Insulation over lath?

How should I address insulating inside rooms over the old lath and blown-in insulation already there? Should I install rigid foam over the lath? And if so, how thick? Or should I rip out the lath and old blown-in insulation, which is very tight, and start fresh?
GBA Detail Library
A collection of one thousand construction details organized by climate and house part
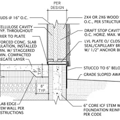
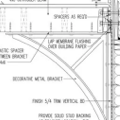
Replies
Deborah,
You should install rigid foam insulation directly over the lath and plaster. There really is no limit to the thickness of the foam -- except the length of the necessary screws to attach the foam. In most cases, you'll want to install 1x3 or 1x4 strapping, 16 inches on center (either vertical or horizontal strapping), on top of the foam with screws to make it easier to fasten your drywall.
All electrical boxes will need to be relocated or extended, and of course you'll have to build jamb extensions for your windows.
Deborah,
Where are you located and what type of blown-in insulation do you now have? It may be possible to salvage the existing insulation and re-use it.
You won't be able to rework the wiring and move the boxes inward unless you open up the existing walls. Opening up the walls also allows air-sealing of any joints, gaps and penetrations. Air sealing is often as important as insulating to improve the building's efficiency.
You may also have to remove the plaster in order to rework the door and window trim and baseboards, as those were often integrated into the plaster coat.
Once walls are opened and all necessary repair or upgrades completed, you have the option of using interior foam board or the less expensive cross-hatched framing to thicken the walls to allow more blown insulation (cellulose is far superior to fiberglass).
Thank you Martin and Robert,
I'm located in Northfield, MA, just south of the NH border. This is a 100 year old 2 story farmhouse. We have had to jack up to replace sills and fieldstone foundation on the rear L. The front foundation is stone with brick on the top courses, and a poured floor. We're now removing the entire roof system, due to a fire back in the 70's in the main house and a 2/12 pitch on the L end. At this stage we're left with just the outside walls standing, we even had to tear down 2 chimney's, cause the mortar was all falling out.(have salvaged a large number of the bricks to reuse at a later time) I also saved the fancy trim and doors, but due to lead paint, will probably reuse only some of it. Windows had been replaced maybe 10 years ago. I bought the house and land as a long term (5-10 year) investment. At this point I will probably never recoup the expense of repairs, but do want to make an effort to have a warm, efficient home when all is done.
I think the old blown insulation is fiberglass, it's very itchy. All of the plaster on ceilings and walls has been removed and we opened up spaces in the lath to allow for the electrical and plumbing and heating work to come. My contractor says to fill the voids with fiberglass batting. Maybe the addition of extra insulation inside the walls is a small thing when compared to the enormous amount of work on the rest of the building?
At this point things can only improve and I appreciate any and all ideas on how to proceed.
Deborah,
If you've stripped the house to its essentials, then the only sensible course would be to perform a major energy-efficiency retrofit. The additional cost of air sealing and thickening the walls for insulating to current energy code standards will offer the best payback in both comfort and future financial savings. I would also suggest replacing all existing windows with new, efficient ones.
Putting fiberglass batts into the existing framing cavities is the least sensible approach. Fiberglass batts do not stop convective air movements (with the consequent energy penalty and increased condensation potential), do nothing to improve the building's fire resistance, and are an open invitation to insects and rodents.
If you choose to install batts, then use borate-treated recycled cotton batts, and create an interior thermal break with 2" of XPS rigid foam board, strap and drywall. Otherwise, use 2x2 cross-hatching or a secondary interior wall to deepen the insulation cavity for dense-pack cellulose, if you choose to avoid petrochemical foam.
The IECC insulation standards for your climate zone call for minimum R-38 ceilings, R-20 walls, R-30 floors and R-10 foundations, as well as maximum U-0.35 windows (R-3, or double-glazed lowE). To put that kind of money and effort into this rebuild without bringing the house up to current efficiency standards would be throwing money away. If your contractor suggests stuffing fiberglass back into the walls and calling it good, then you need another contractor.