Insulating and air sealing in an attic with a strapped floor

As part of an insulation upgrade job for my attic, I want to air seal the attic floor and build-up rigid foam at the eaves to try to get more total insulation value in that area (I unfortunately have low heeled trusses).
The problem I’m wrestling with is how to properly detail the floor, particularly at the eaves. The current stack-up from inside to attic is 1) drywall, 2) poly vapor barrier, 3) 1 x 4 strapping attached perpendicular to the bottom of the trusses. Should I detail the poly as the air barrier?
I’ve also attached a diagram of what I was thinking of doing at the eaves – basically stacking up foam until I get 18″ of height. The problem again is how to detail the first layer of foam. The foam itself will basically be a vapor barrier (likely foil faced graphite eps or maybe polyiso) so should I remove the vapor barrier at the eaves to prevent trapping the strapping between two vapor barriers? I could then detail the foam as the air barrier in that section. For air sealing, I was planning on using a combination of acoustical sealant, canned spray foam and Siga Wigluv.
Any advice would be greatly appreciated.
GBA Detail Library
A collection of one thousand construction details organized by climate and house part
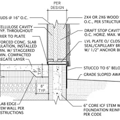
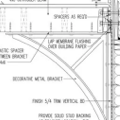
Replies
Maybe I should save myself the trouble and get someone to put in closed cell spray foam instead of the rigid boards? ...is it possible to spray it to that kind of thickness though?
We had my basement done with closed cell and I had to get the contractor to come back three times until I was happy with the jobs...missed spots, too thin in other places, etc. And that was supposed to be the bust people in town. The experience has made be reluctant to use spray foam again.
I think your design is way overboard. You have a drywall ceiling, use that as your air barrier. Seal the perimeter of the drywall (top plates, etc.), and any penetrations and you should be good to go. You don't need a vapor barrier on the floor of a vented attic.
I would not use stacked rigid foam like this. You can use rigid foam to form your vent baffle, and it might make sense way out at the eave over the top plate there, but the massive stack further in is overkill. What I would do if you want to put rigid foam out at the top plate, is to cut a beveled peice and put in enough to just cover the top plate to fill the space between the top plate and the bottom of the vent baffle. Fill the rest of that space, and the entire attic floor, with blown cellulose.
You don't need all the canned foam, tape, and other details on the ceiling between the slats -- the drywall should be all you need to provide an air barrier there. There is no need to air seal the back of a continous sheet of drywall since the drywall itself won't have any leaks. You only need to seal gaps where the drywall makes a transition, such as the ceiling to floor area at top plates, and this is mostly because air can leak up from the stud cavities in the wall and get up into the attic through the gap at the top plate. Wire and pipe penetrations are the other place to seal. There are some articles on GBA about the "airtight drywall method", which you can refer to get some detail (and good drawings) -- just remember that you'll be working in reverse, sealing from the backside and not as you hang the drywall. The basic principles are he same either way.
You don't need spray foam here, it isn't necassary. Use my simple method with basic air sealing, some rigid foam for vent baffles and maybe over the top plates out at the eaves, and blown cellulose over the rest of the attic floor. This is all you really need. Put in thick enough cellulose to get to the R value you want. Blown cellulose can get into the space out near the top plates pretty well as long as you have at least a few inches, so it's only the very tight far reaches that you might want to fill with a wedge of rigid foam. You could potentially also use a little spray foam in this band around the perimeter instead of rigid foam.
Bill
By the way I got the idea for the stacked foam from Martin's and Norman's posts here:
https://www.greenbuildingadvisor.com/question/solutions-to-inadequate-insulation-at-truss-heel
Thanks you very much for your advice Bill. A few points of clarification:
1. The vapor barrier is already there. I'm not adding it. There will likely be spots where it would be hard to detail the drywall as an air barrier because the joints would be covered by strapping, the vapor barrier, or both. So this raises the question of whether it's better to detail the vapor barrier as the air barrier rather than having to remove it to get at the drywall.
I've included an updated diagram highlighting some potential areas of interest:
a) at the top plates, there's typically a piece of strapping that runs parallel to the top plate so
the drywall joint is inaccessible
b) the vapor barrier often runs right up to penetrations so you could seal it or pull it back a bit
and seal the drywall instead.
2. In my original diagram, I understood that the drywall could be an air barrier and that it only needs to be sealed at the edges. But I was again challenged by the fact that the joints at the top plate would be under the strapping. So I thought instead maybe I could detail the first layer of foam as an air barrier.
Nonetheless, I agree the cost and complexity of the foam stack is probably not worth the extra R-value. Just inside the top plate, I estimate I might have maybe 6"-7" of height for insulation so we're talking about a difference of maybe R7 to R8 between cellulose and stacked up foam. That's not trivial but maybe also not enough to worry about.
...I wish I had spent more time on GBA before choosing a home to buy. I would have looked for one with raised heel trusses or considered a custom build.
3. The reason for the tape was that my house experiences quite a bit of seasonal movement in the framing. I've read that canned spray foam doesn't hold up well as an air barrier when there's movement so I wanted to use tape instead. Even without the foam stack, I think I'll still probably use tape or a stretchy caulk wherever I can to cope with this movement.
Joints between drywall sheets should be sealed with mud/tape on the interior, so you only need to worry about the perimeters. In your case, you could either seal both sides of a slat, or if the vapor barrier is in good condition (no tears or holes), you could detail that as your air barrier. The way you're describing things, I think detailing the vapor barrier as the air barrier is probably going to be easiest.
I don't think it's worth a massive stackup of rigid foam at the eaves. You only need rigid foam where you need max R per inch, and in areas where you need to cut to fit a wedge shape, since loose fill insulation doesn't always get tight into small angular spaces. Your new drawing shows a better approach in my opionion, using rigid foam where it's most needed but not going overboard where the blown insulation can do the "work" of insulating things.
Tape is your best bet for things that move. Caulk is probably next, but you need a good caulk. I like the polyurethane caulks for tough spots. Canned foam can sometimes seperate, but the flexible "door and window" type might hold up better. I say "might" here because while this has been discussed before, I'm not aware of anyone having done any real long-term testing to show if it's actually any better than "regular" canned foam or not.
I wouldn't choose a home solely based on info on GBA. There is lots of info on GBA about energy efficiency, but that's not the only thing that you should consider when buying a home. A lot of the things discussed here can be added to any home, so I would (and I did myself :-), choose a home more based on things you CANNOT easily change. In my case, I picked a more rural area, and a large, wooded lot. You can't "fix" or "renovate" your way to a different community, and you're very limited in terms of what you can do with the lot, so in my view those are the first considerations. My house was good, but not perfect, so I've been working to get closer to perfect. Remember that any home is likely to have at lease a few things you wish were different (I can think of things like that about my own home). Don't sweat the small stuff, basically :-)
Bill
Too true....can't renovate a lot or location. I live in a decent sized urban center (Ottawa, about 1M population) and I wanted to be able to walk to the light rail line for my daily commute to work.
We managed to find a property with all the features we need (garage, rooms, bathrooms, etc.) within that walking distance and with no rear neighbours and a bit of a view. Virtually impossible to get all that and modern energy efficiency. All the new housing stock is sprawled out to the boundaries of the city.
If I won the lottery, I'd keep this property and do a deep energy retrofit. In the meantime, I'm trying to find reasonably priced upgrades that will pay-off in terms of utility bills and comfort.
I would recommend you carefully plan out all your energy retrofit projects. A lot of that can be done in small steps, but some "steps" really need to be done together. If you plan things carefully, you can spread out the costs and still do things in a logical way. I do that on my own home, usually because I either don't have enough time to do it all at once, or because my wife would prefer to not be in a constant state of renovation :-)
I'm not familiar with Ottawa, but I have family outside of Hamilton, so I'm familiar with that area. Toronto especially has become quite the megalopolis. Even in the more rural areas of Ancaster development has been going at a quick pace.
Bill