Converting Barn into Living Space

Hello,
This is my first post. I’m working on an old Pennsylvania bank barn built in the late 1800s. I recently asked this question on another forum but just discovered this forum and it seems more active with more up to date information – so sorry to repeat if you visit the other forum as well. I’m looking for expert and sound advice on creating conditioned space within the barn from the inside out, without disturbing the exterior – definitely not the typical way to build these days.
The barn is post and beam construction – 8″x8″ posts with 8×8 beams, collars and girts. 1×12 board and batten siding is attached to smaller 3×5″ mid girts. The post and beam structure is 40’x60′ made up of 4-15×40′ bays with a 29′ gable peak, and this structure sits on a thick stone wall foundation (18″+) cut into the bank for ground level access on the bank side which faces north. The area below the timber frame is enclosed on 3 sides by the stone foundation (east, north and west), and has insulated garage doors in front on the lower ground level (south side). In the lower space, there is a 4″ slab over 4″ crushed stone w/vapor barrier for a floor, and the front side where doors are, is separated from the outside by vertical sub-surface 1″ foam board between slab and driveway. The lower ceilings are 8.5′ high, and covered by 1x beaded board attached directly to the underside of 3″x9″ floor joists of the structure above. The shell is in great shape overall and has a screwed on corrugated metal galvalume roof, on rafters 30″ on center w/oak purlins spaced @ 24″.
There is currently a two story apartment in 1.5 of the upper 15’x40′ bays, that is insulated with OC Icynene sprayed from the inside walls and ceilings against Tyvek and felt paper and inside 2×4 walls inside the timber frame. The floor is insulated w/cellulose in this space. The apartment performs very well during the cooling season and is inexpensive to heat, though the first floor wood floor is cold in the winter, largely due to the fact that HVAC is supplied by ductwork hanging from the ceiling between the first and second floors, 13′ off the floor.
This apartment is separated from the remaining 2.5 unconditioned bays, by a 2×4 wall, insulated with Icynene sprayed to Tyvek and covered in 1x shiplap siding. All walls have 2 layers of 5/8″ fire code drywall.
I’m looking at the possibilities of creating additional living space in part or all of the remaining upper level bays and looking for the best approach to create an envelope from the inside out. This project will likely need to be done in phases due to the cost of materials and sheer size of the space. I can either do a finished section at a time (most likely), or try to stretch and do the entire interior envelope and then build out within it.
The total space has nearly 4,000 sq ft of wall to insulate, 1,000 sq ft of floor and 2,000 sq ft of ceiling/roof.
Spray foam may be out of the question here at $2-5/sq. ft for appropriate R value, and based on my research so far may not be the most economical (long term) or environmental choice these days. So I’m considering adding an air space between the inside of the existing siding boards (for rain screen), by running additional 1x girts between the posts and attaching a house wrap to the inside of these girts. This would create a 3/4″ air space between the siding the the house wrap. Then we would attach 2″ or 3″ used PolyIso foam boards to the girts, taped and then sealed & caulked between the posts (at the recommendation of Dana1 on another forum – thanks!). We could then frame inside the foam boards with a 2″x4″ wall, likely covered in either drywall or directly w/t&g 1x cladding.
I’m concerned that I do not introduce conditions detrimental to the timber frame structure or the existing board and batten siding by whatever approach I take here by introducing humidity or moisture in the wrong place. The existing 1×12″ cypress exterior siding is in great shape and I replaced the battens several years ago and repainted the outside w/oil primer and high quality latex paint – all brushed on after grueling prep. The backside (inside) of the siding has never been painted. There are small gaps and cracks here and there in the siding where air and a strong blowing rain can get in but overall its in beautiful shape for its age and I do not want to disturb it at all on the exterior side.
Our main goal is to find a cost effective way to add some additional conditioned living space that we may ultimately add on to (inside the same structure) in years to come, yet do it in an eco-friendly way that is efficient to heat and cool. To avoid repeating the cold floor issue in the other space, we’re likely going to run PEX over a plywood subfloor with sleepers for heat and possibly add a mini-split for cooling.
As I said, we will most likely have to implement this in phases over several years but there may be reasons to try to complete the envelope first.
Appreciate any thoughts or advice on this from those with more experience!
GBA Detail Library
A collection of one thousand construction details organized by climate and house part
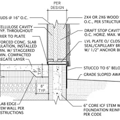
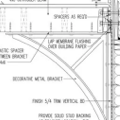
Replies
This sounds like an interesting project and I know that many people are converting barns into living space. I'm sure there are some GBA members with experience with this type of conversion, or at least some good ideas. Perhaps it would be helpful to post some photos so we can have a better understanding of what you describe in your post.
My guess it that it would be best to build a house within the barn - treating the barn just as an imperfect wind/rain/UV barrier.
When I look at my local barns the siding was not intended to be water or air tight. The siding board just butted up against the next ¼ inch gaps would be common, if a little rain got in it was not a problem as a lot of air also got in and dried it up before and thing rotted. If you make changes to the walls they may begin to rot and grow mold. If your tarpaper spray foam walls are working well, they may well be your best and the low cost option. Making your walls waterproof without changing the look will not be cheap.
If you want warm floors heat the basement.
I do like the house inside the barn idea.
Walt
Thank you all for your thoughts. I'm working on creating a 3D model of the place but in the meantime, here are some photos.
As far as the house inside the barn idea goes, what kind of spacing are you talking between the existing barn siding and the "house inside the barn" walls? How would the house wall be clad and how would the windows work? Just extra deep windows boxed out with a space between house exterior wall and barn interior wall where you could walk? Wouldn't this create a potential path for fire?
It could be minimal space, much like vented cladding. But good questions that I don't have answers for.
Thank you all for your thoughts so far. I'm working on creating a 3D model of the place but in the meantime, here are some photos.
As far as the house inside the barn idea goes, what kind of spacing are you talking between the existing barn siding and the "house inside the barn" walls? How would the house wall be clad and how would the windows work? Just extra deep windows boxed out with a space between house exterior wall and barn interior wall where you could walk? Wouldn't this create a potential path for fire?
photo
Deleted
trying again
Inside of barn at ground level on bank side of barn (lower ground level on slab is below this).
The inside of the siding boards are not wet at all, they've just weathered that way over 100+ years.
Also interested in thoughts on sealing and insulating the roof. It is a corrugate galvalume metal roof screwed to 1"x4" oak purlins (24"oc) on 3x5.5" rafters (~30" oc).
Quick sketch of wall/floor details...
...
At this point it seems like the way forward may be to apply girts between posts to create a gap, adding tar paper or Tyvek inside these girts, attaching polyiso to the inside of the girts/paper and sealing with tape/caulk. Then build interior wall framing inside of the sealed polyiso insulation. I guess the rain screen layer will not be able to get between all existing framing members for total drainage in the conventional sense, but should be able to prevent moisture that gets behind the siding from migrating inside. Make sense?
If so, does it matter which side of foil backed Polyiso would go in/out? What if using 2 layers?
Do I need an interior vapor barrier/plastic layer between insulation and wall sheathing?
Also, for the roof insulation, I can follow same approach as for siding but strongly considering installing baffles between joists and doing a 1-1.5" flash coat of closed cell spray foam to seal before installing any other ceiling/roof insulation. If I go with this approach, is it ok to spray foam the entire sloped roof and center flat ceiling now and then build out the interior little by little or will this create potential moisture issues as all walls and floor would not be insulated yet? For example if I spray foamed the entire roof/ceiling but then only add a single insulated room inside the larger space for the time being with other surrounding exterior walls uninsulated for now?
Barn Restoration,
Your plan for the walls would work. It would make sense to specify rigid foam that meets the minimum R-value requirements described in this article: "Calculating the Minimum Thickness of Rigid Foam Sheathing."
If you use the same approach for the roof assembly, the riskiness of the finished product will depend on whether or not there is a good vent channel above the insulation. Ventilation makes the assembly more robust. It sounds like you are considering either a continuous layer of rigid foam, or a mash-up between rigid foam and flash-and-batt.
If you end up proceeding without a ventilation channel, it's important to follow the rules for flash-and-batt unvented roof assemblies. More info here: "Flash-and-Batt Insulation."
Just wondering how you ever made out with this? I’m at the exact stage you were 3 years ago in my barn and attempting to get to the insulation stage. My contractor was going to simply put up closed cell spray foam and we’ve been debating adding tar paper underneath. Any advice about what you decide to do would be treasured.
At the moment, I am working on my homework on insulation techniques for green building, I found your discussion and it is extremely useful. The various perspectives and experiences shared by the community have enriched my understanding of the topic and expanded my knowledge beyond the confines of task that I am going to get done by experts. I have found review of Edubirdie at https://www.sitejabber.com/reviews/edubirdie.com and would love to delegate my task to professionals. It's encouraging to witness professionals and enthusiasts engaging in meaningful conversations about insulation, fostering an environment of continuous learning and innovation in the field of green building.
If Edubirdie wrote your reply, get your money back.