Insulating a Shed Roof

(I asked a version of this a year ago but new parameters/information make it easier to ask again):
I will be re-roofing a 4:12 pitch shed roof (about 880 sq. ft.) on our mid-century modern home in Maryland/DC region. The room below is fully finished and so any insulation work has to happen from above. The roof is 2×10 rafters (the low side has a 2′ overhang and is vented at the soffit; the high side terminates on an upper clerestory wall and has venting through the fascia that overhangs the clerestory wall about 2″). It is currently insulated with 9.5″ of fiberglass insulation installed (in 1977) (that’s right, the 9.25″ “vented” cavity is filled with 9.5″ faced fiberglass; thermal images show lots of poorly placed insulation, gaps, etc.). The roof faces western exposure. Under the rafters is 1/2″ drywall with latex primer/paint (no poly). The building has 2×6 and 2×8 walls and has poly vapor barrier; everything has been carefully airsealed and the windows are fairly airtight for their age.
I will re-roof with Union Corrugating standing seam, and they spec plywood sheathing, hi-temp ice-water, a slip sheet of synthetic underlayment, and the standing seam panels attached with pancake heads into the plywood.
I want to redo the insulation when we re-roof. I see a couple of options and want to hear what others would argue is the proper approach.
Option 1) Plan to add 7.5″ of XPS in cut/cobble assembly (~R35) and leave a biut less than a 2″ vent space. This is the cheapest approach to achieve foam, allows me to (maybe) leave some pieces of plywood in place and while a pain, save a lot of money (when plywood is $50 a sheet), and allows me to work in stages on my schedule, not on foam installers schedule. Questions: Do all the edges need to be foamed all seven inches, given there will be a vent? Do the butt joints need to be sealed? Since vented, can I be fussy about the first layer of edge sealing and then just dry fit the top layers?
Option 2) The $6800 quote I just got from the most recommended foam insulator: I remove existing roofing, existing plywood decking, leave it all tarped and vulnerable until they spray foam between the rafters (closed cell to 5 1/2″ to achieve R-38, leaving 3-4″ of vent space)), then I lay new decking, and proceed. Company estimator said beyond 5 1/2″ is decreasingly pointless. (they also tried first to suggest fully filling the cavity with open cell was acceptable and I said, not according to everything I’ve read, and they quickly moved to closed cell with a vent)
or Option 3) I add 2″ SPF strips to the rafters and make the 2x10s effectively 2x12s and then place R-38 of Rockwool and maintain a 2″ vent channel. Seems to have the advantage of cost effectiveness, I’ve been told not to worry about windwashing, and the work can all be prepped. Getting the 2″ strips attached effectively so the sheathing has the appropriate strength will be key (I guess construction adhesive and attach the sheathing with 3 1/2″ framing nails so there is 1″ embeddment into the existing rafter?)
Any other options I’m missing? Thanks for any guidance. and thanks to those who responded a year or so ago.
GBA Detail Library
A collection of one thousand construction details organized by climate and house part
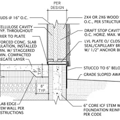
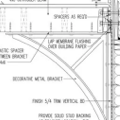
Replies
Michael,
This gives a pretty comprehensive overview of the options to choose between: https://www.greenbuildingadvisor.com/article/five-cathedral-ceilings-that-work
yes, thank you. I've studied this article, Martin's two articles on cathedral ceilings and cut/cobble and thus narrowed it down to these three options (and have some slight variations from the prescriptions in the articles). At this point, I'm leaning to cut/cobble as described. I joined GBA so I could get a final "here's why that would be a mistake" or "if this were mine and I was faced with same constraints, I'd also do option x as you describe," or "you missed this other way to proceed that is better." The last thing I want to do is mess this up and have to redo it.
Code for roofs in MD is R49. You should aim for that, as a reasonable minimum. The spray foam guys routinely say that anything past "x" thickness isn't worth it, but that's because spray foam is so expensive that they're probably right. They ignore the fact that, in most places, R49 is the law. That said, many jurisdictions have some sort of existing building treatments that allow less insulation so long as you fill your cavities, and that would even still allow venting + fill in most cases. If your jurisdiction does this, your approaches would all work, though the 5-5" SPF might not meet the spirit of even a rehab code. Note also that R38 is allowed by code in lieu of R49 if the full thickness of insulation extends over the top of the wall plates. It sounds like you may be able to do this in your assembly. If that's the case, then your options 2 and 3 meet code and will work from a moisture standpoint.
Your option 1 does not, but could if you swap out the XPS for polyiso insulation. This would also be a better solution from a climate standpoint, as XPS is not very "green." You can probably find recycled polyiso in your area to significantly cut down on costs. I would use at least one layer of foil-faced polysio and that would be the layer I would aggressively air-seal. The rest could be loose-laid, so long as the gaps aren't bigger than about 1/4".
Still, I think option 2 would be the easiest (not very green, even with HFO blown foam). Make sure you get your full thickness of SPF if you go this route. many foam installers short you pretty significantly. Option 3 would be cheapest, especially if you can do a lot of the work yourself.
This is awesome. Thanks. I can definitely cover the wall plates and assumed that for aiming for R38. Polyiso is a great suggestion. It appears all that is available around me is foil faced. Is that an issue to have each layer foilfaced? Is there any preference for sealing (gaps cracks can foam? Tight fit and a good caulk? And not worry as much about upper layers?).
Assuming 16 oc, your 7.5" of cut and cobble works out to around R30 assembly. If you go with HD batts, that is around R26. That is a lot of extra work for not much gain.
Overall, all your options work out to similar assembly.
The one with the foam strips does bump up the R value a bit but you would need an engineer to sign off on it. Rigid insulation needs to go over plywood decking to spread out the point load from the rafters plus your roof sheathing is now disconnected from the rafters which can create structural issues.
If you want a high R value roof, your best bet is to dense pack over the batt in the existing roof to fill all voids than install around 3" of poyiso over the roof deck before the metal roof goes on. Lot of metal panels can be installed either directly over foam or 1x4 strapping. This would avoid having to pull up the deck or even sections of it. This would get your around an R45 roof.
This can also be staged, cut holes, dense pack, cover in peel and stick followed by the rigid with synthetic underlayment + strapping finally the metal roof goes on. Except for the dense packing and the metal roof, you can do the rest of the work yourself. Currently 3" roofing polyiso is about the same cost as plywood here, so it is free since you don't have to replace the roof deck.
R30 for the assembly because of thermal bridging in the rafters?
Yup, thermal bridging from the rafters. You are putting ~R9 of wood in parallel with your ~R30/R35 of insulation. Even more pronounced if you are using spray foam.
This is the reason that rigid insulation should always continuous and exterior to the structure, more efficient use of an expensive material.