Condensation With A-Frame Metal Roof

Brand new metal roof causes condensation and mold growth on the entire interior roofline. About a year ago we replaced the roof on our 1975 A-frame house from shaker shingle to metal standing seam with a high temp ice and water shield under laminate (I don’t know the brand). The new vapor-impermeable roof caused moisture to build up inside. In addition, the metal changed the temperature of the interior roofline causing condensation build up and mold to grow all along the interior roof during winter. After a year of research, I have concluded that the roof needs to be removed, poly iso board insulation (total of 3″ thick consisting of two layers =R20), and OSB decking with additional ice and water shield under laminate need to be put down and new metal back on. However, I am still left with a few questions. Notes on the house: It is located in Bentonville Arkansas. The roof consists only of 2″ thick tongue and groove. No attic, no air gap, just wood. The metal roof is Horizon Loc by Metal Central 1) Is this the correct solution in addition to reducing interior moisture? 2) Is an air gap necessary directly below the metal roof for efficiency gains? 3) Will we smell the second layer of under laminate (that is below the metal but on top of insulation and OSB) in the summer? The current smell in the summer from the metal roof heating the under laminate is horrendous inside. 4) how much more efficient is a light-colored roof than a darker (charcoal grey) roof? I can’t find a straight answer to this. Thanks for your help!! This has been an emotional challenge for sure.
GBA Detail Library
A collection of one thousand construction details organized by climate and house part
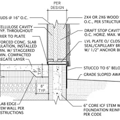
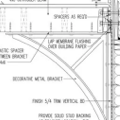
Replies
Cavallaro,
You need to tell us where you are and humidity conditions in general before anyone can answer what is potentially needed. It would helpful to know what roof underlayment was used, too.
Hi Onslow, thanks for your input, I've updated the post. Unfortunately, I don't know the brand of the under laminate, and the house is in northwest Arkansas (Bentonville).
The roof as it was built was guaranteed to fail, the vapor barrier (which the I&W is) over the T&G is a bad idea. I'm not surprised you had winter time condensation and mold issues.
The solution with exterior rigid insulation you are looking at is the right way to go. You are in warmer climate so the R20 is not a bad start from energy efficiency, not great but you don't have that many HDD there. No foam will actually be R6.6 in the long run, LTRR of most polyiso is around R5.6, so 4" to 5" of rigid is a better target. Compared to all the work you need to do, it doesn't add that much extra cost but you get a better roof out of it.
The important part for you is that much rigid insulation above the roof deck, it is enough to warm the outside of T&G enough to prevent condensation in the winter time. As a bonus it should also reduce the temperature of the existing I&W in the summer so it should smell less.
For the new roof, you don't need any I&W layer. Your roof is steep enough that the I&W is adding only cost. A regular synthetic underlayment (I prefer a permeable one) over the new OSB deck will work just fine.
Venting gap is something you need only in places with extreme snow, in your climate it is not worth the extra cost.
Generally lighter colors are better but roof color doesn't necessarily track with SRI (solar reflectance index). Your roofing supplier should be able to provide the SRI for each panel color to compare. For most roofs, once you are insulated, the heat gain from the panels matters much less so a high SRI won't make all that much difference. For winter time you actually want the opposite, a lower SRI to increase solar gain. SRI is not something I would not loose too much sleep over.
P.S. That is a fantastic looking place.
P.S.S Some I&W would still be a good idea each side of those valleys.
Thanks for your response! This is very helpful. At the risk of repeating from the conversation below, I would certainly appreciate your perspective. I did an analysis of diminishing returns and found that the efficiency gains are very incremental after R20ish and there will be hardly any additional energy cost savings. (See attached graph). Note- I was unsure of my region's exact HDD so I analyzed using 3500 and 5400 as I have seen both for Bentonville AR. The insulation cost estimate is also attached. To get closer to the code would be an additional $4K. Since the metal roof was $34K and just adding R20 insulation will be an additional $37K I thought that the marginal efficiency gains don't justify spending an extra $4K. My analysis indicates we very likely wouldn't see a return on investment in energy savings if we increase thickness. I also justified that the saved $4K could be used to put a vapor barrier in the crawl space further helping the interior mold issue. I also wonder about the code for roof insulation as my assumption is that it's written for houses with attic spaces, which get hotter than the ambient temp in the summer which is slightly different construction than my house. Your thoughts on this would be much appreciated. Would you spend the extra $4K for R30 ish if you didn't see significant efficiency gains or energy cost savings? Do you see any flaws in my analysis or thought process?
Thanks for the info on LTTR I did not realize insulation properties diminish over time. I’m glad to hear that color is relatively negligible as well. I thought using a synthetic under laminate would be an option but the roofer said not a good idea. Left a little baffled by that.
Thanks again, can't express enough gratitude for your input.
Diminishing returns from increasing insulation
https://www.greenbuildingadvisor.com/article/the-diminishing-returns-of-adding-insulation
How many sqft is your roof? Around me 2" polyiso is about $1/sqft, so $4k buys a lot of iso. Maybe they are quoting box store polyiso which is about 2x roofing polyiso.
Installation of two layers of iso is about the same labor no matter the thickness, maybe a couple of dollars more for the longer screws. You do generally hit diminishing returns above R20 to R30 in most climates especially when using rigid insulation. In most cases, even code min has no ROI.
Lot of metal roofing can be installed over strapping, you might be able to save a bit of cost if the sub uses 1x4 or 2x4 on flat horizontal strapping instead of a new 2nd roof deck. The side benefit of strapping is you can use it as an almost built in ladder during install but that might not be possible on such a steep roof. In case of strapping, the underlayment would go directly over the rigid.
Roofers like peel and stick because is looks more impressive and costs more. If not needed, I would not add it. No need for the extra cost plus it is impossible to remove without also replacing the roof deck if the roof ever needs to be repaired.
First of all, I just want to say that that is a beautifully unique home! What is your location? I ask because if you are going to go through all the trouble, you might as well at least get the code-minimum amount of insulation on your roof (if not more.) If I'm undrstanding you correctly, there are no roof rafters enclosed under the finished ceiling, and so there is no cavity insulation. The entirety of the roof structure is what is shown in the interior photo and there is zero insulation in/on this roof. I became acquainted with a home like this several years ago but it wasn't an A-frame. I called it a "deck house." The owners had a new metal roof installed with rigid foam insulation just as you propose, but I'm unsure if they included a ventilation channel or if one would be necessary. What does the roofing manufacturer have to say on the topic of ventilation? If the manufacturer says that ventilation is required, then it would definitely be required for warranty purposes as well as to follow the code (code requires materials to be installed as per manufacturer instructions.) I believe that code also requires all roofs to be vented, but that may have changed. There were some condensation stains on the ceiling of that deck house, but I believe they were old and occurred before the insulation was installed; it was completely dry when I saw it in the winter and there was no evidence of mold. I'm assuming that you're keeping the existing membrane. It is providing an air barrier where there was no air barrier before, plus it would probably be near impossible to remove. The odor that is currently happening when the roof gets hot may be reduced or potentially eliminated once the insulation is installed because the existing membrane will not get as hot even if the metal roof is extremely hot. The more you can isolate that existing membrane from the hot roof, the less likely you will experience the odor on a hot day, which may be another incentive to add as much insulation as you can manage. The second membrane may not be as odoriforous because the reason you may be smelling the first layer is because the underside of the membrane is releasing VOC's when it gets hot, and then the VOC's are seeping right through the cracks between the deck boards and into the house. If that is the case, the second layer may also release VOC's, but those VOC's may not have a direct route into the house as it will not be in contact with any "holes" that are connected to the interior, as is the case with the first layer. Finally, the real reason I responded to your post (other than commenting on your lovely home:) Is that a Tree-of-Heaven (Ailanthus altissima) in your planter box? If so, please destroy it right away. If it is growing into the ground below the box, it will be difficult to kill without herbicide. If you cut them down, they just send up a bunch of root suckers.
Edit: The effects of roof color may be greatly exaggerated when there is sufficient insulation. And Bentonville, AR appears to be in Climate Zone 4. Here's the map:
https://www.greenbuildingadvisor.com/article/updated-climate-zone-maps-reflect-warming-trend
I'm not sure what code your area has adopted (if any,) but the 2021 code minimum is R60. The previous code minimum was R49. That is for new construction. Older homes are normally not required to upgrade to code minimum, but it's not a bad idea, especially since it will be near impossible to add more at a later date. You should save on your energy bills too; you may even find that your HVAC equipment is grossly oversized after the improvments. And your home will be more resilient in case of a power outage. Those are the silver linings to this unfortunate situation.
https://basc.pnnl.gov/information/2009-2021-iecc-and-irc-minimum-insulation-requirements-new-homes
Thanks so much for your response and all the information! Thank you so much for your response and all the helpful insight. I do love this home and it's the most unique I've ever been in. Although has required a lot more out of me than I could have imagined.
I considered going to code (R38 now updated to R60) however, I did an analysis of diminishing returns and found that the efficiency gains are very incremental after R20ish and there will be hardly any additional energy cost savings. (See attached graph). Note- I was unsure of my region's exact HDD so I analyzed using 3500 and 5400 as I have seen both for Bentonville AR. The insulation cost estimate is also attached. To get closer to the code would be an additional $4K. Since the metal roof was $34K and just adding R20 insulation will be an additional $37K I thought that the marginal efficiency gains don't justify spending an extra $4K. My analysis indicates we very likely wouldn't see a return on investment in energy savings if we get to code. I also justified that the saved $4K could be used to put a vapor barrier in the crawl space further helping the interior mold issue. I also wonder about the code for roof insulation as my assumption is that it's written for houses with attic spaces, which get hotter than the ambient temp in the summer which is slightly different than my “deck house”. Your thoughts on this would be much appreciated. Would you spend the extra $4K for R30 ish if you didn't see significant efficiency gains or energy cost savings?
You are correct, we will be keeping the existing membrane, it couldn't come off if we wanted it to and I don't think it will get hot enough for us to notice the off-gassing with the new insulation. The second layer of under laminate will get hot but I’m under the assumption that it will not seep directly through poly iso insulation and since the seams of the two layers of poly iso are staggered, it will have an even harder time. Further and oddly enough those gasses won't get through the first ice and water shield as it has a plastic vapor barrier membrane.
Im glad to hear the effects of roof color are exaggerated, although surprised. You corroborated Akos’s perspective too. Regarding the tree of heaven. Thanks so much for pointing that out. I was wildly wrong thinking it was native to this region (as I am fairly new to the area). I couldn't believe how fast it grew in just a few months. I will certainly be taking care of that!
https://www.greenbuildingadvisor.com/article/the-diminishing-returns-of-adding-insulation
Cavallaro,
You spoke of mold "all along the interior roof during winter". Since a major part of your wall/ceiling IS the roof, did you mean the mold was showing at the intersect of your vertical end walls and roof/ceiling? I ask because your exterior photograph looks like the tongue and groove deck boards extend past framing to create the overhang. The gaps between decking boards provide air exchange with the outside under this condition. The Deck Houses mentioned by adrienne_in_nj also shared this feature, which in some cases caused staining at the transition point. Interior moisture meets cold air here.
You may also be suffering from moisture being trapped by the loss of evaporative capacity through the wood shingled roof. The original roofing paper would have been more vapor open by far than the new ice and water shield. The stink you have encountered may also have been exacerbated due to not using the high temperature version for use under metal roofs. Be sure that the new roofing membrane is rated for under metal roofing.
Your heat calculations are a bit hard to interpret without window areas, wall areas and R values. I would tend to look more at the cooling loads in your case. You may find that a 150F roof surface will warrant the extra insulation, especially with increasing summer heat. You must definitely control the ground moisture in your crawl space. Hopefully your heating system is not coupled with it.
A side shout out to adrienne_in_nj if I may. The other thread is quiet and I wanted to let her know the product she asked about was Quadlock's retrofit system. The one sided lock bars grab the insulating panels such that you can screw them to the wall be insulated then cover the screws. Siding gets screwed to the outboard "finger" just like you would with normal ICF. I do not know if they still offer the system.
Onslow
The mold is only on the tongue and grove, not any walls. It is also not at the joint between the wall and roof where the overhang is created. I suspect lots of is exchanged through this joint, but it is no evidence as you mentioned in your example. I thought long and hard about how to address that air exchange.
I know I am also suffering from moisture being trapped with the new roof, so I installed bathroom fans and have a dehumidifier running all winter. However, that portable dehumidifier is not a long-term solution. I actually don't know what the long-term solution is other than an ERV or HRV (which is not feasible at the moment) and vapor barrier in the crawlspace.
Regarding the smell, they did use a high temp ice and water shield, but even that will heat up and off gas it seems.
Can you explain the need for including window areas, wall areas, and R values when calculating the benefit of adding insulation to the roof? I know they are important, but can't we make a pretty good calculation of the decrease in heat transfer through the roof without those values? Seems to be making it impossibly complicated to determine the most beneficial roof insulation thickness for the dollar. I can figure out these values but would have no idea how to include this in the roof insulation analysis and the impact on the roof R-value.
What does it mean when you say “hopefully your heating system is not coupled with it”?
On that note, does anyone know a professional that can help me figure out the necessary R-value to stop the interior roof from reaching the due point and the most efficient R-value for the buck? Expert advice backed by analysis would really help me, my wife and baby sleep at night.
Cavallaro,
This may get long winded, but I will try to explain why I have asked certain questions.
The pictures of the mold makes me think about biofilms. Human activity in homes eventually creates a film of food greases, soap, smoke and other goo which builds up on surfaces. Try looking on top of your refrigerator, or kitchen cabinets if they stop short of the ceiling. I have scrubbed many a kitchen for re-hab and the levels can be quite appalling. My suspicion is that the mold has appeared along the board seams and knots because that is historically where the airborne goo collected on their way out. The process is quite similar to the synthetic airborne goo now used to air seal the myriad fine gaps revealed after first blower door tests. The current loss of air flow at the moldy locations thanks to the new I&W shield has tipped conditions to favor mold growth.
I would chance a wager that more of the mold appears as you get closer to the kitchen or bathrooms. One thing in your favor is not seeing a corresponding build up at the roof/wall intersect. Maybe the original builder put sealant along the deck board seams as they went up. A smoke test would settle the question, but later on that. Meantime, a bit of scrubbing with non scratch pads and ordinary food cleaners followed with a light wash of a disinfectant cleaner should knock down the mold. Do not use Lysol, the finish won't take it. No Clorox. Test any choices on a place you don't stare at a lot. If the mold has had time to degrade the finish, scrubbing may leave lighter spots. Touch up will be a bear. Test first. I find that food washes are the gentlest starting point. Murphy's Oil Soap will lift very aggressively. I ruined some bent wood chairs with it.
I am just guessing that you have a forced air heating system. Your very open concept home design infers that the furnace resides in a small utility closet on the first floor or in the crawlspace. If your furnace/air handler is in the crawl there is good reason to think you are picking up crawl space moisture when the system runs. This will make your dehumidifying more difficult as the system is likely entraining humid air from below on a constant basis. You have already perceived the need to put a barrier in the crawl space, so I will guess you also perceive it as damp-ish. If it is an unconditioned/vented crawl space you will also be gaining humidity from outside air. You will have difficulty with controlling air conditioning for the same reasons.
As for heating and cooling load calculations, you can't do either properly without knowing total surface areas involved and their corresponding R values. You will also need to rank your roof surfaces for sun exposure to ensure adequate analysis of your cooling needs. I think it is safe to say some face north. Remember, the metal roof in full sun will get quite hot compared to the original (cedar?) shake shingle. Higher R value in the roof will help keep your cooling needs down by reducing heat influx from the much more full and direct sun energy. This is why people put solar panels on roofs not side walls.
The vertical walls and windows losses need to be calculated in to know true heat or cooling demand. You must also include your 1st floor area if it is insulated from an unconditioned crawl space. Heat goes to cold regardless of what surface it is. Without knowing the total load from all surfaces you will possibly find the furnace capacity too large after the new roof insulation. Same for the AC unless you are struggling to keep cool now. Mis-sized systems will short cycle. This is more an issue with AC since the short cycling will affect your dehumidifying capacity. You don't want to run an independent dehumidifier with AC as floor dehumidifiers put out warm air into your living space. If you can't find any info on the windows you can guess R3 for double pane.
I know it is tempting to focus on the one main energy hole in your envelope, but until you know the full energy needs as they are now you won't be able to judge the effects on your heat and AC. The risk is trading one problem for another. Take the time to measure carefully and define the various surface areas and window sizes. Apologies if the following is rather obvious, but I am not seeing your work numbers other than the cost of installation. As you likely know, the heat loss formula for btu/hr is - Area x U x delta T. Remember how hot full sun on the roof can get, it will mean bigger delta T in summer than just ambient to interior. Ambient air in winter for the same areas is okay.
The Bentonville weather station info I see says Carroll County 99% heat is 15F and 1% cooling is 93F. Ratio of HDD to CDD is 1. I would still suggest that you will be better served to build for cooling loads as things are not trending down.
Hi Onslow,
Thanks for the information. I think what you are getting at is that if I over-insulate my roof, I will lose the heat by some other means (walls, windows, floor) and it could lead to other issues such as an over-capacity HVAC system. However, is that likely a significant issue if I'm debating between R 20 and R 30 on the roof? Knowing the total heating load seems like it wouldn't matter until we are upgrading our HVAC. I just cant see how heating load and determining R20 or R 30 are related. Being that the roof is a substantial part of the walls, seems that more insulation will have even further benefit. The HVAC system is about 11 years old, so the concern of diminishing its life span seems a bit unnecessary to worry about. although i do understand that it may cause short cycles. However currently the HVAC is running all winter and all summer, so seems that it might not be undersized even with the additional roofing insulation.
Cavallaro,
After doing a WAG on surface areas based on your photo, I can assure you that you are in no danger of having an undersized HVAC system whichever insulation level you choose.
Since I can only guess if the house is cross shaped based on the interior photo, I set the basic peak height at 20', base of triangle at 18' and adjusted roof area for the overhang which appears to be 18". So best guess is about 2500 sf of roof to cover and 2260 sf that are thermally relevant. The vertical wall area is approx. 180 sf per triangle and thus I have used 720 sf as a serviceable number. I can't imagine the vertical walls are well insulated if the roof was bare, but I granted an R-12 average with windows. Probably generous. The roof temperatures will range from near to ambient in shade to 165 -75 in full sun. I arbitrarily set an average of 135F for all to account for shadowed surfaces.
Using 70F as the indoor temp, the delta T for roof surface to inside is 65 during summer. Using the 93F 1% value for vertical wall area the delta T is 23.
Update of values coming
Wall area R-12 1,380 Double this number if only R-6 due to no insulation in walls.
For winter 99% design value the delta T for roof to interior drops to 55 but wall delta T goes up to the same 55.
Update of values coming
No estimate of loss through floor because I don't know what is under it. I do note that you have wedge shaped areas like the one behind the sofa. Do these areas currently get very hot or cold? Have you encountered the mold in these areas? If these areas are isolated from the general air flow you might want to add vents.
Mind you these numbers are WAGs without true dimensions. Still, you can see the sharp drop with R20 will be good, but even better with R-30. As I noted before, the summer load is higher though not as bad as I had in mind. If your heat/AC is currently running all the time, you might need to review your ACH rate. The duct work is another place to look and see if you are warming your crawl space instead of your home. If the furnace is rated at more than 60,000 you will have a lot of short cycling post insulating. If it is more like 40,000 then selecting a lower blower speed might help both for heat and for AC. The air simply has to be moved over the coil long enough to strip out the humidity. Short cycling will mess with that. If you do go R-30, you will have a great shot at using an ASHP very effectively. That may only be 8-10 years in your future even with your newish, but still lower efficiency system.
I think the R-60 suggestion is a mis-reading of EnergyStar recommendation. I believe it is a suggestion to use R-38 to R-60 in zones 5-8 not a hard rule. If you do go ahead with removing the metal roof and placing strapping over the foam, please consider setting the strapping on an angle to encourage draining of morning condensation under the panels. I think it was Matt Risinger who uses this trick in humid Texas. Not sure about Arkansas, but you can judge.
Hi Onslow
Sorry for the delayed response and thank you so much for your analysis! You got really close on the dimensions for having no measurements! The roof is 2219 sf and the walls are 250 sf. The walls are insulated, and I believe R 12 would be a close estimate, with no insulation in the floor/ crawlspace. The values provided are really helpful and give me more confidence that R30 is not a waste of money. That there will be enough efficiency gains to recoup the investment (although over a 10 + year time span)
We are losing heat in the crawl space and I've done some work to solve that but it requires me to take off the ducting insulation to get to all the joints to seal them. Unfortunately, we don't have a variable speed HVAC fan, so reducing short cycle that way isn't possible. My HVAC is rated at 36,000 BTU so by your logic, we are not too far off and we might not have much trouble with short cycling.
We won't be using any strapping as it has been told to me by a number of people that its not necessary. They say it won't hurt but won't really provide any benefit as the ice and water shield under laminate will catch any condensation under the metal and that the efficiency gains are not justifiable. Eventually, ASHP is ideal, as the temperature difference between rooms right now can be up to 20deg which. So having individual controls in each room would be ideal in conjunction with the significant efficiency gains over our current unit.
There is one last issue I am trying to double-check before giving the roofers the final go-ahead. Which is does this insulation (say R20) ensure the interior roofline doesn't reach dew point at the worst-case scenario of 70% interior humidity, 25 deg outside, and 70deg inside? Do you have a quick way of determining the internal roof surface temp? I've done the math but am not confident in my answer.
Cavallaro,
New post tomorrow. Will explain.
Cavallaro,
Well, my 5th grade math teacher's ghost rose up last night and scolded me quite sharply about checking my work. I am very shamed.
In my haste I wrote down the R value of 2" of pine and then merrily doubled it when I came back to the computer said to myself, "two times the R" for the decking. So, I managed to not only double your existing R value for the roof, but I then proceeded to not add back my bad value or the true existing R value to the add-on insulation. I had become too focused on just the added insulation effects.
Very poor of me to present incorrect figures. My apologies and I hope you will still see that the net corrected results still show value in insulation. Keeping in mind that the losses presented are for maximum design points, you can see why your furnace has been busy trying to keep up. Your saving grace in summer has likely been a large fraction of roof area being in shade and formerly having wood shingles.
For simplicity, and to not get myself off track again, I am using the same area as before.
Using 70F as the indoor temp, and the prior 65 Delta T for summer loads your current roof is probably cooking you much harder.
Roof with corrected R-3 and 2260 sf active area would be 48,917 btu/hr
Roof with corrected R-23 and 2260 sf active area would be 6,390 btu/hr
Roof with corrected R-33 and 2260 sf active area would be 4451 btu/hr
This does make the case for R-20 making the summer reduction quite massive. A bit less convincing to go for R30. Code may say otherwise.
Roof with corrected R-3 & 2260 sf and 55 Delta T for winter loads, the losses double as well for current situation.
Roof at R-3 loses 41,392 btu/hr
Roof at R-23 loses 5,407 btu/hr
Roof at R-33 loses 3,737 btu/hr
Floor losses - unknown
Again, these numbers strongly suggest R-20 would make a world of difference to your comfort levels and also that taking care of the cold floor would be worth considering.
Condensation-wise, the question you posed is a bit trickier than my now obviously inept figuring can safely answer. Standard dew point charts indicate that 70F air at 70% humidity will form condensation at 60F. The key question being where in the wall or roof build-up does 60F occur. Hopefully, you would never encounter these conditions outside the bathroom after a long hot shower.
Your windows would certainly be drenched everywhere. The wall sheathing would also be at risk as you have no exterior insulation and presumably batt insulation in the walls. Your roof does not have a homogeneous insulation profile and the calculations for deriving actual point-by-point temperature profiles through dissimilar materials requires a level of math that would make my 5th grade teacher's ghost cackle with glee to watch.
A typical wall profile with the same R-20/R-3 insulation ratio would be considered quite safe. However, given my poor demonstration in a prior post, I am not going to make any claims. Perhaps someone with proper math skills can give you definitive assurance.
How long a condensation risk period lasts and the drying conditions present also need to be figured in. Arkansas doesn't strike me as a land of long winters, but I have never been there. Something else to consider is local code and long term sales value of anything you do now. Re-roofing often slips by new code directives. Perhaps the new insulation being added will draw attention. If so, then you may find that R-30 is the least they will allow.
A Design Temperature Exemption Request might be feasible since you will be jumping up so much better than existing. While very few people buy energy efficiency, your resale value could be better if you can show good heating/cooling costs. A long gamble to be sure, but meantime you will be more comfortable.
I am not sure how you are getting 250 sf on walls, but then I can't see the whole house. Hope the update is taken in the spirit of guidance not gospel. The hidden pockets behind the living room walls still concern me. There are many questions unanswered about possible moisture issues. You really would do well to seek out local sources doing energy reviews and or energy efficient designs. Nothing beats on site people over voices on the internet.
Hi Onslow,
hahaha, your 5th-grade teacher sounds like he made quite the impression on you if his ghost is still arriving in your sleep! Thanks for catching your mistake and recalculating! This further confirms my understanding of the benefits we will gain with the differing R values. I do intend to insulate the floors or the crawl space at some point, but that is at least a year off. I have my confusion as to the best method/ insulation to use (that's for another post). As far as the condensation parameters, these are the worst case if I'm not running a dehumidifier and my wife is taking all the hot showers one could possibly enjoy, as well as not having the crawlspace vapor barrier. Currently, we do have a lot of condensation on the windows (1975 house) not all double pane are in the best shape and some are single pane. I digress.
Ps the 250 SF wall came from solid modeling my house knowing the house width (24.1ft) and the roof height (21ft).
I would love to consult with an energy review, however, my search for that expertise in the area has been unfruitful. I will likely revisit this after I solve the mold issue/ add insulation to the roof. There will still be many opportunities to improve efficiency. Thanks again for all your help! I sincerely appreciate it.