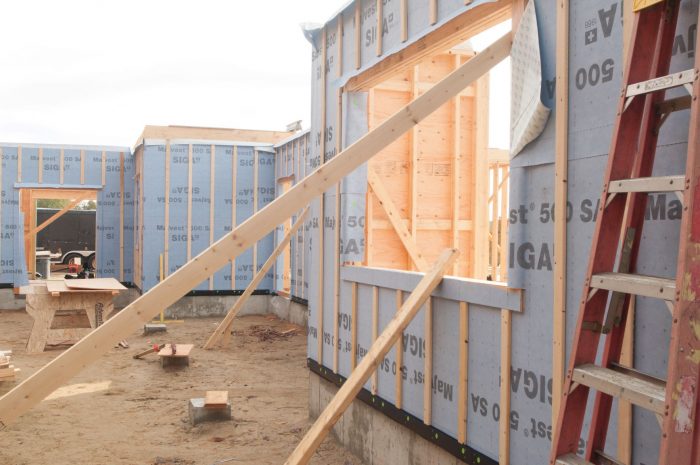
The subhead to this article—Whether you follow your local building code or shoot for high performance, use this guide to make sure your walls won’t fail—makes a promise it can only partially keep. The information you’ll find here can help you design a wall that will perform well in theory, but installation details are equally, if not more important.
Most catastrophic wall failures are the result of one thing: water getting into the assemblies and not being able to dry. Despite their name, the presence of water-resistive barriers (WRBs) isn’t enough. WRBs must be installed impeccably and integrated properly with flashings, and even then, they are known to fail when water can’t drain or dry. That’s why most of the wall assemblies you are about to see incorporate rainscreen siding details that most homes with most siding types in most climates can benefit from, though there are exceptions.
Similarly, walls can fail to perform when the air barrier is not designed and installed to be continuous from one plane of a building to the next. A leaky house is not only inefficient and uncomfortable, it is air infiltration and not vapor drive that causes most condensation issues in walls.
Walls also can fail when not enough insulation is installed or when it is installed poorly. While this failure is often about efficiency and comfort, in some of the assemblies you’ll see below, insulation is used to reduce the likelihood of condensation by controlling the dew point temperature at potential condensing surfaces. Therefore, a failure in this case can also lead to rot and mold issues.
Finally, walls can fail when vapor retarders are used improperly. This failure is not typically the result of poor installation, but rather the result of using a…
Weekly Newsletter
Get building science and energy efficiency advice, plus special offers, in your inbox.
This article is only available to GBA Prime Members
Sign up for a free trial and get instant access to this article as well as GBA’s complete library of premium articles and construction details.
Start Free TrialAlready a member? Log in
21 Comments
Very informative Brian, thanks.
Question: Why does the Zip System perform better than a more conventional combination of sheathing and house wrap/WRB? As far as I understand the Zip System is just OSB boards with house wrap already attached. And you tape the seams between the boards. How is this materially different from taking OSB boards and wrapping house wrap around them?
It seems like it's more convenient, but I don't understand how the assembly is ultimately different from the norm. And you'd be stuck with their house wrap while perhaps the standalone house wrap manufacturers iterate and innovate faster...
Hi Blue Solar,
Below, Rick gave a good answer to your question. ZIP with taped seams and taped plywood or OSB should be able to achieve the same airtightness, all things equal. The reason I wrote about ZIP the way I did is because of my experience covering houses that have used it and the remarkably low ACH numbers the builders have been able to achieve. This is in part because I cover houses that are built really well and the builders favor ZIP for various reasons.
All that said, without taped seams, mechanically fastened housewrap must be meticulously detailed as an air barrier and even then will not likely perform like taped sheathing or ZIP. I have never seen a house with great ACH numbers with house wrap as the primary air barrier on the walls.
Does this answer your question?
BlueSolar,
--" As far as I understand the Zip System is just OSB boards with house wrap already attached. And you tape the seams between the boards. How is this materially different from taking OSB boards and wrapping house wrap around them"--
The real comparison is OSB with seams taped and house wrap over it. From a performance perspective, this works just as well, if not better than Zip System. ( I used taped plywood with house wrap for my house.) Zip system just eliminates the house wrap part. Its more of a labor savings issue than a performance issue. OSB with a peel and stick WRB would also work very, very well and eliminate the taping.
Hi, this article is very apropos for us, as we're meeting with our local building department tomorrow to discuss options for our upcoming build. In the article above, under the 'Continuous exterior insulation may soon be required', it says "In Climate Zones 3, 4, 5, and Marine 4, the IRC gives options for either cavity insulation alone or a combination of cavity plus continuous insulation."
So if I'm interpreting this correctly, the IRC does not provide any prescriptive options for using ONLY exterior rigid insulation, correct? This would be like the Matt Risinger 'perfect wall' house sometimes discussed here. I'm just trying to figure how to come at our local officials, as they seem to think that an assembly with no cavity insulation would not be allowed - even though a wall with only exterior insulation is clearly superior to cavity+exterior.
HI Aaron.
I'm not sure that your assessment that the "Perfect Wall" is better, is actually true. As long as you provide enough continuous exterior insulation to keep the sheathing warm, which offers protection from wetting and therefore makes the assembly more durable, there is nothing wrong with cavity insulation to help minimize heat loss.
Total wall R-value is what matters and there is more to the equation that just cavity insulation vs exterior insulation, windows and doors play a big role too. The best way to determine insulation levels would be to have someone do some energy modeling that considers the size, number, orientation, and performance of your windows and doors as part of the total wall. You can turn these dials a lot of ways and get different results or turn them a lot of different ways and get equal results, which may lead you to decisions based on costs, materials, etc.
As far as your project and meeting with the building department, I can think of two possible ways to approach the subject: Ask the inspector what R-value you need to hit and show them that you can do it with only exterior insulation or use the U-factor alternative. For more on that see N1102.2.4 here: https://codes.iccsafe.org/content/IRC2018/chapter-11-%5Bre%5D-energy-efficiency#IRC2018_Pt04_Ch11_SecN1102.
New HFO blowing agents for closed-cell SPF have decreased the GHG contribution of these products approximately 8-fold compared to HFC-based closed-cell SPF. Yes - the environmental impacts of ccSPF insulations, even with the new low-GWP blowing agents, are higher than fiberglass, the difference is not much.
Caution should be used when directly comparing the environmental impacts of these insulation products reported in environmental product declarations (EPDs). ccSPF is air-impermeable, providing an air seal for the assembly and reducing internal convection that lowers R-value. About 2" of ccSPF provides a Class II vapor retarder. ccSPF also provides a secondary water barrier when used below roof assemblies. To fairly compare the environmental impact of fiberglass to ccSPF, one also needs to include the environmental impacts of the additional air barrier, vapor retarder and water barrier materials needed by fibrous insulations to render performance equivalent to ccSPF. .
There are also less tangible advantages for ccSPF. ccSPF is water-resistant and reduced environmental impacts from not having to landfill ccSPF after a flood or wetting event should be considered. ccSPF has a higher R/inch than fibrous insulations, reduced framing depth (wood) needed. Reduced framing material improves the initial environmental impact of the building. Instead of comparing the 'face value' of products environmental impacts reported in an EPD, it is recommended that a whole-building LCA approach be used.
Rick,
Using ccSPF as primary air control in an assembly is an illconceived approach. There are way too many bypasses for water vapor laden air and other IAQ pollutants to find their way into and out of a wall, roof, or floor. An external air control layer, typically at the sheathing plane, is more effective and more economical.
Using ccSPF as a vapor control layer is effective as you point out in your post but is it the best choice given the assembly and climate zone specific to the project? Every building needs to be designed for vapor control on a case by case basis.
To tout ccSPF as a "secondary water barrier below roof assemblies" is dangerous. Roof leaks need to rear their ugly head immediately so the building owner/occupants can be alerted. ccSPF absolutely can contain a bulk water leak but why would anyone want that? It will only lead to rot and possible structural failure.
Comparing EPDs is very tricky and can lead one down a very deep rabbit hole. We have the ability to make our buildings carbon negative with well informed decisions. Using ccSPF in new construction is lazy but it definitely has a limited role to play in renovations where air and vapor control are impractical without its use (rim joists, top plates to rafters, etc).
Filling our buildings with this product is really just kicking the can down the road. It will end up in a landfill upon the next renovation, and the future carpenters are going to hate every second of peeling this stuff out of assemblies.
On a 100-year scale, HFO-blown ccSPF looks pretty good, especially compared to HFC-blown and considering some of its unique properties. I have to give kudos to the spray foam industry for moving forward with the more-benign blowing agents even after the the ruling that would have made them law this month was retracted. The problem is that we don't have 100 years for the benefits to catch up with the environmental damage created by materials with high up-front carbon emissions.
It's pretty easy to create airtight, vapor-controlled structures that are foam-free, and the materials used usually have relatively low carbon emissions--paying their carbon debt quickly, not over 100 years. It does require builders to learn a few new skills but nothing that is particularly difficult or expensive.
Brian,
Thanks for the reply. I agree that there should be little performance difference between the exterior insulation only wall, and a wall with cavity insulation and a suitable level of exterior insulation (all properly installed, as pointed out). I was more looking at the exterior insulation only, compared to cavity insulation only - one is clearly superior, is it not?
In any case, we're in Marine 4, a mild climate in all seasons, so we're neither looking for nor needing extreme levels. We do not want to use any 'fluffy' or fibrous insulation, for various reasons, but the idea of using rigid insulation between the studs seems ill-advised, which is one major reason we're looking to go all exterior foam. This is actually not for our primary residence, but an outbuilding, so it's not like we'll be keeping it 70+ degrees year round. However, the AHJ says if it's heated at all, it needs to be insulated to the same levels as a primary residence.
In any case, I will definitely look at the link you provided and see if it gives us some good guidance as to how to approach the county, thanks!
Aaron
Hi Aaron.
Perhaps if all other things were equal, it would be best to put all of the insulation outside of the sheathing, which would keep the framing entirely inside the conditioned envelope and do the most to mitigate thermal bridging (that's the "Perfect Wall" idea). I did want you to think there was anything wrong with adding cavity insulation though. Often the most cost-effective approach is a combination.
Brian,
Understood. I didn't think there was anything inherently wrong with having cavity insulation, and it almost always is the most cost effective approach, whether alone or in combination. Not having any cavity insulation, however, does open up some very interesting possibilities and ease certain aspects of construction, while admittedly making others more difficult. :) This site has been one of the primary drivers of our design plans regarding insulating and sealing, specifically the 'Getting Insulation Out of Your Walls and Ceilings' article by Martin Holliday. That article is now over 10 years old, and the concept still seems foreign to the code and local officials (admittedly we're in a very small county).
Cost is always a factor, but realistically, the added cost to use rigid foam for the entire structure rather than cavity-only fiberglass, or cavity+rigid foam, is minimal compared to the cost of the whole building - at least in terms of material costs. Compared to rock wool, the difference is even less. The idea of keeping the entire frame and sheathing within the conditioned space, seems to me, a major benefit for the exterior only method. If we were paying someone to build for us, we'd probably be more apt to penny pinch, but we're building ourselves, so we can afford to put a bit more into the components.
Totally agree about the design possibilities. I love the interior of Matt Risinger's Perfect House, which was designed by Eric Rauser.
Aaron,
It's a small distinction, but as long as the exterior foam is thick enough to deal with moisture problems, assemblies that include cavity insulation also "keep the entire frame and sheathing within the conditioned space".
I think it helps to explain that there are 5 control layers, to distinguish bulk water from moisture. Distinguishing them separately explains:
1. why rain screen cladding faces are distinct from the water resistant barrier (WRB) layer (sometimes far) behind, usually a completely different product;
2. the reservoir nature of masonry and cement-based cladding systems, why both a cavity and a WRB is needed behind, and why mechanical wraps struggle in this location;
3. why the surface where dew point occurs has to manage condensing droplets, potentially for a lengthy period, and not just rain;
4. the complexity of figuring out vapor permeability as well as drive direction with the possibility of both in some climates;
5. the design clarity needed for both air sealing and vapor control measures;
6. the (manufacturer-induced) confusion with mechanical wraps and their inadequacy to manage moisture within a wall versus their original air infiltration function and temporary construction protection against bulk water.
At least here in the Southeast, humidity and moisture are big problems that cause mold even under big roof overhangs. The cause is confusing if you only think about envelope protection from rain, but the problem crystallizes once you comprehend that a cold house cavity in humid summer needs to somehow manage condensation within the envelope.
Hi Steve.
The four control layers of a wall include bulk water, air, vapor, and thermal. I think what you mean by "moisture," is the vapor control. What is the fifth layer that you propose?
You can read about the control layers here: The Four Control Layers of a Wall
Hi Brian,
For me the 5 controls are for bulk water, moisture, vapor, air, and thermal.
Bulk water is shed by the exterior, such as by brick, siding, glass, FRC panels, metal panel, roofing, etc.
Moisture is "incidental." It clearly includes any exterior moisture not immediately shed, like wind blown water under the rain screen. But it also includes a lot of other source we forget—condensation of exterior humidity on the chilled interior of a house, vapor driven out the back of cladding by the sun, and capillary action directly out of the cladding and adjacent materials and the ground. The controls are as diverse as the moisture—pre-applied WRB on sheathing, spray-applied, flashings and membranes, maybe even multiple layers of mineral wool that is completely vapor open.
The reason to distinguish moisture from bulk water is that most envelope systems do not shed 100% of the water. This is where problems begin. Rain screens relocate the bulk water control away from the moisture control. Anchoring systems and insulation potentially create problems behind the shedding surface. Brick works the same way, where the face excludes very little water and rivers flow behind. Weeps and turn-out flashing details are important, as is cavity depth, anchor placement, and rigid insulation placed within the cavity. Glass is impervious to water, but frames usually have a management system that baffle installers of windows, wraps, and sealants. Panels and water-managed curtain walls are even more complex. So It's important for any design to be clear about how all the "incidental" moisture is managed, because it's where 99% of the problems happen. Adsorption is a powerful force.
Vapor, just to touch on, is not always managed by something outboard where the WRB lives. It could be drywall, some vapor "adjustable" membrane under the drywall, craft paper insulation facing, or closed poly in the extreme climates correct for that. We also know that the most closed surface usually acts as a vapor control layer, too, but sometimes additional vapor control inboard is helpful if we need it more inboard than the WRB (like empty metal stud cavities).
The challenge is usually that one product/layer manages multiple controls: vapor-permeable WRBs, asphalitic felt, exterior rigid insulation, etc. So I find that outlining all five layers in wall sections and details with corresponding colors to be a simple visual double check of design to manage "cross-over" points where lines merge or diverge. It especially helps me think about all those drops of moisture that un-vaporized or crept behind the cladding.
Thanks for the thorough reply. And your thinking makes sense to me and I agree about the importance of knowing exactly what product or building material is responsible for which control. That's one of the reasons why I decided to write this article. Though the information is the same as in the article about control layers. The examples help to show how each control is performed in various assemblies.
Hi Brian,
I’m wondering why you did not mention Zip system R sheathing as an option? It seems like this could have been a footnote in the “integrated panels” wall assembly? Perhaps you would want to add it to the “continuous insulation” wall assembly?
I’m curious where the Zip R sheathing fits in? It sure seems like a wall assembly of (in to out) 1/2” drywall - 2x6 framing - roxul batt insulation - zip R sheathing - rainscreen - siding would do quite well for many climates and I like the fact that it doesn’t change the construction flow for many builders or present new or extra detailing. AnY thoughts on this as an option? Is it different enough from the “continuous insulation” example because the foam is in-board of the sheathing? Or does that not matter?
Cheers
Hi Michael.
There is no reason why we didn't include a wall with ZIP-R other than to limit the scope of the article to a reasonable length. The five walls are what seem to be the most common, with some variation to explain how various materials change the assembly.
I do need to learn more about ZIP-R and maybe a post specifically about how to use it right will be coming in the future. It's an interesting product, offering some characteristics of continuous exterior insulation by mitigating some thermal bridging through studs and some characteristics of a flash-and-fill, since the foam insulation is inboard of the sheathing and the cavity still needs to be filled with some other type of insulation.
I've been curious about it for a while. Maybe it's time to take a look.
Please do take a look at ZIP-R. I just undertook a project with it and have seen comments on GBA from others who have as well. In my area, it was the only way I saw to achieve a successful exterior insulation installation with limited skillset trades.
Hello, all.
I am new to the site but have really appreciated the information provided and the building knowledge that is shared. We will begin construction on a custom metal home (aka "barndominium") in the next few weeks. I will have help/advice from my brother-in-law contractor (he only builds traditional homes) but will mostly be my own GC. I have been reading and rereading information regarding the best wall and insulation system to meet our needs and would greatly appreciate professional advice to get it right.
Our house will be a "hybrid" with a red iron "skeleton" and wood 2x4 framing in between the red iron; therefore we will have both wood and iron studs flush to the exterior. We live in south Georgia....very hot and very humid. We only have a couple of months of cold weather with maybe only a couple of weeks of freezing temperatures. Most people in this area that build metal homes are using spray foam for insulation, but I want to limit the use if at all possible for two reasons: high cost and the possibility of trapping interior moisture.
Here are my thoughts for the wall system from inside to out: sheetrock; unfaced batt insulation; wood/metal studs; XPS 3/4 inch rigid foam board (unfaced) that will be taped and sealed completely; vertical commercial grade metal siding.
I would like to have the continuous insulation of XPS foam board to reduce thermal bridging. I can't use any more than 1" because I did not factor this into the equation when we contracted and ordered the metal building, but metal contractor does not believe 1" or less will be a problem. He usually installs the MBI but we know we do not want that. I do not believe other sheathing will be structurally necessary. Also, the external foam board will help us achieve required R rating with only 2x4 cavity in the walls for other insulation.
We will have a vaulted ceiling and the roof will be traditional metal (NOT standing seam) attached to metal trusses, rafters, etc. There will not be wood framing in the roof structure. We will probably use closed cell foam on the ceiling to achieve air/vapor barrier and high R value. The wings will have attic spaces that will be within the conditioned envelope.
We will research and use the best HVAC system for our home. I know there are special requirements and plan to have a professional help us with what is needed as far as variable speed, humidity control, fresh air intake, etc. I do not have enough knowledge to speak to this but know there are special requirements especially if using spray foam, so we will contract with a professional.
My questions:
1 - Will the XPS serve as a sufficient water resistant barrier and air barrier if taped and sealed as required and all windows and doors installed correctly with needed sills, wraps, etc.?
2 - It seems that XPS is slightly vapor permeable which may allow for some drying outward. Is that correct and will that be helpful in our climate? Is the XPS enough to limit moisture from driving inward?
3 - I am thinking the corrugation of the metal will be enough of a 'rainscreen" to allow moisture to drain down without furring strips. Would this be enough?
4 - I am assuming the metal siding is enough structurally since most metal homes in this area are metal siding with spray foam applied directly to metal without any other exterior sheathing. Is a separate sheathing needed?
I want to get the wall system right without overbuilding. I am very concerned with avoiding any moisture problems and achieving a well insulated envelope for efficiency. Any advice or critiques will be greatly appreciated! Thanks!
Log in or become a member to post a comment.
Sign up Log in