How to cantilever a double stud wall (and other questions)?

Hi all,
I hope to dip again into your well of generosity and knowledge. It’s been a great help so far.
I’m designing an ADU in CZ6, southern Quebec. It’ll be a full basement, single-storey with 18″ floor trusses, and a vented flat roof. It will attach to the back of the house where we’re demoing a section down to the subfloor (2×8 joists) and connecting that to the ADU.
Floor space is at a premium given the site and zoning limitations. So I want to have an R40 double stud wall, dense-packed cellulose, with the interior 2×4 load bearing and then cantilever out the exterior 2×4 wall by 5″–I know this takes it into Larsen truss territory though the line between the two is somewhat grey.
I’m considering three options from what I’ve gleaned in other discussions:
1) 2×12 common plate on top of sub floor
2) extend 3/4″ CDX subfloor out
3) use 2×12 sill plate extended out, which provides insulation for the rim joist
So my questions are:
– Do all of these work structurally for a 5″ cantilever? Or would I need a cleat underneath or other bracing? Would it carry the weight of ‘outie’ windows?
– Buildability: What’s the easiest/fastest? In option 1) Would you build both walls at the same time on the 2×12 common plate and stand up together (using a crane)? In option 2) Would you build the exterior wall, stand it up and brace it temporarily, then build the interior wall?
I’ve attached drawings of the three options.
Any and all commentary is welcome. Many thanks.
Cheers.
Shaun
GBA Detail Library
A collection of one thousand construction details organized by climate and house part
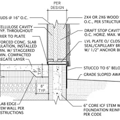
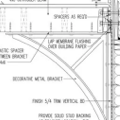
Replies
I don't see any of those as properly supporting the outside wall, a 2x12 in that orientation has very little strength, the subfloor even less.
Why not just have the truss extend to be flush with the outer wall? You can fill the rim area with insulation and get the same amount of insulation.
I think it will be much simpler and inspector friendly to bring your floor joists out so at least part of the outside wall bears directly on it. This means a bit less rigid by the rim joist but you will still have some. If moving the truss is an issue, you can add an extra rim joist to do the same thing.
Anything else is outside of code, so if someone ask, you might need an engineer's stamp to continue. Not sure that is worth the cost and complexity.
One good concept for figuring out how to hold these things up is a how the line of force acts. The assumption here is this force is at 45 deg, so in your case (0.5" canti plus at least 2.5" bearing), you need a bottom plate that is at least 3" thick.
You could essentially make a Larson truss out of the two studs by gusseting them with ply, as long as you bear on the inner stud and just support siding with outer. But as akos said you’d need engineer stamp I assume.
Sean,
I would do as Akos suggests and reduce the thickness of the foam at the rim joist - or move the foam from the exterior of the foundation to the interior, and simply have the walls fully bear on the foundation.
Hi all,
Thanks for your thoughts. It felt like that cantilever was pushing in.
In an earlier plan I did have the floor joists extending out as Akos suggests. And that works for the new build. (See drawing below).
However, the challenge is building this wall on the existing subfloor and connecting it on the same plane to the new ADU. (I'm hoping to keep and use the 2x8 floor joists and subfloor.)
As Freyr_design suggests, on this part of the building could I do a Larsen truss with plywood gussets and have it extend 5", like a Riversong truss wall? (In a this design can the windows be on the outside wall or would they have to be placed in the interior load bearing wall?)
Otherwise, I'll move everything inwards so both walls are over the foundation wall and give up some square footage. But trying to both have and eat my cake.
Cheers.
One of the big problems is if your shear lives on the outer wall you can get huge uplift and point load forces on the framing members that would probably not be supported by this build up. It makes more sense to actually do a Larson truss and keep your shear at the load bearing wall. The other option would be interior sheathing for shear, but that presents other issues.
Why not just build a Larson truss? Or use exterior insulation?
The picture on the left is the way to do it -- truss overhanging the foundation. There should also be a rim joist on the end of truss, the rim joist is flush with the wall studs and the sheathing covers both and ties everything together.
In this configuration I'm not sure the inner wall can be load bearing, there isn't a solid path to the foundation. Maybe others know for sure.
"However, the challenge is building this wall on the existing subfloor and connecting it on the same plane to the new ADU." I don't understand what this means and what the issue is.
DC,
The complication is how you cantilever the trusses where they are parallel to the foundation?
You have to run them the other way.
Take out one joist, double the next one and run a bunch of ~24" pieces perpendicular.
Thanks for the input. And sorry for not being clearer.
Just as a broad layout: in the drawing below the area outlined in the orange at the bottom is the existing house. We'll demo the roof and walls down to the subfloor. But we'll keep the subfloor, which is 2x8 joists.
Then the other rectangle connecting to that is the new ADU which will have 18" floor trusses.
So it's figuring out how to have the same wall depth with these two different subfloors.
I can extend the floor trusses out on the new ADU but cannot do that on the existing 2x8 subfloor. Given the last two drawings I posted (one with floor trusses, one with 2x8 floor framing), how can I do both so the wall is the same overhang to the exterior so they are flush where the new ADU meets the exiting house?
- Extend the trusses on the ADU
- Larsen truss on the existing 2x8 subfloor - is it not a Larsen truss how I drew it in my previous post with plywood gussets? Or is it because the inner load bearing wall is not bearing above the rim joist?
I would plan metal bracing on the interior wall rather than sheathing.
And Malcolm brings up another point of how to cantilever the trusses when parallel at the foundation.
I appreciate your patience. I hope that is clearer.
Thanks.
I think your plan is certainly doable, and I understand that you are trying to eeck out a bit more floor space due to setbacks measured at foundation (like Steve Baczek when he used Larson trusses in this article: https://www.finehomebuilding.com/2024/01/10/understanding-larsen-trusses)
If it were me, I would do same technique as Steve because I use ply for shear out here on west coast and it is a good place to air seal. My suggestions:
Get an engineer sign off on whatever you do
If you cantilever truss and load inner studs have them add a member to have continuous load path like dc mentioned
If you are coming up with a unique design just realize that you may end up at a detail you hadn’t thought of that needs a solution and which has not been solved yet by others. Think through all your connections and maybe model the build.
That is the benefit of using a system that has been done before, there are a lot of how to’s out there….
The way to make the floor framing cantilever over the foundation is to have the joists overlap the foundation wall where they run perpendicular. Where they run parallel, have a double joist about 18" in from the foundation wall and have about 24" of joist running perpendicular.
I see about $750 worth of lumber in the existing floor, while it could be modified I think you'd come out ahead to rebuild it completely in the shape you want. The lumber that's in it could be repurposed in the construction. Unless there's some zoning requirement or similar that requires you to keep the existing physical object.
"I would plan metal bracing on the interior wall rather than sheathing."
You have to be very careful with metal bracing that it not short-circuit your insulation. It's especially true when you're going to such great effort to make a highly-insulated building.
Sheathing does more than just provide bracing, it is an air barrier and gives you something to mount windows and doors to. I'd rethink this approach.
For the existing, you can add extra rim joists to bring out the edge of the floor past the foundation. For the new section, you can set the trusses out so they support the outside wall. Make sure to talk to your truss supplier as they need to put in extra support for this.
OBC requires 2/3 of the bottom plate to bear on structure bellows so that is 2.25" of bearing for a 2x4 wall or 3.75" for a 2x6 wall.
It might make sense to bump up the outside wall to 2x6 and reduce the gap between the double stud walls (the assembly R value is about the same). This will put the outside wall pretty close to proper bearing on the floor without much monkeying except maybe and extra rim joist or slimming down the 4" rigid a bit. You can now make the outside wall handle the shear loads so you won't need any extra bracing.
The cost delta between a 2x4 16" OC vs 2x6 24" OC is pretty much noise.
There was a very similar question here recently but now I can't find it. When faced with a similar issue, this is what I came up with and it was approved by a licensed structural engineer. Basically a thicker-than-normal (or engineered lumber) mudsill and plywood gussets to help support the outer wall, with the inner wall being structural.
Reading through the entire thread, I feel like the question is based on a fundamental misconception. Even if the inner wall is the load bearing wall that holds the roof above, that doesn't mean the outer wall can be essentially unsupported. Just the wall itself is going to weigh a lot, it's got to hold the siding, windows and door in addition. And the solution isn't to try to make it lighter by skipping the sheathing.
The solution is to support it properly from below.
I agree that in a double wall it simplifies things to designate one wall as the bearing wall, that allows you to use prescriptive framing. My recommendation however would be to designate the exterior wall as the bearing wall, which allows you to treat the interior wall as a non-bearing interior partition.
Sometimes you simply can't "just support it properly from below." I don't fully understand the OP's limitations but when using exterior insulation on the foundation, options are limited. My very conservative engineer had no problem with us using a PT 4x12 bottom plate and gussets for a 2-story home. We aren't in a seismically active zone, but it is relatively windy and that location has a 60 psf ground snow load. For additional shear strength, you can add cross-strapping or let-in bracing to the inner wall, but I've never had an engineer require it.
It's not just helpful to designate one wall of a double-stud wall the structural layer, it's absolutely critical to understand which wall holds the structure up and which one is mostly holding insulation and finishes. (A lesson learned the hard way having designed and/or built dozens of them.)
Windows should be supported by plywood bucks that span between the two walls, transferring the load to the interior. Doors should be set to the interior, or special accommodations can be made to have them on the exterior but it adds significant complexity.
I prefer for the exterior wall to be the structural layer and keep foundation insulation to the interior, because it's simpler and easier. But it's not always an option.
Michael --
I know you know this, but for the benefit of the other people in the conversation, there's basically two choices when you go to build something. You can hire a structural engineer to design it and submit stamped plans, or you can follow the prescribed designs in the code -- the prescriptive route.
If you're going with an engineer, I find it's best to tell him what you need and not how to do it. So presumably in this conversation we're talking about going the prescriptive route.
If we stipulate that the requirements are for a double-studded wall, and a foundation with 4" of external foam, and the sheathing of the first floor wall is flush with the outside of the insulation, those are our requirements. I think that can be done prescriptively. I'm not aware of any prescribed method of doing a double-stud wall, but it can be done as an exterior wall with an internal partition wall a few inches away.
The prescribed method for having an exterior wall that overhangs the foundation by more than a third of the width of the bottom plate is to use cantilevered joists. There's no rule that all the joists have to run the same way, so on the short sides of the building you run short joists that run into a header that is a minimum of 12" in from the sheathing.
Since the interior walls will all be perpendicular to the joists it doesn't seem like anything more needed for them.
There may be details I'm missing but it seems like that's the foundation of doing it in a prescriptive manner.
DC,
The problem I see with cantilevering the floor system is that you can't run the exterior foam up over the rim-joists, where arguably it is most useful.
Malcolm --
Shawn wants to put a 12"+ wall above. You can put 12" inches of insulation on the inside of the rim joist to good effect.
Alternately, with a 2x6 bottom plate and studs you could inset the rim joist 1-1/2" and put that thickness of foam on the exterior of the rim joist. Or keep a 2x4 wall and inset 1". It ends up you're only cantilevering 3" or so, but there's really no cost in making those trusses 6" longer.
On the short ends it seems like a lot of trouble to cantilever only a few inches, but you'd want that perpendicular blocking anyway to support the interior wall. Basically you're just making the interior blocking a few inches longer than usual and beefier.
DC,
I agree, there are lots of ways to insulate the rim-joist, I was making a narrower point.
The best way to avoid moisture problems with rim-joists directly over crawlspaces or basements is to either use impermeable insulation on the inside, or sufficient exterior insulation to keep the rim-joist warm. It just seems a shame when you are already running exterior insulation up the stem-walls not to be able to continue it up to the exterior walls.
DC, I appreciate your clarification, but I am arguing that my approach CAN be done prescriptively. In the OP's case, they could cantilever the joists, but when using insulated slabs-on-grade, as with my example, that's not an option.
I always tell engineers how I want something done; they are rarely creative and revert to their standard solutions unless I am clear about what I want to do differently than what most people design and build. They also rarely understand moisture-related concerns as well as I with they would.
Thanks everyone four your helpful feedback.
So the new build seems more straightforward. I will get the trusses designed to overhang and make the exterior wall structural and sheathed. I can't get the same trusses for the existing foundation (as per DContrarian's suggestion) as that would create a large elevation discrepancy in the floor of the existing house.
Following Akos suggestions, I could do the 2x6 exterior structural wall sheathed and taped, with 1/3 overhanging and adding another rim joist and slimming down the foundation foam.
Going down this road further I wonder if there would be any advantages to doing a 2x8 wall with exterior insulation instead of the double stud wall. With 2/3 still bearing on the foundation wall would this work? I don't believe it would perform quite on the same level as the double stud. And not sure cost would be much different given the extra labor to install the exterior insulation and the material cost of Gutex or Rockwool.
#1
3/4 wood siding
2 x 1x3 strapping, vented rainscreen
WRB
1/2 plywood taped air barrier
2x6 stud wall
10.5" of dense pack cellulose R39
2x3 or 2x4 stud wall
Intello Plus
1/2 drywall
#2
3/4 wood siding
1x4 vertical strapping, vented rainscreen
WRB
2 1/2 Gutex or Rockwool Comfortboard (R9/R10.5)
1/2 plywood taped air barrier
2x8 (7 1/4 dense pack cellulose R27)
Intello Plus
1/2 drywall
Would you favour one wall over the other in terms of performance, cost, buildability?
Thanks very much.
Shaun
To be clear, I wasn't talking about rebuilding the existing floor with trusses but with cantilevered 2x8s.
Okay. Thanks for the clarification.
double stud walls are very convenient for running wires, and anything else going through them... so much less drilling. I'm not really sure about your application but that is just one of the big benefits I've encountered. The 2x8 is probably easier to frame for the conventional framer, but if you think about it and draw stuff out double stud is not hard either.
I would do a cost comparison if it were me. Also keep in mind that all the cellulose insulation actually has a negative GWP
I would go for #2 as it is the simplest to build.
If you go for 1.75" of rigid over the foundation and 2x6 wall, you don't need the extra rim joist or any floor cantilever. Canti the 2x6 plate 1.75" (this is fine in the OBC) past the floor joists and run the rigid up to the bottom plate.
Akos,
But doesn't that sort of leave you in no man's land on the foundation. With 1.75" of exterior foam, you are still going to have to insulate the interior if you want to get anywhere comparable to the insulation levels being used elsewhere in the build. And if you have to insulate the interior, you might as well put all the foam there.
Hey Malcolm,
Are you suggesting putting all the foam on the interior simply because it is easier than splitting it between the exterior and interior? Or is it a performance issue? I think I read elsewhere of someone sandwiching the foundation wall in foam and Martin said it would be fine, like a SIP.
Or could I put 1.5" exterior foam and then build a 2x4 stud wall on the interior and insulate with mineral wool?
Cheers.
Interior foam is easier to get right because you don't have to worry about thermal bridging. You also don't have to worry about protecting the foam.
Have you determined how your code enforcement measures the extent of the building? Around here exterior foam is popular because land is expensive enough that inches matter, and code enforcement measures from the exterior of the sheathing or the foundation wall, whichever extends further. So exterior insulation essentially gives you a couple of free inches.
But things like that are hyper-local.
Shaun,
I'd pick one or the other. Splitting it gives you all the work and complications of both approaches. My preference is to put it on the interior, where you can use a mixture of foam and batts to get the R-value you want.