How do I insulate an unvented roof with a T&G ceiling? Also: question on wall detail

I have read many of the articles on low slope unvented roofs and still am unclear. I need to know if both those plans work and if not, what is the solution. I am in CZ6 Utah cold winter below zero and hot summer up to 95 degrees and very dry. 1/12 pitch roof, monopitch south to north, south being the taller side. Passive solar design with south windows,
Plan from exterior to interior:
Option 1. Sika Sarnafil membrane, 4″ fiberglass face Polyiso (the brown covered stuff), 5/8″ sheathing of OSB or Plywood, 1″ Closed cell spray on underside of sheathing as air barrier, rest of 12″ TJI cavity filled with cellulose, Polyester netting, Tongue and groove wood.
Option 2. Sika Sarnafil membrane, 4″ fiberglass face Polyiso (the brown covered stuff), 5/8″ sheathing of OSB or Plywood, 12″ TJI cavity filled with cellulose, CertainTeed Membrain as netting and air barrier, Tongue and groove wood.
(Basically thes same as option 1, but with certainteed Membrain just above T&G instead of the 1″ Closed cell spray foam underneath sheathing deck.)
As for my wood frame above grade walls, does it matter if I use 2″ of paper faced polyiso or 2″ foil faced polyiso on the exterior?
Here is the plan from the exterior to interior: Swisspearl cement board open rainscreen cladding, Vaproshield Revealshield Weather barrier, 3/4″ battens for rainscreen airgap, 2″ polyiso (paper faced or foil faced?), 7/16″ OSB or plywood, 2×6 wall with cellulose (densepack or blown?), drywall and paint.
Thanks very much for any help on this, as I want to get this right in my very cold winter and hot summer climate.
Steve
GBA Detail Library
A collection of one thousand construction details organized by climate and house part
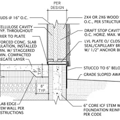
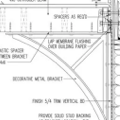
Replies
Steve,
In Climate Zone 6, you want to aim for R-25 of insulation above your fluffy insulation. If you choose polyiso, which performs poorly at cold temperatures, you might rate the polyiso at about R-5 (average) per inch -- so 4 inches gives you about R-20. Five inches would be better, although adding 1 inch of closed-cell spray foam on the underside of the sheathing gets you closer to your goal (at the expense of encapsulating the sheathing, of course, so that it can't dry as easily to the interior).
All things considered, I guess I'd go with Option 1, as long as "polyester netting" (whatever that is) is a true air barrier with carefully sealed seams.
The polyester netting I referred to is just the stuff to hold the fluffy insulation in until the T&G boards or drywall are installed. I'm sure it's not an air barrier.
So if I make sure I get R25 of polyiso above the sheathing, can I just put CertainTeed Membrain above the T&G boards, with cellulose filling the rest of the cavity, therefore allowing drying to the inside and saving the high cost of the spray foam under the sheathing?
Thanks again,
Steve
Thanks again.
Steve,
Q. "So if I make sure I get R-25 of polyiso above the sheathing, can I just put CertainTeed MemBrain above the T&G boards, with cellulose filling the rest of the cavity, therefore allowing drying to the inside and saving the high cost of the spray foam under the sheathing?"
A. Yes, as long as the MemBrain is detailed as an air barrier. Here is a link to an article with more information on these issues: Insulating Low-Slope Residential Roofs.
Martin,
Thanks you. I've read that article at least twice, and was still not clear if 1" of closed cell polyurethane sprayed under the roof sheathing acts as a sufficient air barrier when using T&G ceiling material, since the T&G is obviously very air permeable. I believe you answered my question.
Can you advise on the second part of my original post with the question as to the wall assembly? I've re-posted it below.
As for my wood frame above grade walls, does it matter if I use 2" of paper faced polyiso or 2" foil faced polyiso on the exterior?
Here is the plan from the exterior to interior: Swisspearl cement board open rainscreen cladding, Vaproshield Revealshield Weather barrier, 3/4" battens for rainscreen airgap, 2" polyiso (paper faced or foil faced?), 7/16" OSB or plywood, 2x6 wall with cellulose (densepack or blown?), drywall and paint.
Thanks again, you and the folks who advise here are a wealth of information and it is appreciated.
Steve
Steve,
A couple of responses to your wall questions:
1. The exterior polyiso can have any kind of facing you prefer. A foil facing will provide a small (R-1 or R-2) boost in R-value for the whole wall assembly, buy only if you can manage to have one side of the polyiso facing an air space.
2. Your siding will dry more quickly if it has an air space behind it. Installing your WRB between the furring strips and the siding defeats some of the benefit of the rainscreen gap. The preferred location for the WRB is either (a) between the rigid foam and the furring strips, or (b) between the wall sheathing and the rigid foam.
Steve,
You asked whether the cellulose insulation should be "dense-packed or blown." That's confusing, because dense-packed cellulose is blown.
The only issue is how densely the cellulose should be blown. The answer to that one is easy: a dense installation is better than a less dense installation. When installing cellulose into stud cavities, the installer should be aiming for a density of at least 3 pounds per cubic foot -- and when that method is used, it's called a "dense-packed" installation.
Steve,
Q. "I was still not clear if 1 inch of closed-cell polyurethane sprayed under the roof sheathing acts as a sufficient air barrier when using T&G ceiling material."
A. The question is hard to answer. There is no doubt that 1 inch of closed-cell spray foam is a good air barrier. (For that matter, so is roof sheathing with taped seams, as long as you have chosen a high-quality tape like Zip System tape.)
The reason that this question is hard to answer is that you are planning to install cellulose between the air barrier and your T&G boards. In theory, you don't want any convective loops of interior air in this air-permeable insulation, so an air barrier at the T&G ceiling layer is desirable. In practice, this is more of a concern with fiberglass batts than with cellulose (especially dense-packed cellulose), because there isn't much convective looping through cellulose. However, the air barrier under the T&G boards is cheap insurance, preventing problems in the event that your cellulose installer is sloppy.
Thanks again Martin.
Last questions here regarding the basement: I plan to put 2" of EPS foam on the exterior of the 8'-9' foundation basement walls. What should I put on the interior? This is a new build with thermal breaks between the basement slab/foundation wall/footings.
My plan was this, outside to inside: 2"EPS, damproofing, foundation wall, 1"-2" of Polyiso (again foil faced or paper/fiberglass faced?) some studs with cavity filled with cellulose, drywall, paint. Perhaps I don't need the cellulose?
How much insulation under the slab and of what material? EPS, XPS, or is Polyiso OK?
Any suggestions or advice so I can move forward?
Hopefully this thread will be helpful to others in a Zone 6 climate :-)
Steve
Steve,
Q. "I plan to put 2 inches of EPS foam on the exterior of the 8'-9' foundation basement walls. What should I put on the interior?"
A. According to the 2012 IRC, in Zone 6 you need a minimum of R-15 for your basement walls. The 2 inches of EPS gives you about R-8, so you still need another R-7. I would say that another 2 inches of EPS on the interior would be one easy way to go. For more information, see How to Insulate a Basement Wall.
Q. "My plan was this, outside to inside: 2 inches EPS, damproofing, foundation wall, 1"-2" of Polyiso (again foil faced or paper/fiberglass faced?) some studs with cavity filled with cellulose, drywall, paint. Perhaps I don't need the cellulose?"
A. You can use polyiso if you want -- you'd need 1.5 inch or 2 inches of polyiso to satisfy minimum code requirements. I would skip the cellulose; it's a bad idea to use cellulose in a basement, because basements can flood.
Q. "How much insulation under the slab and of what material? EPS, XPS, or is Polyiso OK?"
A. You can't use polyiso in contact with the soil, because it absorbs moisture. XPS is manufactured with a blowing agent that has a high global warming potential, so green builders avoid XPS. That leaves EPS. I would install at least 2 inches of EPS; 4 inches would be better. Don't use the cheap, crumbly stuff -- use EPS rated for ground contact.
Does it matter if it is the foil faced or paper/fiberglass faced polyiso?
Steve,
No.
If using foil faced polyiso on the interior of the foundation when there's 2" of EPS with an unspecified exterior finish you have to be sure to have a very good capillary break between the concrete and sill plate (like an EPDM sill gasket).
There isn't any drying toward the exterior to be had through 2" EPS and most EIFS finishes, and just raw EPS is going to be less than 2 perms @ 2", assuming Type-II or Type-IX EPS. With a foil facer preventing drying toward the interior and very little drying toward the exterior, the moisture content of the concrete could end up being pretty high. The concrete is fine even when fully saturated, but the sill plate, not so much. But an impermeable EPDM sill gasket would keep the wood dry. (A capillary break between the footing and the foundation wall is a good idea too.)
In US zone 6B it's financially rational on a lifecycle basis to put R10 under the slab, but beyond that there's little rationale from an energy use basis. Unless it's radiant floor heating 3"(R12.6) of Type-II or Type-IX EPS would be plenty. Beyond that, the cost another inch can be more expensive than the lifecycle cost of grid tied solar supplying that difference in energy, especially at the favorable insolation levels found in UT.
If you happen to be in a volcanic zone with higher than average deep subsoil temps, even 2" might be the financially rational limit. There are parts of zone 6 in Utah with subsoil temps north of 60F, and others with subsoil temps south of 50F. A really crude subsoil temp map lives here:
http://www.builditsolar.com/Projects/Cooling/US-ground-temps.gif
Your county or state (or a ground source heat pump installer) may have better resources for figuring out what the temps are under your house.
Dana,
Thanks for your insight, you guys are a wealth of knowledge on a subject that can get very confusing, especially with different climate zones, humidity levels, etc.
I will be using 2" paper/fiberglass faced polyiso for the interior foundation walls as per Martin's suggestion. Most of the foundation basement walls will be below grade aside from a foot or so above grade. Putting an EPDM sill gasket should not be too difficult. Are the foam sill gaskets not good enough?
Yes, there will be hydronic radiant heating in the basement slab. I would like to get away with 2" of EPS under the slab from a cost standpoint. The ground temperature may be pretty high where we are in Midway, UT. There is a LOT of natural hot spring and geothermal activity in the area like this http://geology.utah.gov/map-pub/survey-notes/geosights/midway-hot-pots/ We are building 1.5 miles NE as the crow flies of the Homestead Hot pot Crater. I will see if I can find a ground temperature map.
Thanks again,
Steve
The 1/8"-1/4" thick foamy sill gaskets don't really cut it if the foundation concrete is damp. EPDM sill gaskets are cheap insurance in the grand scheme of things, and unlike most foam sill gaskets, they usually do a pretty good job of air sealing that joint.
If you're heating with the slab, go with the extra inch of sub-slab EPS unless it's known-toasty sub-soil.
What is the heating fuel for the hydronic system?
The heating fuel is Natural Gas.
On the subject of sill gaskets and separating heat/cold transfer areas, what is the best product to separate the footing from the foundation if I choose to? This seems to be a more common building practice since the last home I built in 2008 that was ICF from footing to roof.
Dana,
I never answered that the heating fuel is natural Gas. I'm not sure if that matters, not that I can change it.
Dana or Martin,
I have a new question on my roof assembly and a vapor barrier. From outside to inside...Sarnafil membrane, 5" polyiso, 5/8 OSB, 14" cellulose, vapor retarder, T&G ceiling.
HERE IS THE QUESTION: is 7/16 osb with sealed seams a good enough vapor retarder, as I am considering using a type of pre-finished floor material for my t&g wood ceiling, and therefore may want the OSB as the backing for nailing?
I want to avoid being redundant with membrain and the OSB, if the OSB will work as a vapor retarder.
Again, thanks for all your help.
Steve
Steve,
Q. "What is the best [capillary break] product to separate the footing from the foundation if I choose to?"
A. Here are some options:
1. Asphalt-based dampproofing
2. Latex-based low-permeability paint (elastomeric paint) -- for example, UGL DryLock latex masonry paint
3. Delta Footing Barrier.
4. Cementitious coatings (cement-based waterproofing) -- for example, Thoroseal
5. A fluid-applied product like Tremco TREMproof 250GC, Henry CM100 Cold Fluid-Applied High Building Waterproofing, ePro ECOLINE-R Liquid Applied Membrane, or BASF MasterSeal HLM 5000 (formerly SonoShield HLM 5000).
Some builders have used 6-mil poly, although poly isn't easy to work with in this location. (Then again, asphaltic dampproofing isn't easy to work with either.)
Here is a link to a relevant video: Installing a capillary break on top of concrete footings.
Steve,
Q. "Is 7/16 inch OSB with sealed seams a good enough vapor retarder [on the interior side of my cellulose], as I am considering using a type of pre-finished floor material for my tongue-and-groove wood ceiling, and therefore may want the OSB as the backing for nailing?"
A. Yes, it is good enough. You don't really need a vapor retarder in this location (except to satisfy your code official), but it is a good idea to have an air barrier in this location. OSB with sealed seams will work fine. In case your building inspector needs to know, dry OSB has a vapor permeance of 2 perms.