Another garage conversion in the Northwest

Hello all. I am in the process of planning my garage conversion. I haven’t used it as a garage for years, and since I finally got my crawl space finished, heating and plumbing systems fininished, it is time to tackle the garage conversion.
FYI, garage space is about 460 sq ft.
I have a couple of questions about how to accomplish this.
1) My garage does not have a stem wall around the perimeter. The garage walls are finished with insulation and drywall. When laying the floor insulation, do I just but it upto the drywall on the existing wall? Even with 5” of foam? See below.
2)I believe I will need to take the drywall off the walls and add furing strips to make the wall a 2×6 (currently 2×4) and insulate.
3) I plan on raising the garage floor to be equal with the house floor about 6 and 3/4” above. My thoughts were to put a vapor barrier down, add about 5” of foam board, then two 1/2” sheets of plywood in a floating floor configuration.
4) Given the space, I would like to run my HVAC ducts in that space. I was thinking two runs of wall duct (3.25” x 10.5”) from main trunk line in crawl space (furnace and duct system already designed for added load) would work. With 5” of foam board, and the duct space, this would leave only 1.75” of space under the duct for insulation. Is this sufficient?
5) How big of an issue is the duct contacting the uninsulated part of the foundation for a little bit? The delta between the crawl space ceiling and the garage floor means the ducts enter really tight to the floor.
6) The HVAC installers used 6” round to the crawl space wall (from the main trunk) then converted to 6” oval. Going to wall duct should flow more for the long run to then end of the garage, but is it overkill?
Thanks for any and all help. I have read most of the guides, but I think this situation is a little unique.
I have a bunch of pictures for your viewing pleasure.
Thanks!
GBA Detail Library
A collection of one thousand construction details organized by climate and house part
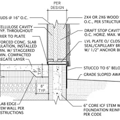
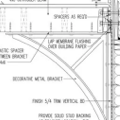
Replies
Hey David, I don't really have much for you on the ducting as it's not my area of expertise, but I have converted a couple garages here in Seattle. In fact I'm sitting here writing this in one right now.
One of the things you didn't mention is how you plan to level the floor. Garages are almost always pitched so that wet cars will have their water run off toward the garage door. I've accounted for this by cutting sleepers (a fancy name for 2x6s that lie on the ground) to match the pitch. I then put the rigid foam insulation in between the sleepers. This method does create a thermal transfer opportunity through the wood, but in my experience it's not been too substantial. The benefit besides a flat and level floor is that you don't have to worry about the compression of the foam if you go with something like big box store EPS.
-Andy
Hi David,
I'm not sure why do you think you will need to take the drywall down and extend the depth of the wall cavities? To meet a certain R-value with cavity insulation? If you don't go that route, I would consider cutting the drywall back and installing your foam tight to the wall framing.
I know one architect who regularly specs floating floors just as you have described. As you know it is important to get the right density foam and, like Andy said, make sure the floor is level. Even if it isn't pitched, low or high spots could effect your installation.
I'm sure some of our mechanical experts will be along soon to help with the HVAC questions.
Thanks for the reminder of the floor level. It seems my garage was blessed with a flat floor.
Any other opinions with putting the insulation right next to the drywall or how to beat put the ducts in the floor?
Don’t let the duct contact the concrete anywhere. You’re likely to rot out the duct doing that, even without any excess moisture. If you have 1.75” of space between the duct and the concrete, put rigid foam in there to both help insulate the duct and keep it from contacting the concrete floor. You can fit around R9-11 or so with 1.5”-1.75” of polyiso, which should be fine. Try to keep the long parts of the duct runs away from exterior walls as much as you can to minimize any heat loss if you’re concerned about limited insulation in the floor.
If the duct is only contacting the foundation wall where it penetrates into a basement or crawl space, just put something between the duct and the masonry to protect it. Any of the common vapor barrier materials should work fine. I’ve seen ducts rot out too many times to ever leave them in contact with masonry.
If you can fit the rectangular duct I’d do that instead of using round duct. You’ll have more compact transitions to registers, and you can always reduce the flow with dampers if needed. Make sure you have dampers on the ducts where they branch off of the main run. You might need some turning vanes in there too depending on the system design, but you might be able to just rebalance dampers to get the flow you need.
Bill
Bill,
I will be sealing the garage with left over vapor barrier, and will include the areas near the duct work to keep the contact points to a minimum. I am going to try and use the wall duct with some insulation below it. The floating plywood floor will contact the wall duct (floor duct now?) but I don’t see that as an issue.
Getting the insulation I need and the included plywood puts the flooring costs close to 1k, so I might rethink the usage of sleepers. I don’t want to because of the ducts and some plumbing stuff I might run, but I need to look at the costs.
Does anyone have any good reference as to how to flash / configure the garage door intrance to minimize water leakage?
Also, it sounds like no issues leaving the drywall how it is near the ground and just building the floor up work 5.5 inches of insulation?
I will post some pictures of the door frame tomorrow for reference.
David,
A couple of points:
1. You need a continuous air barrier and a continuous insulating layer around the entire building. One reason to consider removing the drywall at the bottom of the wall is to make sure that you don't have hidden air leakage pathways at the bottom of the wall. Ideally, you will install horizontal 2x4 blocking between the studs, level with the top of your new rigid foam, with the blocking installed in an airtight manner. This makes it easier to ensure air barrier continuity at this critical location.
2. To design your duct system, you will need (a) to do a heating and cooling load calculation, and (b) to design your ducts to meet the airflow requirements of your HVAC system. For more information on these issues, see:
"Who Can Perform My Load Calculations?"
"All About Furnaces and Duct Systems"
Jeez, it has been two years and I am finally getting around this effort. Reading through this, it seems best to pull off the drywall from the bottom so that the insulation can be tight to the framing. This gets more of an issue in that the garage was wired with outlets about 4 to 5 feet up, and redoing the outlets to put them more towards the ground, requires additional drywall work. Add to that my 2x4 framing making it likely I will need to increase cavity depth to meet insulation requirements (residing out of the question right now) coupled with my spouses want to make the ceiling more open (cathedral) is getting darn close to just rebuilding the garage / or tearing it down a lot more.
I think I need to save up and do all of this right, or rather figure out the end state of what all needs to be changed.
So, with all of this, I am going to focus on removing the 2 car garage door and replacing it with an exterior wall (no windows / no doors) for the short term, while we finalize overall plans for the space.
Off to go look up details for an exterior wall.
Thanks (even if late)
One issue I could use help with is the flashing to use. We are going to replace the garage door with an exterior wall. I am going to build it with 2x6 studs (for insulation purposes) and side it with T1-11 or something like that. The goal will be that once the final garage configuration is finished, money is saved up, we will reside the walls (existing walls too) and add / replace windows with higher quality and then add exterior insulation as well.
So, for now I could use some guidance on how to flash this. I am going to replace the white 2x4 that is shown with a 2x6 wall, and the T1-11 on the outside, but is there a special type of flashing I should use? The studs will be flush / maybe stick out a little bit from the concrete pad, but the T1-11 will stick out.
The picture "Flashing_help" should help clarify the issue.
Thanks,