Cold climate wall options

Getting ready to do first home build in zone 6a mid 2021 so researching as much as possible to prepare. GBA and other fine sources as data base but not sure as to which direction to go. Double stud wall 2×4 filled with cellulose and continuous external insultion, traditional 2×4 with external insulation exceeding code and then cavity fill, or 2×6 Advanced framing plus external insulation and cavity fill. Was leaning toward 2, 1 inch EPS layers on external with a rain screen. and cellulose internally. Like Rockwool but the cost… this will be a pretty good house on a budget cause I am a tight wad. Any direction will be appreciated. By the way this source is a wealth of info and geek out reading, watching, linking to all the material. Keep on doing It!
Chuck
GBA Detail Library
A collection of one thousand construction details organized by climate and house part
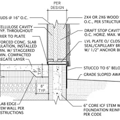
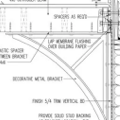
Replies
Hi Chuck.
The only things I am going to point out about your options is that the double stud wall doesn't need additional exterior continuous insulation. That's why you would choose a double-stud wall. It is thermally broken between the two walls and that space can be adjusted to reach your R-value goals.
Some folks feel that walls with enough continuous exterior insulation are the most durable option, keeping the framing inside the water, air, and thermal barriers. But, designed and built right, all of your options can work. For that reason, it is worth also considering what your designer, builder, or you (if you are designing and building yourself) feel most comfortable/experienced with.
Do you have an R-value in mind? Do you have performance goals in mind for the house? With a new build, that's a good place to start, because the walls are only one aspect of the house. What windows and door you choose? How you air seal transitions? What's the plan for foundation insulation, and attic or roof air sealing and insulation? All of that is equally important. It may be worth working with a professional who can do some energy modeling for your project. Otherwise, everything is a guess, maybe educated, but still a guess.
This article gives a good overview of wall options and the decisions you'll need to make about whichever assembly you choose to go with: Walls that Work
Thanks for your fast response. the link to "Walls that work" excellent, lol didn't notice the author until finished reading. IRC 2018 code for zone 6 has mandated continuous insulation. My initial thought was the double wall method, but the debate on cold sheathing caused me to cool (pun intended) on the subject, and a reexamination of the topic. Given that everything in paragraph 3 of your reply is a factor and yes working with professionals is a marvelous idea, however going passive or even pretty good house at the $ amounts often quoted per sq.ft to build makes them a little bourgeoisie for most folk in USA. My goal is a "Pretty Good House" self built as cheap as possible but with the best practices and materials that are affordable in a budget scenario. Hippie modern Pretty Good. So preliminary research followed by professional guidance is a good word. Any thoughts about comparison of performance between self applied wrb vs a Zip type system. The touted benefit is usually in labor savings. How does Zip compare to Georgia Pacific Forcefield. And finally if you went with a double wall system Plywood vs OSB to offset the permeability issue for either directional drying. I know that many articles already written but your thoughts or links would be appreciated.
Hey Chuck,
I'll just add that I personally would avoid buying anything from Georgia Pacific given their parent company's environmental record. Zip System is a proven system with a 10+ year track record. Zip tape is excellent and has also been tested and proven over time.
Self-adhered WRBs are certainly better than mechanically fastened WRBs but you will pay a premium for them.
Regarding plywood in double stud walls: these still fail WUFI modeling in cold climates. Nevertheless, I have plywood-sheathed double stud walls on my home in zone 6a and am far from losing sleep over it.
Good luck and enjoy your build!
Thanks! I really am drawn toward the double stud wall method with cellulose internal and perhaps eps on the external to meet code. The issue of sheathing moisture and that whole debate is the hiccup for me but isnt settled as of yet. IE the post!
You don't need external EPS to meet code.
Chuck,
What are the heating degree days for your location and describe the energy code for your zone. A lot of the cost figures for building beyond code thrown around on GBA are fantasy by builders hoping to win the lottery. It does not cost much more to build beyond code especially if you don't mind a bit of sweat equity.
Thanks Doug for the link. The heating degree days are 7261 for Traverse City, Mi area. Code says that there must be 20 +5 or 13+10 depending 2x4 or 2x6. As this is a self built house labor will be free + tons of favors to friends and family. As a heavy equipment operator I will do all the dirt work, prep forms, hire concrete pour and finish and maybe hire the trusses set on walls. I just feel that to make a real difference in pertinent issues of environment, more personal investment / sweat equity at affordable cost is a must.
>"Code says that there must be 20 +5 or 13+10 depending 2x4 or 2x6."
That is NOT what the code says.
The code says that it MAY( not "must") be 2x6/R20 + R5 c.ci, or 2x4/R13 + R10 c.i., or ANY OTHER wall assembly that is not more than U-0.045 (= R22.2 "whole-wall", with the thermal bridging of the framing factored in as well as the R-values of all layers including air films factored in.) There are also "mass wall" R & U prescriptives that differ somewhat, allowing up to a U-0.060 U-factor provided there is sufficient thermal mass, and at least half the insulation is on the exterior of the thermal mass.
See TABLE N1102.1.2 and TABLE N1102.1.4:
https://codes.iccsafe.org/content/IRC2018/chapter-11-re-energy-efficiency?site_type=public
Chuck, Exterior insulation is not required by code. There are several methods to show code compliance, the table on requirements by component being one of them. You can also use the u-value table, or use a whole-house software. So your double stud wall can work without exterior insulation.
Be that as it may, I am a fan of exterior insulation. If the first layer is 1 1/2" thick, it gives you all kinds of options to provide ledgers and the like for decks and porch roofs, etc. The second layer should be the minimum thickness (more or less) for your climate zone to keep wall sheathing above dew point.
Thanks. Perhaps I am going off wrong code chart residential IECC 2018 section R 402.1.2 removes the optional +5 and makes it mandatory. Please give a reference to the appropriate code chart. End result being a comfortable low cost house to both build and operate.
If your local code is similar to mine, there are two options prescriptive and performance. The tables you are looking at are the prescriptive options, basically "build it exactly like" and you comply with the code.
What you need to look at is the performance option, here you need to show the U value of your assembly meets their U value target. You have to show the calculations that your wall can hit the target without rigid insulation. For example a 2x8 24 OC wall with R30 batts, has a lower (better) U value than the 20+5 prescriptive assembly.
>"Thanks. Perhaps I am going off wrong code chart residential IECC 2018 section R 402.1.2 removes the optional +5 and makes it mandatory."
Try "R401.1.4 U-Factor Alternative" (= the same as the IRC N1102.1.4)
https://up.codes/viewer/philadelphia/iecc-2018/chapter/RE_4/re-residential-energy-efficiency#R402.1.4
Why is cold sheathing considered a risk? We all agree that air sealing is essential. If you do the air sealing on the warm side of the double stud insulation, no vapor will be carried out to the cold sheathing, and so no condensation will occur on the cold sheathing. So where is the risk?
Does external insulation always require its warm side surface to be an air barrier? If so, does this require all of the exterior insulation joints to be sealed on the warm side?
Moist air always seems to sneak into the wall, and air barriers can fail/leak/get damaged over time. Having enough exterior rigid foam eliminates the risk. You do still want to be diligent with your air barriers though.
Rigid foam doesn’t necessarily “need” to be sealed on the outside, but it usually is. Sometimes the rigid foam serves at the primary air barrier, other times it’s a belt and suspenders approach to backup other air barriers. I seal thee exterior rigid foam, the exterior sheathing, and I do air tight drywall on the inside too. It doesn’t hurt to be extra careful, and my thinking is the assembly will hold up better over time this way.
Bill
Ron,
You ask a good question.
https://www.greenbuildingadvisor.com/question/to-tight-scares-me-exterior-xps-over-plywood
This post did not get much response but Mike put his finger on a sheathing (fiberboard) that has been used here in the upper Midwest since after World War II. I have been into many walls over the years, have seen a lot of fiberboard sheathing and do not recall any moisture buildup or deterioration. . Flashing detail failures have been noted especially under windows, this with more recent builds than aged ones. Plaster walls with early fiber insulation, diagonal pine sheathing or fiberboard along with roofing felt under the wood siding or stucco seem to have held up very well.
With the new variable perm air barriers available we should be able to build a double wall that dries to both sides. Couple this with a robust exterior drainage plane and I think you have a working system.
This often repeated claim that cold sheathing is risky makes is sound like the basic design principle is inherently risky, and should be avoided. And yet the risk is usually claimed to be in careless construction. Yet, in those terms, the whole building process is risky.
A well thought out and executed plan of construction eliminates the risk of careless construction. Then there is no need for belt and suspenders. I don’t like the belt and suspenders approach because it doubles the work, and the confidence that one backs up the other tends to reduce the diligence in execution of either one.
Chuck, I am interested to see where you end up.
I am in the same decision stage as you in Charlevoix, except I am hoping to hire a builder this fall. I am also a tight wad but only because I don't really have another option!
Anyway, I will likely hire a pro who specializes in designing this type of cold-climate "Pretty Good House" approach and interview a few of the more affordable local builders until I find one interested in following the plan details. My hope is that an investment in the design of framing and mechanical programs will pay off.
Good luck with your design and let's see if we end up with similar approaches.
Jim
Thanks Jim here is my number 2706175092 perhaps we can share info. Using the kiss model keep it simple, but leaning toward 1500 sq ft, passive orientation, 2x4 walls still not sure of double or not but like the thought. with 2, 1 inch layers of eps external. super seal every aspect of framing then zip, again with meticulous wrb up and over top plate. raised heel trusses and vented attic. Zoning in on R13 25-35,45 in underslab/foundation, walls and attic. Looking at 7 (4 on south side) really nice 2 pane window (at 62 not seeing the ROI in triples) heat pump multi split, heat pump water heat, ERV/Hrv. Doing the work my self will enable me to spend abundant time on air/water seal. That said the plan is to move from Kentucky in spring and be framed in near Traverse City fall. lol I know that can be September. Just pricing online while I work can up with a ballpark number of around 50k in materials to complete rough in not including siding, hope to score some locally sourced material for that. Best results on your upcoming build.
LOL Guess is should say zip then eps foamboard.