am aware that Dow Thermasheath might not require such a covering, but it is unavailable in our area.
So, finally to my question: is it good practice to use sheet rock as a thermal barrier in the crawlspace? It is my understanding that the paper backing is an ideal food for mold; also if the crawlspace were to flood in an extreme storm event, the wet sheetrock would all have to be replaced?
Because of the complexities arising from the thermal barrier issues, many insulation contractors in our area are insulating crawl spaces using perforated vinyl faced fiberglass roll batting, with the vinyl face toward the interior of the crawlspace. Do you think this practice is acceptable? It seems that many articles I've read vehemently oppose the use of fiberglass in crawl spaces.
Thank you so much for any advice as how best to approach code compliant insulation of crawl spaces in our area.
Response to Ross Philip
Ross,
Q. "Is it good practice to use sheet rock as a thermal barrier in the crawlspace?"
A. Yes, as long as you have taken the necessary steps to keep the crawl space dry. Properly detailed, a crawl space can be (and should be) as dry as a finished basement.
Q. "Many insulation contractors in our area are insulating crawl spaces using perforated vinyl faced fiberglass roll batting, with the vinyl face toward the interior of the crawlspace. Do you think this practice is acceptable?"
A. The practice you describe probably meets code, but it's risky. If the climate is dry, and the crawl space is dry, fiberglass insulation can work. However, there is always the risk with this method that the walls will get moldy.
This approach works better in Colorado than North Carolina -- but I still wouldn't recommend it.
Log in or become a member to post a comment.
Sign up Log in