Door to basement or no door to basement?

We’ve got an unfinished, but nice basement in our 1940s cape just outside of Boston. There’s an oil furnace, gas water heater, and gas dryer running down there. There’s also one heat duct and a dehumidifier. I’ve had the door to the basement removed since we purchased the home in the spring and have liked it that way. My wife is telling me to put it back on because it’s going to cause our heating bills to be greatly higher than they would be if it were reinstalled. There is no insulation between the floors.
Is she right again?
GBA Detail Library
A collection of one thousand construction details organized by climate and house part
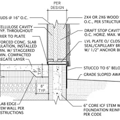
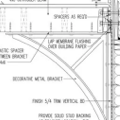
Replies
Stephen,
In case you haven’t figured it out by now, she’ll always be right. Unless your basement floor and walls are insulated, she is right. Now, you can pay that bet by doing the dishes…
Stephen,
Is this an interior door at the top of the basement stairs or an exterior door leading to the great outdoors?
Stephen,
If the doorway is wide open you may have more to worry about than energy. From your description the basement is open to the great outdoors so I have to go with the wife on this. If the opening is covered and air sealed well its not likely to be noticed on your energy bill. A layer or two of foam sheets will make a quick and cheap energy barrier. Just pay attention to sealing all the cracks. If you are worried about your neighborhood thief something a bit stouter than foam may be called for, maybe foil faced foam. ;-)
john the toymaker
Ha! This is an interior door. Leading to the kitchen from the basement stairs.
Stephen,
If you leave the door at the top of your basement stairs open, you allow air to flow up the stairs from the basement (in response to the stack effect). As air leaks through holes in your top-floor ceiling, replacement air comes in from your basement rim-joist area. This makes your dehumidifier work much harder.
Thanks Martin. I also have a heat duct that had to be moved due to a kitchen remodel. It is currently open in the basement because I haven't punched a hole in the kitchen floor yet. I was considering keeping it running in the basement and just letting the heat rise up through the kitchen floor. That would keep the basement warmer too. Another Bad idea?
Stephen,
It's your house; you can choose to heat the basement if you want, or to leave it unheated (or, as some people say, accidentally heated by whatever appliances you already have down there).
If you think your basement is too cold without a heat register, and if you like to hang out down there, then go ahead and add a heat register. Of course, if your basement walls are uninsulated, you will suffer an energy penalty due to your plan to add more heat to your basement.
Thanks Martin, Do you also recommend weather stripped doors between conditioned floors to slow stack effect and heat rising to thr top floors in these old capes?
Stephen,
If the stack effect in a house is bad enough that you need weatherstipped doors at the top of every flight of stairs, you have a problem. (I've lived in houses like that.)
If that's the case -- if you are leaking so much heat out of your top-floor ceiling that it's hard to hold any heat on the ground floor without weatherstripping the door at the top of your stairs -- then you would be better of devoting your energies to plugging the holes in your ceiling (that is, your attic floor).
Understood Martin. It holds heat on both living space floors pretty well, but the furnace kicks on and off quite often. The main floor has vinyl double glazed windows and the upper floor has old single panes with storms. Think I'll be using some plastic on them this year.
Builder remodeler advice.
1- Keep a door up and closed, mainly for fire safety separation. Make sure you have your smoke and CO2 alarms installed and working in proper locations.
2- You can add a door sweep to the basement door.
3-If when you say you have gas, you mean natural gas not propane, your home should be switched for todays costs anyway to a gas heating unit. There are incentives to look for.
Lastly, read up here on how to seal up parts of your home. But you can get in trouble too doing such willy nilly.
Leaving oil for gas... I like if you like. If your budget big... there are more fun choices in the blogs and around this site.
Aj, We're in the process of converting to natural gas. The house came with a full tank so we'll burn through it first. What % efficiency should one shoot for? Our budget is small.
The efficiency can save on install cost or not depending on your flue and installer.
Gas is so inexpensive that you won't save that much by highest efficiency though that is what I install. Get prices from many contractors. Then follow up and go to their shop, and call some customers.
On this site Energy Vanguard Doc Allison...along with Dana are the super pros to answer your question. Dana may be your best bet for free advice.
Air sealing the interface between the basement and the first floor in a house with multiple duct penetrations, probably close to a dozen plumbing/drain/vent penetrations and score of electrical penetrations is something of a fools errand. Even if you nailed up an OSB ceiling and applied copious foam/mastic/caulk it's hard to make much headway against stack effect beyond the biggest and most obvious of holes.
But you CAN usually air-seal the foundation & band-joist to the outside to thwart stack-effect leakage. Also high on the list are sealing up any plumbing-vent or wiring chases that go from basement to attic. If your basement is currently un-finished, air sealing & insulating the foundation with a couple inches of closed cell spray foam (at ~$2/square foot, maybe $2.50) will take a healthy double-digit fraction off the heating fuel use, lower the humidity load in the basement and the basement would stay warmer.
Air sealing the attic is also important, since that's the top of the "stack". Wiring penetrations, plate-less partition walls, flue & plumbing vent penetrations all need to be attended to, not just the weatherstripping on the access hatch (but fix that too, eh? ;-) ) If you have a lot of air sealing to do, buy a $50 version of a pro foam gun that takes the screw-on cans rather than using the box-store throwaways with the cheezy straw tips. You'll save a lot time money and aggravation with the real tool.
On the gas-furnace, anything over 90% (condensing) is fine- just be sure to not oversize by a huge factor, and be sure it's a "direct vent" type that draws it's combustion air from the outside rather than from conditioned space. Since condensing furnaces vent out the side rather than a flue, brick up the flue openings to prevent IT from sucking infiltration air 24/365 too.
Right-sizing a furnace does wonders for comfort, by keeping the cubic-feet-per minute wind-chill/air-blast low & quiet, with long comfortable burns rather than on 5 minutes, off 15, etc. Sealing up all the seams & joints of the existing ducts with duct-mastic will also quiet the thing down and improve flow to the far-registers by lowering the leakage- it's a DIY project for those who don't mind getting dirty.
The oil furnace is probably at least 2x oversized, and very likely more than 3x oversized, if experience is any guide. If you have a K-factor stamped on a mid or late-winter oil bill, let's have it, because a very real upper bound on the whole-house heat load can be derived from that, in combination with your outside design temperature. For Boston the 99% design temp is +12F, but in Gloucester it's +5F, so your actual zip code may count. See:
http://www.energystar.gov/ia/partners/bldrs_lenders_raters/downloads/Outdoor_Design_Conditions_508.pdf
At typical 1940s ~1500-1800 foot cape that has some insulation and at least storm-windows if not double-pane replacement windows will usually have a heat load at +10F of around 30-40,000BTU/hr, yet most older oil furnaces are blasting away at over 100KBTU/hr out.
Old school heating hack in this area eyeball the place and say something like " Lessee, 1800 feet times 35BTU a foot give ya 63K, so bump it to the next size, up, call it 80KBTU/hr" But real heat loads are much smaller than that, and those rules of thumb RELIABLY oversizes it, usually by 2x or more, and 2x oversizing is enough to impact comfort- you really want it to be no more than 1.5x. Even at 1.5x you're good down to about 30-40 below, a temp not seen in Boston since the last ice age.
There are proprietary software tools for calculating the load based on construction (R-values, U-values, total area of each) but those are easy to screw up too, with unrealisticically low design temperatures or overestimating the air leakage. The K-factor (=degree-days per gallon of oil) doesn't lie, and using the nameplate efficiency of the furnace (or just calling it 85%) you have a measurement (however crude) not a estimate. You have to change the degree-days to degree-hours, and gallons-in to BTUs out and look up the 99% design temp, but it's enough information to put an upper limit on what the heat load is: The oil-burner is never more efficient than 85%, and unless you kept the place at 50F the calculated number will still have some margin over the true heat load at +12F.
Thank you Dana! I am in Waltham. Is your company located near Boston?
My company is a few miles up 128 from you, but we're not in a relevant biz. (I've probably learned enough to be a home-efficiency & building-efficiency consultant, but I make my living in a completely unrelated field, and haven't been directly involved in construction for decades.) I do my own heating & building design when making changes at my own house, and have done a fair amount of advising (and even some of the design work) on "friends & family" projects (including on a deep energy retrofit on a 3-family in Worcester that should be at or near completion this week- I'll be peeking in on it this weekend.)
BTW: If you have a supply duct but no return duct in the basement (or in any room/zone without adequate return paths) the air handler will end up being a much higher infiltration driver than any stack-effect issue. Air-sealing the house is VERY important for system efficiency on any ducted air system, as well as a balanced duct system with reasonably sealed ducts. Duct imbalances and duct leakage creates room-to-room pressure differences, and with a leaky house a fraction (sometimes a LARGE fraction) of the return path is the great outdoors. Take a look around and identify any rooms with supply ducts that are potentially doored-off from the nearest return- retrofitting jump ducts or transfer grilles, (or the under-door units from Tamrack, if it's not too architecturally inappropriate) may be in order.
In large scale site-surveys & testing in CA the typical leakage on existing ducted systems the volume of duct leakage was well into double-digit percentages and even 40% wasn't rare, prompting a requirement for duct testing & remediation to reasonably-achievable limits for new construction under CA Title 24 building code.
Also, any heat load calculations should use a design temp of about +9F, not +12F as in Boston. Waltham doesn't get nearly the moderating influence of water and urban heat island effect as Boston, but it's not as cool as Framingham (99% design temp= +6F). It only makes a ~5% difference, but 5% is 5%. Any heat load calc will have more than a 5% error, but staring out with the right design temp reduces the size of the error bars.
Do you have a mid-to-late winter oil bill with a K-factor to work backward from?
Dana - The only supply duct is in the living room right above the furnace. There are no return ducts in the entire house. I don't have any bills because we just bought the house from an estate sale. But I have been in the house during the winter, hearing that furnace kick on and off every 5 minutes. They had the chimney flue wide open which I'm guessing could have had something to do with the heat loss. I need a stuff something up there..
There simply MUST be some sort of return-path for the furnace air- is it an open-grill right at the furnace (sucking in basement air)?
For a crude I=B=R type calc, measure the total square footage of exterior wall on the first floor, subtracting out the square footage of the windows & doors (keep the total square footage of windows & doors too.) Measure the square footage of the upper floor ceiling. Either in a spreadsheet or napkin work the math:
Assuming an interior temp of 68F, exterior temp of 8F that's a 60F delta-T.
If it's 2x4 framing with clapboards or shingles and there's ANY type of cavity insulation, multiply
[total wall area] x 0.1 x 60F= BTU/hr loss out walls at 8F
If the windows have storms or are older double-panes multiply:
[total window & door area] x 0.5 x 60F= BTU/hr loss out windows & doors @ 8F
(If they're single-pane windows in good shape, plan on buying some low-E storms.)
If the attic has 6" batts or blown insulation multiply:
[total ceiling area] x 0.08 x 65F= BTU/hr losses out the ceiling.
(If it's more like 12" of attic insulation, cut that number in half.)
Measure the uninsulated foundation-wall area that is above-grade, multiply:
[above-grade foundation area] x 1 x 60F (or 50F, if unheated)= BTU loss out the basement
(If you intend to insulate & seal the basement, divide that by 10.)
Add them all up, and it'll probably be but a fraction of to the name-plate output of the old oil furnace.
Even if it's a fairly air-leaky house the true heat load won't be anything like 2x that number, but it might be as much as 1.5x if the place is one drafty wind-tunnel of a place. But for purposes of sizing the furnace assume you'll be doing remedial air-sealing. Putting anything over 1.25x the raw calculated number will likely be a mistake if you're planning on tightening up the place at all.
There is usually some margin in that type of calculation- running an I=B=R method on my own place delivers a number fairly close to the fuel-use number, but the fuel use also include hot water for 3 (and my kid is the king of endless showers- I put the bathroom light on an occupancy sensor that times out in 12 minutes to give him the hint.) At the water temp I'm running for the hydronic space heating I'm radiation-limited to about 1.1x the calculated number, yet it still kept up without trouble when it hit -8F last year, fully 13F below the design temp.
If you have an open undampered fireplace flue, some of the top-sealing dampers seal pretty tight. There are also inflatable flue-balloons, but they're a PITA if you actually ever want to use the fireplace. There are also air-tight wood burning fireplace-insert/stove units that burn cord wood at ~ 70% efficiency too. (The guy doing the deep energy retrofit on the 3-family heats his personal home with one of those.) A wood-burning insert can be about as expensive to install as a small condensing gas furnace. (Not counting hooking the house up to the gas main.) A chimney-top flue damper is about a hundred + installation, and are pretty easy as a DIY install if you don't mind working at that height.
Great stuff Dana. Very straight forward calcs.. The only supply/return is just above the furnace on the first floor. Nothing on the 2nd floor.. I'm going to try and make my own flue balloon out the wifes yoga ball.
An exercise ball isn't flexible enough to seal tightly. Purpose made flue-balloons aren't expensive (cheaper than one visit to a marriage counselor after she starts in about you sabotaging her health... :-) ) and unlike a ball, they'll actually work. One online source that's pretty local:
http://www.energyfederation.org/consumer/default.php/cPath/21_0_421_4149
I'm surprised that there are NO ducts to other rooms- often they would put a supply to each room and a single central return, but having single supply and having it located right next to the return guarnatees that the thing will short-cycle and leave the remote rooms much cooler than the room with the supply when it's cold out. It's probably worth springing for a Manual-D compliant duct system to go along with the new-improved gas furnace. If this is a 1.5 or 2 story you may have to compromise a bit on the upper floor.
Depending on where your heat load numbers come out and how much they're charging to hook you up to the gas grid there may be a financial argument for installing a ductless air source heat pump (mini-split/multi-split) instead of a gas furnace. The operating cost would be only marginally greater than condensing gas (and way cheaper than oil or propane), and you'd have high efficiency air conditioning out of the same equipment. If they have to extend the main even 100' to get to you the costs of just hooking up to the gas can exceed the installed cost of a ductless heat pump, but if they're just tapping in and trenching 40' to your house from a main right out front the charges aren't usually egregious.
I am saying things wrong.. All of the rooms have heat supply ducts.. But there is only one, central, return duct. The house already has gas piped in and running for the dryer and water heater. The oil furnace is right next to the gas pipe inlet from the street, so the pipe work will be minimal.
Ductless air source heat pump (mini-split/multi-split) sounds good for my other project. I'll have to look into them.
OK, THAT makes more sense!
In small houses a single central return can work OK, but only as long as doored-off areas have sufficient return paths when the doors are closed, otherwise the great-outdoors becomes part of the return path(!). Door grilles, transom-grills, jump-ducts etc. can all be used. Partition-walls can be sometimes be employed as a jump duct while preserving privacy by installing a grill at the bottom on one side of the wall, at the top on the other, etc. But that approach can also become an air-leak into the attic in some houses- a lot depends on how the house was built.
A door-cut at the bottom can work, but at most flow requirements it takes a hamster-escape sized cut to achieve the low-low pressure differential required. If your doors aren't of huge architectural-purity interest there's a retrofit bottom-of-door solution made by Tamrack Industries that fills the bill even with close-fitting thresholds tight enough to keep hamsters & lizards from escaping:
https://www.greenbuildingadvisor.com/blogs/dept/green-communities/perfect-balance-makes-cut
http://www.tamtech.com//store/indoorairpressure-balance-ashrae-energystar-transfer-grille,Product.asp
If the gas-fired hot water heater is vented into the flue rather than a power-vented type with a side-vent you could end up with condensation & backdrafting issues. google "orphaned hot water heater" for details.