Basement insulation strategies

Now that I’ve got my above grade strategy worked out I’m starting to look at my basement and foundation strategy. Climate Zone 6.
I’ve listened to the excellent podcast featuring Martin here:
And read these two links as well as other articles on basement insulation:
https://www.greenbuildingadvisor.com/blogs/dept/musings/how-insulate-basement-wall
https://www.greenbuildingadvisor.com/blogs/dept/guest-blogs/basement-insulation-part-1
https://www.greenbuildingadvisor.com/blogs/dept/guest-blogs/basement-insulation-part-2
The prescriptive code IRC 2015 Table N1102.1.2 states that for climate zone 6 the basement wall shall be and R-value of 15/19. Where 15/19 mean R-15 continuous insulation on the interior or exterior of the home or R-19 cavity insulation at the interior of the basement wall. 15/19 shall be permitted to be met with R-13 cavity insulation on the interior basement wall plus R-5 continuous insulation on the interior or exterior of the home.
My insulation guy is suggesting we use a RES-Check analysis to only use a continuous blanket drape which gives about an R-11 and then put studs on top of that to hang the dry wall and not even filling the stud bays. That might pass RES-Check and inspection but I’m not sure how you go about air sealing the basement then?
I’d always thought the best way to do it would be to use rigid foam insulation like described here at GBA.
I still have a few questions regarding a rigid foam strategy.
1) You don’t want to use a polyethelene vapor barrier so the concrete has a chance to dry to the inside. However using rigid foam especially a foil faced Polyiso will prevent drying to the inside. Does it make sense to use 1″ of XPS instead and then 2×4 blown in stud cavity to allow for interior drying?
2) In going with a combined approach of rigid foam and blown in stud cavity is there a ratio rule of thumb between rigid foam and blown in insulation like in roofs and walls (51% and 36%)? It seems like there should be because of the hot moist summer air cooling on the inside of the foam and potentially causing moisture issues in the stud cavity?
3) A foundation wall it is unlikely to be very smooth or dead straight. Foam board is flat and very rigid. How difficult and costly is it to attach the foam board to the concrete wall?
4) Is air sealing the basement wall just as important as air sealing the above grade stick frame?
5) How are the portions of basement wall that are above grade insulated? If I’m planning an R-30 exterior foamed stick frame above grade and per the code the basement requires R-18 then the part of the basement wall above grade exposed to the snow and all the elements is the weak part of my design. How do people typically handle that issue?
Steve
GBA Detail Library
A collection of one thousand construction details organized by climate and house part
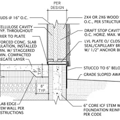
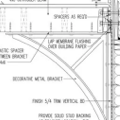
Replies
Steve, I don't recall if you are talking about a new or existing home? If existing, are the foundation walls poured concrete, or something else?
You can insulate either the interior, the exterior or both. I prefer to insulate the interior only in most cases. The best approach is to use rigid or spray foam only on the walls, but if sealed carefully with the right proportions you can add studs and fluffy insulation if you really want to. I avoid foam when I can but this is one place I think foam is best used.
I've heard Dr. Joe Lstiburek call the drape-style insulation "diapers." They perform similar functions. Neither is appropriate for basement walls.
Using similar ratios as for above-grade walls is safe. In theory it could be reduced starting about halfway down the wall, but it's easier and better to just do it all the same.
Concrete does not need to dry to the interior. It doesn't need to dry at all, as concrete is not affected by moisture, but it can move water via capillary action so it's important to have a capillary break at the mud sill level, and hopefully excellent drainage and waterproofing on the exterior.
Use Hilti IDP fasteners. Knock off any extra-high spots or carve out the foam to span them.
Unless cracked, and even then, foundation walls are airtight on their own. Extra attention will be needed at the slab and at the mudsill and rim joist area, though.
By "portions of the basement wall above grade" do you mean framed walls? If so, you can insulate them just like above-grade walls, or chose a different insulation system.
Steve,
Q. "You don't want to use a polyethylene vapor barrier so the concrete has a chance to dry to the inside."
A. No, that's not quite right. You don't want polyethylene anywhere near a stud wall in your basement, because the polyethylene can trap moisture and allow for the growth of mold. There is no need for the concrete to dry. For more information on this issue, see Joe Lstiburek Discusses Basement Insulation and Vapor Retarders.
Q. "Using rigid foam (especially a foil-faced polyiso) will prevent drying to the inside."
A. True, but you don't want to invite moisture into your basement, so preventing inward moisture movement is a good idea.
Q. "Does it make sense to use 1 inch of XPS instead and then 2x4 blown in stud cavity to allow for interior drying?"
A. In Climate Zone 6, I would advise the use of at least 2 inches of rigid foam before switching to fluffy insulation. Better yet, meet the code requirement for R-value entirely with the foam layer, and skip the fluffy insulation. Green builders don't use XPS -- instead, choose EPS or polyiso. For more information, see Choosing Rigid Foam.
Q. "In going with a combined approach of rigid foam and blown in stud cavity is there a ratio rule of thumb between rigid foam and blown in insulation like in roofs and walls (51% and 36%)?"
A. Yes. For basement walls, a conservative approach is to follow the same foam-to-fluffy ratio rules used for above-grade walls. These ratios vary depending on your climate zone.
Q. "A foundation wall it is unlikely to be very smooth or dead straight. Foam board is flat and very rigid. How difficult and costly is it to attach the foam board to the concrete wall?"
A. With a modern house, it's easy. With an old stone foundation, it's impossible. If the foundation wall is rough and uneven, you have to use closed-cell spray foam.
Q. "Is air sealing the basement wall just as important as air sealing the above-grade stick frame?"
A. Air sealing a basement is important, but a poured concrete wall is not usually leaky. Leaks are elsewhere. For more information, see Air-Sealing a Basement.
Q. "How are the portions of basement wall that are above grade insulated?"
A. If the above-grade wall is concrete or concrete blocks, the insulation is continuous and identical, whether the portion of the wall you're talking about is above grade or below grade. If the above-grade wall is framed with 2x4s or 2x6s, it is insulated just like any other framed wall.
For zone 6 you'd need at least R7.5 rigid foam for dew point control at the foam/fiber boundary on the above-grade section of the foundation wall. Going with just an inch of foam risks (performance undercutting) frost/ice in the fiber insulation at the above grade section during cold snaps.
If there is only a few inches of above grade exterior exposure and there is no capillary break between the top of the foundation and the foundation sill it's sometimes advisable to allow some drying capacity of the concrete toward the interior. One way to do that is to stop the wall foam (and sometimes the cavity insulation) about a foot from the slab. This isn't a great solution, but is called for in situations where the groundwater level is seasonally at or above the footing, or the foundation can't be adequately drained for other reasons. In extreme wet-soil cases a dimple mat between the wall foam and foundation wall is called for. With a foot or more of well drained above grade exposure on the foundation &/or an EPDM sill gasket the risk to the foundation sill is low, and the foundation doesn't need to dry toward the interior.
In a typical house the air leak the foundation sill & band joist is usually larger than all of the window & door crackage combined. The air leak at the seam where the slab meets the foundation wall can be almost as big as the foundation sill leakage in some houses (as any radon abatement pro can tell you.) Air leaks at the bottom and top of the house are far more important than at the mid-plane, since those are the leaks with the biggest stack effect driving air infiltration. Sealing leaks in the basement are generally MORE important, not merely "...just as important as air sealing the above-grade..." walls, to minimize stack effect infiltration and to minimize levels soil gases inside the house.
Thanks for the corrections on the drying. It will be a new home construction.
The reason for not just doing away with the fluffy insulation is that I have to put up stick frame to support my sheet rock so I might as well fill the cavity with fluffy stuff. Using a combined foam and fluffy stuff minimizes the impact to my interior floor space.
Is the reason for having the ratio's of rigid to fluffy insulation the same as the above grade walls the same? i.e. To ensure the surface of the concrete remains above the dew point to prevent condensation forming.
My exterior design temperature for the outside walls is 22F. I'd imagine my basement walls being insulated from the air by earth then my design point will be significantly higher than 22F so therefore it seems the ratio of fluffy to rigid insulation could be less? The problem is those parts of the foundation wall above grade before the 2x6 frame starts. I think by code the foundation wall has to extend 6" or so beyond grade. Those 6 inches are the weak spot in the foundation insulation strategy. Is it worth worrying about the 6" concrete above grade?
I'll also not have to de-rate my Polyiso so much to R-5 so maybe R-5.5 to R-6.0.
By my calculations if I use 1.5" of Polyiso de-rated to R-5.5 per inch and then use a 2X4 blown in cavity insulation in as light as possible a fill to prevent settling say about R-3.9 per inch I end up with about a 36% ratio of rigid to fluffy stuff, the same ratio as my stick framed wall above.
As all new home builders I'm trying to balance costs and I've already blown my insulation budget by a large number.
Steve
Steve,
Q. "Is the reason for having the ratios of rigid to fluffy insulation the same as the above-grade walls the same -- i.e., to ensure that the surface of the concrete remains above the dew point to prevent condensation forming?"
A. You're half right. The cold surface you are worried about -- the surface where condensation might form -- is the inner face of the rigid foam. If the foam insulation is too thin, the inner face of the foam can be cold enough to allow for condensation to form.
You are correct that the top of the concrete wall is the coldest section. When the outdoor temperature is zero, so is the top of the concrete wall, and the rigid foam on the inside of the cold concrete can also get cold -- unless the rigid foam is thick enough.
A recent project I vetted for a co-worker was an all foam solution behind 1.5" steel furring on which to hang the wallboard, which came in cheaper than a foam + 2x4 studwall w/ fluff. (That won't necessarily work for walls need electrical boxes.)
There was substantial labor savings by being able to rough-cut all of the steel furring to length in one go, letting the slop in the steel top/bottom channel-plates manage the subtle variations in wall height. Between that and the avoided additional step of installing the fluff it turned out to be lowest cost proposal, and resulted in a very even, flat finished wall. (There is not much warp or twist in steel framing.). I'm guessing that type of approach is more common in commercial construction- it was the first time I'd seen steel furring applied in a residential basement.