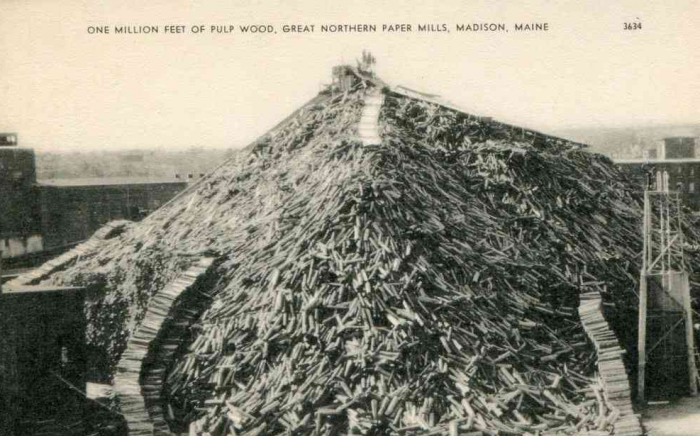
Builders eager to get their hands on wood fiber insulation produced on this side of the Atlantic will be waiting until the end of next year before it becomes available.
GO Lab is now repurposing a shuttered paper mill in Madison, Maine, and is on track to become the first North American producer of a type of insulation that’s available only as a European import. The company, which first announced its plans in 2017, says it will close on $60 million in financing in late July or August. But engineering, financing, and other parts of the business have come together more slowly than the company originally thought, pushing the start of production of loose-fill and batt insulation to the fourth quarter of 2021 and to late 2022 or early 2023 for board insulation. That time frame could still be changed.
GO Lab originally hoped hoped to begin producing some insulation this year. In a telephone call, GO Lab President Joshua Henry—a college chemistry professor turned entrepreneur—said the delay should work in the company’s favor. Trying to launch a new product in the middle of a global health crisis would have been tough.
Wood fiber insulation, which is readily available in Europe, is imported into the U.S. and sold under the Gutex and Steico labels. But high shipping costs have kept it an expensive niche product. GO Lab, a spinoff of the Belfast, Maine, design-build firm GO Logic, is aiming to make wood fiber insulation competitive in cost with other types of insulation on the market.
Henry says wood fiber insulation has several performance advantages, including better ecological credentials, better sound attenuation, and vapor openness that won’t trap moisture in building assemblies. Its thermal performance is about the same as mineral wool (for batts) or cellulose (for loose-fill). Wood fiber insulation has grown into a $700 million market in Europe, where masonry, not wood-frame buildings are the norm, he said. Because wood fiber batts, panels, and loose-fill are essentially drop-in replacements for what’s already available, they should be a good fit here—as long as their appeal extends beyond green builders.
“We see that this is not going to be a successful project unless the product is accessible beyond the green home market, or the ecological builder, or the carbon-neutral builder,” he said. “And I think it has every reason to be that. It’s not just the ecological choice, which it is, but it offers performance benefits. It offers solutions and it is cost competitive and we think everyone is going to love this product.”
Batts and loose-fill will be first
GO Lab will be using part of a paper mill that closed four years ago as the state’s paper industry was contracting. The labor pool and the region’s extensive wood resources are still there. The used equipment for the production lines is coming from a German manufacturer.
The first two production lines will be geared toward loose-fill and batts, in part because they can be installed with the same equipment and in the same way that cellulose, fiberglass, and mineral wool are being installed now. Insulation contractors will not have to learn new techniques or buy new equipment to use it.
The batts will be made from wood fiber mixed with a small amount of polyester fiber. The mixture is formed into a mat, put into an oven and heated, causing the polyester fiber to begin to melt and bind the wood fibers together. The polyster retains enough of its structural integrity to give the insulation batt some rigidity while remaining flexible.
Batts will come in widths for 16-inch and 24-inch framing but will not be faced with either kraft paper or foil. The firm consistently of the batts will allow a good friction fit between framing members.
Loose-fill will behave much like cellulose, Henry said, and installers should be able to use existing equipment without any special retraining. The only difference is that wood fiber loose-fill will not have to be packed to the same density as cellulose in order to get the same R-values.
Board stock will come last
There are several reasons for this GO Lab strategy. For one, it didn’t seem prudent to bring three production lines on at the same time. Despite updated energy codes, many builders still don’t use a continuous exterior layer of insulation on the houses they build, and some of the details that go along with it can vary by climate zone, so there isn’t the same broad, ready-made market for wood fiber board insulation as there is for batts and loose-fill.
In addition, Henry said, it would be possible for GO Lab to import board stock from Europe and sell it here while the import numbers absolutely don’t work for either loose-fill or batts because those products are not as dense. Shipping costs become prohibitive for the batts, which weigh about 3 lb. per cubic foot. A shipper might be able to get $500 worth of batts into a container but face shipping costs many times as much. “It just does not work at all,” he said. “The board doesn’t really work, either, but it’s better.”
Henry did not offer any specifics when asked about finance or retail partners, but he did say GO Lab’s distribution area would probably be the Northeast. In general, shipping insulation is expensive because of its low density. As Henry put it, “it’s a product that cubes out before it weighs out.”
Another startup folds
While GO Lab’s future looks promising, another Maine startup that was developing a different type of wood-based insulation has closed up shop.
Nadir Yildirim, a Turkish native who attended the University of Maine for his doctoral work, later developed an insulation made from nano-fibers of cellulose. Yildirim won a $247,496 grant from the National Science Foundation and formed a company called Revolution Research. He was able to produce insulation prototypes, which he called Arbolate, as he searched for manufacturing and licensing partners and sought a second round of funding.
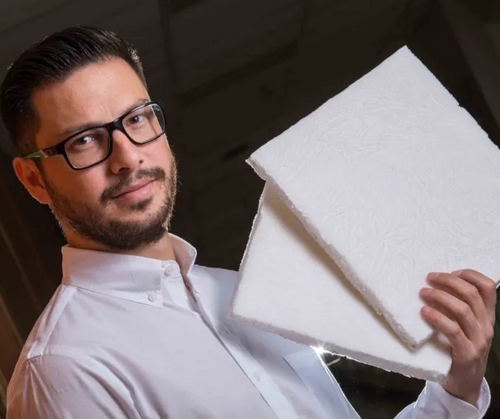
But the venture folded, and Yildirim has returned to Turkey where he is now an associate professor at Bursa Technical University and founding general manager of the university’s Technology Transfer Office.
In an email, Yildirim said tests showed that Arbolate was similar in performance to other types of insulation on the market but in the end was too expensive to manufacture competitively.
“They showed comparable results with the commercial products,” he wrote of the prototype panels he produced. “However, we couldn’t…decrease the production costs due to our one-of-a-kind manufacturing method. The cost killed everything.”
Yildirim never explained how the panels were made, other than to say they were formed with “cellulose nanofibrils” and water and sometimes corn starch. Interviewed in 2016, a year before his return to Turkey, Yildirim said the insulation panels were “easy to make” and that he was trying to patent the process.
More recently, he said he did seek a provisional patent as the University of Maine but later withdrew the application. The original grant money went for laboratory rent, equipment purchases, tests and researcher salaries, he said, but a second grant application was turned down. Before he left for Turkey, Yildirim said he donated his company’s equipment to the university.
Yildirim is no longer pursuing the research. Asked whether anyone else was carrying on his work, he said: “Not with exactly my products. But I heard that some in Maine [are] also working on development of cellulose insulation.”
Scott Gibson is a contributing writer at Green Building Advisor and Fine Homebuilding magazine.
Weekly Newsletter
Get building science and energy efficiency advice, plus special offers, in your inbox.
0 Comments
Log in or create an account to post a comment.
Sign up Log in