Best practice for retrofitting insulation in a daylight basement

Hi all,
I’ve read quite a number of great articles here and on FHB about insulating basements. However, it seems most of the articles are targeting full height basements.
I have a project that differs a bit in that it is a daylight basement with a transition from concrete foundation to conventional 2×6 stud wall. I’d love to get some advice on whether folks here think my plan is reasonable and what the best practice might be. Additionally, it seems like there is some detail around the transition that might be hard to manage.
Previous system:
Wall:
42″ high concrete wall with drywall firred off the concrete. No insulation
51″ stud wall on top of the concrete foundation (2×6, fb batts), all above grade
Proposed modifications:
Install 1″ foil-faced polyiso, ideally glued and sealed to the concrete foundation wall to a height of 42′
Interior non-load bearing 2×4 stud wall 24″ o.c., filled with 3.25″ mineral wool batts to the ceiling (R value overkill but whatever)
No interior vapor barrier (climate zone 5b, Colorado) at the drywall to avoid the vapor barrier sandwich (but a vb would be good above grade)
Wall will be finished with corrugated metal wainscot below grade (to 42″) and drywall above
While I’d love to do exterior excavation and apply XPS outside the building shell, the excavation costs appear to be formidable.
Some questions arise:
1. Can I get away without the vapor barrier at the interior wall? There will not be the typical vapor retarder of latex paint below 42″ since the finished surface is corrugated metal. I suspect this is not a great idea.
2. Can I install a vapor barrier behind the corrugated metal panel? I suspect that is also not a great idea as I would be creating a vapor barrier sandwich (also not desirable: see below).
3. Can I put metal directly over polyiso? I suspect not because the letter of the code would not be met in regards to fire resistance. Others have previously mentioned this problem in regards to metal over foam. I suppose Thermax could address this concern?
4. Transition: It would be nice to have a vb at the drywall above grade to protect the insulation. One option is to place that vb at the interior side of the existing stud plane and not place one behind the drywall. In that case, I’m almost building two separate walls and stacking them on top of each other.
Here’s the goal, which might help:
This basement is in the 100 year floodplain. It needs to be built with flood resistant materials. As such, choices for materials below the 42″ foundation mark (about the 100 year base flood elevation) are limited and exclude drywall. There is a GP fiberglass backed drywall type product but I haven’t laid my hands on it or anyone who has used it. Corrugated metal survives temporary wetting just fine and can be removed and reinstalled later to dry a wall. I had selected mineral wool batt for its drainability but have been discouraged from using it directly against the concrete foundation. Hence the addition of the 1″ of polyiso as a vapor barrier at the interior concrete boundary. However, polyiso supposedly will take up water in the event of a wetting so I’m not excited about its addition to the wall system.
Anyone have any suggestions for a wettable, drainable wall system that also can insulate the concrete and deal with the transition from concrete wall to above grade stud wall mid wall height?
If the answer is excavate and address insulating the concrete on the outside of the building envelope, I’m ok with that but need to hear that from the voice of experience since it is a big budget sell.
Thanks!
GBA Detail Library
A collection of one thousand construction details organized by climate and house part
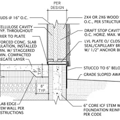
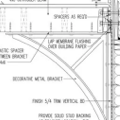
Replies
In order:
1: Adding a vapor retarder tighter than standard latex paint on the interior of your non-structural studwall would only create a moisture trap, since there is an impermeble foil facer on the exterior side of the stud bays. In a zone 5B climate the inch of iso between the concrete and studwall is more than sufficient for keeping condenstation events minimal to non-existent inside the stud bay, and the studwall can dry toward the interior.
2: There is no point to installing a vapor barrier behind the metal wainscotting.
3: Thermax is not a code compliant thermal barrier suitable for occupied condityioned space on it's own,(but IS an ignition barrier that would meet code for crawl spaces, etc.) The wainscotting doesn't change that. But 3.25" of rock wool qualifies as a suitable thermal barrier.
4: Insulation doesn't need to be protected from water vapor- wood does. If you have an inch of iso on the cold side of the assembly and R15 rock wool in the stud bays, the foil facer will stay above the dew point of the conditioned space air, and no condensation will occur. The foil facers of the iso is a powerful vapor barrier to block moisture migration to the exterior sheathing, but it must be made air-tight to be effective. If you are putting metal wainscotting on the lower half of the wall, the primary drying path for the stud bays is through the gypsum at the top of the wall, into the room, so don't block it!
Foil faced iso can only take on water through the edges- the foil is waterproof to both liquid vapor forms of moisture. As long as the cut edge isn't resting on the slab, you won't have an issue with it. The common solution is to put an inch of EPS underneath both the iso and the bottom edge of the stud plate, as both a thermal and capillary break, so than no ground moisture can wick into the susceptible materials via the slab. It's not a sponge either- in the event of a flood as long as the tide goes out reasonably quickly (a couple of days, not a couple of weeks), the iso of less concern than wooden studwall framing.
Keith,
Your focus on vapor barriers and vapor diffusion is entirely misplaced. To learn more about these issues, see:
Vapor Retarders and Vapor Barriers
Forget Vapor Diffusion — Stop the Air Leaks!
Do I Need a Vapor Retarder?
By the way, corrugated metal is a vapor barrier. (Presumably, you are referring to steel roofing or steel siding panels.)
Keith,
One more point: if you anticipate flooding, I would substitute EPS for your proposed layer of polyiso.
Martin,
Vapor barriers and diffusion:
Thanks for the clarification. You are right: I was conflating vapor barriers and air barriers. Based on the links you sent, I'm going to try to rethink my problems.
EPS: Why? Reduced water uptake?
Anticipate flooding might be a bit strong. Remodeling in a flood resistant fashion is more the target. However, I want to be sure that a lighting wetting (<2" of water) is casual to deal with.
Thank you for the feedback.
Keith,
Of the three types of rigid foam -- XPS, EPS, and polyiso -- polyiso is the most water-absorbent.
In contrast, XPS and most types of EPS continue to perform well, even when wet.
Dana,
Thank you for the detailed answer, particularly related to keeping a drying path open upwards. It sounds like I may want to use as breathable a latex paint as I can get.
Is there value to using a smart air barrier/humidity sensitive vapor barrier like CertainTeed Membrain or IntelloPlus at the interior edge of the structural stud bays? If you don't like those products, is there a permeable air barrier you like? Since I'll have the interior stud bay for electrical, it was my hope to add an air barrier to the existing exterior stud bay.
Thanks again.
Keith
You have the foil facers place at an approriate depth in the middle of the R-stack, and there's no point to further vapor retarders. If you want to use a sheet-type air barrier that's reasonably rugged and vapor permeable, use a housewrap (Typar, Tyvek), and detail it as an air barrier by appropriately sealing the edges, seams, staple holes etc. Keep some housewrap tape handy when you put up the metal wainscotting, since you'll probably nick the housewrap a few times in the process.