Bottom edge of rigid foam on basement wall

I’m going about installing 2″ or 3″ of XPS 4×8 sheets on my basement walls and then installing 1×3 firring strips across the top. I’m wondering if I should bring the foam all the way to the basement floor, or leave a gap and fill the gap with expanding foam. My vote is the first method, but I think maybe the gap with expanding foam may be a tighter seal.
Also, bit different question, in zone 5 with a walkout basement (1 side 50% exposed 1 side 100% exposed) should I consider installing foam and plywood on my floor? Contractor never installed it before the pour because he had never seen it done in our area. I’m wondering if it’d be worth the investment and extra hassle.
GBA Detail Library
A collection of one thousand construction details organized by climate and house part
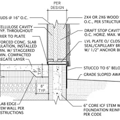
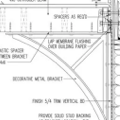
Replies
Nicholas. You find a lot of guidance in this article: https://www.greenbuildingadvisor.com/blogs/dept/musings/how-insulate-basement-wall
Nicholas,
Q. "I'm wondering if I should bring the foam all the way to the basement floor, or leave a gap."
A. If you are installing EPS or XPS on the wall, the rigid foam can extend all the way to the basement floor. (For airtightness, it's always a good idea to seal this rigid foam to the wall with a bead of caulk between the rigid foam and the wall.) If you are installing polyisocyanurate -- a type of foam that can absorb moisture -- it's a good idea to leave a gap of about 1 inch between the bottom of the foam and the slab. The gap can be filled with canned spray foam.
Q. "In zone 5 with a walkout basement (1 side 50% exposed 1 side 100% exposed) should I consider installing foam and plywood on my floor?"
A. Yes. As I wrote in one of my articles, All About Basements, "The main reason to include the [horizontal] rigid foam under [or above] the slab — at least in cold climates — has nothing to do with energy savings; the foam is there to keep the slab [or the flooring above the slab] warm enough during the summer to avoid condensation or moisture accumulation ... If the slab [or the flooring above the slab] stays dry during the summer, the basement is less likely to smell damp and moldy. That's why it makes sense for builders in Climate Zones 4 through 8 to install horizontal rigid foam under [or above] a basement slab."
One final point: One of the most common mistakes for walk-out basements is to forget the vertical rigid foam at the perimeter of the foundation on the walk-out side. You need to extend this vertical rigid foam down at least 2 feet below grade -- 4 feet is better -- to prevent frost from coming in sideways at the vulnerable perimeter.
Hey Martin, thanks for that. Unfortunately the concrete contractor didn't use foam anywhere except for a beam pocket....
A bit too late to do foam on the footings, unfortunately. I did use a very high grade thick mil plastic before the pour, and requested no rebar since it would poke holes as they walked. Instead I got fiber infused cement for durability. My basement is dry and smells fine, being only 1 year old. I haven't noticed any water or musty-ness. I believe the two exposed sides do help keep things dry. In addition, it's all heated and cooled. Since this is the case, do you still see the xps floor as an added benefit if I don't have problems with smell, or moisture? If so, wouldn't my poly below the concrete cause a layer that can never properly dry to one side or the other as XPS is not very permeable? I see myself doing the walls in the next few months, the floors may be something I do a few years+ from now.
Nicholas,
The polyethylene under the slab won't help prevent the problem I'm talking about. The problem I'm talking about occurs when moisture in the air (usually in the summer) condenses on the cold concrete. Since the moisture comes from above, the poly doesn't help.
If you have no vertical rigid foam at the perimeter of the foundation on the walk-out side, it's not too late to add it. Of course, you'll need a shovel...
If it's not too late, swapping the foam to polyiso would be cheaper, greener, and higher performance. XPS is blown with an HFC soup, the predominant component of which is HFC134a, which is a powerful greenhouse gas (well over 1000x CO2). Polyiso is blown with pentane (~7x CO2). As the bulk of the HFCs leak out of the XPS (2-5 decades) it's performance drops by about 12-15%, eventually stabilizing at about R4.2/inch of thickness instead of the labeled R5/inch.
Though the above grade portion of polyiso will underperform it's labeled R by a bit in the dead of winter in a zone 5 climate it will outperform it's label during the shoulder seasons. The below grade portion will outperform it's labeled R value pretty much year round in your climate. This is an artifact of it's non-linear derating curve, gaining performance at cooler temps, peaking somewhere around R7/inch when the mean-temp through the foam is ~60F or so.
Deep subsoil temps in zone 5 tend to be in the 50F range, then falls off to about R2/inch when the mean temp through the foam is +5F. So with a 65-70F basement temperature it will be in the sweet spot for most of the year below grade and through shoulder seasons, but even at 0F outside you're still at a mean temp of about +30F to +35F, well above the abyssmal performance zone. Even when the mean temp through the foam is +45F (70F inside, 20F outdoors, which is probably a bit below your mean outdoor temp in January) it will be no worse than 20 year aged XPS, inch for inch.
Martin (And maybe Dana? :) ) ---
I just purchased 8 2" thick and 8 1" thick XPS sheets 4x8 in size. WOW, the cost is higher than I had originally though. I think it's about $15 to $16 per inch, I did 2" and 1" so I could overlap my seams. I'm only doing my rim joist cavities right now so I am not locked into this method, but I was going to do the 3" total, then run 1x3 horizontal then 1x3 vertical 16" o.c. to create a channel for wires and also wood for drywall. This was the thinnest wall idea I could think of, and I thought that 2" alone would not be enough r-value for climate zone 5.
I am rethinking this a bit, wondering if 1" thick xps (or polyiso) and then a 2x4 studwall tight against that with fiberglass, unfaced, would be a an equal or better option? It would cut my costs down by about 50% if I did it that way the entire basement. The catch is I have only 1" of XPS between concrete and my wood and fiberglass. Zone 5. Is that a risk, at all? I know wood should never touch concrete walls, and I know that fiberglass is normally a bad idea in a basement unless there is a good block between the condensation point and the fiberglass. Considering there is dirt up against 2 walls on the exterior, and then two walls are nearly completely exposed (walkout), maybe the 1" is not sufficient? What are you guys thinking?
Nicholas,
Your plan to use 1 inch of XPS or polyiso against the concrete wall, followed by a 2x4 wall filled with fiberglass batts, will work. (A conservative approach follows the guidelines explained in this article: Calculating the Minimum Thickness of Rigid Foam Sheathing. In other words, in Climate Zone 5, a minimum of R-5 of rigid foam works with a 2x4 wall.)
That said, I wouldn't go so far as to proclaim that your approach "would be an equal or better option." I still prefer the all-rigid-foam approach -- with no fiberglass -- because basements sometimes are subject to flooding.
For more information on this topic, see How to Insulate a Basement Wall.
Martin,
If I were to use XPS instead of PolyIso, does that harm me down the road as the theory currently is that XPS foam eventually loses R-Value, and at that time, my R-5 requirement may not be met. Should this be a concern and head the notion to *only* use Poly-Iso if going for a total of 1" rigid foam?
Thanks!
Nicholas,
If you haven't bought the rigid foam yet, you should choose polyiso, not XPS. Polyiso is more environmentally friendly than XPS.
Here is a link to an article with more information on the issue: Choosing Rigid Foam.
Another option is to purchase used (recycled or reclaimed) rigid foam, which often costs only 1/3 as much as new rigid foam.
Martin,
I treat information and posts here like a bible to building. I have already purchased *some* XPS. I did price the two, Poly ISO and XPS. PolyIso was actually about $5 more per sheet. I think it was foil faced, as there wasn't any unfaced poly iso sold here. I may be able to get some leftover XPS too, from other jobs, but not PolyISO. Blue Dow is the go-to around here, not just because of the marketing but because it's what the building supply stores sell the most of and don't offer the stuff that doesn't sell as well. The drawback of a smallish town. ;)
I have a floor drain and feel like the fiberglass would not get wet unless some serious damage occurs, which, at that stage means the drywall comes out anyway. Hopefully it never comes do that, but if so, I am not concerned about replacing the fiberglass in that situation. My big concern is to build proper so that I am not fighting condensation issues.
Type-I EPS with facers (foil or plastic) is usually quite a bit cheaper per R than XPS.
For a zone 5 climate 1.5" of Type-I EPS (labeled R5.7-R5.8) and a batt insulated 2x4 studwall works, from both a dew point control and code-max U-factor point of view.
Then there's always used/reclaimed goods, at dirt cheap pricing, eg:
http://worcester.craigslist.org/search/sss?query=rigid+insulation