Condensation Problems with A-Frame and Metal Roof

Hi all,
I have an 80s built a-frame in Climate zone 7 Colorado. The existing construction is 2×10 rafters @ 24″o.c. with a standing seam metal roof. Recently, we discovered moisture damage happening on the interior ceiling paneling. Long story short, we had some mitigation guys come out and investigate and they found lots of water damage on the upper parts of the roof sheathing and rafters (see photo). The existing construction had batt insulation between rafters and a plastic vapor barrier attached to that.
There have been some conflicting theories about what caused this between roofers, contractors, and insurance adjuster: some think it was purely a condensation issue. (It looks like they planned for a ridge vent when you look at the roof from the outside, but there wasn’t a gap left in the sheathing at the ridge to allow for this, and there’s no soffit vent. The batt insulation was placed right up next to the sheathing, no baffles). Others think the metal ridge cap isn’t long enough or got damaged and wind blown rain and snow got in from the outside.
Now we have the opportunity to rebuild this and redo it correctly and I’m conflicted about what to do. I would typically lean towards closed cell spray foam and an unvented assembly – this would help us achieve proper R-value and wouldn’t have to worry about condensation – but my roofer hates spray foam and thinks it could cause issues down the road. He would prefer to create a ventilation channel on the underside of the sheathing and fill the remainder with batt insulation and create a proper ridge vent. The problem is that with the current construction there’s no way to get a soffit vent. And this wouldn’t get us to proper R-values. I could also consider adding some rigid foam on the exterior or interior? The whole roof is coming off and getting replaced.
I would love to hear what you guys would do in this scenario?
GBA Detail Library
A collection of one thousand construction details organized by climate and house part
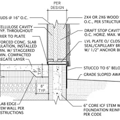
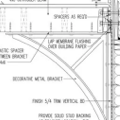
Replies
Pick one of the 5 options in this article.
I tend to avoid spray foam as it will be the most expensive option unless you scrimp on the R value below modern code requirements.
https://www.greenbuildingadvisor.com/article/five-cathedral-ceilings-that-work
Walta
Hi Walta,
Thanks for the link. I have already it in detail and understand the options, I was just curious which one others would choose in this particular scenario. I will say I haven't found a contractor yet who is willing to to attach the amount of rigid insulation on top of the roof deck we need to create that type of assembly. So that's always a challenge as well.
Ibaker222,
What will the roof replacement cost? leaving it alone and putting that money towards the insulation and air-sealing makes some of the expensive options more palatable. I would consider assembly #5 from the link Walta posted. If you want more insulation you can also fur down the rafters for extra depth.
Malcom,
#5 is definitely an option I would be interested in. Honestly the roof itself is in great shape, and it's a shame to have to replace it, but insurance will be covering it as they have to remove the standing seam roof in order to replace some of the water logged sheathing. So it's won't be coming out of our pocket. I believe insurance will be paying for the cost to replace batt insulation (since that's what was there before) and we will probably just be responsible for any upgrades beyond that cost.
ibaker222,
That's great news! See what your builder thinks of assembly #3. You avoid spray foam (I share your builders reservations) get good air-sealing, the sheathing is protected, and it doesn't need ventilation.
Thanks Malcom!
I like that idea too but it's been basically impossible for me to find anyone willing to attach 6" of rigid insulation to the roof deck. Any tips on how to convince them or methods to suggest?
ibaker222,
What about this then:
- Create an above sheathing vent channel with 2"x2"s attached through to the rafters.
- Cover this with either another layer of plywood, or horizontal strapping.
- Fur down the rafters with plywood gussets and 2"x4"s on edge to get the depth you want for insulation.
- Completely fill the rafter bays with batts or cellulose.
Do not count on insurance paying. All it takes is one bean counter to decide the damage was the result from a non-code compliant plan or faulty construction and it is claim denied up to the day the check clears the bank. No matter how you look at it denied claims equal bigger bonus check so they are motivated. I hope the claim goes thru but you need a plan for that possibility.
The commercial roofer do thick foam every day but they generally work on the flat and charge higher rates.
Walta
Another option is to attach what amounts to a second set of rafters over the roof sheathing to then fill with batts (i.e. fur up). Leave some vent space, a roof WRB, then cross strap for metal roof. I would still hit interior to exterior R requirements as you would with foam, and I would also tape the sheathing for air tightness.
I've done the foam over roof. I'm not sure I would try to talk someone into it that wasn't already excited about it. It's totally doable but has challenges and frankly cutting foam is no fun. If you don't have any valleys, hips, etc. it's a lot easier.
On second thought, with 2x10 existing, that's a lot of exterior insulation (whether foam or not) for CZ 7. I would likely build down.
I'd also consider foam on the interior as a decent option, but I've never done it so maybe it's grass is greener type of thing. It's a sound assembly though and the extra details are all interior.
If I were to do it, I think I would put enough foam on top for the climate zone to counter the fluffy stuff in the rafter bays. One would think this is much less than 6 inches
Whatever is required to mount the roof system on top of the foam[strapping? plywood?]
It somehow offends me to but more wood on anything than is required for structure.
A well detailed drawing of 'this is what we are doing' has the best potential for eliminating unwanted conversation[with contractors]
In CZ 7 you need 61% exterior-R to total-R ratio. With R-30 in the 2x10 cavity (which might be an underestimate) that's about R-47 exterior. Using R-6 per inch for foam, that's over 7.5 inches.
I forget the number people like to use for polyiso R per inch due to cold weather derating (for condensation control calculation purposes) but I don't think it's over 6 and may even be under.
But you don't need r77 no?
https://www.greenbuildingadvisor.com/article/the-ratio-rule-for-hybrid-roof-insulation
yeah, still a fair bit............
No you don't need R 77 and that wasn't my point. You would have to reduce the cavity R and find a way to suspend the reduced size batts to be tight against the underside of thr sheathing.
The ratios in your link are the same as I said: 61%
FYI - the most recent code version IRC 2021 calls for R30 rigid and R60 total in zone 7, so 50%. Table R806.5
Alternatively, you can follow the Section R806.5.1.4 and calculate the amount of rigid for your specific location, based on your local temperatures. It's not complicated math but you need to know the monthly average air temperature for the 3 coldest months of the year (Tcold in the calculation below).
By my calculation, if you have 50% rigid insulation then you're good for an average coldest air temperature of 22 degrees. If your average coldest air temperature is higher than that you can go with less than 50% and meet code.
Tcold + [(68-Tcold) * (Rrigid / Rtotal)] >= 45 degrees
This calculation ensures that the temperature at the inner face of the rigid insulation stays above 45 degrees. The Code idea is that the indoor humidity level is reasonably low and won't condense at 45 degrees.
I'll have to revisit this when I can get in front of a computer, but I think you may be misinterpreting something if you are thinking the new 2021 code allows only 50% exterior R to total R for clinate zone 7, based on the table alone.
OK, I'm not positive, but what I think might be going on is that you are using R-60 and then saying 30/60=.5 (50%). But the code isn't calling for R-60, it's calling for U-0.024.
Does that make sense?
I'm not sure why it would go from 61% in the 2018 version to 50% unless there was some new data...